Untitled
APPLICATION MANUAL 2016
09 GENER AL INFORMATION
86 Machines, Tools, and Aids
14 General Product Information
21 Swarovski Products and Suitable Application
100 Quick Assistance101 Swarovski Hotfix Selector
23 SOLDERING, PL ATING, AND STONE SET TING
SEWING, EMBROIDERY,
AND HAND APPLICATION
24 Machines, Tools, and Aids25 Suppliers
112 Product Overview
112 Machines, Tools, and Aids
34 Directions for Jewelry Manufacturing
116 Application123 Useful Information124 Quick Assistance
127 MECHANICAL APPLICATION
40 Machines, Tools, and Aids43 Suppliers
128 Product Overview
128 Machines, Tools, and Aids
58 Overview of the Application Processes
59 Product-specific Application Instructions
160 Useful Information
161 Quick Assistance
163 CARE INSTRUCTIONS
164 Textile Care Instructions
73 Machines, Tools, and Aids
167 General Care Instructions
168 Laws, Regulations, Norms, and Standards
168 Warning Notices
169 Care Instructions
Swarovski is the premium brand for the finest crystal
embellishments since 1895. It is recognized for its
innovative excellence and its collaborations with
top-class designers and brands in the fashion, jewelry,
accessories, interior design, and lighting industries
across the globe.
Available in myriad colors, effects, shapes, and sizes,
crystals from Swarovski offer designers a fabulous
palette of inspiration, and are produced according to
the innovative, lead-free* Advanced Crystal standard.
Born out of a passion for detail and high-precision
cutting, these precious ingredients impart refined
glamour to everything they embellish. They can be
recognized by the ‘Crystals from Swarovski' seal, which
serves as a certificate of authenticity that identifies
products made with genuine Swarovski crystals.
A family-owned company for more than 100 years,
with values rooted in integrity, respect, and excellence,
Swarovski is noted as much for its ethics in business as
for its contemporary artistry and innovative flair.
* Crystal glass and all other materials containing 0.009% lead or less.
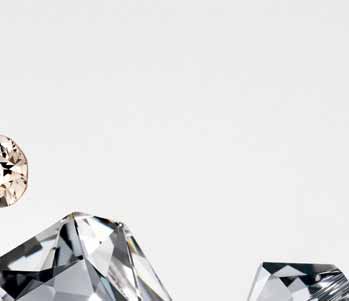

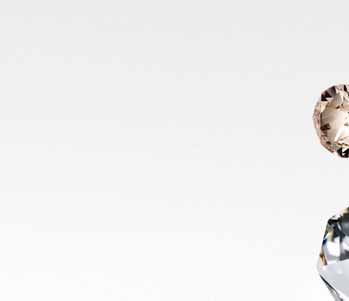

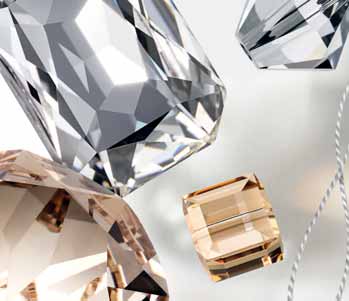
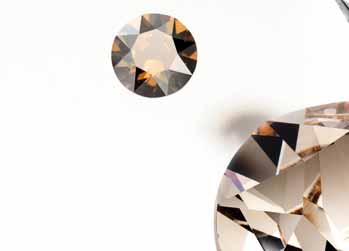
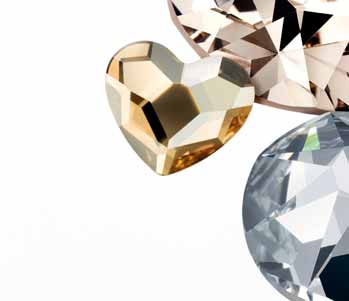
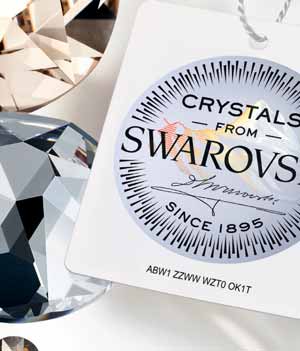
SEAL YOUR SUCCESS
Be part of our exclusive Ingredient Branding program
TAKE THOUSANDS OF CRYSTALS WHEREVER YOU GO
Wherever you are, whatever you're looking for, search over
15,000 loose elements and 200,000 forward-integrated elements with
Swarovski's inspirational new Crystal Collection App.
Online or offline, stay app-to-date with the latest innovations and find
popular classics – it's easy to install, easy to browse, easy to use.
E XCELLENCE, THROUGH INNOVATION AND ORIGIN
Advanced optical measurement and
The variable temperatures at which
high-precision manufacturing deliver
Hotfix glue can be activated enable the
premium cuts characterized by
application of crystals on a broad range
SCIENCE OF GEOMETRY
ENHANCED APPLICATION
of textiles.
CRYSTALS – MADE IN AUSTRIA
With its new advanced foiling technique,
The combination of innovation with
Swarovski has set a new standard in the
sustainability and respect for individual
lifespan of crystals.
wellbeing means that quality is
EQUIPPED TO RESIST
always assured.
PREMIUM , BY SERVICE AND DESIGN
Throughout its global network of Design
Swarovski's Global Service Network
Centers, Swarovski offers exceptional
provides customers with dedicated
service provided by the industry's best
personal assistance on a local level.
LEADING CREATIVIT Y
creative talent.
APPLICATION SERVICE
DESIGNER EDITIONS
A comprehensive range of application
Creative collaborations with top
services means customers benefit
designers result in exclusive cuts and
from the extensive experience of leading
unique designs for Swarovski crystal.
APPLICATION SERVICE
DESIGNER EDITIONS
international experts, as well as
COMPLIANCE, WITH INTEGRIT Y
ADVANCED CRYSTAL
Regular legal monitoring of chemical
Swarovski's patented lead-free* formula
requirements and reasonable testing
has changed the DNA of crystal while still
provide customers with the comfort of
offering the same sparkle, dependability,
and variety for which Swarovski is famous.
COMPLIANCE MAT TERS
trust in Swarovski's products.
*Crystal glass and all other materials containing 0.009 % lead or less.
COMPLIANCE SERVICE
Oeko-Tex® Standard 100 Class II
Assessments regarding substance
(direct contact with skin) certification
limitations as well as compliance
creates confidence in chemical safety
information and advice to support
COMPLIANCE SERVICE
SAFET Y SOLUTIONS
of textile applications.
customers in complying with relevant
laws, regulations, and voluntary standards.
INFORMATIONSwarovski offers a comprehensive range of services,
tailored to customers' requirements, for the application of Swarovski products.
APPLICATION MANUAL
This Application Manual offers extensive information on the various Application Services provided by Swarovski.
Thanks to their outstanding quality, and with the help of specially developed application techniques, Swarovski products can be processed easily and quickly to produce a high-quality finished product. The processes involved are described
in this manual on a step-by-step basis, with photos and illustrations.
Each application method contains detailed information on the following areas:
Swarovski products that are suitable for the application technique in question
Machines, Tools, and Aids
List of machines, tools, and aids necessary for application
Selection of suppliers that sell these machines, tools, and aids
Detailed description of the entire application process and the product-specific procedure.
Furthermore, the Hotfix Selector outlines extensive application parameters for suitable product and carrier material combinations
Useful Information
Advice and tips on working with Swarovski products
A checklist of typical application problems, along with possible causes and recommendations on avoiding them (in each chapter these are marked with a
Extensive care instructions and further information on laws, regulations, norms, and standards are featured at the end of the manual.
APPLICATION ONLINE : SWAROVSKI.COM/PROFESSIONAL
All the information contained in this manual is regularly updated on the Swarovski products business website (SWAROVSKI.COM/PROFESSIONAL). In addition, application techniques are demonstrated through animations and videos. The site is an excellent way to find out about Swarovski's application services and application techniques.
To gain access to the restricted section of the business website, please contact your local Swarovski representative.
APPLICATION SERVICES
Swarovski offers a comprehensive range of services, tailored to your requirements, for applying Swarovski products. In doing so, the company aims to meet the needs of each industry, and to jointly offer flexible and integrated solutions.
Technical enquiry service
Compliance service Technical customer support – field services Application partner network
Technical enquiry serviceAvailable worldwide, the technical enquiry service can help you in the fol owing areas: Product information Technical drawing Care instructions Information on industry standards Individual application tests based on customer samples Information on machines, tools, and aids
Compliance serviceThe worldwide available compliance service can support you in the fol owing areas: Certificates Information on laws and regulations Compliance information of Swarovski crystals Compliance statement to customer-specific requirements
For further information, please contact your local Swarovski office.
General Information
Technical customer support – field services
Swarovski imparts its crystal application expertise through customized Crystal Application Workshops, Crystal Application Consultancy, Troubleshooting, and Technical Assessments. These can take place either on customers'
premises or at Swarovski locations. The focus is always on customers' individual needs, the efficient use of Swarovski products, and on the quality of the crystal application.
Our services have been created to take advantage of our comprehensive crystal application expertise in the following areas: mastery of the relevant techniques, technical knowledge of Swarovski products, process-engineering competencies, and our experience of crystal application equipment, together with our product manufacturing knowledge of various industries.
Service results (dependent on the particular individual service package):
PREVENTION OF INCREASED DEVELOPMENT COSTS THROUGH TECHNICAL INPUT IN:
The correct choice of Swarovski products The correct technical design The correct application technique The correct integration of an application process into the entire process landscape Application process set-up
PREVENTION OF COST COMPLAINTS THROUGH TECHNICAL INPUT IN:
The correct positioning and arrangement of Swarovski products Learning how to check the quality of crystal applications Suitability of the customer's equipment, tools, and aids
PREVENTION OF INCREASED STAFF DEVELOPMENT COSTS THROUGH:
Staff training in appropriate application techniques Building your technical knowledge base, thereby enabling you to be self-sufficient
Application partner network
As a company with a global sales network and deep understanding of the market, Swarovski has comprehensive knowledge of various application companies and their services from around the world.
Based on this knowledge, Swarovski has developed a global application partner network. These partners offer a wide
range of technical and product-related services, as well as tailored production solutions. In order to qualify and to get
access to the application partner network, certain criteria with regard to application techniques, know-how as well as product assortment need to be fulfilled by the application partners.
Application partners can assist you with a variety of application techniques, such as gluing, Hotfix application, sewing, embroidery, and mechanical application. In addition, many partners can carry out technically complex solutions, such as Flat Back Leather and the automated, mechanical application of Rivets. The services offered by our partners range from product and design consultancy, to prototyping and carrying out production, and make up a key component of our customer focus.
Should you require a professional partner to assist you in applying items such as Flat Backs onto interior, Transfer Motifs onto T-shirts, Rivets onto belts, or Plastic Trimmings onto jeans, the "Application Partner Platform" or your local Swarovski office can offer guidance.
Application Partner Platform (APP)
The Application Partner Platform enables you to find the right application partner swiftly and easily, wherever in the world production may be taking place. Through a tailored "search function", you can send out a specific, detailed request (e.g. searching for a specific country, an application technique, or products) to select partners around the world.
The platform is made up of two core areas – "Find a Partner" and "Become a Partner":
Find a Partner
Using the search function, this area enables you to locate the best application partner for your application work. You are immediately provided with a list of application partners, which you can download and save. If you use the search function for a specific enquiry regarding an application service, you receive detailed information from the application partners contacted.
Become a Partner
If you are interested in becoming an application partner yourself, the "Become a Partner" section contains key information on the requirements and an application form to complete. Your local Swarovski office will then contact you as soon as possible.
Access to the Application Partner Platform: Part of the "Application Partner Platform" is located in the restricted area of the business website SWAROVSKI.COM/PROFESSIONAL. Under "Design & Application" "Application & Manufacturing" you will find access to the Application Partner Platform.
For access to the restricted area of the business website and for further information, please contact your local Swarovski office or register online on the business website.
General Information
GENER AL PRODUCT INFORMATION
This list offers an overview of Swarovski products that are suitable for the application methods described. Product categories/
descriptions are based on the 2014 Collection.
Round Stones are loose crystal elements. Most of them are pointed on the reverse side, making them
easy to apply in either metal claw settings or pre-set cavities in die-cast metal alloys. The assortment features a wide variety of different cuts, the most innovative one is the XIRIUS Chaton.
Fancy Stones are offered in numerous shapes ranging from classical gemstone-inspired cuts to progressive trend cuts. They come in a huge assortment of different sizes and colors. Showing either
Fancy Stones & Settings
a faceted or flat reverse side, Fancy Stones can be glued into pre-cast cavities or used in metal settings. Their precision-cut facets ensure the highest brilliance and endow design ideas with a unique sparkle.
Beads offer the highest standard available on the market. The high-quality precision cutting and the clear through-hole achieve high brilliance and clarity. Rounded hole edges reduce the wear on thread
and increase the durability of designs. The assortment is divided into classic, romantic, and progressive shape characteristics. They are available in the latest fashion colors, effects, and cuts.
The BeCharmed assortment, from Beads, Crystal Pearls, Pavé, and Rondelles, to Stoppers and Pavé Balls in a brilliant array of colors and effects, offers unlimited combination possibilities. All products
BeCharmed & Pavé
of this unique line feature a high-quality stainless steel part with Swarovski branding and a 4.5 mm-diameter hole, which is the standard size for existing charm concepts, making BeCharmed pieces ideal collectibles.
Crystal Pearls are perfect replicas of genuine pearls. They are made of a unique crystal core covered with an innovative pearl coating, which features a flawless, silky smooth, rounded surface. They are
available in a variety of shapes, sizes, and colors and are delivered loosely threaded or, if desired, also knotted.
Pendants have timeless elegance and are available in a large range of classical and avant-garde cuts and shapes, as well as in many colors and effects. Pendants offer a whole range of design possibilities
for different segments thanks to their easy application, with the hole on top requiring only a jump ring/pinch bail with a chain or cord.
Flat Backs No Hotfix are loose crystal elements backed with platinum foiling for extra brilliance and
Flat Backs No Hotfix
protection. These Flat Backs are easy to apply to a variety of carrier materials using standard one- or two-component glues. They are available in a multitude of sizes, colors, shapes, and cuts.
Flat Backs Hotfix are loose crystal elements with a flat reverse side that has been pre-coated with a heat-sensitive glue. These Flat Backs can be easily applied to a large range of textile carrier materials
Flat Backs Hotfix
using heat to produce a durable and long-lasting crystal effect. Flat Backs Hotfix are available in a multitude of colors, shapes, and cuts.
Sew-on Articles are loose crystals that can be easily sewn (either by hand, or with a standard domestic or industrial embroidery sewing machine) onto any type of textile or accessory. Sew-on Articles come
in two- or three-hole varieties, including round, oval, and triangle holes for use in a wide range of decorative applications for fine embroidery or even jewelry. Lochrosen are crystals with just one hole. Sew-on Articles have rounded edges on the hole entry and exit areas to guarantee thread protection.
Self-adhesive Elements such as Crystal-it, Crystal Fabric-it, Crystaltex-it Chaton or Crystal Rocks-it are eye-catching and innovative products that come ready-to-apply. They are pressure-sensitive
Self-adhesive Elements
and self-adhesive. When applied to paper and solid surfaces, they can create elegant, romantic, or sporty designs.
Transfers are ideal for Hotfix application on all kinds of textiles. They are available in a large range of motifs and numbers of rows, which are made up of different articles from the Flat Back Hotfix
assortment. Featuring designs from the in-house design team, they can comprise XIRIUS and XILION Roses, or Creation Stones, as well as Metallics and Cabochons.
These versatile products open up a multitude of creative design possibilities through their numerous application techniques. They combine elegant crystals from Swarovski that can be applied using Hotfix
Synthetics Hotfix
technology with synthetic carrier materials. They are ideal for use in the textile, interior design, jewelry, and accessories segments.
Plastic Trimmings are plastic carrier materials with integrated crystals. These multi-functional products
Plastic Trimmings
can either be hand- or machine-sewn or glued onto various surfaces. The range of bandings not only offers a color selection of chatons, but also a variety of casing colors.
Crystal Buttons can be used in exactly the same way as standard buttons. The assortment of available buttons ranges from those for shirts, blouses, jackets, and coats, to buttons for denim and accessories.
Buttons, Fasteners & Zippers
They are suitable for hand and mechanical application. Zippers from our assortment are unique because the crystals are integrated into the zipper teeth, allowing them to be used in the same way as standard zippers.
Metal Trimmings are forward-integrated metal products. They can be sewn by hand or machine and
mechanically applied onto different fabrics or other materials. Metal Trimmings are bestsellers among
the textile, shoe, and accessories segments because their wide range of application possibilities ensures that they can be used in a multitude of different ways.
Crystal Mesh is a flexible metal mesh carrier with integrated loose crystals. The product is available in
a wide range of colors and casings, either as a Hotfix version, which can be applied using heat, or as a
No Hotfix version that can be hand- or machine-sewn.
These products are metal chains and findings that can integrate either Round or Fancy Stones and Beads into any creative design. They can be divided into seven sub-categories: Single Stone Settings,
Cupchains & Findings
Cupchains and Brass Components, Multi Stone Settings, Channels, Metal Buttons, Rondelles, and Linked Findings. Each of these groupings is available in a wide variety of shapes, sizes, colors, and platings.
Crystal specifications
Pavilion (rear side)
Rear view (Pavilion)
Foiling is the process of mirror coating the reverse side of the crystals.
Silver Foiling (A)A silver mirror finish for XIRIUS and XILION Hotfix articles only.
Platinum Pro Foiling (F)A silver mirror finish that is coated with a platinum colored protective layer of highest quality. The Platinum Pro Foiling is not only resistant to environmental damage from chlorine, salt water, and perfume – it can also withstand processes such as soldering and electroplating, giving it unprecedented durability (e.g. art. 4120).
Aluminum Foiling (M)An aluminum mirror finish is applied using a vacuum coating process (e.g. art. 2855 Flat Back HF).
Protective Layer (P) for Beads and PendantsProtective layer is a transparent lacquer system that is applied over the effects. This lacquer is designed to protect the effects from scratches, fingerprints, and other damage and also helps to prevent moisture that can lead to corrosion (e.g. from perspiration) penetrating into the effect layer when jewelry is designed to incorporate Crystal Stones that are not set in casings/settings.
General Information
Vacuum Coating Effects
LacquerPRO Effects
Vacuum coating processes on the surface of the crystal
A premium opaque varnish which is applied to the reverse
produce either a special surface or a translucent effect,
side of the crystal instead of foiling, resulting in an
according to the application methods used.
Please find below a list of all Swarovski effects followed by
Effect Code
an explanation of the special vacuum coating processes.
Surface Effects
(Vacuum coating on the surface of the crystal)
Effect Code
Variations on Surface Effects
Comet Argent Light
Both sides of the stone are treated with an effect
(e.g. art. 5000AB 2).
Hematite (only on Jet)
Effects on three sides of a cube shape
(e.g. art. 5601 AB B).
The effect is used in reverse. A surface effect
Metallic Light Gold
is used like a translucent effect (e.g. art. 2420
NoHF SSHA V - Silver Shade on the reverse side).
Nut (only on Jet)
Only a part of the stone is treated with an effect
(e.g. art. 4869 HEL Z).
Scarabaeus Green designed by JPG
FC (Full Coated)
Improved technology allows for the perfectly homogeneous, all-round application of high-intensity metallic effects in the Bead assortment
Translucent Effects
(art. 5000).
(Vacuum coating on the reverse side of the crystal, effect shines through the transparent crystal)
CAL´V´SI & CAL´VZ´SI
Effect Code
The effect CAL (Comet Argent Light) is also used
as a mirror coating on the reverse side of the
crystal instead of standard foilings (A, F, .) in
special cases (e.g. art. 2035).
Article with partly (PF) or fully frosted (FF) surface
(e.g. art. 2611/G)
Patina Effects(Partial coating of the correspondingly modified effects)
Innovative technology allows for the partly coated
Effect Code
application of adapted effects. Its historical edge
and "used" look give it a certain timelessness,
without losing its crystalline appearance
(e.g. art. 2034).
Special Surface Effects
Swarovski has been able to achieve various special surface effects by using special chemical and mechanical processes on the surface of the crystals.
Effect Code NameMAT Matt
The Matt Finish effect is achieved by performing a chemical matting process on the entire surface of the crystal. Small variations in the size of the articles may occur as a result of this chemical process. Using a special process, the outer facets of Flat Back Roses can be blackened. The Cosmojet effect is only possible for the color Crystal (001).
General Information
Crystal Silver Shade
Crystal Moonlight
Crystal Light Chrome*
Palace Green Opal
Crystal Aurore Boreale
Crystal Comet Argent Light*
Provence Lavender
Crystal Luminous Green*
Crystal Silver Night**
Crystal Golden Shadow
Crystal Metallic Sunshine*
Crystal Rose Gold*
Crystal LacquerPRO Effects
Crystal Powder Yellow*
Light Colorado Topaz
Crystal Astral Pink
Crystal Powder Rose*
Crystal Red Magma*
Crystal Powder Blue*
Crystal Antique Pink*
Crystal Powder Green*
Crystal Vitrail Light**
Crystal Powder Grey*
Crystal Paradise Shine
Caribbean Blue Opal
Crystal Vitrail Medium**
Crystal White Patina
Crystal Volcano**
Crystal Rose Patina*
Light Smoked Topaz
Crystal Lilac Shadow
Crystal Silver Patina*
Crystal Heliotrope**
Crystal Gold Patina*
Crystal Bermuda Blue**
Crystal Black Patina*
Crystal Metallic Blue*
Crystal Blue Shade*
Crystal Scarabaeus
Marbled Light Grey
Marbled Terracotta
Crystal Iridescent Green*
Crystal Metallic Light Gold*
Crystal Bronze Shade*
This color range offers a wide choice of traditional Swarovski crystal colors.
Exclusive Colors:
This color range is offered exclusively by Swarovski.
The listed colors and effects are based on the Color Chart for Round Stones (2016).
The standard assortment of colors and effects may vary per product group. Slight changes in shades are unavoidable. Colors may vary according to cut and shape.
The plating resistance of effects is tested according to Swarovski's plating guidelines (SWAROVSKI.COM/PROFESSIONAL). Customers are advised to carry out their
own tests if customers' plating parameters diverge from Swarovski plating guidelines. Details for parameter settings can be found on page 19.
Crystals are not resistant to plating and similar processing.
Crystals are resistant to plating only if they are foiled.
*** The color Indian Siam is available only for a specific size range. Please refer to the current Collection.
**** Designed by Jean Paul Gaultier
Testing the plating-resistance
For testing the plating-resistance of effects, the following parameter settings have to be considered:
Setting up the stand
Electrolytic degreasing
t < 1 min, 3 A/dm2, pH < 12, T < 45 °C (113 °F)
t = 30 sec, T < 25 °C (77 °F)
t < 20 sec, pH ∼ 1
t = 30 sec, T < 25 °C (77 °F)
Bright copper plating
t < 15 min, 3 A/dm2, pH < 1, RT
t = 30 sec, T < 25 °C (77 °F)
Palladium interim coating
t < 5 min, 1 A/dm2, pH < 8, RT
t = 30 sec, T < 25 °C (77 °F)
t < 5 min, 1 A/dm2
Note: Swarovski cannot warrant the resistance of effects when the parameters as set out above are changed. Swarovski's
declaration of resistance does not discharge customer from carrying out its own tests of the suitability for the intended finishing of products. The use and processing of these techniques and products are solely the user's responsibility.
General Information
Various measurement abbreviations are used to classify the jewelry stones.
Pearl Plate (PP), Sieve Size or Stone Size (SS)
Metric figures in millimeters for crystal components and
for round crystals.
geometric forms.
SS 459.85– 10.19 mm
10.19– 10.54 mm
10.54– 10.91 mm
SS 387.93–8.16 mm
SS 6515.47–15.72 mm
SS 418.67–8.95 mm
SWAROVSKI PRODUCTS AND SUITABLE APPLICATION TECHNIQUES
Fancy Stones Fancy Stones
BeCharmed & Pavé
Flat Backs No Hotfix
XILION Rose & XIRIUS Rose
Framed Flat Backs
Creation Stones Plus
Self-adhesive Elements
XILION Transfers & XIRIUS Transfers
Creation Transfers
Creation Transfers Plus
Diamond Transfers
Metallic Transfers
Crystal Rocks & Crystal Fine Rocks
Decorative Bandings
Plastic Components
Buttons with Plastic Shank
Snap Fasteners & Decorative Buttons
Inset Snap Fasteners & XIRIUS Flat Back
Buttons with Metal Shank
Chaton & Flat Back Bandings / Motifs
Rivets (Crystal Pearl, Square, Chessboard,
Roses & Chaton Montées
Rose Pins, Chessboard Pins & Rhombus Pins
Cupchains & Findings
1 These products are not suitable for sewing with a sewing machine 2 Art. 3129 3 Not suitable for Crystaltex Chaton Bandings 4 Art. 50 002, 50 003, and 50 004 (single-row) 5 Crystal Fine Mesh is not suitable for sewing with a sewing machine
General Information
SOLDERING, PLATING, AND STONE SETTING
Swarovski offers an ideal product selection for soldering, allowing for
simple and problem-free production of state-of-the-art jewelry pieces and accessories. Further techniques such as plating and stone setting complement the comprehensive and diverse application options offered by Swarovski.
PRODUCT OVERVIEW
The following products are suitable for soldering, plating, and stone setting:
Flat Backs No Hotfix
Cupchains & Findings
* It is recommended to use the unplated versions (Z).
MACHINES, TOOLS, AND AIDS
The following machines, tools, and aids can be used for soldering Swarovski crystals:
Micro soldering kit
Propane gas burner
It is recommended that solder wire with a flux
Solder paste containing flux must be applied
Solder pellets should be placed in an acid flux
core is used, which guarantees an even flow
at exactly the right spot to create a clean
before being used. This ensures that the solder
will flow correctly.
Polishing machine
J-board, express cement
Protective eyewear
This list provides an overview of selected suppliers worldwide.
MACHINES / TOOLS / AIDS
Micro soldering kit
Propane gas burner
Siegfried Remschnig
SRA Soldering Products
SRA Soldering Products
SRA Soldering Products
SRA Soldering Products
SRA Soldering Products
J-board (solder mold)
SRA Soldering Products
Express cement (solder mold)
E.H. Ashley & Company, Inc.
Franz Simm Metall- und Zinkdruckgusswaren GmbH
Josef Bergs GmbH & Co. KG
Application techniques
A solder mold is required to reproduce jewelry pieces. First the original model of the jewelry piece is soldered. This is then
used to make an impression in a suitable impression material (J-board, express cement). Depending on the size of the jewelry
piece and mold medium, this impression can be made several times.
1 Solder the original model.
2 Strengthen the rear of the original model
3 Press the original model into a suitable
4 Once the material hardens, the original
model can be removed.
Note: The solder mold must be designed in such a way that hardly any pressure is needed to position the
Cupchain segment into the mold. The crystals may be damaged if there are high levels of mechanical stress on the cups, or if they are deformed.
Materials and aids should be clean, and particularly free of any grease, to ensure proper application. When
soldering and plating, adequate ventilation is essential. In addition, it is recommended that protective clothing,
protective eyewear and protective gloves are worn in line with the manufacturer's safety information sheets. Wearing
protective gloves also prevents aids from getting dirty.
Selecting the optimum solder and flux
When selecting solder, the working temperatures and flow characteristics are particularly important. Solder is available
from various manufacturers in wire form, with or without a flux core, as a paste and as pellets.
Only soldering alloys with a working temperature up to 280 °C (536 °F) should be used for soldering Cupchains. The higher the working temperature of the solder material used, the more precise workmanship and exact temperature control are necessary to avoid damaging the crystal and the foiling.
When soldering Cupchains, solder wire with a flux core is more suitable. If solder pellets are being processed, or the wire used does not have a flux core, the flux should be adapted according to the solder manufacturer's instructions, while any corrosive effects on the foiling should be checked via pre-testing. These effects should be assessed after plating, as damage done during soldering is often only visible at this point.
For soldering Cupchains we suggest using one of the following lead-free solder wires:
96.5% Sn, 3.45% Cu,
Soldering time and temperature
The right flame size and the time it is applied are important criteria when manufacturing soldered Cupchain pieces. The size of the flame must comply with the instructions for use provided by the tool's supplier. Only heat the part of the jewelry piece in which the solder should flow. If the flame is held too long on the jewelry piece, the piece and the crystals may become overheated and therefore damaged or destroyed.
Note: A sudden drop in temperature after the soldering process should be avoided (e.g. shock cooling), as this could
damage the crystal (e.g. chipping).
Application techniques
Color during soldering
1 Too low temperature
2 Optimum temperature
3 Too high temperature
Color after soldering
1 Too low temperature
2 Optimum temperature
3 Too high temperature
Optimum soldering joint
The width of the joint to be soldered should be between 0.05 mm and 0.2 mm. If the joint is wider than 0.2 mm, the solder will not fill the joint sufficiently. A joint that is too narrow will also not contain enough solder to make it strong and neat.
Optimum solder quantity
The right amount of solder ensures strong and clean soldered joints, which can then be cleanly plated. Correctly applied solder flows into the joints of the jewelry piece and provides a strong connection. Either too much or too little solder can damage the creations or result in unwanted discoloring of the crystal.
Exact amount of solder
Too little solder
The solder is drawn into the solder gap via
Too much solder results in the cup backfilling,
Too little solder means the soldering gap is not
capillary action.
with the hot solder damaging the foiling. This
completely filled, and the joint is weakened.
damage creates a corroding surface following
plating, and the foiling is destroyed. As such,
these types of soldering errors are only really
visible after plating.
1 Cut the Cupchain to the required length.
2 Put the Cupchain in the solder mold.
3 Solder the required spots.
4 Remove the soldered Cupchain from the
Alongside the application methods outlined in this manual, Swarovski products can also be employed using metal settings. Crystals can be set manually (using pliers, metal spatulas, or punching tools) or by machine.
According to how the crystals are integrated into the metal settings, there are various types of settings, both plated and unplated. Whenever possible, the crystals should be set before plating the settings. The Swarovski assortment features products like Cupchains that have already been set, as well as Settings for Fancy Stones. Crystals can be set after plating as well, depending on the shape and geometry of the jewelry. Please be aware that a selected range of Swarovski crystals cannot be plated. For further information on this, please see the current Swarovski Crystal Collection.
Application techniques
Settings for gluing
With bezel settings, the crystals are bezelled in
With prong settings, Swarovski crystals are held in
In this type of setting (crystal) elements are
to remain in the cup.
position by claws. In most cases there are four
prongs. Settings with flaps have significantly
broader claws. The advantage here is that the broader claws are much less likely to damage very sensitive carrier material.
1. Depending on the shape and size, the cup is held using tweezers, flat nose pliers, or flat head pliers, without deforming it. 2. Place the crystal in the setting using a pair of tweezers or vacuum tweezers.
3a. Bezel setting: Press the cup shut using a setting closer. Setting closers are available from jewelry suppliers. 3b. Prong setting: The prongs of round cups can be pressed in place using a suitable setting closer. For all other forms, the
prongs are individually closed in opposite positions, using a suitable pressing tool.
Note: After setting, the crystal should still be slightly movable in the setting. The setting must be constructed so that the
crystal can be positioned into it without damaging the foiling. When settings are too tight or prongs are bent, the foiling or the protective lacquering can be damaged, possibly resulting in corrosion. If the setting is closed too strongly, the crystal can be damaged.
Application methods for set crystals
The following application possibilities are available for already set crystals:
Sew-on cups are applied by sewing onto
These types of settings are suitable for
textiles and leather. There are holes in the cups
soldering with other cups and/or with
for the thread to pass through.
Cupchains. They are mostly used in the jewelry segment.
Mechanical application
With this special type of setting, the set crystal
Settings that can be used as a pendant have
is applied onto the textile using claws. For more
an eyelet at the top, to which a chain can be
information please consult the corresponding
attached. Settings with two eyelets can be
attached to other elements.
Working with end connectors (brass components)
Plated Cupchains and Findings can easily be combined with end connectors (brass components) in order to create striking pieces of jewelry.
The end connectors can be attached to the end of the Cupchain with flat-nosed pliers and interconnected by either jump rings or lobster claws.
To avoid corrosion, soldered items should be cleaned as soon as possible after the soldering process. This will make the plating process significantly easier. Care must be taken when using mechanical polishing devices. Polishing media that are too hard or drums that rotate too quickly can damage the items and the crystals. Check the quantity, the polishing agents and time, the rotating speed, and the height of the fall, in order to keep mechanical stress levels as low as possible. In order to preserve the high quality of the creations, we recommend not using organic solvents and not exceeding a maximum temperature of 100 °C (212 °F).
Removal of excessive solder alloy by polishing
Application techniques
Plating serves to finish the jewelry piece. During this process, metallic coatings are electrolytically added to the surface
of the material. The process can only be carried out if the material to be plated is conductive. During the design process,
please ensure that individual colors and coating effects can withstand plating. For further information, please see the color overview in the current Swarovski Crystal Collection.
The most important criteria for an excellent finishing process are:
Selecting reliable electrolyte suppliers who offer good service and who can provide detailed operating instructions
Selecting suitable high performance electrolytes
Careful maintenance of the unit and the electrolytes Using the recommended settings for plating Cupchains
Note: Strong alkaline solutions, long exposure times in alkaline baths, the incorrect use of ultrasound, and high current
densities usually lead to chemical and/or mechanical damage to crystals.
Short descriptions of the processing steps
Hot degreasing: Here, most of the surface pollution (e.g. dirt, grease, soldering flux) is removed.
Electrolytic degreasing: Only cathodic degreasing, suitable for brass and non-ferrous metals, is recommended for fine
cleaning Cupchain jewelry.
Pickling: This part of the process serves to remove oxidization from the metal and also the remains of any scale left from
the soldering process.
Cyanide copper plating: This processing step serves to improve adhesive strength and conductivity.
Pyrophosphate copper plating: Like cyanide copper plating, this process improves adhesive strength and conductivity.
The advantage is that the process does not involve cyanide, though the disadvantage is that higher current densities and longer exposure times are required.
Bright copper plating: The use of sulfuric bright copper plating is recommended because of its excellent ability to cover
surface flaws and create an even finish.
Palladium coating: Palladium is presently the only recommended replacement for nickel since the bronze electrolytes
currently available on the market can, through their extreme alkalinity, lead to damage of the foiling.
Silver coating: Shiny silver coatings are usually separated from cyanide solutions that contain alkali silver (I)-cyanide,
alkali cyanide, alkali carbonate, and organic and/or inorganic additives.
Gold coating: It is recommended to use phosphorus or citric acid electrolytes (pH ∼ 3 – 4), which contain potassium gold
Rhodium coating: Sulfur or phosphoric acid based electrolytes are used for rhodium plating, from which shining, nearly
silver-white layers can be applied.
Tarnish protection – Temporary protection against tarnishing: These are based either on wax mixtures in organic solvents or
long-chained sulfuric organic compounds, which can be used as wet-on-wet aqueous emulsions.
– Permanent tarnishing protection systems: Cataphoretic lacquering systems have been proven especially effective as
a longer lasting protective system for Cupchain jewelry. They have the advantage over conventional dipping and spray lacquers based on acrylic or zapon varnish (cellulose lacquer) in that only the conductive surfaces are very evenly coated while the isolated facets of the crystals remain uncoated.
Parameter settings for plating Cupchains
Setting up the stand
t < 5 min, pH < 12.5, T < 55 °C (131 °F)
t < 30 sec, T < 25 °C (77 °F)
Electrolytic degreasing
t < 15 – 20 sec, 3 A/dm2, pH < 12.0, T < 45 °C (113 °F)
t < 30 sec, T < 25 °C (77 °F)
t < 15 – 20 sec, pH < 1
t < 30 sec, T < 25 °C (77 °F)
Cyanide copper plating
t = 1 min, 2 A/dm2, pH < 10.5, T = 60 °C (140 °F)
Pyrophosphate copper plating
t = 3 min, 1 A/dm², pH = 9.2, T = 55 °C (130 °F)
t < 30 sec, T < 25 °C (77 °F)
Bright copper plating
t = 5 – 6 min, 3 A/dm2, pH < 1, RT
t = 1 – 2 min, 1 A/dm2, pH = 8-9, T = 25 – 30 °C (77 °F-86 °F)
t < 1 min, 2 A/dm2, pH < 12.0, RT
t < 30 sec, T < 25 °C (77 °F)
t < 30 sec, T < 25 °C (77 °F)
Tarnish protection
t < 30 sec, T < 25 °C (77 °F)
t < 30 sec, T < 25 °C (77 °F)
t < 30 sec, T < 25 °C (77 °F)
Hot rinsing and drying
T = 50 °C (122 °F)
Hot rinsing and drying
Hot rinsing and drying
T = 50 °C (122 °F)
T = 50 °C (122°F)
AN ADDITIONAL EFFECT OR PROTECTIVE LACQUERING CAN ALSO BE APPLIED.
Application techniques
DIRECTIONS FOR JEWELRY MANUFACTURING
This section offers a brief overview of the ways in which Swarovski products can be integrated into jewelry design software, and a summary of the two most important production techniques for jewelry: rubber mold and lost wax.
Jewelry design software
Leading software manufacturers offer special programs with three-dimensional display possibilities for the design of jewelry
and accessories. These 3D-design programs feature a whole range of functions that simplify and support the design process
and therefore also the entire production process.
Special software solutions that have integrated a range of digitally processed Swarovski crystals in their programs are
already available (www.3design.com). These can be simply and quickly integrated into any design, thus allowing the designer to work with Swarovski crystals right from the beginning of the design phase.
Production process
RUBBER MOLD PROCESSES
This process is widely used in the production of fashion jewelry. Tin alloys are mostly used here, and the biggest advantage of this procedure is the favorable price of the required tools.
1 Several original models are shaped out
2 These original models are pressed into
3 Channels are cut in the rubber plate for the
of metal, which must already exhibit an
a rubber mold. The rubber mold gets
casting process.
excellent surface quality. The expected
vulcanized to create a rubber casting model.
shrinkage during casting must be taken into account.
4 The completed rubber molds are pressed
5 After cooling and removing from the mold,
6 The cast model achieved by this process is
together and filled with the molten metal
the casting channels are cut off.
ground and polished in preparation for the
alloy during rotating (centrifugal casting
plating process.
The lost wax process is used for metals with a higher melting point, for example brass, silver, and gold.
1 Production of a prototype, e.g. through rapid
2 The prototype is either formed with silicone
3 The already produced mold is injected with
prototyping; the better the surface quality is
or vulcanized between raw rubber plates.
molten wax by a wax injector to create a
here, the better the casing will be later. The
expected shrinkage during casting must be
taken into account.
4 The wax forms created this way are each
5 The tree is now placed into a cuvette, the
6 The wax is melted out after the implantation
melted onto a wax tree format with a wax
holes are glued up and it is embedded in
paste has hardened. Remaining wax is burnt
welding device. The trunk of the wax tree
implantation paste under vacuum and vibration.
out in a kiln. The wax must be completely
later serves as the casting channel.
burnt out, leaving only the clean cavities.
7 While it is still hot, the cuvette is filled,
8 After casting, the hot cuvette is plunged into
9 After the jewelry pieces are removed
under vacuum, with the molten metal.
cold water. The casting tree is then cleaned.
from the casting tree, they are finished by
Because of the porosity of the form, the
grinding and polishing and pre-treated for
molten metal fills every part of it.
the galvanization process.
Application techniques
QUICK ASSISTANCE
The following table outlines common problems and their causes when soldering, plating, and stone-setting Swarovski products, and offers advice on how to avoid them. Further details and more extensive descriptions can be found in the section marked
Metal components:
The solder joints crack.
The jewelry piece has restricted movement.
The metal surface is defective.
The metal surface is uneven.
Defective finishing on the soldered areas.
Corrosion occurs on the metal.
CrystalThe crystal chips off.
The crystal becomes discolored.
Too little solder is used. This weakens the solder joint,
Use more solder.
as the soldering gap is not completely filled.
Too much solder is used. A large solder joint can result
Use less solder, especially in the areas close to the
in cracks, because any force applied to the piece
moving parts. Too much solder at these parts restrict
directly affects the solder.
their flexibility.
The flow of the solder is insufficient.
The following factors contribute to a sufficient flow of solder: The flame needs to be strong enough so that both solder
and cup can heat up to the required working temperature.
To make sure the flux cannot vaporize, the soldering
temperature must not exceed 280 °C (536 °F). A vaporized flux means that the solder is not able to cover the metal surface.
The melting temperature of the solder must not be
higher than 280 °C (536 °F).
The metal surface, solder, flux, or solder mold is dirty.
Special attention must be paid to use clean (and above all grease-free) metal surfaces.
Exposure to the finishing process has been too long.
The exposure time for functional and flexible elements should be kept as short as possible. Optimizing the polishing processes and the use of high quality electrolytes is also recommended.
Insufficient cleaning after soldering.
Incorrect cleaning has a negative impact on the finishing process. Carefully check the cleaning process.
Poor quality of polishing. The metal surface shows
Carefully polish the product and take care that the processor
irregularities like burns or an orange color.
plating baths are set up correctly.
Unsightly finishing on the solder areas can have
Carefully follow the soldering steps described in this chapter.
several causes: incorrect soldering insufficient cleaning after the soldering process the use of sulfuric acid in the pickling process
(if lead-containing solder has been used)
the absence of or incorrect use of copper plating
Insufficient rinsing or using contaminated rinsing water can
The transfer times between the individual stages of the process
cause tarnishing or corrosion.
should be kept as short as possible. Rapid tarnishing of silver can be prevented by using effective tarnishing protective systems (e.g. coatings, wax, lacquer etc.).
Poor quality of solder mold.
The solder mold must be designed in such a way that hardly any pressure is needed to position the Cupchain segment into the mold. The crystals may be damaged if there are high levels of mechanical stress on the cups, or if the cups are deformed.
Thermal shock during the soldering or cooling process
Avoid extreme differences in temperature during and after the
can cause tension in the crystals.
soldering and cooling process.
When using polishing drums, the surface of the crystals can be Mechanical stress levels should be kept as low as possible. damaged through hard polishing components in the rotating
Check the quantity of articles used, the polishing agents and
time, as well as the rotating speed and the height of the fall.
Using barrel plating can damage crystals in heavy or sharp
In general it is recommended that Cupchain jewelry should be
Cupchains due to the Cupchains‘ size or shape.
finished on a plating rack. If using a barrel plating, choose the best type of drum and optimize the rotation and the fall height.
When the drum is between the different stages of the finishing
process and contains no liquid, the items being plated inside
the drum may damage each other.
The soldering temperature is too high.
If the soldering flame is too strong or the soldering times are
too long, there is the danger to overheat the solder joints. This
can damage the crystals. It can be helpful using a solder that melts at a lower temperature. For more details see the temperature information on page 27 – 28.
Too much solder is in the cups. This can damage the crystals‘
To make sure the right amount of solder is used, remove one
foiling and subsequently leads to discoloring.
crystal from the cup. If there is any solder left in the cup, reduce the amount of solder. This can be achieved by using a solder wire with a maximum diameter of 1 mm or by reducing the time the solder is in contact with the cups.
Incorrect cleaning with ultrasonic can damage the foiling of
Take care not to use the ultrasonic too intensively or for too
the crystals.
Faults occured during the finishing process.
Check the alkalinity, current density, exposure times, and temperatures of the plating baths used. Further mistakes could be incorrect rinsing and post processing techniques.
Application techniques
GLUINGSwarovski products can be glued to a wide range
of materials in a variety of application areas.
The greatest quality is ensured by following the entire
PRODUCT OVERVIEW
The following products are suitable for gluing:
Flat Backs No Hotfix
Self-adhesive Elements
Synthetics Hotfix
Plastic Trimmings: Basic Bandings
Metal Trimmings: Chaton & Flat Back Bandings/Motifs, Spike Bandings
* Plastic Trimmings made of PE or PP are not suitable for gluing.
MACHINES, TOOLS, AND AIDS
The following machines, tools, and aids can be used for the various processes involved in gluing Swarovski products:
CNC milling machine
Twist drill 90°/
Twist drill 95°/
for XILION Chatons
for XIRIUS Chatons
Test Pen (art. 9030/000)
Precision balance
Protective eyewear
Dispensing syringes with dispensing tips
Application techniques
Two-component epoxy resin glue: 50 g cartridge
Two-component epoxy resin glue: 100 g tube
Two-component epoxy resin glue: 2 kg tin
(25 g component A, 25 g component B)
(50 g component A, 50 g component B)
(1 kg component A, 1 kg component B)
Two-component epoxy resin glue: 50 g
Two-component epoxy resin glue: 750 g box
cartridge (33.3 g resin + 16.7 g hardener)
(500 g resin + 250 g hardener)
Chaton Sieve for Chatons size PP 0 – PP 1
Chaton Sieve for Chatons size PP 2 – PP 20
Chaton Sieve for Chatons size PP 21 – SS 34
Vacuum pick-up system
This list provides an overview of selected suppliers worldwide.
MACHINES / TOOLS / AIDS
90° NC drill/milling cutter
Swarovski: art. 9030/000
Epoxy & Equipment Technology Pte Ltd
(with/without vacuum suction)
Hottemp (M) Sdn. Bhd.
I & J Fisnar, Inc.
PT. SKT International
Vacuum pick-up system
Epoxy & Equipment Technology Pte Ltd
I & J Fisnar, Inc.
Two-component epoxy resin glue
art. 9030, 50 g Cartridge, America, Asia, Europe
art. 9030, 100 g Tube, America, Asia, Europe
art. 9030, 2 kg Box, America, Asia, Europe
Two-component epoxy resin glue
art. 9030, 50 g Cartridge, America, Asia, Europe
art. 9030, 750 g Box, America, Asia, Europe
Mixing nozzle for CG 500 and CG 610
Swarovski: art. 9030/126
Araldite® adhesives
Huntsman International LLC.
3M™ Scotch-Weld™ adhesives
DELO Industrial Adhesives
ELASTOSIL® adhesives / MS Clear HS
LOCTITE® adhesives
Hobby Line Schmuckstein Kleber
C. KREUL GmbH & Co KG
UHU plus endfest 300
Tile glues / joint sealers
PCI Augsburg GmbH
Application techniques
MACHINES / TOOLS / AIDS
For Chaton size PP 0 – PP 1: art. 9030/003
For Chatons size PP 2 – PP 20: art. 9030/001
For Chatons size PP 21 – SS 34: art. 9030/002
DELO Industrial Adhesives
Heraeus Holding GmbH
Herbert Waldmann GmbH & Co. KG
Heraeus Holding GmbH
VWR International, LLC.
When gluing Swarovski crystals, optimal results are obtained by coordinating the entire application process. Following the application steps in the right order is very important. Experience has shown that the most common reasons for crystals becoming detached are inappropriate areas of application, poorly produced cavities, unsuitable gluing systems, and insufficient quantities of glue. Product-specific application instructions are detailed later in this section.
CHECKING SURFACE
CAVITY PRODUCTION
Many Swarovski crystals require cavities in order to be applied to materials. A properly produced cavity in combination with a suitable gluing system ensures a stylish, long-lasting application. The cavity makes it easy to glue properly and ensures higher protection of the crystal against mechanical and chemical stress.
There are several different production methods and cavity types. Always take into consideration the requirements and base material of the finished product when choosing the appropriate cavity, pre-treatment method, and kind of glue.
Production methods
Drilling is when materials are machined using a power drill and drilling tool. Milling is when materials are machined using a milling machine and milling cutter. Milling machines can be fitted with
appropriate tools depending on the materials, e.g. for working with metal and plastic, wood, or natural stone. Modern CNC machining centers offer the greatest precision and can be used to produce cavities of every shape necessary. Please note that when machining natural stone, ceramic, or glass, for example, special diamond-tipped tools must be used.
Water jet cutting allows materials to be separated via a high-pressure jet of water. Economic reasons make water jet cutting
machines ideal for certain crystal shapes that are integrated into flat materials. Please note that only end-to-end cavities can be produced in this way. In addition, materials that swell through water cannot be worked with. Absorbent materials must be fully dried before gluing the crystal.
Casting: To reproduce cavities, particularly in the jewelry sector, the cavities can be made when the metal component is
cast. When following this process, the cavities must be cut into the original model. To prevent the bottom of the cavity being rounded off, which would result in the crystal sitting too high, it is recommended that an additional indentation is made when producing the original model.
Further instructions on jewelry production can be found on page 34.
Application techniques
Depending on the Swarovski products used, various cavity types can be made using the different production methods.
Glue protectsthe foiling
The optimal cavity for a XIRIUS Chaton is produced at an angle of 95° – 98°, for a XILION Chaton at 90° – 93°. The cavity should have the same maximum diameter as the crystal plus at least 0.1 mm. The stone sizes available for Swarovski crystals can be found on page 19. For particularly large crystals with a prominent girdle, it is advisable to use an additional countersinking
process. Please find a cavity calculator on SWAROVSKI.COM/PROFESSIONAL.
Chaton casting cavity
For jewelry manufactured by casting, an additional indentation at the bottom of the cavity can be drilled to avoid a rounded tip, therefore preventing the crystal from being raised out of the cavity.
Flat Backs No Hotfix
Self-adhesive Elements
When gluing Swarovski crystals with a Flat Back, it is also advisable to create a cavity as
Crystal Fine Rocks
shown here. This cavity ensures that the crystal is better protected against mechanical and chemical stress. The depth of the cavity depends on the height of the girdle and the strength of the base material.
End-to-end cavity
Flat Backs No Hotfix
Water jet cutting
An end-to-end cavity is the simplest option when producing cavities. When selecting the glue (page 48), please note the additional instructions regarding the gluing gap.
Plastic Trimmings
A blind hole is another option when producing cavities. It allows Swarovski crystals in a variety of heights to be set and protected in the material. When selecting the depth of the cavity, ensure that there is still a gap between the lowest point of the crystal and the base material. When selecting the glue (page 48), please note the additional instructions regarding the gluing gap.
Compared to a simple blind hole, step milling offers better hold of the crystal with less glue. When selecting the depth of the cavity, ensure that there is still a gap between the lowest point of the crystal and the base material. When selecting the glue (page 48), please note the additional instructions regarding the gluing gap.
3D milling offers an optimum fit with the smallest gluing gap. Due to the fact that the cavity
is adapted to the contours of the crystal, CNC milling machines are required.
Production tolerances for cavities
When producing cavities, the dimensions should be based on the main dimensions, including the maximum tolerance for the crystal components used, and the production tolerance. These dimensions can be requested from your Swarovski sales organization.
Maximum level of tolerance (+ 0.10 mm)
Incorrect cavities
Crystal too large/cavity too small
Rounded tip of the cavity
Cavity with uneven surface
Application techniques
CHECKING SURFACE
CAVITY PRODUCTION
Checking the surface tension
The surface tension is an indicator for the wetting properties of the surface to be glued. A surface tension of at least 38 mN/m is recommended for gluing Swarovski crystals. It should also be randomly tested during production.
It is best to use the Test Pen (art. 9030/000) to measure the surface tension.
1 Before gluing, mark the surface.
2 If the ink remains visible for 2 seconds, the
3 If the ink disappears or forms bubbles, the
surface is suitable for gluing.
surface is not suitable for gluing. In this case,
the pre-treatment cleaning methods should be checked.
Note: On porous or absorbent materials, the surface tension cannot be checked with the Test Pen. If the Test Pen is used on
highly polluted surfaces (e.g. grease, oil) or on material like wood, the Test Pen might be polluted as well and cannot be used anymore.
If the surface tension is below 38 mN/m, the following pre-treatment cleaning methods, applied in the correct order, can be effective in reaching the right level. After each cleaning process, the surface tension has to be checked again.
TYPES OF CLEANING
PRE-TREATMENT CLEANING METHODS
Mechanical cleaning
This involves sanding, blasting, or brushing but is usually not
Removal of dirt, rust, scale, and residues of varnish
necessary for jewelry.
Roughening the surface
Washing and degreasing
It is important to ascertain that the tensides do not contain silicone,
Cleaning with tenside solutions, rinsing with de-ionized
as this would impair adhesion.
When using solvents it is advisable to test the durability of the
Cleaning with isopropyl alcohol/ethanol
surface to be cleaned beforehand to avoid any damage. Solvents
Cleaning with acetone (MEK/ethyl acetate)
containing substances with a high boiling point should not
Cleaning with a cleaning solvent: should not contain high
be used due to the risk of residue. If using cleaning solvents, wait
boiling point substances (risk of residue)
a few minutes to allow them to evaporate.
TYPES OF CLEANING
PRE-TREATMENT CLEANING METHODS
Physical cleaning and activation
These cleaning methods can be applied if mechanical cleaning
Flame treatment via a blow torch
or washing and degreasing are either not possible or have
The surface to be treated is exposed to the flame of
not resulted in a surface tension of >38 mN/m. Therefore
a torch very briefly. When using special gas mixtures,
the pre-treatment cleaning method used should be done
surface silication can also be carried out, so as to apply
on a case-by-case basis.
a more adhesive coating.
Corona treatmentAn electric corona discharge is briefly applied
to the surface.
Plasma treatmentPlasma treatment offers precise cleaning and activates
the surface via an ionized gas.
Chemical cleaning and primers
Applying a primer improves adhesion and helps
Applying small amounts of solvent and activating
to prevent corrosion.
the surface.
Applying a primer.
CHECKING SURFACE
CAVITY PRODUCTION
The selection of the best gluing system is the next stage in ensuring a long-lasting application. When selecting the most suitable glue, the following factors should be considered:
The type of cavities/the resulting gluing gap The size of the crystals/gluing surface The gluing properties and finish required The type of base material
The type of cavities/the resulting gluing gap
When selecting an adhesive, it is also important to consider the gluing gap that results from the type of cavity chosen. For cavities offering a large gluing gap, soft and gap-filling glues such as silicone glue are recommended to avoid tension in the glue joint. Epoxyethane/polyurethane glues offer greater strength and can be used for cavities with a small gluing gap.
The size of the crystals/gluing surface
Please note that when gluing small crystals, glues with higher shearing strengths (e.g. epoxy resin glue CG 500 (A+B)) should be used. Further information can be found in the manufacturer's technical data sheets.
Application techniques
The gluing properties and finish required
When selecting glues, it is important to consider properties such as pot life, viscosity, color, curing time, ease of dosing, and shrinkage. Further information can be found in the manufacturer's technical data sheets. Adhesives tend to shrink during curing. There will be a greater amount of shrinkage if the wrong glue has been chosen, it is hardened under the wrong conditions, or if there is an incorrectly sized cavity (too much space around the crystal). The tension thus created can damage the foiling and the crystals may even detach. Glues that are very hard after curing and shrink considerably are
The foiling is torn from the crystal because of
not suitable for Swarovski crystals with foiling.
excessive glue shrinkage (shown in yellow).
The type of base material
The following table provides a selection of commonly known and globally available adhesives that are suitable for different uses and materials. Application tests are advisable to make sure the chosen glue fulfills the specific needs of your application.
Viscosity: Measure of a fluid‘s resistance to gradual
Color: Description of the glue‘s color type after curing.
deformation by shear/tensile stress. It corresponds to the
Bonding: Depending on the carrier material, the bonding
informal notion of "thickness".
of the glues can vary.
sufficient or excellent bonding can be reached
sufficient bonding is possible
sufficient bonding is nearly impossible
POLYURETHANE CYANE-
DOUBLE DISPERSIONS &
EPOXY RESIN GLUES
high high med high
1 The second gluing part has to be UV transparent. 2 For permanent (wash-resistant) application a Hotfix application is suggested.
CG 500 (A+B) Two-component epoxy resin glue
CG 500 (A+B) is a high-performance gluing system for both foiled and unfoiled Swarovski crystals, exclusively distributed by Swarovski for professional use within the jewelry segment and other industries such as accessories, interiors, and electronics.
Main advantages of CG 500 (A+B)
Ideal mechanical resistance Ideal chemical resistance Future-oriented solution Diverse areas of application
IDEAL MECHANICAL RESISTANCE
CG 500 (A+B) absorbs impacts and withstands distortion. In addition, maximum elasticity protects the crystal foiling.
XILION Chatons that have been glued with
XILION Chatons that have been glued with
CG 500 (A+B) remain in the cavities after
a standard epoxy resin fall out of their
extreme mechanical stress due to optimal shock
cavities after extreme mechanical stress due to
absorbance (up to 500%).
its poor shock absorbance (around 10%).
IDEAL CHEMICAL RESISTANCE
CG 500 (A+B) OFFERS EXCELLENT CHEMICAL RESISTANCE AGAINST:
CG 500 (A+B) prevents infiltration of humidity into the glue and thus any corrosion.
Jewelry pieces can be stored and worn in places with high humidity.
CG 500 (A+B) prevents infiltration of perspiration into the glue and thus avoids corrosion.
The glued Swarovski products are not damaged by perspiration.
Salt and chlorinated water
CG 500 (A+B) protects Swarovski crystals when they are exposed to salt or chlorinated water. The glued Swarovski products are not damaged during swimming.
Application techniques
DIVERSE AREAS OF APPLICATION
CG 500 (A+B) OFFERS IDEAL ADHESION FEATURES ON:
E.g. Application of Swarovski products on plated surfaces, brass, stainless steel, titanium,
gold, rhodium, and silver within the jewelry industry
E.g. Application of Swarovski crystals on ABS, PMMA, PVC etc. within the accessories and
Gluable synthetics and rubber
electronics industries
Glass, crystal, wood, stone, cork, and porcelain
E.g. Application of Swarovski products in the interior and home décor industries
CG 500 (A+B) technical data
Mixture ratio (A:B)
Pot life at room temperature (23 °C/73.4 °F), quantity applied: 1 g
Complete curing time at room temperature (23 °C/73.4 °F)
Complete curing time in oven (40 °C/104 °F)
Complete curing time in oven (70 °C/158 °F)
Complete curing time in oven (100 °C/212 °F)
Handling time at room temperature (23 °C/73.4 °F)
Viscosity (mixed)
15.000 +/– 5.000 mPa*s
Mixing CG 500 (A+B) two-component glue
The exact mixing of the two-component glue is especially important. Only a fully homogenous mixture leads to the desired results. Care must be taken to follow the manufacturer's instructions.
1 Weigh out the two glue components at
2 Mix the two components until a homogenous
3 Put the glue in a dispenser.
a ratio of 1:1.
result is achieved.
4 Attach the dispensing tip to the syringe.
CG 610 (A+B) two-component epoxy resin glue
The CG 610 (A+B) two-component epoxy resin glue was specially developed for gluing Swarovski crystals of very small sizes, starting with PP 0. Depending on the area of application the adhesive can be used for crystals up to the size of PP 14.
Suitable for gluing very small crystals (starting with size PP 0) Low viscosity allows an easier dosing of small glue quantities Cost saving due to long pot life (140 min.)
Available Packaging Sizes
The CG 610 (A+B) adhesive is available in the following two packaging sizes and in two regional versions*:
CG 610 (A+B) 50 g cartridge
CG 610 (A+B) 750 g box
(33.3 g resin + 16.7 g hardener)
(500 g resin + 250 g hardener)
*Please note: The compostition of the adhesive is the same for both versions; the different description on the packaging is due to local legal requirements. It is mandatory to order accordingly.
Mixing ratio (A : B)
2 : 1 (resin : hardener) by weight
Pot life at room temperature (23°C/73.4°F) – quantity applied: 1 g
Complete curing time at room temperature (23°C/73.4°F)
Complete curing time in oven (40°C/104°F)
Complete curing time in oven (70°C/158°F)
Complete curing time in oven (100°C/212°F)
Handling time at room temperature (23°C/73.4°F)
Elasticity (break extension at 23°C/73.4°F)
Viscosity, mixed (23°C/73.4°F)
1.750 +/- 250 mPa*s
Areas of Application
The following table provides an overview of the glue's bonding on different materials:
+ sufficient or excellent bonding can be reached
o sufficient bonding is possible
- sufficient bonding is nearly impossible
Application techniques
Mixing CG 610 (A+B) two-component glue
The 50 g cartridge of CG 610 is designed in a way that the containing resin and harder do not have to be mixed together by the user. Just attach a dispensing gun and the dispensing tip (delivered with the 50 g adhesive package) to the cartridge and start gluing.
When using glue of the 750 g box, resin and hardener have to be mixed. First, weigh the two glue components at a ratio of 2 : 1 (resin : hardener). It is very important to keep an exact mixing ratio of the two components to achieve maximum adhesion. Mix then the two components well for at least one minute. Only a fully homogenous mixture leads to the desired results.
When a homogenous mixture is achieved, put the glue into a dispenser/syringe and attach a dispensing tip.
CHECKING SURFACE
CAVITY PRODUCTION
The glue can be precisely dispensed via a variety of dosage systems. Dispensers with a vacuum connection prevent the glue from dripping and reduce the amount of cleaning needed. The correct amount of glue will additionally protect the foiling from external influences. Attention must be paid to the application and quantity of the glue.
Irrespective of the shape of the gluing area, the glue should be applied as follows:
Gluing area on the reverse of the crystal
With a round gluing area, a dot of glue in the centre is sufficient. When the crystal is applied, the glue will be evenly distributed in the gluing gap. To glue a single spot, aim the dispensing needle just above the spot to be glued and lift it slowly upward to avoid any glue spreading out sideways.
With a square or rectangular gluing area, apply a cross of glue to ensure it is evenly spread into the corners.
When selecting the amount of glue to dispense, ensure that when setting and pressing down on the crystal, the glue spreads to the edges, thus offering additional protection for the foiling.
Glue protects the foiling
Application techniques
Glue protects the foiling
Glue does not fill the gluing gap
Half Hole Pendants
Two different types of adhesive can be used to affix the single Half Hole Pendant to the metal cap: UV glue and two-component epoxy resin glue. If using UV glue, the crystal must be permeable to UV light. This applies for the following Half Hole Pendant colors and effects: Crystal, Crystal AB, and Amethyst. Best results in internal tests were achieved using the UV glue DELO-PHOTOBOND GB 368.
Please note that some crystal colors absorb UV light and are thus unsuitable for use with UV glues: Siam, Smoky Quartz, and Jet. In this case using epoxy resin glue is suggested. In internal tests, the best bond was achieved using CG 500 (A+B).
As colors and effects not explicitly mentioned may provide variable results, in these cases it is recommended to perform application tests with UV glue or to choose the option of gluing with epoxy resin glue. For further information about commonly known and globally available glues and their adhesion on metal, please consult the Application Manual on our business website SWAROVSKI.COM/PROFESSIONAL.
1 To achieve precise and consistent results, it is
2 After setting the metal cap into the hole,
suggested to use a dosage system. Choose
the glue should be evenly distributed in the
a dispensing tip with a diameter smaller
gluing gap and spread over the edges to
than 1 mm and put a dot of glue into the
also affix the metal part on top of the crystal.
pendant's hole. The amount of glue used
Remove excess glue before it is hardening,
depends on the type of adhesive and its
e.g. with a cotton wipe soaked in isopropyl
curing behavior; performing application tests
is therefore recommended.
Once the glue has been dispensed the Swarovski product can be positioned. Pick up the crystals, for example with a wax stick or tweezers, apply them to the gluing position, and press down gently.
For preparing Chatons for the positioning process, a Chaton Sieve can be helpful. Take the black sieve (for size PP 0 - PP 1, art. 9030/003), the gray sieve (for size PP 2 – PP 20, art. 9030/001) or the blue sieve (for size PP 21 – SS 34, art. 9030/002) according to the Chatons' sizes. As each sieve provides two sides with different cavity sizes, make sure to choose the sieve type and side that perfectly matches the Chatons to be set. Place some crystals onto the sieve. By slightly shaking the tool and wiping over it with glove-covered fingers, the majority of Chatons automatically turn into the suitable position for gluing (table pointing upwards).
Chaton Sieve for Chatons size PP 0 – PP 1
Chaton Sieve for Chatons size PP 2 – PP 20
Chaton Sieve for Chatons size PP 21 – SS 34
As a next step the Chatons can easily be picked up from the Chaton Sieve using a tool like the wax stick, tweezers, or a vacuum pick-up system. The use of a silicone wax stick is not recommended as this can impair the adhesion and the brilliance of the crystals.
Apply the crystals to the gluing position and press down gently. When working with cavities with large gluing gaps, the following aids assist in ensuring the optimum positioning:
A cross (or a similar tool) prevents the crystal
To prevent the crystal from sinking or tipping during the hardening process, a small plasticine ball
from tipping over. Press the crystal down flat on
can be used to fix it in place.
the material using the chosen tool.
Application techniques
CHECKING SURFACE
CAVITY PRODUCTION
Excess glue that escapes during setting can be carefully removed using a cotton wipe that has been soaked in a solvent, e.g. isopropyl alcohol. It must be removed while the glue is hardening, as dried glue cannot be fully removed. Remember to follow the glue manufacturer's instructions, as well as considering the resistance of the base material.
The curing time of the glue depends mainly on the temperature, or on the humidity in the case of silicone glues. Please note the glue manufacturer's instructions. To minimize shrinking and tension during hardening, we recommend a maximum curing temperature of 50 °C (122 °F), with the exception of two-component epoxy resin glue CG 500 (A+B). CG 500 (A+B) can be cured at a maximum temperature of 100 °C (212 °F), without any changes to its properties.
OVERVIEW OF THE APPLICATION PROCESSES
1 The surface must be correctly pre-treated
2 The glue should be applied with a dispenser.
3 Pick up the crystal, e.g. with the wax stick.
before gluing (e.g. cleaning, degreasing,
4 Carefully place the crystal in the cavity and
press it down gently; post-clean and cure.
PRODUCT-SPECIFIC APPLICATION INSTRUCTIONS
Applying UV-transparent materials
When using UV glue, at least one part of the materials must be translucent for UV light. On a metal surface for example, only crystals without foiling can be applied. Similarly, foiled crystals can only be glued to UV-transparent materials.
Please note that some crystal and glass colors as well as UV-stabilized plastics absorb UV light and are thus unsuitable for UV glues.
1 The surfaces to be glued must be properly
2 Dispense the UV glue.
3 Press down on the crystal, until the glue
pre-treated to achieve a sufficient surface
completely covers the gluing area.
tension. This can be tested via a Test Pen
(art. 9030/000).
4 Cure the glue for a few seconds using a
UV light (following the manufacturer's instructions), and remove any excess glue using a cleaning agent. The curing process
can then be continued, according to the manufacturer's instructions.
Note: It is recommended that UV-protective eyewear is worn during curing, to prevent injury. Please follow the manufacturer's
Application techniques
Applying Synthetics Hotfix on solid surfaces (with external glue)
1 The surfaces to be glued must be properly
2 Apply the correct amount of glue onto the
3 Elapse the glue equally on the material.
pre-treated, so as to achieve sufficient
carrier material.
surface tension.
4 Position the motif in the desired location and
5 Glue that escapes during positioning can be
6 During curing it is suggested to put some
press down firmly for a few minutes.
carefully removed using a cotton wipe.
weight on the motif.
Applying Self-adhesive Elements
APPLYING CRYSTAL TATTOOS
Crystal Tattoos are coated with a dermatologically tested glue that poses no threat to health and can therefore be applied directly to the skin.
1 Clean the skin with soap.
2 Peel off the white protective film at an acute
3 Position the motif in the desired location and
press down firmly for around 10 seconds.
Note: Please read the additional instructions on working with Crystal
Tattoos at the end of this manual.
4 Carefully remove the transparent film at an
acute angle and press down on the motif again.
APPLYING CRYSTAL-IT
1 Press the crystals onto the transparent film.
2 Peel off the white protective film at an acute
3 Position the motif in the location desired and
press down firmly for around 10 seconds.
4 Carefully remove the transparent film at an
acute angle and press down on the motif again.
Applying other Self-adhesive Elements
1 The surfaces to be glued must be properly
2 Press the motif onto the transparent film.
3 Peel off the white protective film at an acute
pre-treated, so as to achieve sufficient surface
4 Position the motif in the location desired and
5 Carefully remove the transparent film at an
press down firmly for around 10 seconds.
acute angle and press down on the motif again.
Note: Prevent the self-adhesive back from sticking together, as separating it can cause damage. The minimum application
temperature is 18 °C (64 °F), with the glue fully hardening after 72 hours.
Application techniques
For applications on surfaces subject to high mechanical stresses, it is recommended that a cavity is produced.
When applying Synthetics-it and Chatons, remove the white protective film during application in the pre-produced cavity.
When producing cavities, the dimensions should consider the tolerance of the product and the production tolerance. The tolerances of the product can be requested from your Swarovski representative.
For larger motifs and those that must be positioned accurately on surfaces, a wet application is recommended. It is essential,
however, that the base does not absorb the soap water that is used here.
1 Moisten the cleaned surface with soap water.
2 Carefully peel off the white protective film
3 Carefully remove the transparent film at an
at an acute angle, and carefully position the
acute angle and leave the surface to dry.
product on the wet surface. After positioning it, press down on the soap water beneath the motif, e.g. using a rubber roller.
4 After drying, press down firmly on the motif
again, e.g. using a rubber roller.
Applying Flat Backs No Hotfix for mosaic tiles
Due to their dimensions (outer dimensions and height) and coating (protective lacquer), selected Flat Backs No Hotfix have been tailored specially for use in tiles and mosaics.
Protective lacquer
Protective lacquer is applied to the foiling of all crystals, and fully covers the reflective surface. Protective lacquer prevents moisture, cleaning agents, etc. from coming into direct contact with the reflective layer, which can lead to corrosion and damage the crystal.
Long-term, satisfactory solutions can only be achieved with paper-glued mosaic tiles and the use of recommended tile glues and joint sealers. When working with net-glued mosaics, their absorption and storage of moisture means the support net must be completely removed in the areas where the crystals are to be applied.
Find suppliers for tile glues and joint sealers on the supplier list on page 43. Solvent-resistant and alkaline tile glues and joint sealers are not recommended.
UNSUITABLE AREAS OF APPLICATION
In swimming baths and steam rooms In contact with chlorine and other aggressive cleaning agents In saunas, due to the high temperatures and moisture Outside
1 Cut out the marked tile area and remove it
2 Apply the tile glue to the prepared base
3 Place the individual crystals in the gaps and
from the mosaic.
according to the manufacturer's instructions,
lightly press down.
then carefully position the mosaic tile and
4 Before curing, remove any excess glue with
5 After curing, remove the paper support.
6 Excess joint sealer can be removed with a
a damp sponge; follow the manufacturer's
Following this, the mosaic can be grouted
wet sponge during curing.
information regarding curing.
with a soft rubber scraper.
Note: Please be aware that many tile glues and joint sealers can contain abrasive materials, which can lead to scratching
of the crystal. To avoid damaging the crystal, these parts should be carefully cleaned with mild, pH-neutral cleaning agents and cleaning sponges.
Application techniques
USEFUL INFORMATION
Applications on silver jewelry
Without protection, silver jewelry can turn yellow or black with time due to chemical reactions. To slow or stop these reactions the surface of silver jewelry is often covered with a temporary (wax-based) or permanent protective coat (varnish-based). Tarnishing on the surface of the metal often results in a decline in the surface tension under the recommended 38 mN/m.
TARNISHING PREVENTION SYSTEMS
Temporary protection against tarnishing:
Permanent protection against tarnishing:
Low surface tension
Surface tension depends on varnish
Protect the rest of the piece after gluing
Use a tarnishing protection system with sufficient surface tension
A self-adhesive film can protect against dirt during the application process and aid in positioning.
1 To protect the surface of the material used
2 It is then cut out along the previously
3 The crystal can now be glued into the cavity.
(e.g. metal, tiles, etc.) from dirt, a self-
produced cavities.
Once any excess glue has been removed,
adhesive film can be applied.
the adhesive film can be removed following
END-TO-END CAVITIES
1 Apply a self-adhesive film to the front of the
2 Place the Flat Backs No Hotfix elements into
3 Now fill the cavity with glue. The glue should
the end-to-end cavity from the back.
cover the entire foiling of the crystal, so as
to avoid corrosion. The self-adhesive film prevents the glue spreading onto the front.
Note: Highly viscous glues are best suited for end-to-end cavities, as
they do not spread through the cracks at the front.
4 Once the glue has cured, the film can be
Cutting and gluing Crystal Mesh
The transparent film should not be removed before gluing. The film allows the individual crystals to be aligned perfectly, and provides Crystal Mesh with the stability necessary for flawless application.
Cut the transparent film between the rows of crystals with a Stanley knife, though do not pull
it away – otherwise the stability of the crystals will be lost.
When gluing flexible Crystal Mesh products, do not remove the transparent film until the glue has cured to ensure the proper alignment of the mesh.
Application techniques
Cutting Crystaltex Chaton Bandings and Cabochon Bandings
When working with Crystaltex Chaton Bandings and Cabochon Bandings, the lack of space between crystals means great care must be taken during cutting, so as to avoid damaging the crystal.
1 Cut into the support film between the crystal
2 Snap and cut off the Crystaltex Chaton
rows with a Stanley knife.
Banding and Cabochon Banding along the
scored edge.
Applications on plastics
There are many types of synthetic materials. The following table contains information regarding the adhesive
qualities of a selection of plastics.
USUAL COMMERCIAL NAME
ADHESIVE QUALITIES
Abselex, Lacqran, Tynrene
Ultraphan, Saxetat, Thodialite
Araldite, Ferropox, Duroxyn
Degamid, Nylon, Perlon
Polycarbafil, Lexan, Andoran
Geberit, Hostalen G, Ferrozell
Cardura, Atlas, Eralyt
Formanyl, Holoplast, Kerit
Parapol, Oppanol, Vistanex
Plexiglass, Resartglass
Delrin, Kematal, Ertacetal
Moplefan, Proplex, Verelite
Hostyrene, Styropor, Noblen
Teflon®, Gaflon, Ferrotron
Marcoproplat, Ravinil, Sumilit
Litac, Tuf-Flex, Vestoran
Silopren, Contiduct, Corotex
Celipal, Sirester, Vestopal
QUICK ASSISTANCE
The following table outlines common problems and causes when gluing Swarovski crystals, and offers advice on how to avoid them. Further details and more extensive descriptions can be found in the section marked with a
The crystal has become discolored:
The crystal is matt or yellowed.
The crystal seems black and dull compared to the surrounding crystals.
The crystal has been plated.
The crystal has detached from the cavity without the foiling:
The crystal has become discolored.
The crystal has detached with the mirror coating but without the platinum foiling or the glue.
The crystal has detached from the cavity with the foiling:
Glue is attached to the crystal.
10, 11, 12, 13, 14
No glue is attached to the crystal anymore.
Before hardening.
After hardening.
Glue residues have not been completely removed and
Use a suitable dispenser to apply exactly the right
have been smeared over the crystal.
amount of glue. Dispensers with a vacuum connection prevent the glue from dripping and reduce the amount of cleaning needed.
Too much glue was used.
Be sure to use the exact recommended dosage and to carefully remove any excess glue, e.g. using acetone or isopropyl alcohol.
The axis of the cavity was already off-center in the
Use a special bit when drilling the original model. This
original model or the cavity was not drilled straight in the
offers more precise control of the direction and depth of
unfinished casting.
the drilling.
The jewelry was only plated after the crystals had been
It is recommended to complete the plating before gluing
glued to it.
the crystals.
A gluing gap that has not been completely filled is
Make sure the exact dosage of glue is used.
causing corrosion.
Tensile stresses are reducing the adhesion of the mirror
Use glue that is more elastic and that does not shrink
coating. Oxygen is penetrating between the stones and
the mirroring and causing oxidization.
An incorrect glue system was used.
Carry out tests with other glue systems.
Incorrect proportions of resin and hardener were used.
Follow the glue manufacturer's mixing instructions.
Cleaning agents have affected the glue and/or the
Use less solvent or a different type of solvent.
protective coating.
Residues of polishing agent were not completely removed
Double check the type of cleaning process used.
before plating.
A varnished piece of jewelry has not been correctly
Improve the adhesion of the glue, e.g. with low-pressure
pre-treated before gluing.
plasma treatment or flame treatment if necessary.
Too little glue was used.
Make sure the exact dosage of glue is used.
The cavity has the wrong shape after plating.
Re-work the original model to improve the cavity shape.
Electrolyte residues have not been completely removed.
Double check the type of cleaning process used.
Application techniques
The specified processing time was exceeded and as a
Reduce the processing time.
result the glue has already hardened.
Too little glue was used.
Make sure the exact dosage of glue is used.
General glue problems.
Follow the manufacturer's instructions. Check the conditions under which the glue is stored. Excess solvent could have corroded the glue and/or the foiling.
The jewelry piece was put under stress before the glue
Make sure the glue has hardened, for example before
had hardened.
transporting the jewelry.
Application techniques
CERALUN Ceralun is a high-performance, two-component
ceramic epoxy composite especially developed for the application of Swarovski products.
PRODUCT OVERVIEW
The following products are suitable for application with Ceralun:
Flat Backs No Hotfix
Ceralun is a versatile and strong two-component, high-performance ceramic epoxy composite. This clay has been specifically developed and tailored to embed foiled and unfoiled crystals. It is an absolutely essential material for innovative design. Ceralun has a high level of hardness, rigidity, and shock absorbance. It is resistant to sweat, humidity, or climatic changes, and shows no aging.
Available Basic Colors
Available Shining Colors
MACHINES, TOOLS, AND AIDS
The following machines, tools, and aids can be used for the various processes involved in the application of Swarovski products with Ceralun:
Test Pen (art. 9030/000)
Precision balance
Protective eyewear
Ceralun (A + B)Two-component ceramic epoxy composite(5 x 20 g)
Two-component ceramic epoxy composite
Two-component ceramic epoxy composite
Two-component ceramic epoxy composite
Application techniques
Vacuum pick-up system
Contains high molecular liquid wax (100 ml)
Chaton Sieve for Chatons size PP 0 – PP 1
Chaton Sieve for Chatons size PP 2 – PP 20
Chaton Sieve for Chatons size PP 21 – SS 34
: istockphotoafía
This list provides an overview of selected suppliers worldwide.
MACHINES / TOOLS / AIDS
Swarovski: art. 9030/000
Ceralun Basic Colors
art. 9020, 5 x 20 g, America, Asia, Europeart. 9020, 100 g, America, Asia, Europeart. 9020, 10 x 100 g, America, Asia, Europeart. 9020, 1 kg, America, Asia, Europe
Black (A+B), Dark Sapphire (A+B), Malachite (A+B), Red (A+B), Rose (A+B), Walnut (A+B), White (A+B), Yellow (A+B)
Ceralun Shining Colors
art. 9020, 5 x 20 g, America, Asia, Europeart. 9020, 100 g, America, Asia, Europeart. 9020, 10 x 100 g, America, Asia, Europeart. 9020, 1 kg, America, Asia, Europe
Anthracite (A+B), Gold (A+B), Pearl Silk (A+B), Shining Green (A+B), Shining Lilac (A+B), Shining Red (A+B), Silver (A+B)
Ceralun Release Agent
art. 9020, America, Asia, Europe
Vacuum pick-up system
I & J Fisnar, Inc.
Epoxy & Equipment Technology PTE., Ltd.
Hottemp (M) Sdn. Bhd.
PT. SKT International
For Chaton size PP 0 – PP 1: art. 9030/003
For Chatons size PP 2 – PP 20: art. 9030/001
For Chatons size PP 21 – SS 34: art. 9030/002
Heraeus Holding GmbH
VWR International, LLC
Application techniques
When working with Ceralun, optimal results are obtained by coordinating the entire application process. Following the application steps in the right order is very important. Experience has shown that the most common reasons for crystals becoming detached are inappropriate areas of application, the wrong mixing ratio of the two components, or not mixing them together long enough until a homogenous appearance is achieved.
Main advantages of Ceralun
Specifically developed and tailored to embed foiled and unfoiled Swarovski crystals.
High level of hardness, rigidity, and shock absorbance.
Resistant to perspiration, humidity, or climatic changes and shows no aging.
Allows new design possibilities.
Perfect material to generate a large variety of surfaces and structures.
Applicable on 3D-shaped surfaces.
Alternative solution to gluing.
Ceralun two-component ceramic epoxy composite
Ceralun was especially developed for the application of both foiled and unfoiled Swarovski crystals, exclusively distributed by Swarovski for professional use within the jewelry segment and other industries such as accessories, interiors, and electronics.
Mixing ratio (A : B)
Pot life at room temperature (23 °C/73.4 °F)
Total hardening time at room temperature (23 °C/73.4 °F)
Time needed to harden in an oven at 40 °C/104 °F
Time needed to harden in an oven at 80 °C/176 °F
Time required before handling strength is reached at room temperature
(23 °C/73.4 °F)
Humidity during curing
Hardness (according to DIN 53505)
Storage conditions
Storage time at room temperature (23 °C/73.4 °F, 55% rel. hum.)
Lowest storage temperature
CHECKING SURFACE TENSION
AND PRE-TREATMENT
Ceralun has optimal adhesive characteristics for applications on metal, glass, crystal, gluable plastic surfaces, rubber, wood, cork, and porcelain, unless the materials do not have the right surface tension.
Checking the surface tension
The surface tension is an indicator for the wetting properties of the surface the Ceralun should be applied to. A surface tension of at least 38 mN/m is recommended for working with Ceralun. It should also be randomly tested during production. It is best to use the Test Pen (art. 9030/000) to measure the surface tension.
1 Mark the surface.
2 If the ink remains visible for 2 seconds, the
3 If the ink disappears or forms bubbles, the
surface is suitable for working with Ceralun.
surface is not suitable for applying Ceralun.
In this case, the pre-treatment cleaning methods should be checked.
Note: On porous or absorbent materials, the surface tension cannot be checked with the Test Pen. If the Test Pen is used on
highly polluted surfaces (e.g. grease, oil) or on material like wood, the Test Pen might be polluted as well and cannot
be used anymore.
If the surface tension is below 38 mN/m, the following pre-treatment cleaning methods, applied in the correct order, can be effective in reaching the right level.
TYPES OF CLEANING
PRE-TREATMENT CLEANING METHODS
Mechanical cleaning
This involves sanding, blasting, or brushing but is not usually
Removal of dirt, residues of varnish, rust and/or scale
necessary for jewelry.
Roughening the surface
Washing and degreasing
Here it is important to ascertain that the tensides contain no silicone,
Cleaning with tenside solutions, rinsing with de-ionized
as this would impair adhesion.
When using solvents it is advisable to test the durability of the
Cleaning with isopropyl alcohol/ethanol
surface to be cleaned beforehand to avoid any damage. Solvents
Cleaning with acetone (MEK/ethyl acetate)
containing substances with a high boiling point should not
Cleaning with a cleaning solvent: should not contain high
be used due to the high risk of residue. If using cleaning agents,
boiling point substances (risk of residue)
wait a few minutes to allow them to evaporate.
Physical cleaning and activation
These cleaning methods can be applied if mechanical cleaning or
Flame treatment with a blow torch
washing and degreasing are either not possible or have
The surface to be treated is exposed to the flame of
not resulted in a surface tension of >38 mN/m. Therefore the
a torch very briefly. When using special gas mixtures,
pre-treatment cleaning method used should be done on a
surface silication can also be carried out, so as to apply
case-by-case basis.
a more adhesive coating.
Corona treatmentAn electric corona discharge is briefly applied to the
Plasma treatmentPlasma treatment offers precise cleaning and activates
the surface via an ionized gas.
Chemical cleaning and primers
Applying a primer improves adhesion and helps to prevent corrosion.
Applying small amounts of solvent and activating
the surface.
Applying a primer.
Application techniques
CHECKING SURFACE TENSION
AND PRE-TREATMENT
Please pay high attention to not deviate from the recommended mixing ratio of 1:1 of the components (resin and hardener) and to mix the two components until a homogenous appearance is achieved.
Mixing Ceralun two-component ceramic epoxy composite
1 Cut off resin and hardener with a knife.
2 Weigh the two components. The mixing ratio
2 Mix resin and hardener until a homogenous
for Ceralun is 1 : 1 by weight.
appearance is achieved.
Proper setting of crystals
After mixing the two components together, the crystals can be set. To prepare Chatons for the positioning process, a Chaton Sieve can be helpful. Take the black sieve (for size PP 0 – PP 1, art. 9030/003), the gray sieve (for size PP 2 – PP 20, art. 9030/001) or the blue sieve (for size PP 21 – SS 34, art. 9030/002) according to the Chatons' size. Place some Chatons onto the sieve. By slightly
shaking the tool and wiping over the crystals with glove-covered fingers, the
majority of Chatons automatically get turned into the suitable position for gluing (table pointing upwards).
Using a Chaton Sieve can facilitate the setting
As a next step the Chatons can easily be picked up from the sieve using a tool like the wax stick, tweezers, or a vacuum pick-up system. The use of a silicone wax stick is not recommended as this can impair the adhesion and the brilliance of the crystals. Apply the Chatons to the desired position and press down gently.
We recommend a maximum working time of three hours at a temperature of 23 °C/73.4 °F to set the Swarovski products. It is not possible to set crystals at room temperature after a period of three hours because the required level of adhesion can no longer be achieved.
Please take care that the pavilion of the crystal is surrounded by Ceralun right up to the level of the stone's girdle.
It is not necessary to leave any particular space between the crystals when setting them.
CHECKING SURFACE TENSION
AND PRE-TREATMENT
Different processing methods
Ceralun is the perfect material for generating a variety of surfaces and structures. Possible ways of processing are the forming method and the stamping technique.
1 Place and press the clay onto the relevant
2 Mold the surface into the required
3 Pick up the crystal with a vacuum pick-up
area. Be careful not to trap air between
shape and smooth the surface with the
system – or with a pair of tweezers or a wax
Ceralun and the base material.
recommended Release Agent.
stick. Carefully place the crystal and press it down gently.
GENERATING SHINY SURFACES WITH THE FREE FORMING METHOD
When a piece of jewelry is created where parts of Ceralun are visible, a smooth and shiny clay surface might be desired.
In order to create a shiny surface, gently wipe and polish the clay with your silicone glove-covered finger using the
recommended Release Agent or some water drops. The Ceralun surface can be polished up to 2 hours after the crystals
have been set.
STAMPING TECHNIQUE
The stamping technique is suitable to produce structured surfaces.
1 Pre-treat the pattern cautiously with the
2 Gently press the pattern onto the surface.
3 After removing the pattern from the clay,
recommended Release Agent.
the crystals can be set.
GENERATING SHINY SURFACES WITH THE STAMPING TECHNIQUE
If a larger surface of shiny Ceralun is needed, the following aids are required: transfer foil, a pasta machine or rolling pin, and a freezer. Knead the clay and put it between two layers of foil. Smoothen it with the help of a pasta machine or with a rolling pin. Using the pasta machine is the recommended option, as a consistent height of the Ceralun is achieved easier than with the rolling pin. When the clay inside the foil is as flat as desired, put it into the freezer for approx. 15 minutes. The cold reduces the bonding between Ceralun and foil, so that the foil can easily be detached from the flat and shiny clay.
Application techniques
3D SILICONE MOLDS
The work and cost saving method of using 3D silicone molds is recommended for larger production units. A 3D silicone mold is produced based on a master model. This can be re-used for several times.
1 First press the Ceralun into the 3D silicone
2 Any overlapping material can be trimmed off
3 In order to make it easier for you to remove
mold to form the required shape.
with a knife.
the Ceralun from the mold, it should first be stored in the freezer. The length of time the filled mold should remain in the freezer
depends on the thickness and amount of the Ceralun used.
4 After taking the mold out of the freezer, the
5 Please be sure to remove any condensed
6 Once the Ceralun reaches a lukewarm
Ceralun can be removed from it and gently
temperature, you can proceed with setting
pressed into place on the chosen object.
the crystals.
CHECKING SURFACE TENSION
AND PRE-TREATMENT
The hardening time and final adhesion strength of Ceralun are dependent on the temperature. The total hardening time at room temperature of 23 °C (73.4 °F) takes 72 hours. This can be accelerated using heat of max. 80 °C (176 °F).
USEFUL INFORMATION
Extension of pot life
1 Store already mixed Ceralun in a freezer to
2 This makes it possible to interrupt the setting
3 It is necessary to gently remove any
extend the pot life. Ceralun can be stored in
process and continue again later without
condensed water that occurs during the
a freezer for up to 24 hours at a temperature
losing the adhesion force.
defrosting process.
of around – 20 °C (– 4 °F).
MIXING DIFFERENT COLORS OF CER ALUN
You can mix different colors together as you wish. Please consider that you have to separately mix the epoxy resin and hardener of each color before you mix them together. Below you find some examples of mixed colors and the corresponding mixing ratio.
Based on Black SP
Based on White SP 300
Application techniques
QUICK ASSISTANCE
Ceralun does not cure.
Ceralun is not bonding with the base material.
Crystals fall off.
Ceralun cannot be removed from the silicone mold.
Using the stamping technique, Ceralun cannot be removed from the surface pattern.
Ceralun appears foggy/cloudy after curing.
An error has occurred during the calculation of the right mixing
Do not deviate from the recommended mixing ratio of the
ratio between the two components (resin/hardener).
components (resin/hardener), 1 : 1.
Resin and hardener have not been mixed until a homogenous
Be sure to use the exact recommended dosage and to
appearance was achieved.
carefully remove any excess Ceralun, e.g. using acetone or isopropyl alcohol.
The base material is not suitable for using Ceralun or it has been
Check the surface tension. If the surface tension is below
38 mN/m, carry out pre-treatment cleaning methods.
The specified processing time was exceeded and as a result
Reduce the processing time to a maximum of two hours at
Ceralun has already hardened.
a temperature of 23 °C (73.4 °F)
If stored in the freezer, condensed water can occur during the
Take care to gently remove any condensed water that
defrosting process.
occurs during the defrosting process.
Ceralun has been stored for too much time in the freezer.
Make sure not to exceed the recommended time of 24 hours when Ceralun is stored in a freezer at a temperature of around – 20 °C (– 4 °F).
No or not enough Release Agent has been used.
The Release Agent is a useful aid to be able to remove Ceralun from any surface. Carefully dose the used amount of Release Agent.
Ceralun has not been stored in a freezer or has been stored for
Storing Ceralun in a freezer makes it easier for you to remove
too little time.
it from the mold.
Source: http://www.crystalart.si/image/data/Pripomocki/Application_2016_English_1.pdf
prepared in collaboration with the WHO Collaborating Centre for International Drug Monitoring, The aim of the Newsletter is to disseminate information on the safety and efficacy of pharmaceutical products, The WHO Pharmaceuticals Newsletter provides you with the latest information on the safety of medicines and based on communications received
A REFERENCE GUIDE 393 University Avenue, Suite 1700, Toronto, Ontario M5G 1E6 arthritis.ca 1.800.321.1433 /ArthritisSociety A Reference Guide © The Arthritis Society, 2015 WE HAVE ARTHRITIS IT DOESN'T HAVE US The Treatment Series Does not require a prescription Requires a prescription May require a prescription Does not require a prescription Requires a prescription May require a prescription