Untitled
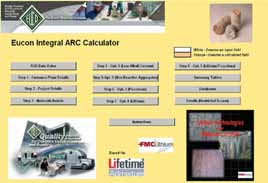
Economics of Lithium Technology for
ASR Control vs. Alternatives
By Claudio Manissero, Sales and Marketing Manager, FMC Corporation, Lithium Division
Randall Stewart, Lithium Technology Manager, The Euclid Chemical Company
Concrete durability, and more specifically Alkali Silica Reac-
tivity (ASR) is fast becoming an item of great concern toowners following research conducted under the StrategicHighway Research Program (SHRP) and more recently
the Innovative Pavement Research Foundation (IPRF). Even thoughthe issue of ASR has been around for several decades this research hasshown that traditional ways to address the issue were not as effective asoriginally thought, and field evidence of ASR occurrences in concretehave proven this, resulting in agencies and owners having to modifytheir specifications incorporating new technologies to minimize therisk of ASR.
Why is this of concern to the ready mixed producer? After all, ASR
does not show up as cracking and expansion for years, considerablyafter the concrete has been placed and paid for by the owner. To quoteJC Roumain, Holcim Cement, "The biggest competitive threat toconcrete is BAD concrete." In other words, if the concrete placed doesnot meet the design life expectancy, or if the concrete placed requires
ASR Options Calculator Spreadsheet
significantly more maintenance than planned, then the life cycle costarguments that clearly show that concrete is the material of choicebecome suspect, and force the owners to seek alternatives. One of the
ASR Mitigation Options - Materials Costs
first steps taken is to change the specifications by requiring tightertesting procedures, but allowing options on how to meet the
NOT VIABLE
standards. One of the new options that is appearing in a number of
Low Alkali Cement
specifications is the use of lithium admixtures. Since this is new, it is a
largely unknown option thus very difficult to evaluate with regards to
NOT VIABLE
developing bids utilizing this option. In addition, the rumor in the
marketplace is that lithium is "too expensive". As a consequence a
Lithium Only
producer is too often likely to ignore this option and bid using better
Low Alkali Cement
Lithium Plus
known options, at times ending up losing the bid to a more savvy
producer who took the time to fairly evaluate all options and realized
that the lithium option is not only an economical option, but at timesthe lowest cost option available to meet the specification requirements.
It is the purpose of this article to dispel rumors regarding lithium
Example of Comparative Chart from ASR Calculator
technology and assist the producer in fairly evaluating options
While obviously not exhaustive, these examples demonstrate that lithium
available to meet ASR requirements, and producing bids that will be
technology is a practical, economically viable alternative that should be
competitive and profitable.
considered when allowed in spite of its reputation of being "tooexpensive". Like all other new technologies, the reputation came from the
According to state-of-the-art specifications, the options available for
fact that it is difficult to understand the cost of the technology without
ASR mitigation are:
having considered all aspects, and providing a means to evaluate its cost
1. Use of non-reactive aggregates;
compared to the other alternatives available. The purpose of this paper is
2. Use of suitable pozzolans;
to dispel these rumors and provide the ready mixed producer a better
3. Use of lithium admixtures; and
understanding of how to evaluate relative costs and make the best
4. Use of combinations of pozzolans and lithium.
economical decisions in the bidding process.
CONCRETE in focus ı 43
In the new specs, these options must pass tests that are specified,
new aggregates and adjust accordingly to avoid any potential
which are usually modifications of ASTM C 1260, Test Method for
production issues.
Potential Alkali Reactivity of Aggregates (Mortar-Bar Method). When
2. Use of suitable pozzolans
deicing compounds are used that are salts of sodium or potassium,
The most common pozzolan that can be used to prevent ASR is fly
such as on airfield pavements, additional testing requirements may
ash. However, not all fly ashes are alike. The most suitable ashes are
include a further modification of this test that incorporates the deicer
Class F fly ashes with a low lime (less than 8% CaO) content. In most
in the soak solution used in the test. A number of researchers
cases Class C fly ash is not acceptable or allowed. When using Class F
recommend that ASTM C 1293, Test Method for Determination of
ashes with a medium to high lime content (e.g. greater than 8%)
Length Change of Concrete Due to Alkali-Silica Reaction, be used to
testing must be conducted and the amount needed may be so high as to
evaluate mixes, but this test takes two years for the results and
cause real issues in set time, strength gain and in obtaining the
therefore is not practical for construction purposes and, even though
necessary amount of air in the mix (mostly dependent on the LOI of
allowed on some specifications, it is very seldom adopted.
the ash). In addition, due to recent changes in the Clean Air Act that
A traditional way of combating ASR was to utilize low alkali
resulted in changes that power plants had to make in order to meet the
cement at below 0.6% sodium oxide equivalent (Na
new regulations, availability of good Class F ash has been decreasing
2O eq.). Over the
years it has become apparent that this approach did not work as
and is more difficult to get. Pricing of good quality Class F ash has also
effectively as was previously thought. The important parameter should
been increasing due to demand outstripping supply. The amount of
have been total alkali of a mix rather than the alkali percentage of the
Class F ash needed is based on the reactivity of the aggregates and
cement component. In addition, this approach cannot compensate for
should be determined by testing.
external sources of alkali such as some deicing salts. In some areas
Ground granulated blast furnace slag (GGBFS) may not be an
where very low alkali cements are available (e.g. 0.4% Na
option in cases where it is not readily available or the amount needed is
lower), and the aggregates are moderately to mildly reactive and there
too high to combat ASR where the new deicer ASR testing is used for
are no sources of external alkali, this approach is still a viable option.
airfield pavements (See Northwest Mountain Region Federal Aviation
When the ready-mix producer is faced with having to bid on a
Administration specification P-501, modified June, 2006), scaling is an
project with specifications for ASR allowing those options, care should
issue or there are concerns with finishing and curing concrete if not
be taken in evaluating and costing out each option prior to submitting
handled properly.
a bid. This evaluation may take some effort at first, but once the
Silica fume can be effective, however, care must be taken to ensure
producer has determined his costs using locally available materials, this
proper mixing and dispersion in the mix because clumps of silica fume
evaluation becomes significantly easier for future bids. This evaluation
in a mix can be the cause of ASR. Price of silica fume is also higher than
will improve the chances of winning the bid based on the most
cement, thus its use will in most cases increase cost significantly.
economical option for the particular job, and allows the producer to
Natural pozzolans can be very effective, but their availability is very
increase his/her margins by minimizing risk and variability
scarce throughout the US. If a pozzolan is used, in order to fully
encountered when actually producing a job. Let's examine what the
evaluate the costs the producer should ensure availability, determine if a
cost factors are with each option.
silo is available for the material or make arrangements for one to be
1. Use of non-reactive aggregates (both coarse and fine)
installed, and mix design testing should be conducted.
This sounds like an obvious solution, however tests have gotten
3. Use of lithium admixtures
tougher over the years so that some aggregates that historically passed
Lithium admixture (nominal 30% lithium nitrate solution) can be
the tests are now deemed to be potentially reactive. Historical data for
used with any aggregate source and allows the use of any local materials.
a particular aggregate is proving, at least in some instances, not to be a
Amount of admixture needed is based on the alkali content of the mix
reliable indicator due to changes in the aggregate characteristics in
from the cement. Manufacturer recommendations for most aggregates
different parts of a quarry. Availability of non-reactive aggregates has
is 0.55 gallons of admixture for each pound of alkali supplied in a cubic
also decreased over time, as their use was preferred in the past. Since
yard of concrete, so the amount needed is based on both the quantity of
reactivity of the aggregate is due to its mineralogy, it is unlikely that if
cement used and the alkali content (Na2O % equivalent in the mill
a particular aggregate were determined to be potentially reactive other
report). This is referred to as the 100% dosage. Certain aggregates may
aggregates from nearby sources would test as non-reactive. In many
require more than the 100% dosage, which can be ascertained by
cases, non-reactive sources may need to be imported from distant
conducting the required testing. Using low alkali cement can minimize
locations. Cost of transportation of aggregates must be taken into
cost for this option. Lithium can be added as any other admixture and
account and at present fuel prices this can significantly impact the
in most cases addition of lithium will have minimal effect on the
total cost. The producer must bear in mind that trucks must get to the
properties of the mix except for a slight acceleration of setting time.
aggregate supplier empty and return full, thus transportation costs
Care must be taken to ensure that according to manufacturer
must be figured at twice the distance. In addition, the cost of the
recommendations, 0.85 gallons of water must be removed for each
aggregates will most likely be higher if they are not from the standard
gallon of admixture added to maintain the proper w/c ratio.
supplier or the producer's quarry, and provisions must be made to
4. Use of combinations of pozzolans and lithium
isolate the nonreactive aggregate from the aggregate normally used at
This option combines the good qualities of both of the other
the plant. Finally, in most cases it is prudent to test your mix with the
options while reducing the cost of the mix. In general, it is possible to
CONCRETE in focus ı 45
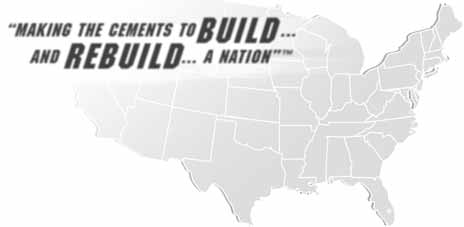

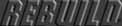

substantially reduce the amount of lithium needed in the mix by using it
them to demonstrate the methodology. The figures in these examples
in combination with a suitable pozzolan. The most common practice is
are fictitious for illustrative purposes only - so you should adjust the
to use it in combination with Class F fly ash. The concept is to maximize
figures to reflect your actual costs of materials and manufacturing.
the amount of Class F fly ash used while meeting needed set times and
The actual bid price should be established based on other costs and
strength gain requirements, then top it off with lithium to achieve the
anticipated margin. While the examples are based on actual recent
desired ASR testing results. As a guideline, dosage can be reduced to 52%
specification requirements, any reference to a specific project should
of the dosage when the mix includes 25% (by weight of cementitious
be avoided and is not implied. Each circumstance and each job will
materials) low CaO content Class F fly ash. Lithium dosage is also
be different.
decreased by the fact that it is calculated on the basis of portland cement;
1.) Example 1 – Pavement in a southern state.
therefore it is lowered by the fact that a portion of the cement was
Requirements – Mix must meet ASTM C 1567, Test Method for
replaced with the pozzolan.
Determining the Potential Alkali-Silica Reactivity of Combinations of
It is possible to design a mix incorporating Class C fly ash by the
Cementitious Materials and Aggregate (Accelerated Mortar-Bar
addition of lithium; however with most Class C fly ashes the lithium
Method)¸ testing with a maximum expansion of 0.10% at 14 days.
dosage will have to remain at 100% and in fact can be higher than the
(This procedure is a modification of ASTM C 1260 that evaluates
standard dosage. Of course in these cases the amount of lithium will be
cementitious aggregate combinations.) Standard mix requires 6.5
decreased by the fact that the mix will have lower cement content.
sacks of cement (611 lbs) for the desired strength at 0.45 w/c. The
Testing must be conducted in order to determine if a mix with Class C
project has tight timelines and penalties for lateness. The four
fly ash is a real option with locally available materials.
options discussed above are allowed. Class C fly ash is not allowed.
Lithium can also be used in combination with silica fume, though
Note: Both aggregates (coarse and sand) you have available are
due to price of silica fume this is mainly applicable only to bridge decks.
marginally reactive as measured by ASTM C 1260 at 14 days. The
No testing has been conducted on the use of lithium in combination
cement you have available is low alkali cement at 0.48% Na2O eq.
with GGBFS, so testing must be conducted in order to determine if
You have a silo for fly ash, which presently holds Class C fly ash. A
lithium dosage can be decreased.
good low lime (5.0% CaO) Class F fly ash is available.
So how do you put all the information together and develop figures
for cost of the mix for the different options so you can decide how to bid
Your standard mix (without the Class C fly ash) for 6.5 sacks is as
a particular project? Let's look at a couple of examples and work through
I BETHLEHEM
# MARYNEAL
L New Orleans
BUZZI UNICEM USA®
100 Brodhead Road
Suite 230
L Slag Grinding Plant
Bethlehem, PA 18017
I Corporate Office
*2004 Combination of RC Cement and Lone Star Industries
46 ı FALL 2006
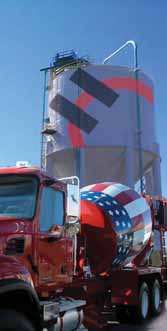

The closest source of nonreactive coarse aggregate you find is 45
miles (90 miles roundtrip). Since it is a new source your cost is
$ 9.50/ton. Therefore your coarse aggregate cost becomes:
(Amount of aggregate x cost of aggregate) + (transportation cost x
Admixtures, etc.
(1884 lbs x (9.50/2000)) + (1884 x (0.12/2000) x 90) = 8.95 +
The closest source of nonreactive sand you find is 55 miles (110
miles roundtrip). Since it is a new source your cost is $ 7.25/ton.
Therefore your sand cost becomes:(1541 x (7.25/2000)) + (1541 x (0.12/2000) x 110) = 5.58 + 10.17 =
Assume that the following are your additional costs/cu yd
Interest on money (90 day pay, 6.0 % PA)$0.58Operating costs
Finally your operating costs would increase an estimated
$ 0.50/cu yd if you take into account that you will have to store and
Fixed/Capital costs
manage separate piles of aggregates.
So if you total in the changes
Total cost per cu yd
Unit Cost Cost/cu yd
Option 1 - Nonreactive aggregate
Estimate your transportation cost. Excellent rates from a common
carrier currently run around $ 0.20/ton/mile on the low end. For a
Admixtures, etc.
captive truck fleet to carry out the hauling, this cost should include
fuel cost (minimum of $ 0.035/ton/mile), cost of a driver, and
amortization of truck, taxes, insurance, maintenance cost and a usage
factor. A conservative estimate is $ 0.12/ton/mile.
We stand behind the strength
of our technical service and the
performance of our products
with the passion to meet the
needs of our customers.
As one of the largest suppliers of portlandcement in the United States, you can counton our support. Holcim - a global companyproviding local solutions.
Corporate Headquarters
Holcim (US) Inc.
6211 Ann Arbor Road
149205_Holcim.indd 1
ocus ı 47
Assume that the following are your additional costs/cu yd
Interest on money (90 day pay, 6.0 % PA)
Fixed/Capital costs
Admixtures, etc.
Total cost per cu yd
Option 2 - Use of suitable pozzolans
Your price for Class F fly ash is $ 65/ton delivered. You can only
Assume that the following are your additional costs/cu yd
pass the ASR testing using 30% ash substitution. At this level you
Interest on money (90 day pay, 6.0 % PA)
cannot obtain the strength using 1:1 substitution, therefore you have
to resort to 1.2 lbs of fly ash for each pound of cement replaced.
Since the testing showed that to control ASR you needed 30% by
Fixed/Capital costs
weight of cementitious materials; the amount of fly ash you will need
is 611 x 0.3 = 183 lbs, the amount of cement in the mix will be 611 –
(183/1.2) = 459 lbs cement.
Total cost per cu yd
In addition, you do not have a silo so you must install a new silo
adding to the fixed/capital costs. You also need to plan to increase the
Option 4 - Use of combinations of
amount of air-entraining admixture to maintain air.
pozzolans and lithium
In this combination, the ASR tests can be met by lowering the
Your costs can be expected to be as follows:
Class F fly ash needed to 25% of the cementitious material and
topping off with a reduced amount of lithium. At this level of ash
when combined with lithium the strength gain requirements can be
met using 1:1 substitution of cement. The amount of lithium
required is expected to be 52% of the 100% dosage, even though
testing should be conducted to confirm this. To determine the
Admixtures, etc.
amount of lithium needed first calculate the amount of Class F fly
ash used in the mix which will be 611 x 25% = 153 lbs of ash. From
that determine amount of cement, 611 – 153 = 458 lbs. Then use the
formula with the reduction factor to calculate the amount of lithium:
458 lbs x 0.48 % alkali x 0.55 gals/lb alkali x 52% reduction =
Assume that the following are your additional costs/cu yd
Interest on money (90 day pay, 6.0 % PA)
Your costs can be expected to be as follows:
Fixed/Capital costs
Total cost per cu yd
Option 3 - Use of lithium admixtures
Admixtures, etc.
Use a price of $ 15/gal as a budget price. This is a figure used by
owners in recent RFP documents, which allow lithium. This figure
does include a fair margin for the ready mixed producer. Actual pricing
is dependent on quantity and location for freight from manufacturingsites. Product is readily available nationwide. To calculate amount
Assume that the following are your additional costs/cu yd
Interest on money (90 day pay, 6.0 % PA)
611 lbs cement x 0.48% Na2O equivalent x 0.55 gals = 1.6 gals of
30% lithium nitrate solution
Delivery cost (20 miles)
Use of lithium allows the use of the local aggregates, does not
Fixed/Capital costs
affect properties of the mix, and will not require any capital
investment (material storage and feeding systems supplied by the
admixture company).
Total cost per cu yd
CONCRETE in focus ı 49
Option 2 - Lithium admixture
In this example, it is clear that if all the other requirements of the job
100% dosage of lithium would be
can be met with the use of the Class F fly ash, then this alternative is the
705 lbs cement x 0.48% Na2O equivalent x 0.55 gals = 1.9 gals
most cost effective (Option 2). However, it can also be seen that if you go
30% lithium nitrate solution
with straight lithium admixture the cost would be approximately the
same as using non-reactive aggregate. The combination of pozzolan and
lithium is significantly less than the use of non-reactive aggregates. This is
generally true if the aggregate has to be transported any distance. In fact
in this example if you work though the numbers this is true if the
Admixtures, etc.
aggregates have to be transported 10 miles or more.
When would using lithium be a better option overall? In some cases,
the lithium is a separate line item that can be charged separately. In thesecases it can be seen that the combination of pozzolan and lithium is the
Assume that the following are your additional costs/cu yd
most cost effective alternative, and your margin would be larger because
Interest on money (90-day pay, 6% PA)
of the additional margin to be gained from the lithium at the budgeted
price. What would be the best alternative if no Class F fly ash were
Delivery cost (20 miles)
available? In this case it probably would be the lithium alone, because
Fixed/Capital costs
there are other advantages to using your standard supply of aggregates,
you can better predict how the mix will perform, and you have the built
in margin for the lithium.
Total cost per cu yd $99.32
2.) Example 2 - Airfield pavement in the Midwest
Option 3 - Combination of lithium with Class F fly ash
In this example the basic mix is based on 7.5 sacks of cement for
strength gain at 0.4 w/c. ASR testing requirements include passing a
Amount of F Ash 705 x 0.25 % = 176 lbs
modified ASTM C 1260 at 28 days at 0.1% expansion, and the new
Amount of cement 705 – 176 = 529 lbs
experimental deicer evaluation test1 (a modification to C 1260 whereby
Amount of lithium
the bar is immersed in deicer solution). The strength requirements are for
529 lbs x 0.48% Na2O equivalent x 0.55 gals x 52% = 0.73 gal
7-day flexural strength of 650 psi. The job has strict timetables andsignificant penalties for delays. No Class C fly ash or GGBFS are
allowed. All four options previously discussed are allowed. Lithium is
paid separately at a budget price of $ 15 / gal.
Note: all materials available and costs are the same as the first example,
except that the Class F fly ash available has moderately high lime content
(e.g. > 7.5%). Testing indicates that with locally available allowed pozzolans,
Admixtures, etc.
no mix with straight pozzolan will pass both the flexural strength
requirements and the ASR testing. Real options are: 1) non-reactive
aggregates, 2) lithium, 3) combination of lithium with Class F fly ash.
Using the same methodology as above the following are the relative costs:
Option 1 - Non-reactive aggregate
Assume that the following are your additional costs/cu yd
Interest on money (90-day pay, 6 % PA)
Delivery cost (20 miles)
Fixed/Capital costs
Admixtures, etc.
Total cost per cu yd
From these calculations it is obvious that the combination of Class F
Assume that the following are your additional costs/cu yd
fly ash with lithium is the most cost effective. Even though straight
Interest on money (90-day pay, 6 % PA)
lithium appears a bit more expensive than nonreactive aggregates, it is
still the second best option because lithium is paid separately as a line
Delivery cost (20 miles)
item, which is not available with the non-reactive aggregates option.
Fixed/Capital costs
While going through the process for determining what the actual
Total cost per cu yd $94.66
50 ı FALL 2006
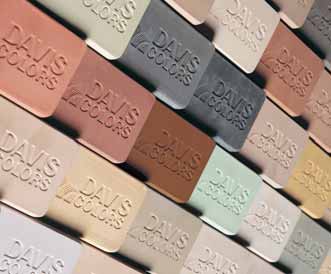
costs of alternatives provided in thespecifications to address ASR are, anunderstanding of the methodology and usingit to cost out a project may make thedifference between winning or losing a bid. Inaddition, the methodology can help to insurethat all costs are taken into account duringthe bidding process and you do not findyourself in the situation of having bid too lowand risk losing money on a project. TheEuclid Chemical Company and FMCCorporation have collaborated to develop aspreadsheet that allows comparison of thealternatives and develop accurate costs for allthe alternatives avoiding a lot of thepaperwork. While this spreadsheet is in a Betaversion, representatives of either company canaccess the worksheet to help you implementthe methodology.
To reach the authors, contact:
Claudio Manissero, FMC Corporation,
Lithium Division, 2801 Yorkmont Road,Suite 300, Charlotte, NC 28208, 704-868-5305, [email protected]
Randall Stewart, The Euclid Chemical
All you need to know
Company, 19218 Redwood Road, Cleveland,OH 44110, 775-324-1590, RStewart@euclid
about concrete color.
The views and opinions expressed in this
Just one call is all it takes to learn how Davis Colors can provide you
with the number one concrete color brand in America, the most
article are those of the author and do not neces-
widely used automatic dosing systems, and the personalized
sarily reflect the views and opinions of the
marketing tools that will help you build your business. Call
National Ready Mixed Concrete Association.
800-356-4848 ext. 323 or visit www.daviscolors.com.
1This evaluation and specification requirement is
primarily in the FAA P-501 specification and is in
response to aggressive deterioration, attributed to ASR,
as a result of the use of newer pre-snow deicing
Tel: 800-356-4848 Fax: 323-269-1053 www.daviscolors.com
P I G M E N T S
2004 Davis Colors, a brand of Rockwood Pigments, Inc.
chemicals, such as potassium acetate. The evaluation
of the cause of deterioration and mitigative testing
procedures is currently being researched.
For more information
please check out our
web site at www.nrmca.org
CONCRETE in focus ı 51
Source: http://www.nrmca.org/research/cif%2006-4%20asr.pdf
NAME OF THE MEDICINAL PRODUCT: Aprotinin 10,000 KIU/ML Injection BP. PRESENTATION: Each 50ml 1 vial of 50 mL contains aprotinin concentrated solution, corresponding to 500,000 KIU (Kallikrein Inhibitor Units) in sterile 0.9% sodium chloride solution. INDICATIONS: Aprotinin is indicated for prophylactic use to reduce blood loss and blood transfusion in adult patients who are at high risk of major blood loss undergoing isolated cardiopulmonary bypass graft surgery (i.e. coronary artery bypass graft surgery that is not combined with other cardiovascular surgery). Aprotinin should only be used after careful consideration of the benefits and risks, and the consideration that alternative treatments are available. POSOLOGY AND METHOD OF ADMINISTRATION: Posology: An appropriate aprotinin-specific IgG antibody test may be considered before administration of aprotinin. Adult: Owing to the risk of allergic/anaphylactic reactions, a 1 ml (10,000 KIU) test dose should be administered to all patients at least 10 minutes prior to the remainder of the dose. After the uneventful administration of the 1 ml test dose, the therapeutic dose may be given. A H1-antagonist and a H2-antagonist may be administered 15 minutes prior to the test dose of aprotinin. In any case standard emergency treatments for anaphylactic and allergic reactions should be readily available (see section 4.4). A loading dose of 1 - 2 million KIU is administered as a slow intravenous injection or infusion over 20 - 30 minutes after induction of anaesthesia and prior to sternotomy. A further 1 - 2 million KIU should be added to the pump prime of the heart-lung machine. To avoid physical incompatibility of aprotinin and heparin when adding to the pump prime solution, each agent must be added during recirculation of the pump prime to assure adequate dilution prior to admixture with the other component. The initial bolus infusion is followed by the administration of a continuous infusion of 250,000 - 500,000 KIU per hour until the end of the operation. In general, the total amount of aprotinin administered per treatment course should not exceed 7 million KIU. Paediatric population - The safety and efficacy in children below 18 years of age have not been established. Refer to Summary of Product Characteristics for use in other specific patient populations. Aprotinin should be infused using a central venous catheter. The same lumen should not be used for the administration of any other medicinal product. When using a multi-lumen central catheter a separate catheter is not required. Aprotinin must be given only to patients in the supine position and must be given slowly (maximum 5 - 10 ml/min) as an intravenous injection or a short infusion. CONTRAINDICATIONS: Hypersensitivity to the active substance or any of the excipients. Patients with a positive aprotinin specific IgG antibody test. If no such test is possible prior to treatment, administration of aprotinin to patients with a suspected previous exposure including in fibrin sealant products during the last 12 months is contraindicated. SPECIAL WARNINGS AND PRECAUTIONS FOR USE: Aprotinin should not be used when CABG surgery is combined with another cardiovascular surgery because the benefit risk balance of aprotinin in other cardiovascular procedures has not been established. Laboratory monitoring of anticoagulation during cardiopulmonary bypass: Aprotinin is not a heparin-sparing agent and it is important that adequate anticoagulation with heparin be maintained during aprotinin-therapy. Elevations in the partial thromboplastin time (PTT) and celite. Activated Clotting Time (Celite ACT) are expected in aprotinin-treated patients during surgery, and in the hours after surgery. Therefore, the partial thromboplastin time (PTT) should not be used to maintain adequate anticoagulation with heparin. In patients undergoing cardiopulmonary bypass with aprotinin therapy, one of three methods is recommended to maintain adequate anticoagulation: Activated Clotting Time (ACT), Fixed Heparin Dosing, or Heparin Titration (see below). If activated clotting time (ACT) is used to maintain adequate anticoagulation, a minimal celite-ACT of 750 seconds or kaolin-ACT of 480 seconds, independent of the effects of haemodilution and hypothermia, is recommended in the presence of aprotinin. Important: aprotinin is not a heparin-sparing agent. Graft Conservation: Blood drawn from the aprotinin central infusion line should not be used for graft preservation. Re-exposure to aprotinin: Administration of aprotinin, especially to patients who have received
Manual on LaserEmitters andFlight Safety Approved by the Secretary Generaland published under his authority First Edition — 2003 International Civil Aviation Organization Manual on LaserEmitters andFlight Safety Approved by the Secretary Generaland published under his authority First Edition — 2003