Manual-solids-type-f - v.b.10-11.p65
INSTRUCTION MANUAL
INSTALLATION, OPERATION AND MAINTENANCE
Pump for Solids Type F
IMPELLER DIAMETER
INSTALLATION DATE
PACKING RINGS QUANTITY:IMPELLER CLEARANCE
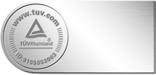
1. GENERAL INFORMATION.
1.1 Description.
1.1.1 Casing.
1.1.2 Impeller.
1.1.3 Wear Rings.
1.1.4 Shaft.
1.1.5 Bearing Frame.
1.1.6 Stuffing Box.
1.2 Installation.
1.2.1 Foundation.
1.2.2 Alignments.
1.2.3 Leveling.
1.2.4 Alignments.
Flexible Disk Coupling.
Cardan joint.
Belt Transmission.
1.2.5 Foundation Finishing.
1.2.6 Suction.
1.2.7 Discharge.
1.2.8 Sealing System.
1.2.9 Service Connection.
1.2.11 Final Verification.
1.3 Starting.
1.3.1 Priming.
Positive Suction Pumps.
Negative Suction Pumps. 10
1.3.2 Rotation. 101.3.3 Stuffing Box. 111.3.4 Starting.
1.3.5 Stopping.
1.3.6 Initial and Periodical Checking.
1.3.7 Service Characteristic.
1.3.8 N.P.H.S (Net Positive Suction Head).
1.3.9 Corrosion and Abrasion.
1.4 Maintenance.
1.4.1 Lubrication.
Grease Quantity.
1.4.2 Labyrinth Seal.
1.4.3 Sealing Shaft Syste.
1.4.4 Stuffing Box Packing Replace.
1.4.5 Impeller Clearance.
1.4.6 Failure Causes.
MANUAL PUMP FOR SOLIDS
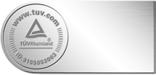
MANUAL PUMP FOR SOLIDS
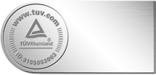
1 GENERAL INFORMATION
design allows a quick mounting and dismantling of
the impeller even in pumps with many years ofrunning.
You have acquired a valuable equipment. Payattention and be careful with your Hidrostal pump in
1.1.3 Wear Rings ( Part 408 )
order to obtain excellent results.
The wear ring has been designed to be easilyreplaced, allowing to maintain the original efficiency
Your pump has been designed and constructed in
with a low maintenance cost.
order to render years of constant service, as longas the user stricly follows these instructions must befully understood before starting the pump.
1.1.4 Shaft ( Part 110 )
Carbon steel shaft C-1045 or stainless steel mounted
on grease lubricated bearings. Replaceablestainless steel shaft sleeve to avoid any damage
Transcribe the data filled in the pump identification
due to the stuffing box packing friction.
plate to this manual and mention it when you referto us for any consultation.
1.1.5 Bearing Frame
Widely sized bearing frame, back pull out designallows the pump to be dismantled without the
As you can notice in the instructions we offer a
removal of any pipe fastened to the casing. the
grease lubricated bearing frame has been
designed for a 50,000 hour of operation rate, when
warranty stops if the pump is used to pump other
the pump runs on its best efficiency point.
1.1.6 Stuffing Box
in our order acknowledgment, likewise by failures
Splitted stuffing box type, which allows an easy
originated by wrong maintenance, inadequate
access to the stuffing box packings for its
replacement. The external connection (3) is to
emplacement or incorrect installation
perform the shaft sealing in the stuffing box.
Normally the equipment is provided by freeasbestos packing.
1.1.1 Casing (Part 400)
Vertical split volute casing with axial suction; radialdischarge and back pull out design, which allows
The pump installation should allow the direct
a fast bearing frame and impeller service without
connectation of the suction and discharge pipe
dismantling any pipe fastened to the casing. If
with their accessories (valves and fittings)
the pump coupling used is a flexible extended type
properly supported. The connection should be
or cardan type. The motor can also stand fixed to
in an independed way to avoid the transmission
the base. The casing has been hydrostatically
of any strength and tension to the pump. Pipe
1.1.2 Impeller (Part 401)
damage. The pipe flanges before being adjusted
Closed type impeller, its hydraulic design provides
with the bolts.
a gentle handing of the solids in suspensionavoiding rough changes in direction and
Project the pipe so that a minimun of curves,
elbows and accesories would be used. Install the
The impeller is firmly mounted on the impeller flange
pipe the nearest possible to the water supply or
fastened to the pump shaft by a central bolt. This
the liquid being held. Remember that if the length
MANUAL PUMP FOR SOLIDS
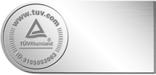
of the pipe increases, the loss of capacity of the
pump by friction increases as well, thus the cost of
When the unit is received with the pump and the
the equipment operation.
motor placed on their common base, this unitshould be mounted on its foundation base. The
Leave enough space in the installation to allow an
couplings should be disconnected, leaving a 3/4"
easy access for the inspection job, dismantling and
and 1.1/2" space between the top face of the
maintenance of the pump and the auxiliary
foundation block and the bottom face of the pump
equipment. If the pumps are placed in pits, they
base, interlocking it with a thin wedge in order to
must be protected againts floods.
count with a convenient space.
The flexible couplings should not be used tocompensate the pump and motor shaft misalignment.
It is great importance to mount the pumps on solid
The flexible coupling allows only absorbing the
foundations, preferently on concrete bases. It is
misalignment produced by temperature changes.
normally satisfactory to build a concrate baseusing a 1-3-5 mix ( cement, sand, and gravel )with a thickness according to the basement
characteristicThe foundation anchor bolts should be fixed to
1.2.4.1 Flexible Disk Coupling ( Fig. 1.3 )
the concrete as showed in ( Fig. 1.2 ).
In order to align the shafts, the two halves of the
The diameter of the pipe placed around the anchor
coupling should have the distance recommended by
foundation bolt should exceed two or three timesthis last, allowing the anchor foundation bolt to befreely removed to its final position.
1.2.2 Alignment
The pumping units is correctly aligned in the factory,
however the experience has demostrated that flexingand bending could happen during transportation in
spite of the tough construction of the bases, in
consequence an aligment re-check is needed afterthe complete pump installation.
MANUAL PUMP FOR SOLIDS
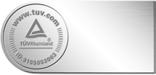
its manufacturer. The distance must be: a=a and
alignments already performed in other directions,
b=b , it can be verified through a gage and a rule.
therefore an accurate final inspection is needed.
The axial distance has to be the same in the wholecoupling circumference; this distance can be
If the pumps or motors heat due to the operation
measured by introducing a gage between the two
conditions, alignment has to be done in these
halves of the coupling. (in different parts of the
normal thermal conditions, so that contraction
and expansion due to temperature changes are
The coupling alignment is considered correct
compensated. Do not forget that a wrong
whenever being measured in four positions with
alignment produces vibrations, shafts bending
90º rotation each time, a play no major of 0.05
and excessive bearing wear.
mm. does not appear, in axial or radial direction.
1.2.4.2 Cardan Joint (Fig. 1.4)If the pump uses a cardan joint, the motor andpump shafts have to be parallel. The angelbetween cardan shaft and pump shaft, and theangle between cardan shaft and motor shaft mustbe equal, a difference major of 1º between thisangles is not allowed. It the difference exceeds
1º a decrease of the universal joint life happens.
If for any reason the cardan joint is dismantled,make sure to mount it with the ribbed shaft on its
original position.
1.2.5 Foundation Finishing (Fig. 1.5)
When alignment is completed foundation bolts
have to be handadjusted and the base grouted
(mix of one part of cement for two parts of sand),
in order to get a strong pump base support. (See
Fig. 1.2).
The grouting has to be done with a support under
the pump base and over the wet foundation until
the surface support is completely covered.
The metallic base interior cavities must be filled
w i t h c o n c r e t e a v o i d i n g a i r b u b b l e s . O n c e
thefoundation base is ready, the foundation boltsmust be tightened.
1.2.4.3 Belt Transmission
Note: The equipment last depends in great
If the pump uses a belt transmission or a chain
deal on a correct alignment and grouting.
transmission, V-belts should not be over-
We do not assume any warranty if these
tensiond. The tension over the V-belts must be
recommendations are not followed.
enough to avoid the slipping between belts andpulleys. Make sure that the belts are similar in
1.2.6Suction (Fig. 1.6)
length, tolerance and dynamically measuredduring its confection. Each belt will take belts
The suction pipe must be direct and short, sized
comply with these conditions.
according to the pump flow. The suction pipe sizeis greater or equal than the suction pump size.
Note: It is very important to remember that the
The flow velocity in the suction pipe must not
exceed 2 Mts./sec. Avoid to place any portion of
MANUAL PUMP FOR SOLIDS
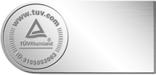
STRAIGHTAPER (CONCENTRIC) REDUCER
OFFSET (ECCENTRIC) REDUCER
the suction pipe over the pump suction centerline,
If the pump suction is positive it is convenient to
because an air pocket could appear in this area
install a gate valve in the suction pipe in order to
and an erratic pump function could be generated
allow an easier inspection job and maintenance.
by this condition.
If the installation contemplates the use of multiple
If a reduction is needed to assemble the suction pipe
pumps using the same source (reservoir), each
to the pump suction, eccentrical reduction is
pump should have its own suction pipe.
If this is not possible, the common suction pipe must
If the suction is negative a foot value must be
be calculated to obtain low flow velocity.
installed in the suction entrance. The foot valve mustbe placed under the fluid lowest level to avoid any
air bubbled inlet and at a convenient distance from
Discharge pipe must include a gate valve, which
reservoir bottom to avoid sludge or sand inlet.
allows the operation and the pump control. If theinstallation has a long discharge pipe or a high
If a foot valve installation is not possible due to (pump
major than 15 Mts. it is necessary to install a quick
size or short space), other system like injectors or
closing check valve to avoid the water hammer in
vacuum pumps could be used for pump priming. For
more specific information, contact Hidrostal
For lower highs a standard check valve could be
engineering department or your Hidrostal local
used. If it is possible, elbows must be avoided
and replaced by long radius curves. The
MANUAL PUMP FOR SOLIDS
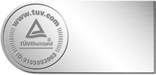
discharge pipe must be sized according to thepump flow rate, avoiding any flow velocity over 3
Mts./sec. The pump discharge size must not be aconditional for pipe discharge sizing. Remember to
prevent the connection for pump priming.
Sometimes it is convenient to install an expansionjoint to avoid the transmission of any discharge pipe
stress over the pump. (Due to thermal expansion,piping misalignment or due to any other reason).
Service Connection Nº. 1This connection is used to introduce sealing waterto the lantern ring (204). The water introduced to
this zone, seals, cools and lubricates the stuffing
box zone. This connection should be used if thefluid to be pumped is sewage water or water withsolids in suspension (Fig. 1.8).
1.2.8 Sealing System (Fig. 1.7)
Hidrostal pumps have a special connection toperform a shaft liquid sealing in the stuffing box.
If the pumped fluid is clean and contains no abrasiveparticles, the connection can be performed from thepump discharge.
If the fluid contains abrasive particles another source
of clean fluid must be slightly higher than the pumpdischarge pressure. In this case, you should take
in account that a portion of this fluid enters the pumpand the balance evacuates through part (101).
1.2.9 Service Connection (Fig. 1.7)
Hidrostal pumps are supplied with the possibility of
various service connections. These connections
should be applied according to the pump service.
MANUAL PUMP FOR SOLIDS

tendency are pumped. This connection can be
done replacing the last packing ring (205) byanother lantern ring (204) Fig. 1.9.
Sometimes the lantern ring position change ise n o u g h , d e p e n d i n g o n t h e p u m p e d f l u i dcharacteristic (204) Fig. 1.10.
The water introduced to this connection goes
directly to the shaft sleeve surface (208), nearthe impeller, avoiding the inlet of abrasive
materials and lubricating the stuffing box.
1.2.10 Instrumentation
To verify the functioning and the pump running
should be connected.
The pressure gages have to be mounted in aconvenient place for easy checking. A shut off
device must be placed before the pressuregauge. If the pump is driven by an electrical
motor, voltmeter, ampmeter and protectionelements must be placed in the switchboard.
If the fluid to be pumped contains small quantities
1.2.11 Final verification
of solids, this connection could be relaced by a
When the pipe installation is finished, check the
grease cup in order to introduce grease once in
alignment one more time; proceed according to
the ruler and gage method above mentioned.
lubricated. Use yellow grease ALVANIA Nº. 3
After the stuffing box adjusting and alignment
checking, the pump shaft should be hand rotated
(free and soft rotation).
Service Connection Nº 2 (E)
1.3 Starting
Used to introduce water inside the chamberformed by the back part of the impeller (401)and the back cover (200), in order to Clean
solids accumulations in this area.
Priming shoul be done before starting the pump,
Normally solids accumulatios occur when the
the suction pipes and the casing will be filled
concentrations with dehydration tendency. This
functioning of the pump without liquid, produces
service connection uses a solenoid valve with a
serious damage to the shaft or stuffing box.
timer to inject the water during 60 seconds fromtime to time. This water injection must be done
1.3.1.1 Positive Suction Pumps
as frequent as needed.
Close the discharge valve and open the suction
In vertical pumps this connection could be used
valve so that the liquid fills the pump. Open the
to evacuate the air accumulated in this area,
drain valve or drain plug located on the top of
especially when the fluid to be pumped has a
the pump and release air until the pump is
tendence to gasify.
completely filled with the liquid and air free.
Finally close the drain valve or screw the drain
Service Connection Nº 3 (F)
This is not a standard conection. It is used whenabrasive liquids or liquids with a crystallize
MANUAL PUMP FOR SOLIDS
1.3.1.2 Negative Suction Pumps
Close the discharge valve, open the priming
Open the admission and discharge valves.
connection and fill the pump casing completely
Check if the pump rotates hand free. Start the
(drain plug) (424). Once the pump is primed,
electrical motor and check the current with an
wait 5 minutes observing the liquid level inside
ammeter in order to avoid any overcharge.
the pump, the level should not vary. If the leveltends to diminish, proceed with the foot valve
In the case that the pressure does not increase
revision and repair it if necessary.
after pump start, it is a sign that air remains inthe suction. In such case, stop the pump
immediately and prime the pump again.
The pump should rotate in the direction indicated
The pump operation without water is harmful and
by the arrow in the casing. The rotation is in
could damage the pump in a short time.
clockwise direction, observing the pump from thedriver side.
1.3.5 Stopping
If the installation has a water hammer prevention
1.3.3 Stuffing Box
valve or if its T.D.H. is no major than 15 Mts., the
In the pumps supplied with stuffing box, the
detention of the motor is enough. In installations
where the T.D.H. is major than the indicated,
determinate application. Prior to the pump
proceed with the partial closing of the discharge
starting, verify the packing conditions, removing
the stuffing box gland (202) (Figs. 1.8, 1.9 and
necessary to avoid the reverse rotation of the
1.10). If the pump is not going to be used within
the first 60 days after its dispatch, a packinginspection is needed. If the period of disuse is
In automatic installations, if the detention is
longer, the packing should be checked and
produced by electrical energy failures, a new
replaced when its lubricant properties are lost or
manual starting is needed.
dryness occurs. In all cases it is important toremember to inspect the packings before pump
1.3.6 Initial and Periodical Checking
vibrations free.
2. Check the bearings temperature. Normally the
excessive leakage and eventually the cause of
temperature must be constant (maximun 70º).
shaft sleeve damages (208). An extra torque is
If the temperature starts to rise, check the
needed in the packing bolts in order to avoid an
excessive leakage.
Once the packings conditions have been verified,
3. Check the stuffing box for leaking according
start the pump as indicated in (1.3.4.) and adjust
to point 2 of 1.3.3 and for any overheating
the stuffing box as follows:
1. Make sure that the bolts in the stuffing box
gland are hand adjusted. In the first 10 min.
of operation, plenty filtration should appear.
temperature of the outlet side and the inletside is no major than 10ºC.
2. Adjust carefully the stuffing box gland bolts
(202) half turn every 10 min. until the spurt
5. Avoid any pump or motor overcharge.
turns into a constant dropping, approximately
6. When the pump works with negative suction,
20 drops/min.
installation is major than the NPSH required
periodically verified during the first week of
by the pump. The reservoir must be always
operation and be adjusted up to 20 drops/
full and free of materials that could cause
pump obstruction.
MANUAL PUMP FOR SOLIDS
7. The T.D.H. specified in the quotation must not
is corrosive or abrasive you must contact our
differ the installation T.D.H. In that case pump
engineering department or your Hidrostal local
failure could occur.
8. When a stand-by pump is available, it is
convenient to use it in an alternate way.
1.4 Periodical Maintenance
1.3.7 Service Characteristic
The Hidrostal pump has been designed to operatewith a determinate speed, T.D.H. and flow,
The bearings must be regularly lubricated. Use
according to the given information. If the T.D.H. is
good quality lithium soap grease, water resistant
different than the one indicated in he order, a
and appropriate for service temperatures between
motor overcharging could occur. It is necessary
-25ºC and 110ºC.
to fix this condition in order to obtain a goodequipment operation. Due to its special design
Apply only the necessary amount of grease (0.025
the solids handling Hidrostal pumps cannot be
kg. per bearing). Excessive grease application
throttled to reduce the motor charge as standard
could cause bearing overheating and failures. Use
centrifugal pumps.
multi-purpose grease Shell Alvania EP-2, MobiloilMultiplex 48 or equivalents.
To reduce the motor overcharge a new impellermust be placed in the pump according to the new
The bearings temperature measured in the
hydraulic conditions. In any case consult our
bearing frame external side should not exceed
engineering department or your nearest Hidrostal
local distributor.
1.3.8 NPSH
Before lubricating, establish the discharge of
(Net Positive Suction Head)
grease amount of your gun grease per eachshooting as follows:
If the pump does not comply with the specified flowrate, a variation in the NPSH available could be
1. Weight the grease amount obtained after 10
attributed to this condition. Each pump has its
own NPSH requirement curve as showed in the
2. Calculate the weight in grams per each shooting
characteristics pump curves. If the NPSH available
and mark this data on your gun grease.
is less than the NPSH required by the pump, the
Proceed to lubricate as follows:
pump is cavitating. Pump cavitation generates
a) Remove 134 and 154 plugs and start the pump
noises, vibrations, motor overcharge and flow rate
for at least 10 minutes in order to evacuate
the old remaining grease from the equipmentby bearing heating. (Fig. 1.7)
The liquid temperature and the altitude of the
b) Set back 134 and 154 plugs.
installation also affect the NPSH available.
(Remember that the atmosphere pressure varies
c) Clean up the lubricating points (G, G1 and G2).
with the altitude). An accurate calculation of NPSHavailable must be done when these conditions
Note: Bearing frame E2S does not have
appear. If the liquid to be pumped has a tendence
lubricating point G.
to gasify a positve suction pump is required.
d) The necessary grease amount in grams must
be injected in each lubricating point as
1.3.9 Corrosion and abrasion
indicated in the table 1.4.1.2.
When the fluid to be pumped has abrasive orcorrosive properties a correct pump material
1.4.2 Labyrinth seal
selection must be done. In this way costly pump
The pumps sealed with stuffing box have a
failures could be avoided. If the fluid to be pumped
labyrinth seal in order to avoid water inlet to the
MANUAL PUMP FOR SOLIDS
bearings. This seal must be lubricated by a
The pumps are supplied with the rings
grease cup (132), using the same bearing
quantities describied in the table 2.
grease according to the stuffing box conditions.
The grease cup must be adjusted until the
Table 2: Packing Rings Quantity
grease appears through the labyrinth seal.
(Fig. 1.7).
1.4.3 Sealing shaft system
It is necessary to check periodically that
the stuffing box dropping rate is in between
20 to 30 drops/min., allowing lubrication andrefrigeration of the stuffing box packing.
When the stuffing box gland (202) is beingadjusted in order to regulate the dropping rate;
make sure to do a half turn per time boltsadjustment. The stuffing box packing must be
replaced, when due to packing wear, the glandreaches the maximun adjustment.
1.4.4 Stuffing Box Packing Replace
Verify periodically that the liquid sealingconnection complies with the descriptions in
1. Loose and take away the stuffing box gland
chapter 1.2.8.
bolts (220) and slip it towards the support.
MANUAL PUMP FOR SOLIDS
2. Take away the stuffing box (201) bolts (221)
adjusted to the back cover (200) and slip istowards the bearing frame. take away thepacking ring (215) from the stuffing box.
3. Slip the lantern rings (204) along the shaft
towards the support and take away the packingrings (215) placed inside the back cover (200).
4. Clean up and lubricate with waterproof grease
the stuffing box cavities. Use yellow greaseA LVANIA Nº. 3, MOBIL-LUX Nº. 2 or itsequivalent.
5. Cut the packing rings according to the shaft
diameters (rolling the packing around acylinder with the same diameter than the pump
shaft). Avoid overtensioning the packings
(around the pump shaft) because leakageamong free spaces could occur, due to cutfailures (Fig. 1.12).
It is convenient to effectuate the cut in 45º
degrees way so that the packings will overlap.
6. Place the packing rings (215) inside the stuffing
box cavity in the back cover (200).
Use the latern ring (204) to push and introduce
the packing rings (215).
Place the packing rings 90º rotated (from the
cut). Install only the quantity of packing ringsneeded in order to place the latern ring exactlyin the water inlet drill hole (Nº. 1) (Fig. 1.8).
7. Place again the stuffing box (201) and fix it with
the stuffing box bolts (221). Do not forget toverify the packing (210) condition and location.
8. Place the missing rings (215) inside the stuffling
box cavity pushing it with the stuffing box gland(202). The packing ring ends (215) must beplaced at 90º from the other one. A specialcare should be taken in order to avoid the last
packing ring to overhang from the stuffing box,allowing in this way the correct placing of thestuffing box gland (202).
The lock nut should be tightened by hand.
9. Before pump starting, proceed as 1.3.3.
1.4.5 Impeller Clearance Adjustment
Check the clearence C between impeller and suction
casing must be 0.4-0.7 mm
MANUAL PUMP FOR SOLIDS
Table 1: Grease quantity according to bearing frames requirement
Point "G"
Point "G1"
Point "G2"
MANUAL PUMP FOR SOLIDS
1.4.6 Failure Causes
Failure Causes(Refer to the explanation below)
Pump does not deliver water
Pump priming loose after starting the pump.
Excessive pump power requirements.
Excessive stuffing box dropping.
Excessive packing ring wear.
Excessive pump vibrations or noises.
Pump clogging.
Bearig overheating (>70º)
Solids damage.
Rotating part in contact with stationary part.
Clogged pump, sand, etc.
Incorrect pump or suction pipe priming.
Wear rings excessive clearance.
NPSH available minor than NPSH required.
Damaged impeller.
Excessive amount of gas or air dissolved
Shaft sleeve (208) wear in packing rings
in the liquid.
Air pocket in suction pipe.
Packing rings or mechanical seal
Suction pipe air filtration.
Pump suction inlet does not have enought
Incorrect packings for operation conditions.
Low pump velocity.
Misaligned pump shaft due to bearing wear.
High pump velocity.
Stuffing box gland bolts overtightened.
Wrong pump shaft rotation.
Poor lubrication.
System TDH major than pump TDH design.
Loose anchor of foundation bolts.
System TDH minor than pump TDH design.
Wrong lubrication.
Pumped fluid densify differs from design
fluid density.
Small sized impeller.
Pumped fluid viscosity differs from design
Pump has not been primed.
fluid viscosity.
High solids concentration in relation with
Low flow pump operation.
pump velocity.
Incorrect pumps engagement not designed
Cavitation (fluid with gas or air in pump
to operate in parallel.
Impeller clogging by strange bodiespresence.
Pump and motor misalignment.
Bended shaft.
/110 1 Be aware that the failure causes above mentioned do not necessarily correspond to the real failure reasons.
400 Therefore we recommend checking the equipment by a pump equipment service expert.
MANUAL PUMP FOR SOLIDS
Portada del Sol 722 - Lima 36, Perú
Apartado Postal 3989 - Lima 1, Perú
Página web: www.hidrostal.com.pe
Servicio al Cliente: 0801 - 1 00 00
Source: http://www.hidrostal.com.pe/images_turbinas/manual-solids-type-f-v.b.10-11.pdf
Samantha hopes future generations won't have to live with Dr. Horner's breakthrough research could mean they won't have to. Supported by an educational grant from The Allergan Foundation. "Glaucoma Research Foundation is dedicated to improving the lives of
See discussions, stats, and author profiles for this publication at: DATASET in SOUTH AFRICAN JOURNAL OF BOTANY · JULY 2011Impact Factor: 0.98 · DOI: 10.1016/j.sajb.2011.07.003 5 AUTHORS, INCLUDING: 43 PUBLICATIONS 245 CITATIONS 54 PUBLICATIONS 706 CITATIONS 232 PUBLICATIONS 2,405 CITATIONS