Corel office document
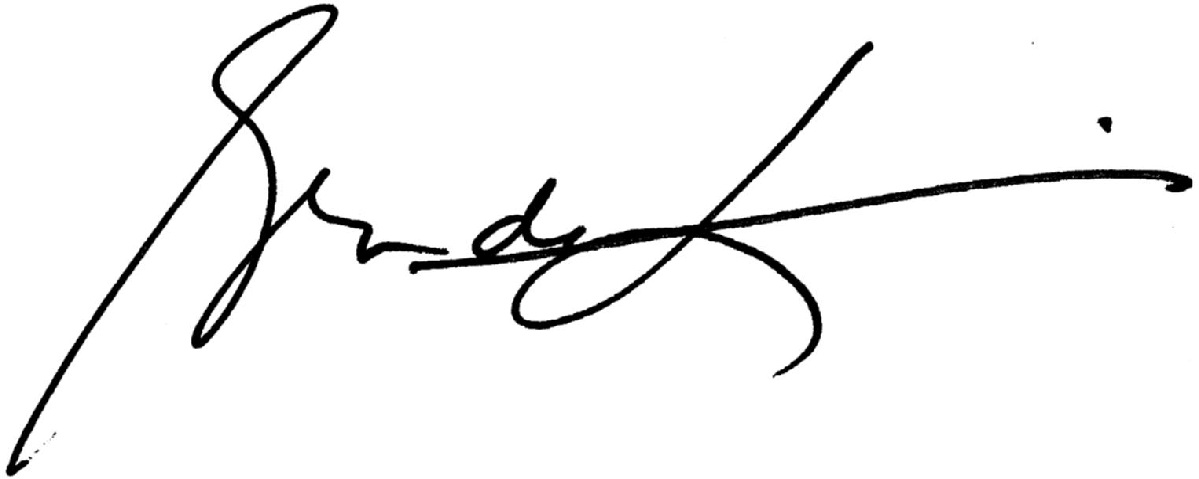
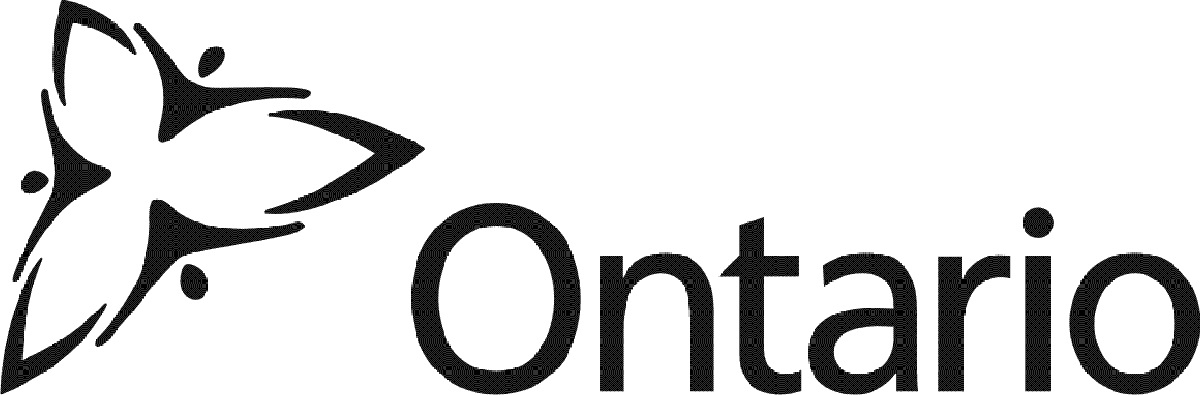
M inistry of
M inistère des
M unicipal Affairs
and Housing
et du Logem ent
Building and Development Branch
Direction du bâtiment et de l'aménagement
777 Bay Street, 2nd Floor
777, rue Bay, 2e étage
Toronto ON M5G 2E5
Toronto ON M5G 2E5
Telephone: (416) 585-6666
Téléphone : (416) 585-6666
Fax: (416) 585-7531
Télécopieur : (416) 585-7531
TO: BUILDING CODE USERS
The enclosed Building Code Compendium replacement pages reflect recent amendments to the BuildingCode (O. Reg. 350/06) and Minister's Rulings. In particular, the Building Code Compendium is amendedby:
• Minister's Ruling MR-13-S-22 to update Supplementary Standard SB-5 with respect to amending
approved systems and which came into effect January 16, 2013.
• Minister's Ruling MR-13-S-23 to update Supplementary Standard SB-12 to recognize the use of drain
water heat recovery units and which came into effect March 15, 2013.
These amendments to the Building Code are identified on the enclosed pages by a unique symbol and acorresponding effective date. These pages should be inserted in your Code now.
ServiceOntario Publications is the official publisher and vendor of the 2006 Building Code and theamendment pages. You may contact ServiceOntario Publications by phone at 416-326-5300, 1-800-668-9938 (toll-free) or www.serviceontario.ca/publications.
For further information on the amendments, please visit the Building Code website atwww.ontario.ca/buildingcode or call 416-585-6666.
Brenda LewisDirector
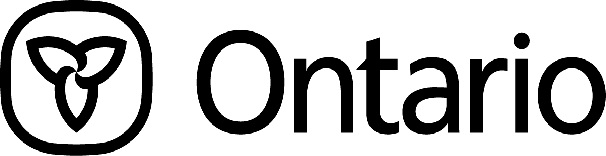
M inistry of M unicipal Affairs and Housing
Building and Developm ent Branch
2006 Building Code Compendium
July 1, 2013 update
(containing Minister's Rulings MR-13-S-22 and MR-13-S-23)
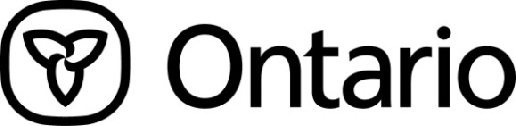
2006 Building Code Compendium
Ontario Regulation 350/06 comes into force on the 31st day of December, 2006.
Amending Ontario Regulation 423/06 comes into force on the 31st day of December, 2006.
Ruling of the Minister of Municipal Affairs and Housing (Minister's Ruling) MR-06-S-01 takes effect on the 31st day of December, 2006.
Amending Ontario Regulation 137/07 comes into force on the 2nd day of April, 2007.
Amending Ontario Regulation 137/07 comes into force on the 1st day of July, 2007.
Amending Ontario Regulation 205/08 comes into force on the 1st day of April, 2010.
Amending Ontario Regulation 365/09 comes into force on the 24th day of September, 2009.
Amending Ontario Regulation 503/09 comes into force on the 1st day of January, 2010.
Amending Ontario Regulation 503/09 comes into force on the 1st day of April, 2010.
Amending Ontario Regulation 503/09 comes into force on the 1st day of July, 2010.
Amending Ontario Regulation 503/09 comes into force on the 1st day of January, 2011.
Amending Ontario Regulation 503/09 comes into force on the 1st day of January, 2012.
Amending Ontario Regulation 315/10 comes into force on the 1st day of January, 2011.
Amending Ontario Regulation 315/10 comes into force on the 1st day of January, 2016.
Amending Ontario Regulation 315/11 comes into force on the 1st day of July, 2011.
Amending Ontario Regulation 159/12 comes into force on the 1st day of July, 2012.
m Ruling of the Minister of Municipal Affairs and Housing (Minister's Ruling) MR-07-S-02 takes effect on the 9th day of March, 2007.
m Ruling of the Minister of Municipal Affairs and Housing (Minister's Ruling) MR-07-S-03 takes effect on the 2nd day of April, 2007.
m Ruling of the Minister of Municipal Affairs and Housing (Minister's Ruling) MR-08-S-04 takes effect on the 1st day of April, 2010.
m Ruling of the Minister of Municipal Affairs and Housing (Minister's Ruling) MR-08-S-05 takes effect on the 18th day of June, 2008.
m Ruling of the Minister of Municipal Affairs and Housing (Minister's Ruling) MR-09-S-06 takes effect on the 2nd day of June, 2009.
m Ruling of the Minister of Municipal Affairs and Housing (Minister's Ruling) MR-09-S-07 takes effect on the 9th day of June, 2009
m Ruling of the Minister of Municipal Affairs and Housing (Minister's Ruling) MR-09-S-08 takes effect on the 1st day of January, 2010.
m Ruling of the Minister of Municipal Affairs and Housing (Minister's Ruling) MR-09-S-09 takes effect on the 1st day of January, 2010.
m Ruling of the Minister of Municipal Affairs and Housing (Minister's Ruling) MR-09-S-10 takes effect on the 1st day of April, 2010.
m Ruling of the Minister of Municipal Affairs and Housing (Minister's Ruling) MR-09-S-11 takes effect on the 1st day of January, 2011.
m Ruling of the Minister of Municipal Affairs and Housing (Minister's Ruling) MR-10-S-12 takes effect on the 1st day of October, 2010.
m Ruling of the Minister of Municipal Affairs and Housing (Minister's Ruling) MR-11-S-13 takes effect on the 17th day of February, 2011.
m Ruling of the Minister of Municipal Affairs and Housing (Minister's Ruling) MR-11-S-14 takes effect on the 11th day of March, 2011.
m Ruling of the Minister of Municipal Affairs and Housing (Minister's Ruling) MR-11-S-15 takes effect on the 22nd day of June, 2011.
m Ruling of the Minister of Municipal Affairs and Housing (Minister's Ruling) MR-11-S-16 takes effect on the 1st day of July, 2011.
m Ruling of the Minister of Municipal Affairs and Housing (Minister's Ruling) MR-11-S-17 takes effect on the 1st day of January, 2012.
m Ruling of the Minister of Municipal Affairs and Housing (Minister's Ruling) MR-11-S-18 takes effect on the 7th day of December, 2011.
m Ruling of the Minister of Municipal Affairs and Housing (Minister's Ruling) MR-12-S-19 takes effect on the 13th day of June, 2012.
m Ruling of the Minister of Municipal Affairs and Housing (Minister's Ruling) MR-12-S-20 takes effect on the 1st day of July, 2012.
m Ruling of the Minister of Municipal Affairs and Housing (Minister's Ruling) MR-12-S-21 takes effect on the 1st day of July, 2012.
m Ruling of the Minister of Municipal Affairs and Housing (Minister's Ruling) MR-13-S-22 takes effect on the 16th day of January, 2013.
m Ruling of the Minister of Municipal Affairs and Housing (Minister's Ruling) MR-13-S-23 takes effect on the 15th day of March, 2013.
Issued April 2nd, 2007.
Issued June 2nd, 2009.
Issued January 1st, 2010.
Issued July 1st, 2011.
Issued July 1st, 2012.
Copyright Queen's Printer for Ontario 2013
ISBN 978-1-4435-2071-3 (set)
ISBN 978-1-4435-2072-0 (vol.1)
All rights reserved.
Questions regarding copyright, including reproduction and distribution, may be directed to the Director, Building and Development Branchof the Ministry of Municipal Affairs and Housing.
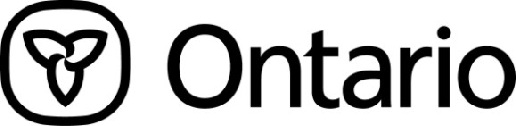
2006 BUILDING CODE COMPENDIUM
Code Amendment History
The first Ontario Building Code was issued in 1975. The 1975 and subsequent editions of the Building Code have beenissued as follows:
Building Code Edition
Date Filed
O. Reg. 925/75 (1975 Building Code)
November 24, 1975
December 31, 1975
O. Reg. 583/83 (1983 Building Code)
September 15, 1983
November 30, 1983
O. Reg. 419/86 (1986 Building Code)
O. Reg. 413/90 (1990 Building Code)
O. Reg. 403/97 (1997 Building Code)
O. Reg. 350/06 (2006 Building Code)
December 31, 2006
The following Table lists the amendments to the 2006 Building Code made since the filing of O. Reg. 350/06:
AMENDMENTS TO THE 2006 BUILDING CODE - ONTARIO REGULATION 350/06
Date Filed
Nature of Amendment
December 31, 2006
Definition of Applicable Law
Editorial revisions; tall stud tables A-30 to A-33
Part 3 stud wall reinforcement and plumbing fixtures
Residential fire sprinklers
September 23, 2009
September 24, 2009
Definition of applicable law
Housekeeping changes
Residential fire sprinklers
December 21, 2009
Low flow water closets
Energy efficiency
On-site sewage maintenance inspections
Part 12 energy efficiency
Glass in guards; new Supplementary Standard SB-13
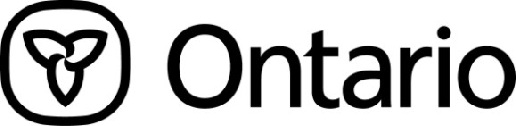
2006 BUILDING CODE COMPENDIUM
The following Table lists M inister's Rulings that have been made to adopt amendments to codes, formulae, standards,guidelines or procedures referenced in the 2006 Building Code:
MINISTER'S RULINGS TO ADOPT AMENDMENTS TO CODES, FORMULAE, STANDARDS, GUIDELINES OR PROCEDURES
REFERENCED IN THE 2006 BUILDING CODE
Date of Ruling
Nature of Amendment
Supplementary Standards SA-1, SB-1, SB-2, SB-3, SB-4, SB-5,
December 31, 2006
SB-6, SB-7, SB-8, SB-9, SB-10, SB-11, SC-1
Revise Table 1.3.1.2. of Division B
Revise Supplementary Standard SB-5
Revise Table 1.3.1.2. of Division B
Revise Supplementary Standard SB-10
Revise Supplementary Standards SA-1, SB-4
Revise Supplementary Standards SB-1, SB-2, SB-5
Revise Table 1.3.1.2. of Division B
Revise Supplementary Standard SB-2
November 30, 2009
New Supplementary Standard SB-12
December 31, 2009
Revise Supplementary Standards SA-1, SB-2, SB-5, SB-10
December 31, 2009
Revise Supplementary Standard SA-1
December 31, 2009
Revise Supplementary Standard SA-1
Revise Supplementary Standard SB-5
Revise Table 1.3.1.2. of Division B
February 17, 2011
February 17, 2011
Revise Supplementary Standard SB-2
Revise Supplementary Standard SB-5
Revise Supplementary Standard SB-5
Revise Supplementary Standard SB-10
Revise Supplementary Standard SB-12
Revise Supplementary Standard SB-5
Revise Supplementary Standard SB-5
Revise Supplementary Standard SA-1
Revise Supplementary Standard SB-13
Revise Supplementary Standard SB-5
Revise Supplementary Standard SB-12
2006 Building Code
Table 1.3.1.2.
Table 1.3.1.2. (Cont'd)
Documents Referenced in the Building Code
Forming Part of Sentence 1.3.1.2.(1)
Title of Document
Hydronics Institute Manuals
Table 11.5.1.1.A.
Table 11.5.1.1.B.
Guideline on F ire Ratings of Archaic Materials and Assemblies
Table 11.5.1.1.C.
Table 11.5.1.1.D/E.
Table 11.5.1.1.F.
Procedure for Loudness Rating of Residential Fan Products
Table 9.32.3.9.
Airflow Test Procedure
ISO 8201; 1987(E)
Acoustics - Audible Emergency Evacuation Signal
Supplementary Standard
1.2.1.1.(1) of Division A
Objectives and Functional Statements Attributed to the Acceptable Solutions
SA-1, June 18, 2012
1.2.1.1.(2) of Division A
Supplementary Standard
Climatic and Seismic Data
Table 9.25.1.2.
SB-1, June 18, 2008
Table 9.32.3.10.A9.33.3.2.(1)Table 12.3.2.1.
Table 12.3.4.2.A.
Supplementary Standard
Fire Performance Ratings
SB-2, February 17, 2011
Supplementary Standard
Fire and Sound Resistance of Building Assemblies
SB-3, June 18, 2008
Supplementary Standard
Measures for Fire Safety in High Buildings
SB-4, April 1, 2010
Supplementary Standard
Approved Sewage Treatment Units
SB-5, January 16, 2013
Supplementary Standard
Percolation Times and Soil Descriptions
SB-6, August 15, 2006
Supplementary Standard
Guards for Housing and Small Buildings
SB-7, August 15, 2006
Supplementary Standard
Design, Construction and Installation of Anchorage Systems for Fixed Access
SB-8, August 15, 2006
Division B - Part 1
Table 1.3.1.2.
2006 Building Code
Table 1.3.1.2. (Cont'd)
Documents Referenced in the Building Code
Forming Part of Sentence 1.3.1.2.(1)
Title of Document
Supplementary Standard
Requirements for Soil Gas Control
SB-9, August 15, 2006
9.13.4.2.(2) to (4)
Supplementary Standard
Energy Efficiency Supplement
SB-10, June 27, 2011
Supplementary Standard
Construction of Farm Buildings
1.3.1.2.(4) of Division A
SB-11, August 15, 2006
Supplementary Standard
Energy Efficiency for Housing
SB-12, March 15, 2013
Supplementary Standard
SB-13, June 27, 2012
Supplementary Standard
Code of Conduct for Registered Code Agencies
3.7.4.1.(2) of Division C
SC-1, August 15, 2006
Guidelines for the Design of Sanitary Sewage Works, Storm Sewers, Water
Guidelines 1985, with
Storage Facilities, Water Distribution Systems, Servicing in areas subject to
Subsequent Revision
adverse conditions, Water Supply for small residential development andseasonally operated water supply
National Fire Codes
Installation of Sprinkler Systems
Installation of Sprinkler Systems in One- and Two-Family Dwellings and
Manufactured Homes
Installation of Sprinkler Systems in Residential Occupancies up to and
including Four Stories in Height
Installation of Standpipe and Hose Systems
Installation of Stationary Pumps for Fire Protection
Installation of Fire Service Mains and Their Appurtenances
Fire Doors and Other Opening Protectives
Incinerators, Waste and Linen Handling Systems and Equipment
Ventilation Control and Fire Protection of Commercial Cooking Operations
Fixed Guideway Transit and Passenger Rail Systems
Chimneys, Fireplaces, Vents and Solid Fuel-Burning Appliances
Water-Cooling Towers
Fire Tests for Flame Propagation of Textiles and Films
Division B - Part 1
Ministry of Municipal Affairs and Housing
Building and Development Branch
2006 Building Code Compendium
Building Code
July 1, 2013 update
2006 Building Code Compendium
Supplementary Standards SA-1, SB-1 to SB-11 and SC-1 come into force on the 31st day of December, 2006.
Supplementary Standard SB-12 comes into force on the 1st day of January, 2010.
Supplementary Standard SB-13 comes into force on the 1st day of July, 2012.
See "Code Amendment History" page in the Preface of Volume 1 for information concerning amendments to SupplementaryStandards issued through Minister's Rulings.
Amendment made to Appendix A or B issued April 2nd, 2007.
Amendment made to Appendix A or B issued June 9th, 2009.
Amendment made to Appendix A or B issued January 1st, 2010.
Amendment made to Appendix A or B issued January 1st, 2011.
Issued April 2nd, 2007.
Issued June 18th, 2008.
Issued June 9th, 2009.
Issued January 1st, 2010.
Issued July 1st, 2012.
Copyright Queen's Printer for Ontario 2013
ISBN 978-1-4435-2071-3 (set)
ISBN 978-1-4435-2073-7 (vol. 2)
All rights reserved.
Questions regarding copyright, including reproduction and distribution, may be directed to the Director, Building and Development Branchof the Ministry of Municipal Affairs and Housing.
Ministry of Municipal Affairs and Housing
Building and Development Branch
2006 Building Code - Supplementary Standards
Supplementary Standard SB-5
Approved Sewage Treatment Units
January 16, 2013 update
Supplementary Standard SB-5
Supplementary Standard SB-5 comes into force on the 31st day of December, 2006.
m Ruling of the Minister of Municipal Affairs and Housing (Minister's Ruling) MR-07-S-02 takes effect on the 9th day of
1 March, 2007.
m Ruling of the Minister of Municipal Affairs and Housing (Minister's Ruling) MR-08-S-05 takes effect on the 18th day of
4 June, 2008.
m Ruling of the Minister of Municipal Affairs and Housing (Minister's Ruling) MR-09-S-09 takes effect on the 1st day of
8 January, 2010.
m Ruling of the Minister of Municipal Affairs and Housing (Minister's Ruling) MR-10-S-12 takes effect on the 1st day of
m Ruling of the Minister of Municipal Affairs and Housing (Minister's Ruling) MR-11-S-14 takes effect on the 11th day of
m Ruling of the Minister of Municipal Affairs and Housing (Minister's Ruling) MR-11-S-15 takes effect on the 22nd day of
m Ruling of the Minister of Municipal Affairs and Housing (Minister's Ruling) MR-11-S-18 takes effect on the 7th day of
m Ruling of the Minister of Municipal Affairs and Housing (Minister's Ruling) MR-12-S-19 takes effect on the 13th day of
m Ruling of the Minister of Municipal Affairs and Housing (Minister's Ruling) MR-13-S-22 takes effect on the 16th day of
e Issued June 18th, 2008.
Copyright
Copyright Queen's Printer for Ontario 2013
All rights reserved.
Questions regarding copyright, including reproduction and distribution, may be directed to the Director,
Building and Development Branch of the Ministry of Municipal Affairs and Housing.
Supplementary Standard SB-5
Table 1 (Cont'd)
List of Approved Treatment Units Meeting Secondary Effluent Quality Criteria in
Table 8.6.2.2.A. of Division B in the 2006 Building Code
Models References
Ecoflo Biofiltration Treatment Unit
MOE letter dated:
Technologies Ecoflontario (Peat
Beds)234 B. Russell Ave.
Ottawa K1N 7X5Phone: 613-738-2991Fax:
Contact: Pierre Gratton
MOE letter dated:
Treatment Plants c/o Make-Way
Environmental Technologies Inc.
Exeter, Ontario N0M 1S7
Phone: 866-625-3929 or
Contact: Bert Knip
Southern Ontario Biocycle Ltd.
Models: 5800, 2500 L/d
MOE letter dated:
280 South Blair St.
Whitby, Ontario L1N 9N2
Phone: 905-665-0537Fax:
Contact: Jake Rempel
Aquarobic Mini Plant,
MOE letter dated:
Aquarobic Maxi Plant,
Utterson, Ontario
Aquarobic Super Maxi Plant
POB 1M0Phone: 800-452-0144
Contact: John Reid
SB-5 Page 3
Supplementary Standard SB-5
List of Approved Treatment Units Meeting Tertiary Effluent Quality
Criteria in Table 8.6.2.2.A. of Division B in the 2006 Building Code
(Approved for Shallow Buried Trenches)
Norweco Equipment Company
Norweco Singulair Treatment Systems
See attached system
220 Republic Street
Norwalk, OH, 44857
Models: 960-500-2000
Phone: 416-729-3212
Contact: M. Price
Orenco Systems Inc.
Orenco Treatment Systems
See attached system
c/o Onsite Sewage Inc.
Models: ISF1111HL, ISF1313HL,
Kitchener, Ontario N2E 3X9
ISF1515HL, ISF2000HL
Phone: 519-578-0969Fax:
ISF1616LL, ISF2020LL,
Contact: Walter Crawford
ISF2222LL, ISF2828LL
c/o Sand Filtration Inc.
RSF2010, RSF1615,
35 A Shirk Place
RSF1818, RSF3210,
Kitchener, Ontario N2K 1R3
RSF2018, RSF2020,
Phone: 519-743-1780
RSF2220, RSF2420,
Waterloo Biofilter Systems Inc.
Waterloo Biofilter Treatment Systems
See attached system
143 Dennis Street, P.O. Box 400
Rockwood, ON N0B 2K0
Models: 11, 16, 20, 25, 30, 35, 40, 45, 50, 55, 60, 65,
Phone: 519-856-0757
70, 75, 80, 85, 90, 95, 100
Contact: E. C. Jowett
Northern Purification Systems
Clearstream Treatment Systems
See attached system
823077 Ontario Inc.
R.R. #1; 2614 Concession 4
Loretto, Ontario L0G 1L0
Phone: 905-729-3212
Contact: Tom Musgrove
Whitewater Sewage Treatment Plants c/o Make-Way
Whitewater Treatment Systems
See attached system
Environmental Technologies Inc.
Exeter, Ontario N0M 1S7
Phone: 866-625-3929 or 519-235-1176
Contact: Bert Knip
SB-5 Page 4
Supplementary Standard SB-5
Table 2 (Cont'd)
List of Approved Treatment Units Meeting Tertiary Effluent Quality
Criteria in Table 8.6.2.2.A. of Division B in the 2006 Building Code
(Approved for Shallow Buried Trenches)
Southern Ontario Biocycle Ltd.
Biocycle Aerated Wastewater System
See attached system description.
280 South Blair St.
Whitby, Ontario L1N 9N2
Phone: 905-665-0537Fax:
Contact: Jake Rempel
Seprotech Systems Inc.
Rotordisk Wastewater Systems
See attached system description.
(formerly CMS Rotodisk Inc.)2378 Holly Lane
Ottawa, Ontario K1V 7P1Phone: 613-523-1641Fax:
Contact: Cliff Johnson
m Bio-Microbics, Inc.
FAST® Wastewater Treatment Systems
See attached system
m 8450 Cole Pkwy.
18 Shawnee, KS
Models: MicroFAST® 0.5
MicroFAST® 0.625
Phone: 913-422-0707 or 800-753-3278
Model MicroMini-28
See attached system
Model MicroMini-45
Utterson, Ontario
Model MiniPlant-70
Model MiniPlant-85
Phone: 705-644-1877 or 800-452-0144Fax:
Contact: John Reid
Nayadic Wastewater Treatment Systems
See attached system
c/o EZFlow Canada
7024 Smith Industrial Drive
McGregor, Ontario N0R 1J0
Phone: 519-726-6444
Contact: Janis Bortolotti or John Winkup
Bionest Technologies Inc.
Bionest Treatment Systems
See attached system
55, 12e Rue, CP 697
Grand-Mère, Québec G9T 5L4
Phone: 819-538-5662 or 866-538-5662
Contact: Marlène Bonneville
SB-5 Page 5
Supplementary Standard SB-5
Table 2 (Cont'd)
List of Approved Treatment Units Meeting Tertiary Effluent Quality
Criteria in Table 8.6.2.2.A. of Division B in the 2006 Building Code
(Approved for Shallow Buried Trenches)
m Premier Tech Aqua
Ecoflo Biofilter Treatment Systems
See attached system
m 1 Ave. Premier
m Rivière-du-Loup, Québec
21 G5R 6C1
Phone: 418-867-8883
Contact: Marie-Christine Bélanger
ST-730PSTB-500 / STB-500B / STB-500BRSTB-570P / STB-570PRSTB-650 / STB-650B / STB-650BR STB-650P / STB-650PRSTB-730P / STB-730PR
m Orenco Systems, Inc.
AdvanTex® Wastewater Treatment System
See attached system
m 814 Airway Avenue
13 Sutherlin, OR 97470
Phone: 1-800-348-9843
AX20-Multiple Units
Contact: Sam Carter
m Ecological Tanks, Inc.
Aqua Safe Treatment Systems
See attached system
m 2247 Hwy 151 North
17 Downsville, Louisiana 71234
Models: AS500, AS600, AS750, AS1000, AS1500
Phone: (318) 644-0397Fax:
Aqua Air Treatment Systems
Contact: Calvin Locker
Models: AA500, AA600, AA750, AA1000, AA1200,
AA1500, AA500-35, AA600-50, AA800-65
m Bord na Móna Environmental Products U.S. Inc.
Puraflo Peat Fiber Biofilter Treatment Systems
See attached system
4 PO Box 77457
Greensboro, NC 27417
Models: Puraflo® P150N*1B
Phone: (336) 547-9338 or (409) 466-4644
Puraflo® P150N*1B Multiple Units
Contact: Colin Bishop
m RH2O North America Inc.
WSB® clean Treatment Systems
See attached system
m 268 Woolwich St. South
14 Breslau, Ontario
Models: WSB clean 400
Phone: (519) 648-3475
Contact: Scott Robinson
SB-5 Page 6
Supplementary Standard SB-5
Model 1500N
This Clearstream Treatment Unit is designed for daily design sanitary sewage flow of 3800 L to 5700 L. It consists of a
septic tank with a minimum volume of 4.5 m3 complete with an effluent filter on the outlet of the tank to screen out solids
larger than 5 mm, overflowing to a Clearstream Treatment Unit with a total volumetric capacity of 9.5 m3, complete with an
aeration tank equipped with two fine bubble diffusers and an air pump rated at 3.4 L/s together with an inner conical up
welling clarifier equipped with surge control weir overflowing to a single pass free access sand filter.
Where the percolation rate of the native subsoil is between 50 min/cm and 125 min/cm, the treatment unit shall also includetwo single pass free access sand filters (model NPSCS-10), or a 100 micron spin filter model number 1100. The sand filtersconsist of a fibreglass tank complete with wood planks covers, 100 mm dia. distribution piping, 6.51 m2 area at 600 mmdepth, filtration sand media (1.0 mm dia. to 2.0 mm dia. with 1.5 uniformity coefficient), 150 mm pea gravel layer and 100 mm dia. slotted collection piping discharging the effluent by gravity to a dosing pump chamber. The dosing pumpchamber shall have a volumetric capacity of 10.08 m3 equipped with a minimum 0.5 HP submersible effluent pump completewith level switches, alarm and control panel together with a forcemain discharging the effluent.
This approval is only for the treatment unit component of the sewage system and the sewage system shall comply with the
Ontario Building Code, as amended from time to time.
It is the responsibility of Northern Purification Systems (823077 Ontario Inc.) and/or its licensed agents to ensure that unitsmeet all other applicable standards. Other standards may include those of the Canadian Standards Association, OntarioMinistry of Labour, Electrical Safety Authority, etc.
SB-5 Page 25
Supplementary Standard SB-5
Pages 26 to 28 intentionally
SB-5 Pages 26 to 28
Supplementary Standard SB-5
m21 Ecoflo Biofilter Treatment Systems
Ecoflo Treatment Systems – ST Series Models (Open Bottom Treatment Units)
Ecoflo treatment units with open bottom are models ST-500, ST-570P, ST-650, ST-650P and ST-730P. Table 1 provides themaximum hydraulic loading rate on the organic filtering media (peat) and the maximum treatment capacity of each model.
ST Models – Open Bottom Treatment Units
Daily Design Sanitary
Maximum Hydraulic
Loading Rate Demand
Filtering Media Volume, m³
Dose, L/m³ per day
Notes to Table 1
(1) When the total daily design sanitary sewage flow exceeds 2 565 L, more than one Ecoflo unit could be used to meet the required flow.
The Ecoflo®Biofilter treatment unit consists of an enclosure confining a compact high-performance organic filter medium(peat), a distribution system that is constituted of a tipping bucket and distribution plates to evenly distribute the septic tankeffluent on the top of the filter medium, and a built-in ventilation/aeration system.
The treatment unit is preceded by a standard septic tank complete with an effluent filter on the outlet to screen out particleslarger than 1.6 mm. Depending on the site configuration, the septic tank effluent can be fed to the Ecoflo®Biofilter bygravity or overflows to a pump chamber. When needed, the pump chamber used to pump out the septic tank effluent to thetreatment unit has to have a minimum effective holding capacity of 0.9 times the daily sanitary sewage design flow andshould be equipped with a minimum 0.3 HP pump complete with level switches, alarm and control panel with a minimum 38 mm dia. discharge pipe, ball valve and a flow controller, terminating in an Ecoflo®Biofilter unit.
The above Ecoflo®Biofilter ST models are placed on a minimum of 200 mm thick layer of crushed stone (15 to 50 mm dia.)or gravel. Treated effluent is collected by means of a device under the stone layer and directed through a 100 mm dia. pipeto a separate effluent dosing chamber. The dosing chamber has a minimum effective volume of not less than half of the dailydesign sanitary sewage flow (Q) and is equipped with a minimum 0.3 HP effluent pump, activated by a conventional on/offfloat in the chamber or control panel for time dosing. The alarm float is connected to an alarm panel placed inside or outsidethe building on an independent electrical circuit. The treated effluent is then dosed to a shallow buried trench system.
Ecoflo Treatment Systems – STB Series Models (Closed Bottom Treatment Units)
The Ecoflo®Biofilter closed bottom models are listed in Table 2. These models are the same as "ST Models" with respect tothe loading rates on the organic filtering media (peat) and the treatment capabilities, except that they come in a closed bottomconfiguration. The treatment unit is also preceded by a standard septic tank complete with an effluent filter on the outlet toscreen out particles larger than 1.6 mm. Depending on the site configuration, the septic tank effluent can be fed to theEcoflo®Biofilter by gravity or overflows to a pump chamber where it is pumped out to be distributed over the media insidethe treatment unit.
SB-5 Page 47
Supplementary Standard SB-5
In these closed bottom models, the treated effluent is collected and stored, in whole or in part, in the collecting layerunderneath the filtering media as provided in Column 3 and Column 4 of Table 2.
Some concrete models provide enough storage capacity such that a separate dosing chamber is not required. For thesemodels, the bottom of the concrete shell must have a storage capacity for the treated effluent that is not less than 0.9 of thetotal daily design sanitary sewage flow. The treated effluent is then dosed to a shallow buried trench system.
Fiberglass and polyethylene models have part of the treated effluent stored at the bottom of the treatment unit and the rest ofthe treated effluent is directed to, and stored in a separate pump chamber located outside the treatment unit. The effectivestorage volume of the treated effluent stored at the bottom of the treatment unit as well as the volume of the treated effluentstored in the separate dosing chamber are provided in Column 3 and Column 4 of Table 2 for each different Ecoflo®BiofilterSTB model. The separate dosing chamber must have a capacity of not less than 0.5 of the total daily design sanitary sewageflow (Q). The dosing chamber for the treated effluent is equipped with a minimum 0.3 HP effluent pump, activated by aconventional on/off float in the chamber or control panel for time dosing. The alarm float is connected to an alarm panelplaced inside or outside the building on an independent electrical circuit. The treated effluent is then dosed to a shallowburied trench system.
STB Models – Closed Bottom Treatment Units
Volume Stored under the Filtering
Minimum Volume of the Separate
Media Provided, L
Dosing Chamber, L
Notes to Table 2
"R" in the model number denotes an integrated pump.
This approval is only for the treatment unit component of the sewage system and the sewage system and its components
shall comply with the Building Code, as amended from time to time.
It is the responsibility of Premier Tech Aqua and/or its licensed agents, to ensure that units meet all other applicablestandards. Other standards may include those of the Canadian Standards Association, Ontario Ministry of Labour, ElectricalSafety Authority, etc.
SB-5 Pages 48 to 48b
Ministry of Municipal Affairs and Housing
Building and Development Branch
2006 Building Code - Supplementary Standards
Supplementary Standard SB-12
Energy Efficiency For Housing
March 15, 2013 update
Supplementary Standard SB-12
m Supplementary Standard SB-12 comes into force on the 1st day of January 2010, pursuant to O. Reg. 503/09.
m Ruling of the Minister of Municipal Affairs and Housing (Minister's Ruling) MR-11-S-17 takes effect on the 1st day of
m Ruling of the Minister of Municipal Affairs and Housing (Minister's Ruling) MR-13-S-23 takes effect on the 15th day of
Copyright
Copyright Queen's Printer for Ontario 2013
All rights reserved.
Questions regarding copyright, including reproduction and distribution, may be directed to the Director,
Building and Development Branch of the Ministry of Municipal Affairs and Housing.
Supplementary Standard SB-12
m22SB-12 Energy Efficiency For Housing
Chapter 1 General
Section 1.1.
Energy Efficiency Compliance
Section 1.2.
Application of Supplementary Standard SB-12
Section 1.3.
Terms and Abbreviations
Definitions of Words and Phrases
Symbols and Other Abbreviations
Section 1.4.
Referenced Documents and Organizations
Chapter 2 Acceptable Solutions for Energy
Section 2.1.
Methods for Achieving Energy Efficiency
Compliance
Prescriptive Compliance Packages
Other Acceptable Compliance Methods
SB-12 Page 1
Supplementary Standard SB-12
This Supplementary Standard provides prescriptive requirements to achieve an acceptable air leakage rate and energyefficiency level as an alternative to achieving a rating of 80 when evaluated in accordance with the technical requirementsof NRCan's "EnerGuide for New Houses: Administrative and Technical Procedures", January 2005. This SupplementaryStandard has been included as a design option in Sentence 12.2.1.2.(3) of the Building Code to recognize the needs ofconsumers and the building industry for a predictable prescriptive solution. The energy efficiency levels achieved in thisSupplementary Standard are intended to meet or exceed, on a systemic basis, the level that would be met by modelanalogues evaluated against the EnerGuide Rating System.
Sentence 12.2.1.2.(3) requires the energy efficiency design of a building or part of a building of residential occupancywithin the scope of Part 9 that is intended to be occupied on a continuing basis during the winter months to comply with:
• Supplementary Standard SB-12; or• Achieve a rating of 80 or more when evaluated in accordance with the technical requirements of
NRCan,"EnerGuide for New Houses: Administrative and Technical Procedures", January 2005.
Subsections 12.3.2. and 12.3.3. of the Building Code are no longer applicable.
This Supplementary Standard contains three compliance options to achieve energy efficiency:
• Select an applicable prescriptive compliance package from Subsection 2.1.1. of this Supplementary Standard,• Design to the performance compliance method in Subsection 2.1.2. of this Supplementary Standard, or• Design to Energy Star requirements as specified in Subsection 2.1.3. of this Supplementary Standard.
This Supplementary Standard does not require labeling to demonstrate compliance with the Building Code. Subsections2.1.1. and 2.1.2. of this Supplementary Standard do not require blower door testing to demonstrate compliance.
1Unless otherwise indicated, all Building Code references in this foreword refer to provisions
located in Division B of the Building Code.
SB-12 Page 2
Supplementary Standard SB-12
SUMMARY OF THE CONTENTS OF SB-12
Chapter 1: General
This Chapter sets out the scope and application of this Supplementary Standard.
Chapter 2: Acceptable Solutions for Achieving Energy Efficiency Compliance
This Chapter contains acceptable solutions for achieving energy efficiency compliance with Clause 12.2.1.2.(3)(b) ofDivision B in the Building Code. Conformance with one of the prescriptive compliance packages in Subsection 2.1.1., theperformance compliance method in Subsection 2.1.2. or Energy Star requirements as specified in Subsection 2.1.3. of thisSupplementary Standard will achieve an energy efficiency performance level that is generally equivalent to a rating of 80 ormore when evaluated in accordance with the technical requirements of NRCan, "EnerGuide for New Houses:Administrative and Technical Procedures", January 2005.
SB-12 Page 3
Supplementary Standard SB-12
SB-12 Page 4
Supplementary Standard SB-12
Section 1.1. Scope
Energy Efficiency Compliance
1.1.1.1. Energy Efficiency
(1) Compliance with this Supplementary Standard shall be deemed to meet the energy efficiency requirements in
accordance with Sentence 12.2.1.2.(3) of Division B in the Building Code.
(2) The energy efficiency of existing buildings shall comply with
(a) Part 10 of Division B of the Building Code with respect to change of use, or
(b) Part 11 of Division B of the Building Code for renovation.
1.1.1.2. Compliance Options
(1) The energy efficiency of a building or part of a building of residential occupancy that is within the scope of Part 9
of Division B in the Building Code and is intended for occupancy on a continuing basis during the winter months shall
comply with
(a) Subsection 2.1.1. (Prescriptive Compliance Packages) of Chapter 2,
(b) Subsection 2.1.2. (Performance Compliance) of Chapter 2, or
(c) Subsection 2.1.3. (Other Acceptable Compliance Methods) of Chapter 2.
(2) Factory built modular homes manufactured before January 1, 2012 in accordance with the Building Code as it read
on December 31, 2011 shall be deemed to be in compliance with Sentence (1).
Section 1.2. Application
Application of Supplementary Standard SB-12
1.2.1.1. Energy Efficiency Design
(1) The energy efficiency of a building or part of a building of residential occupancy that is within the scope of Part 9
of Division B in the Building Code and is intended for occupancy on a continuing basis during the winter months shall
comply with this Supplementary Standard in accordance with Sentence 12.2.1.2.(3) of Division B in the Building Code.
SB-12 Page 5
Supplementary Standard SB-12
Section 1.3. Terms and Abbreviations
Definitions of Words and Phrases
1.3.1.1. Non-Defined Terms
(1) Definitions of words and phrases used in this Supplementary Standard that are not included in the list of definitions
in Articles 1.4.1.2. and 1.4.1.3. of Division A in the Building Code and are not defined in another provision of the
Code shall have the meanings that are commonly assigned to them in the context in which they are used, taking into
account the specialized use of terms by the various trades and professions to which the terminology applies.
1.3.1.2. Defined Terms
(1) Each of the words and terms in italics in this Supplementary Standard has the same meaning as in subsection 1(1)
of the Building Code Act, 1992 or Clause 1.4.1.2.(1)(b) of Division A in the Building Code.
Symbols and Other Abbreviations
1.3.2.1. Symbols and Other Abbreviations
(1) Where used in this Supplementary Standard, a symbol or abbreviation listed in Column 2 of Table 1.4.2.1. of
Division A in the Building Code shall have the meaning listed opposite it in Column 3.
(2) The abbreviations listed in Column 2 of Table 1.3.2.1. shall also apply to this Supplementary Standard and shall
have the meaning listed opposite it in Column 3.
Forming Part of Sentence 1.3.2.1.(2)
annual fuel utilization efficiency
heat recovery ventilator
insulating concrete form
SB-12 Page 6
Supplementary Standard SB-12
Section 1.4. Referenced Documents and Organizations
1.4.1.1. Effective Date
(1) Except as provided in Sentence (2), and unless otherwise specified in this Supplementary Standard, the documents
referenced in this Supplementary Standard shall include all amendments, revisions and supplements effective to October
31, 2011.
(2) All references to NRCan, "EnerGuide for New Houses: Administrative and Technical Procedures" in the Building
Code shall be the 2005 edition with all amendments, revisions and supplements effective to May 31, 2006.
1.4.1.2. Applicable Editions
(1) Where documents are referenced in this Supplementary Standard, they shall be the editions designated in Column
2 of Table 1.4.1.2.
Forming Part of Sentence 1.4.1.2.(1)
Title of Document
Supplementary Standard
Fenestration Energy Performance Evaluation of Windows
and Sliding Glass Doors
Test Method for Measuring Efficiency and Pressure Loss of 2.1.1.11.(3)
Drain Water Heat Recovery Units
Drain Water Heat Recovery Units
Procedure for Determining Fenestration Product U-factors
Procedure for Determining Fenestration Product Solar Heat
Gain Coefficient and Visible Transmittance at Normal
NRCan January 2011
Energy Star for New Homes: Technical Specifications –
Notes to Table 1.4.1.2.:
(1) NFRC refers to the National Fenestration Rating Council. (See Appendix A.)
1.4.2.1. Abbreviations of Proper Names
(1) Where used in this Supplementary Standard, abbreviations of proper names listed in Column 1 of Table 1.3.2.1.
of Division B in the Building Code shall have the meaning assigned opposite it in Column 2.
SB-12 Page 7
Supplementary Standard SB-12
Chapter 2
Acceptable Solutions for Energy
Efficiency Compliance
Section 2.1. Methods for Achieving Energy Efficiency
Prescriptive Compliance Packages (See Appendix A.)
2.1.1.1. Energy Efficiency
(1) Except as permitted in Articles 2.1.1.5. to 2.1.1.10., the minimum thermal performance and energy efficiency of
building envelope and space heating equipment, domestic hot water heating equipment and heat recovery ventilator
equipment shall conform to
(a) Article 2.1.1.2. if the building is located in Zone 1 with less than 5000 heating degree days, or
(b) Article 2.1.1.3. if the building is located in Zone 2 with 5000 or more heating degree days.
(2) All walls, ceilings, floors, windows and doors that separate heated space from unheated space, the exterior air or
the exterior soil shall have thermal resistance ratings conforming to this Subsection.
(3) Where specified in compliance packages in Tables 2.1.1.2.A, 2.1.1.2.B and 2.1.1.2.C and Tables 2.1.1.3.A,
2.1.1.3.B and 2.1.1.3.C, space heating equipment, domestic hot water heating equipment and heat recovery ventilators
shall have the efficiency rating conforming to this Subsection. (See Appendix A.)
(4) Insulation shall be provided between heated and unheated spaces and between heated spaces and the exterior in
accordance with this Chapter.
(5) Reflective surfaces of insulating materials shall not be considered in calculating the thermal resistance of building
assemblies.
(6) Where glass block is used in a wall, the required minimum overall performance of the building envelope shall be
maintained by increasing thermal performance of other components sufficient to compensate for the additional heat loss
through the glass block.
(7) Except as provided in Sentence (8) and except as permitted in Sentences (9) and 2.1.1.10.(2), where the ratio of
the gross area of windows, sidelights, skylights, glazing in doors and sliding glass doors to the gross area of peripheral
walls measured from grade to the top of the upper most ceiling is not more than 17%, the building shall comply with a
compliance package selected from Tables 2.1.1.2.A, 2.1.1.2.B and 2.1.1.2.C and Tables 2.1.1.3.A, 2.1.1.3.B and
2.1.1.3.C. (See Appendix A.)
SB-12 Page 8
Supplementary Standard SB-12
(8) Except as permitted in Sentences (9) and 2.1.1.10.(2), where the ratio of the gross area of windows, sidelights,
skylights, glazing in doors and sliding glass doors to the gross area of peripheral walls measured from grade to the top
of the upper most ceiling is more than 17% but not more than 22%, the building shall comply with a compliance
package selected from Tables 2.1.1.2.A, 2.1.1.2.B and 2.1.1.2.C and Tables 2.1.1.3.A, 2.1.1.3.B and 2.1.1.3.C, and
the overall coefficient of heat transfer of the glazing shall be upgraded to
(a) 1.8 where the selected compliance package requires 2.0,
(b) 1.6 where the selected compliance package requires 1.8, and
(c) 1.4 where the selected compliance package requires 1.6.
(See Appendix A.)
(9) Glazing in main entrance doors and adjacent sidelights to main entrance doors need not be calculated for the
purposes of Sentences (7) and (8).
(10) Except as provided in Sentences (9) and 2.1.1.10.(2), where the ratio of gross area of windows, sidelights,
skylights, glazing in doors and sliding glass doors to the gross area of peripheral walls measured from grade to the top
of the upper most ceiling is more than 22%, the building shall comply with Subsection 2.1.2. (See Appendix A.)
(11) Where a dwelling unit has a walkout basement, the thermal performance level of the exterior basement wall shall
be not less than that required for the above grade wall for
(a) the basement wall containing the door opening, and
(b) any basement wall that has an exposed wall area above the ground level exceeding 50% of that basement wall
(12) The minimum thermal resistance of insulation shall conform to the applicable values specified in Articles 2.1.1.2.
and 2.1.1.3.
(13) The minimum annual fuel utilization efficiency of a natural gas- or propane-fired furnace serving a building of
residential occupancy shall conform to Table 2.1.1.1.A.
(14) Where space heating is supplied by a solid fuel-burning appliance or an earth energy system, the compliance
package is permitted to comply with Tables 2.1.1.2.A. and 2.1.1.3.A.
(15) Where an enclosed unheated space is separated from a heated space by glazing, the unheated enclosure may be
considered to provide a thermal resistance of RSI 0.16.
Furnace Minimum Annual Fuel Utilization Efficiency
Forming Part of Sentence 2.1.1.1.(13)
Furnace Fuel Source
2.1.1.2. Energy Efficiency for Zone 1 Buildings
(1) Except as required in Sentences (2) to (4) and permitted in Sentences (5) to (11), the minimum thermal
performance of building envelope and equipment shall conform to Table 2.1.1.2.A.
SB-12 Page 9
Supplementary Standard SB-12
ZONE 1 - Compliance Packages for Space Heating Equipment with AFUE $90%
Forming Part of Sentence 2.1.1.2.(1)
Compliance Package
Ceiling with Attic Space
Minimum RSI (R)-Value(1)
Ceiling Without Attic Space
Minimum RSI (R)-Value(1)
Minimum RSI (R)-Value(1)
Walls Above Grade
Minimum RSI (R)-Value(1)
Basement Walls
Minimum RSI (R)-Value(1)
Entire surface > 600 mm
Minimum RSI (R)-Value(1)Edge of Below Grade Slab
# 600 mm Below Grade
Minimum RSI (R)-Value(1)Heated Slab or
Slab # 600 mm below grade (R10) (R10) (R10) (R10) (R10) (R10) (R10) (R10) (R10) (R10) (R10) (R10) (R10)
Minimum RSI (R)-Value(1)Windows and Sliding Glass
Maximum U-Value(2)Skylights
Maximum U-Value(2)
Space Heating Equipment
Minimum AFUEHRV(6), (7)
Minimum EfficiencyDomestic Hot Water Heater
Notes to Table 2.1.1.2.A:
(1) Except for notes (3) and (4), the values listed are minimum RSI-Values for the thermal insulation component only. RSI-Values are expressed in
(2) U-Value is the overall coefficient of heat transfer expressed in W/(m²·K).
(3) Compliance package K applies only to a building with both ICF basement walls and ICF above grade walls. Alternatively, any other compliance
package is permitted to be used for a building with both ICF basement walls and ICF above grade walls. The thermal resistance value of an ICF wall
is the total thermal resistance of the entire wall assembly.
(4) Compliance package L applies only to a building with ICF basement walls. Alternatively, any other compliance package except compliance package
K, is permitted to be used for a building with ICF basement walls. The thermal resistance value of an ICF wall is the total thermal resistance of the
entire wall assembly.
(5) Applies to a building with combined space heating and domestic hot water heating system.
(6) Except as required in Subsection 9.32.3. of Division B in the Building Code, an HRV is only required as a part of the compliance package where a
minimum efficiency level is specified.
(7) The minimum efficiency of an HRV shall be based on a test temperature of 0EC. In addition, where an HRV is installed to meet the requirements of
Subsection 9.32.3. of Division B in the Building Code, the energy efficiency of the HRV shall also meet the minimum efficiency requirements of
(8) Only the hot water heating equipment shall meet the minimum AFUE or EF specified in the Table or shall be of the condensing type.
SB-12 Page 10
Supplementary Standard SB-12
(2) Except for solid fuel-burning space heating equipment and natural gas and propane furnaces, where the space
heating equipment efficiency ranges from 78% to less than 90%, the minimum thermal performance of the building
envelope and equipment shall conform to Table 2.1.1.2.B.
ZONE 1 - Compliance Packages for Space Heating Equipment with AFUE $ 78 % and < 90%
Forming Part of Sentence 2.1.1.2.(2)
Compliance Package
Ceiling with Attic Space
Minimum RSI (R)-Value(1)
Ceiling Without Attic Space
Minimum RSI (R)-Value(1)
Minimum RSI (R)-Value(1)
Walls Above Grade
Minimum RSI (R)-Value(1)
Basement Walls
Minimum RSI (R)-Value(1)
Below Grade SlabEntire surface > 600 mm below grade
Minimum RSI (R)-Value(1)Edge of Below Grade Slab # 600 mm
Minimum RSI (R)-Value(1)Heated Slab or
Slab # 600 mm below grade
Minimum RSI (R)-Value(1)Windows and Sliding Glass DoorsMaximum U-Value(2)
Space Heating Equipment
Minimum AFUEHRV(3)
Minimum EfficiencyDomestic Hot Water Heater
Notes to Table 2.1.1.2.B:
(1) The values listed are minimum RSI-Values for the thermal insulation component only. RSI-Values are expressed in (m²·K)/W.
(2) U-Value is the overall coefficient of heat transfer expressed in W/(m²·K).
(3) The minimum efficiency of an HRV shall be based on a test temperature of 0EC. In addition, where an HRV is installed to meet the
requirements of Subsection 9.32.3. of Division B in the Building Code, the energy efficiency of the HRV shall also meet the minimumefficiency requirements of Sentence 9.32.3.11.(2).
SB-12 Page 11
Supplementary Standard SB-12
(3) Where electric space heating is used, the minimum thermal performance of the building envelope and equipment
shall conform to Table 2.1.1.2.C.
ZONE 1 - Compliance Packages for Electric Space Heating
Forming Part of Sentence 2.1.1.2.(3)
Compliance Package
Ceiling with Attic Space
Minimum RSI (R)-Value(1)
Ceiling Without Attic Space
Minimum RSI (R)-Value(1)
Minimum RSI (R)-Value(1)
Walls Above Grade
Minimum RSI (R)-Value(1)
Basement Walls
Minimum RSI (R)-Value(1)
Below Grade SlabEntire surface > 600 mm below grade
Minimum RSI (R)-Value(1)
Edge of Below Grade Slab # 600 mm below grade
Minimum RSI (R)-Value(1)
Slab # 600 mm below grade
Minimum RSI (R)-Value(1)
Windows and Sliding Glass DoorsMaximum U-Value(2)
Space Heating Equipment
Minimum Efficiency
Domestic Hot Water Heater
Notes to Table 2.1.1.2.C:
(1) The values listed are minimum RSI-Values for the thermal insulation component only. RSI-Values are
expressed in (m²·K)/W.
(2) U-Value is the overall coefficient of heat transfer expressed in W/(m²·K).
(3) The minimum efficiency of an HRV shall be based on a test temperature of 0EC. In addition, where
an HRV is installed to meet the requirements of Subsection 9.32.3. of Division B in the Building Code,the energy efficiency of the HRV shall also meet the minimum efficiency requirements of Sentence9.32.3.11.(2).
SB-12 Page 12
Supplementary Standard SB-12
(4) Except for solid fuel-burning space heating equipment, where the space heating equipment efficiency is less than
78% or it cannot meet the requirements of the applicable compliance packages, energy efficiency compliance shall be
achieved in accordance with Clause 12.2.1.2.(3)(a) of Division B in the Building Code or Subsection 2.1.2. of this
Supplementary Standard.
(5) Where the thermal performance of above grade walls, windows or basement walls is reduced by applying
Sentences (6) through (11), only the thermal performance of one of those building components is permitted to be
reduced.
(6) Except as permitted in Sentence (7), where compliance package I or J in Table 2.1.1.2.A is used, the minimum
RSI value for thermal insulation in exposed above grade walls is permitted to be not less than RSI 3.52 provided that
(a) the overall coefficient of heat transfer of the glazing is upgraded in accordance with Sentence 2.1.1.1.(8), in
addition to a upgrade where it is required due to high fenestration to wall ratio, or (See Appendix A)
(b) the thermal insulation value in basement walls has a minimum RSI 3.52 where compliance package J is used.
(7) Where blown-in insulation or spray-applied foam insulation is used in compliance package I or J in Table
2.1.1.2.A, the minimum RSI value for thermal insulation in exposed above grade walls is permitted to be not less than
RSI 3.52 provided that
(a) the thermal insulation value in a ceiling with an attic space is not less than RSI 10.55,
(b) the minimum efficiency of the HRV is increased by not less than 8 percentage points,
(c) the minimum AFUE of the space heating equipment is increased by not less than 2 percentage points,
(d) the minimum EF of the domestic hot water heater is increased by not less than 4 percentage points, or
(e) the building is in compliance with Sentence (6).
(8) Except as permitted in Sentence (9), where compliance package D, E, F, G, H or M in Table 2.1.1.2.A is used,
the minimum RSI value for thermal insulation of exposed above grade walls is permitted to be not less than RSI 3.52
provided that
(a) the overall coefficient of heat transfer of the glazing is upgraded in accordance with Sentence 2.1.1.1.(8), in
addition to an upgrade where it is required due to high fenestration to wall ratio, and the minimum EF of thedomestic hot water heater is increased by not less than 8 percentage points, or (See Appendix A)
(b) the thermal insulation value in basement walls has a minimum RSI 3.52 where compliance package F, G, or H is
used, and the building is in compliance with at least two requirements of Clauses (7)(a) to (d).
(9) Where blown-in insulation or spray-applied foam insulation is used in compliance package D, E, F, G, H or M in
Table 2.1.1.2.A, the minimum RSI value for thermal insulation in exposed above grade walls is permitted to be not less
than RSI 3.52 provided that
(a) the overall coefficient of heat transfer of the glazing is upgraded in accordance with Sentence 2.1.1.1.(8), in
addition to an upgrade where it is required due to high fenestration to wall ratio or the thermal insulation value inbasement walls has a minimum RSI 3.52 where compliance package F, G, or H is used, and (See Appendix A)
(b) the building is in compliance with Clause (7)(a), (b), (c) or (d).
(10) Where a drain water heat recovery unit conforming to Article 2.1.1.11. is provided in addition to the requirements
of a compliance package selected from Tables 2.1.1.2.A to 2.1.1.2.C.
(a) the thermal insulation value in exposed above grade walls is permitted to be not less than RSI 3.52 where it is
required to be RSI 3.87,
(b) the thermal insulation value in exposed above grade walls is permitted to be not less than RSI 3.52 where it is
required to be RSI 4.23, provided that the drain water heat recovery unit has a minimum efficiency of not lessthan 46%,
(c) the thermal insulation value in basement walls is permitted to be not less than RSI 2.11 where it is required to be
(d) the overall coefficient of heat transfer of glazing is permitted to be not greater than 1.8 W/m2AK where it is
required to be 1.6 W/m2AK, or not greater than 1.6 W/m2AK where it is required to be 1.4 W/m2AK,
(e) the minimum efficiency of an HRV is permitted to be not less than 55% where it is required to be 75% or less, or(f) the minimum efficiency of a furnace is permitted to be not less than 90% where it is required to be 94%.
SB-12 Page 13
Supplementary Standard SB-12
(11) Where an HRV is only required for the purpose of meeting the energy efficiency requirements of a compliance
package included in Table 2.1.1.2.A, the HRV may be omitted provided that a drain water heat recovery unit with a
minimum efficiency of not less than 62% is installed in conformance with Article 2.1.1.11.
2.1.1.3. Energy Efficiency for Zone 2 Buildings
(1) Except as required in Sentences (2) to (4) and permitted in Sentences (5) to (8), the minimum thermal performance
of the building envelope and equipment shall conform to Table 2.1.1.3.A.
SB-12 Page 14
Supplementary Standard SB-12
ZONE 2 - Compliance Packages for Space Heating Equipment with AFUE $ 90%
Forming Part of Sentence 2.1.1.3.(1)
Compliance Package
Ceiling with Attic Space
Minimum RSI (R)-Value(1)
Ceiling Without Attic Space
Minimum RSI (R)-Value(1)
Minimum RSI (R)-Value(1)
Walls Above Grade
Minimum RSI (R)-Value(1)
Basement Walls
Minimum RSI (R)-Value(1)
Entire surface > 600 mm
Minimum RSI (R)-Value(1)Edge of Below Grade Slab
# 600 mm below grade
Minimum RSI (R)-Value(1)Heated Slab or
Slab # 600 mm below grade (R10) (R10) (R10) (R10) (R10) (R10) (R10) (R10) (R10) (R10) (R10) (R10) (R10)
Minimum RSI (R)-Value(1)Windows and Sliding Glass
Maximum U-Value(2)
Space-Heating Equipment
Minimum AFUEHRV(6), (7)
Minimum Efficiency Domestic Hot Water Heater
0.57 0.67 0.80(8)
Notes to Table 2.1.1.3.A:
(1) Except for notes (3) and (4), the values listed are minimum RSI-Values for the thermal insulation component only. RSI-Values are expressed in
(2) U-Value is the overall coefficient of heat transfer expressed in W/(m²· K).
(3) Compliance package K applies only to a building with both ICF basement walls and ICF above grade walls. Alternatively, any other compliance
package is permitted to be used for a building with both ICF basement walls and ICF above grade walls. The thermal resistance value of an ICF wall
is the total thermal resistance of the entire wall assembly.
(4) Compliance package L applies only to a building with ICF basement walls. Alternatively, any other compliance package except compliance package
K, is permitted to be used for a building with ICF basement walls. The thermal resistance value of an ICF wall is the total thermal resistance of the
entire wall assembly.
(5) Applies to a building with combined space heating and domestic hot water heating system.
(6) Except as required in Subsection 9.32.3. of Division B in the Building Code, an HRV is only required as a part of the compliance package where a
minimum efficiency level is specified.
(7) The minimum efficiency of an HRV shall be based on a test temperature of 0EC. In addition, where an HRV is installed to meet the requirements of
Subsection 9.32.3. of Division B in the Building Code, the energy efficiency of the HRV shall also meet the minimum efficiency requirements of
(8) Only the hot water heating equipment shall meet the minimum AFUE or EF specified in the Table or shall be of the condensing type.
SB-12 Page 15
Supplementary Standard SB-12
(2) Except for solid fuel-burning space heating equipment and natural gas and propane furnaces, where the space
heating equipment efficiency ranges from 78% to less than 90%, the minimum thermal performance of building
envelope and equipment shall conform to Table 2.1.1.3.B.
ZONE 2 - Compliance Packages for Space Heating Equipment with AFUE $ 78 % and < 90%
Forming Part of Sentence 2.1.1.3.(2)
Compliance Package
Ceiling with Attic Space
Minimum RSI (R)-Value(1)
Ceiling Without Attic Space
Minimum RSI (R)-Value(1)
Minimum RSI (R)-Value(1)
Walls Above Grade
Minimum RSI (R)-Value(1)
Basement Walls
Minimum RSI (R)-Value(1)
Entire surface > 600 mm below grade
Minimum RSI (R)-Value(1)Edge of Below Grade Slab # 600 mm below grade
Minimum RSI (R)-Value(1)
Slab # 600 mm below grade
Minimum RSI (R)-Value(1)Windows and Sliding Glass DoorsMaximum U-Value(2)
Space Heating Equipment
Minimum AFUEHRV(3)
Minimum EfficiencyDomestic Hot Water Heater
Notes to Table 2.1.1.3.B.:
(1) The values listed are minimum RSI-Values for the thermal insulation component only. RSI -Values are
expressed in (m²·K)/W.
(2) U-Value is the overall coefficient of heat transfer expressed in W/(m²·K).
(3) The minimum efficiency of an HRV shall be based on a test temperature of 0EC. In addition, where an
HRV is installed to meet the requirements of Subsection 9.32.3. of Division B in the Building Code, theenergy efficiency of the HRV shall also meet the minimum efficiency requirements of Sentence9.32.3.11.(2).
SB-12 Page 16
Supplementary Standard SB-12
(3) Where electric space heating is used, the minimum thermal performance of the building envelope and equipment
shall conform to Table 2.1.1.3.C.
ZONE 2 - Compliance Packages for Electric Space Heating
Forming Part of Sentence 2.1.1.3.(3)
Compliance Package A
Ceiling with Attic Space
Minimum RSI (R)-Value(1)
Ceiling Without Attic Space
Minimum RSI (R)-Value(1)
Minimum RSI (R)-Value(1)
Walls Above Grade
Minimum RSI (R)-Value(1)
Basement Walls
Minimum RSI (R)-Value(1)
Entire surface > 600 mm below grade
Minimum RSI (R)-Value(1)
Edge of Below Grade Slab # 600 mm below grade
Minimum RSI (R)-Value(1)
Slab # 600 mm below grade
Minimum RSI (R)-Value(1)
Windows and Sliding Glass DoorsMaximum U-Value(2)
Space Heating Equipment
Minimum Efficiency
Domestic Hot Water Heater
Notes to Table 2.1.1.3.C:
(1) The values listed are minimum RSI-Values for the thermal insulation component only. RSI-
Values are expressed in (m²·K)/W.
(2) U-Value is the overall coefficient of heat transfer expressed in W/(m²·K).
(3) The minimum efficiency of an HRV shall be based on a test temperature of 0EC. In addition,
where an HRV is installed to meet the requirements of Subsection 9.32.3. of Division B in theBuilding Code, the energy efficiency of the HRV shall also meet the minimum efficiencyrequirements of Sentence 9.32.3.11.(2).
SB-12 Page 17
Supplementary Standard SB-12
(4) Except for solid fuel-burning space heating equipment, where the space heating equipment efficiency is less than
78% or it cannot meet the requirements of the applicable compliance packages, energy efficiency compliance shall be
achieved in accordance with Clause 1 2.2.1.2.(3)(a) of Division B in the Building Code or Subsection 2.1.2. of this
Supplementary Standard.
(5) Where the thermal performance of above grade walls, windows or basement walls is reduced by applying
Sentences (6) through (8), only the thermal performance of one of those building components is permitted to be
reduced.
(6) Except as permitted in Sentence (7), where compliance package H, I, J or M in Table 2.1.1.3.A is used, the
minimum RSI value for thermal insulation of exposed above grade walls is permitted to be not less than RSI 3.52
provided that
(a) the overall coefficient of heat transfer of the glazing is upgraded in accordance with Sentence 2.1.1.1.(8), in
addition to a upgrade where it is required due to high fenestration to wall ratio and the minimum EF of thedomestic hot water heater is increased by not less than 8 percentage points, or (See Appendix A)
(b) the thermal insulation value in basement walls has a minimum RSI 3.52 where compliance package J is used, and
the building is in compliance with at least two requirements of Clauses 2.1.1.2.(7)(a) to (d).
(7) Where blown-in insulation or spray-applied foam insulation is used in compliance package H, I, J or M in Table
2.1.1.3.A, the minimum RSI value for thermal insulation in exposed above grade walls is permitted to be not less than
RSI 3.52 provided that
(a) the overall coefficient of heat transfer of the glazing is upgraded in accordance with Sentence 2.1.1.1.(8), in
addition to a upgrade where it is required due to high fenestration to wall ratio or the thermal insulation value inbasement walls has a minimum RSI 3.52 where compliance package J is used, and (See Appendix A)
(b) the building is in compliance with Clause 2.1.1.2.(7)(a), (b), (c) or (d).
(8) Where a drain water heat recovery unit conforming to Article 2.1.1.11. is provided in addition to the requirements
of a compliance package selected from Tables 2.1.1.3.A to 2.1.1.3.C.
(a) the thermal insulation value in exposed above grade walls is permitted to be not less than RSI 3.87 where it is
required to be RSI 4.23 provided that the drain water heat recovery unit has a minimum efficiency of not less than41%,
(b) the thermal insulation value in basement walls is permitted to be not less than RSI 2.11 where it is required to be
RSI 3.52, provided that the drain water heat recovery unit has a minimum efficiency of not less than 46%,
(c) the overall coefficient of heat transfer of glazing is permitted to be not greater than 1.8 W/m2AK where it is
required to be 1.6 W/m2AK,
(d) the overall coefficient of heat transfer of glazing is permitted to be not greater than 1.6 W/m2AK where it is
required to be 1.4 W/m2AK, provided that the drain water heat recovery unit has a minimum efficiency of not lessthan 41%, or
(e) the minimum efficiency of an HRV is permitted to be not less than 55% where it is required to be 75% or less.
2.1.1.4. Elements Acting as a Thermal Bridge
(1) Except for a foundation wall, the insulated portion of a wall that incorporates wood stud framing elements that
have a thermal resistance of less than RSI 0.90 shall be insulated to restrict heat flow through the studs by a material
providing a thermal resistance at least equal to 25% of the thermal resistance required for the insulated portion of the
assembly in Articles 2.1.1.2. and 2.1.1.3.
(2) Except as provided in Sentence (3), the thermal resistance of the insulated portion of a building assembly in
Articles 2.1.1.2. and 2.1.1.3. that incorporates metal framing elements, such as steel studs and steel joists, that act as
thermal bridges to facilitate heat flow through the assembly, shall be 20% greater than the values shown in Tables
2.1.1.2.A, 2.1.1.2.B and 2.1.1.2.C and Tables 2.1.1.3.A, 2.1.1.3.B and 2.1.1.3.C, unless it can be shown that the
heat flow is not greater than the heat flow through a wood frame assembly of the same thickness.
SB-12 Page 18
Supplementary Standard SB-12
(3) Sentence (2) does not apply to building assemblies incorporating thermal bridges where the thermal bridges are
insulated to restrict heat flow through the thermal bridges by a material providing a thermal resistance at least equal to
25% of the thermal resistance required for the insulated portion of the assembly in Articles 2.1.1.2. and 2.1.1.3.
2.1.1.5. Log Wall Construction and Post, Beam and Plank Construction
(1) Except as provided in Sentences (2) and (3), log wall construction and post, beam and plank construction shall
have a minimum thermal resistance of RSI 2.1 for the total assembly.
(2) The thermal resistance value in Sentence (1) for the total wall assembly may be reduced to not less than RSI 1.61
if,
(a) the thermal resistance of insulation for the exposed roof or ceiling required in Table 2.1.1.2.A. is increased by an
amount equivalent to the reduction permitted in this Sentence, and
(b) for log walls, the logs have tongue-and-groove or splined joints.
(3) Where milled log walls are installed, the thermal resistance value in Sentence (1) for the total wall assembly does
not apply if,
(a) the mean thickness of each log is not less than 150 mm,
(b) the thermal resistance of insulation for the exposed roof or ceiling required in Table 2.1.1.2.A is increased by
(c) the logs have tongue-and-groove or splined joints.
(4) Where a log wall is constructed in accordance with Sentences (1) to (3), the log wall shall be deemed to comply
with the requirements in Subsection 9.25.3. of Division B in the Building Code.
2.1.1.6. Insulation of Foundation Walls
(1) Foundation walls enclosing heated space shall be insulated from the underside of the subfloor to not more than
200 mm above the finished floor level of the basement. (See Appendix A.)
(2) The insulation required by Sentence (1) may be provided by a system installed,
(a) on the interior of the foundation wall,
(b) on the exterior face of the foundation wall, or
(c) partially on the interior and partially on the exterior, provided the thermal performance of the system is equivalent
to that permitted in Clauses (a) or (b).
(3) If a foundation wall is constructed of hollow masonry units, one or more of the following shall be used to control
convection currents in the core spaces,
(a) filling the core spaces,
(b) at least one row of semi-solid blocks at or below grade, or
(c) other similar methods.
(4) Masonry walls of hollow units that penetrate the ceiling shall be sealed at or near the ceiling adjacent to the roof
space to prevent air within the voids from entering the attic or roof space by,
(a) capping with masonry units without voids, or
(b) installation of flashing material extending across the full width of the masonry.
(5) Except as provided in Sentences (6) and (7), where a portion of a basement slab or a portion of a basement slab
edge is the only part of the slab that is at the exterior ground level such as a walk-out basement, or within 600 mm of
the exterior ground level, those portions shall have perimeter insulation extend not less than 600 mm below the slab
level. (See Appendix A.)
(6) Where the entire concrete slab is within 600 mm of the exterior ground level, the entire surface of the slab shall be
insulated. (See Appendix A.)
SB-12 Page 19
Supplementary Standard SB-12
(7) Where a slab contains heating ducts, pipes, tubes or cables, the entire heated surface of the slab that is in contact
with the ground shall be insulated.
2.1.1.7. Thermal Resistance Values for Roof Access Hatches and Eaves
(1) The thermal resistance values for insulation required by Articles 2.1.1.2. and 2.1.1.3. for exposed ceilings with
attic spaces are permitted to be reduced
(a) directly above access hatches, and
(b) near eaves to the extent made necessary by the roof slope and required ventilation clearances,
except that the thermal insulation value at the location directly above access hatches and inner surfaces of exterior wallsshall be not less than RSI 3.52.
2.1.1.8. Thermal Performance of Windows, Skylights and Sliding Glass Doors
(1) Windows, skylights and sliding glass doors shall meet
(a) the required overall coefficient of heat transfer in Tables 2.1.1.2.A, 2.1.1.2.B and 2.1.1.2.C and Tables
2.1.1.3.A, 2.1.1.3.B and 2.1.1.3.C, or
(b) the corresponding energy rating in Table 2.1.1.8.
Table 2.1.1.8.
Maximum U-Values and Minimum Energy Ratings (ER) for Windows, Skylights and Sliding Glass Doors
Forming Part of Sentence 2.1.1.8.(1)
Minimum Energy Ratings (ER)
(Btu/h•ft.2•°F)
Windows and Sliding Glass Doors
(2) The energy rating and the overall coefficient of heat transfer required for windows and sliding glass doors in a
residential occupancy shall be determined in conformance with
(a) CAN/CSA-A440.2, "Fenestration Energy Performance", or
(b) NFRC 100, "Procedure for Determining Fenestration Product U-factors" and NFRC 200, "Procedure for
Determining Fenestration Product Solar Heat Gain Coefficient and Visible Transmittance at Normal Incidence".
(3) A basement window that incorporates a loadbearing structural frame shall be double glazed with a low-E coating.
2.1.1.9. Minimum Thermal Resistance of Doors
(1) Except for doors in enclosed unheated vestibules and cold cellars, and except for glazed portions of doors, all
doors that separate heated space from unheated space shall have a thermal resistance of not less than RSI 0.7 where a
storm door is not provided.
SB-12 Page 20
Supplementary Standard SB-12
2.1.1.10. Additions to Existing Buildings
(1) Except as provided in Sentence (2), an addition to an existing building shall comply with
(a) one of the applicable compliance packages in Article 2.1.1.2. or 2.1.1.3., or
(b) the thermal performance requirements in Table 2.1.1.10.
(See Appendix A.)
(2) A one-storey sunroom addition to an existing building shall be deemed to be in compliance with Articles 2.1.1.2.
and 2.1.1.3. and Subsection 2.1.2., provided that the overall coefficient of heat transfer of
(a) doors, windows and walls has a maximum U-Value of
1.6 if the building is located in Zone 1 with less than 5000 heating degree days,
1.4 if the building is located in Zone 2 with 5000 or more heating degree days, or
1.4 if the building uses electric space heating, and
(b) roofs and skylights has a maximum U-Value of 2.6.
(See Appendix A.)
Thermal Performance Requirements for Additions to Existing Buildings(3)
Forming Part of Sentence 2.1.1.10.(2)
Electric Space Heating
Less than 5000 Degree-Days
5000 or more Degree-Days
Ceiling with Attic Space
Minimum RSI (R)-Value(1)
Ceiling Without Attic Space
Minimum RSI (R)-Value(1)
Minimum RSI (R)-Value(1)
Walls Above Grade
Minimum RSI (R)-Value(1)
Basement Walls
Minimum RSI (R)-Value(1)
Edge of Below Grade Slab # 600 mm Below Grade
Minimum RSI (R)-Value(1)
Slab # 600 mm below grade
Minimum RSI (R)-Value(1)
Windows and Sliding Glass DoorsMaximum U-Value(2)
Skylights Maximum U-Value(2)
Notes to Table 2.1.1.10.:
(1) The values listed are minimum RSI-Values for the thermal insulation component only. RSI-Values are expressed in (m²·K)/W.
(2) U-Value is the overall coefficient of heat transfer expressed in W/(m²·K).
(3) The building need not conform to minimum efficiency requirements for HRV's, domestic hot water heaters and space heating
equipment required in Article 2.1.1.2. or 2.1.1.3.
SB-12 Page 21
Supplementary Standard SB-12
2.1.1.11. Drain Water Heat Recovery
(1) Where a drain water heat recovery unit is installed to meet the requirements of this Subsection, the unit and its
installation shall conform to Sentences (2) to (5).
(2) Drain water heat recovery units shall conform to CSA B55.2,"Drain Water Heat Recovery Units".
(3) The minimum efficiency of a drain water heat recovery unit shall be determined in conformance with CSA B55.1,
"Test Method for Measuring Efficiency and Pressure Loss of Drain Water Heat Recovery Units".
(4) A drain water heat recovery unit shall be installed
(a) to receive drain water from all showers or at least two showers where there are two or more showers in a dwelling
unit, (See Appendix A.)
(b) in an upright position that does not diverge more than 5 degrees from the vertical,(c) in a position such that the cold water inlet connection is at the bottom of the unit,(d) downstream of a water softener where a water softener is installed, and(e) in a conditioned space or on the warm side of the dewpoint of the wall assembly.
(5) Except as required in Clauses 2.1.1.2.(10)(b) and 2.1.1.3.(8)(a), (b) and (d), and Sentence 2.1.1.2.(11), the
minimum efficiency of the drain water heat recovery unit shall be not less than 36% when it is tested in accordance with
Sentence (3).
2.1.2. Performance
2.1.2.1. Required Performance Level (See Appendix A.)
(1) The performance level shall be measured based on the simulated annual energy use of the building.
(2) The simulated annual energy use of the proposed building shall not be greater than the simulated annual energy
use of the building as if it met the performance level of a permitted compliance package in Subsection 2.1.1. selected on
the basis of
(a) Zone location,
(b) energy source, and
(c) equipment efficiency.
(3) The simulated annual energy use shall be calculated for the
(a) proposed building, and
(b) building conforming to the applicable compliance package.
(4) For the purpose of calculations required in Sentence (3),
(a) a recognized annual energy use simulation software shall be used to calculate annual energy use,(b) local climatic data shall be used, and(c) the equivalent domestic hot water, appliance and other plug-in loads shall be assumed in both calculations.
(5) Except as provided in Sentence (6), for the purpose of Clauses (3)(a) and (3)(b), the air leakage rate of a dwelling
unit may be assumed to be
(a) 2.5 air changes per hour at an air pressure differential of 50 Pa for detached homes, and
(b) 3.0 air changes per hour at an air pressure differential of 50 Pa for attached homes.
(6) For the purpose of Clause (3)(a), values less than Sentence (5) may be used provided that the values are verified
with air leakage tests as conducted in accordance with the requirements of Clause 12.2.1.2.(3)(a) of Division B in the
Building Code.
SB-12 Page 22
Supplementary Standard SB-12
(7) For the purpose of calculations required in Clause (3)(b), the building shall have identical dimensions and
orientation as the proposed design, except where the glazing to wall ratio exceeds 22%, the glazing area shall be
reduced proportionally along each exposure until the limit is met.
(8) For the purpose of calculations required in Clause (3)(b), where frame construction is used, the design of the
framing system shall assume a spacing of
(a) 400 mm o.c. for wall studs,
(b) 400 mm o.c. for exposed floors joists, roof joists and roof rafters, and
(c) 600 mm o.c. for roof trusses.
(9) For the purpose of calculations required in Clause (3)(b), building envelope component properties and
characteristics not specifically described in this Subsection and Subsection 2.1.1. shall be modeled the same for both the
proposed design and a design based on a permitted compliance package unless it can be shown such properties and
characteristics of the proposed design constitute additional energy conservation measures.
(10) Where the overall thermal performance of the proposed building envelope is less than the envelope performance of
the compliance package that is compared against it, the reduction in the performance level of the building envelope shall
not be more than 25%.
Other Acceptable Compliance Methods
2.1.3.1. Other Acceptable Compliance Methods (See Appendix A.)
(1) A building shall be deemed to be in compliance with the requirements of Subsection 2.1.1. provided that the
building is in compliance with the technical requirements of NRCan,"Energy Star for New Homes: Technical
Specifications – Ontario".
SB-12 Page 23
Supplementary Standard SB-12
SB-12 Page 24
Supplementary Standard SB-12
Appendix A
Explanatory Material for SB-12
A-Table 1.4.1.2. National Fenestration Rating Council.
National Fenestration Rating Council
6305 Ivy Lane, Suite 140
Greenbelt, MD 20770, USA
web site: www.nfrc.org
A-2.1.1. Compliance Packages.
Individual components of compliance packages found in Tables 2.1.1.2.A, 2.1.1.2.B and 2.1.1.2.C and Tables 2.1.1.3.A,
2.1.1.3.B and 2.1.1.3.C are not permitted to be mixed with similar components of other compliance packages either found
within the same Table or similar components of compliance packages found in other Tables.
A-2.1.1.1.(3) Mechanical Equipment.
Compliance package tables referred to in this Sentence contain energy efficiency requirements for some or all mechanical
equipment. Where a compliance package includes an energy efficiency level for space heating equipment, domestic hot
water heater or heat recovery ventilator, conformance with the package can only be achieved if the building is equipped
with the mechanical equipment specified in the compliance package.
A-2.1.1.1.(7), (8) and (10) Fenestration to Wall Ratio.
When the fenestration to wall ratio is calculated, all fenestration areas and the entire peripheral wall above grade is
included. The peripheral wall area includes floor rim board areas and all above grade wall areas. It is essentially the sum
of the above grade walls that separate conditioned spaces from unconditioned spaces, and adjacent units. In the case of an
attached garage, the walls that are common with the house and the garage are also included in the wall area calculations.
For attached homes, the above grade portions of the walls that are common to other conditioned units are also included in
the wall area. The fenestration area is based on the rough structural opening provided for windows, skylights, sliding glass
doors, and for glazed portions in doors. For A–Frame structures with steeply inclined roofs that also act as walls, the roof
portion that serves as the interior wall area can be considered as the wall area in calculating the fenestration to wall ratio.
A-2.1.1.2.(6)(a), (8)(a), (9)(a) RSI Reduction of Above Grade Walls in Conjunction
with Upgrading U-Value of Glazing - Zone 1.
Where the above grade wall insulation is permitted to be reduced to RSI 3.52, one of the required compensating measuresis to upgrade the window U-Value in accordance with Clauses 2.1.1.1.(8)(a) to (c). This upgrade is independent of theglazing upgrade that may be required due to a fenestration ratio that is higher than 17%. In cases where the above gradeinsulation is reduced to RSI 3.52 and compensated for with a fenestration upgrade, and the building has more than 17%fenestration, the glazing would be required to be upgraded a second time.
SB-12 Page 25
Supplementary Standard SB-12
A-2.1.1.3.(6)(a) and (7)(a) RSI Reduction of Above Grade Walls in Conjunction with
Upgrading U-Value of Glazing - Zone 2.
Where the above grade wall insulation is permitted to be reduced to RSI 3.52, one of the required compensating measuresis to upgrade the window U-Value in accordance with Clauses 2.1.1.1.(8)(a) to (c). This upgrade is independent of theglazing upgrade that may be required due to a fenestration ratio that is higher than 17%. In cases where the above gradeinsulation is reduced to RSI 3.52 and compensated for with a fenestration upgrade, and the building has more than 17%fenestration, the glazing would be required to be upgraded a second time.
A-2.1.1.6.(1) Permitted Basement Insulation Gap.
The provision refers to the gap between basement insulation and the floor level that might be left at the bottom of a
foundation wall. Insulation can be extended from the underside of the subfloor to the floor level of the basement, or a gap
may be left provided that the gap is not more than 200 mm when measured from floor level to where the insulation is
terminated.
A-2.1.1.6.(5) and (6) Slab Insulation.
Except where specifically required in a compliance package, the entire surface of the slab is only required to be insulated
when the entire concrete slab is completely within 600 mm of the exterior ground level. A typical example would be a slab
on ground construction without a basement. If a slab is partially at the exterior ground level (i.e. a walkout basement) or
partially within 600 mm of the exterior surface, then only those parts are required to be insulated with perimeter insulation.
Where a slab of a house is completely or partially within 600 mm of the exterior ground level, either the entire surface ofthe slab or the perimeter of the slab is required to be insulated but not at both locations.
A-2.1.1.10.(1) Additions to Existing Houses.
In Clause 2.1.1.10.(1)(a), the design and construction of an addition to an existing house can conform to the minimum
building envelope and mechanical equipment requirements where an applicable compliance package is selected from Article
2.1.1.2. or 2.1.1.3.
Alternatively, Clause 2.1.1.10.(1)(b) provides a simpler approach and permits an addition to an existing building to complywith the appropriate column in Table 2.1.1.10. since the design and construction of an existing building is unlikely to bedetermined and matched against an applicable compliance package from Article 2.1.1.2. or 2.1.1.3.
Table 2.1.1.10. further exempts both an addition and an existing building from conforming to minimum efficiencyrequirements for HRV's, domestic hot water heaters and space heating equipment required in Article 2.1.1.2. or 2.1.1.3. This would permit existing mechanical equipment to serve the entire building provided that it has the necessary capacity.
A-2.1.1.10.(2) Sunroom Additions to Existing Houses.
A sunroom addition to an existing house referred in this Sentence applies to a one-storey structure built substantially with
wall/roof fenestration and glass doors but which sometimes contain unglazed low wall panels that support wall glazing
above it. Since the glazing percentage of sunrooms exceeds the limits permitted for compliance packages in Articles
2.1.1.2. and 2.1.1.3. and performance compliance methods may not be possible, these sunrooms are exempt from
compliance package requirements, provided that the thermal performance of the glazing is enhanced further than what is
required for non-sunroom additions.
The maximum U-Values for doors, sliding glass doors, wall glazing and supporting wall panels for sunroom additions inClause 2.1.1.10.(2)(a) have been derived from the maximum U-Values for window and sliding glass doors in additions toexisting buildings in Table 2.1.1.10. and then upgraded in accordance with Sentence 2.1.1.1.(8).
The maximum U-Value of 2.6 for roofs and skylights for sunroom additions in Clause 2.1.1.10.(2)(b) has been derivedfrom upgrading the maximum U-Value of 2.8 for skylights in additions to existing buildings in Table 2.1.1.10. consistentwith the methodology used in Sentence 2.1.1.1.(8).
SB-12 Page 26
Supplementary Standard SB-12
A-2.1.1.11.(4)(a) Drain Water Heat Recovery Units for Showers.
For the purpose of the prescriptive trade off provisions in Subsection 2.1.1., the term "all showers" includes the case
where there is only one shower in a dwelling unit. If there is only one shower, that shower is required to be connected to a
drain water heat recovery unit. Where there are two or more showers, drain water from at least two showers are required
to be connected to a single drain water heat recovery unit or to two individual drain water heat recovery units.
A-2.1.2.1. Application of Performance Compliance Path.
This Article requires two annual energy use simulations. These simulations compare the simulated annual energy use of
the proposed building with the simulated annual energy use of an applicable compliance package. The simulated annual
energy use of the proposed building cannot exceed the simulated annual energy use of an applicable compliance package.
Where a performance compliance path is selected, it is the intent of Sentence 2.1.2.1.(2) that the performance level of thecompliance package takes into account the requirements listed in Subsection 2.1.1. that are applicable to that compliancepackage. Similarly, the annual energy use calculation for a compliance package referenced in Clause 2.1.2.1.(3)(b) shalltake into account the requirements listed in Subsection 2.1.1. that are applicable to that compliance package.
For the purpose of calculating the annual energy use of a proposed design and a design based on a selected compliancepackage, the following software may be used:
• HOT2000 version 9.34c or newer versions• other software referenced by the Energuide Rating System• RESNET accredited Home Energy Rating System (HERS) software, such as:
• OptiMiser• EnergyGauge• EnergyInsights• REM/Rate
A-2.1.3.1. Other Acceptable Compliance Methods.
Compliance with the technical requirements of the Energy Star Program may be achieved using either the prescriptive path
or the performance path required by NRCan,"Energy Star for New Homes: Technical Specifications – Ontario".
Clause 2.1.1.1 of NRCan,"Energy Star for New Homes: Technical Specifications – Ontario" allows the designer to use anNRCan-approved compliance option described in NRCan, "Energy Star for New Homes: Compliance Options" (Ontario).
Only the technical provisions contained in NRCan,"Energy Star for New Homes: Technical Specifications – Ontario" andother Energy Star documents it references are mandatory under this Supplementary Standard. However, in addition to thetechnical requirements, the administrative requirements of the Energy Star documents may be used to demonstratecompliance with Sentence 2.1.3.1.(1) by obtaining an Energy Star label for the building.
SB-12 Page 27
Supplementary Standard SB-12
SB-12 Page 28
Source: http://www.publications.serviceontario.ca/ecomlinks/510136_OBC_Amendment_8.pdf
ISSN: 2393-9583 (P)/ 2393-9591 (O) An International Journal of Research in AYUSH and Allied Systems Review Article REVIEW ON ROLE OF HERBAL DRUG IN THE PREVENTION AND MANAGEMENT OF KIDNEY DISEASE Laxmi Maharana1*, Om Prakash Dadhich2 *1PhD Scholar, 2Dean Academic & H.O.D. P.G. Dept. of Sharir Kriya, National Institute of Ayurveda, Jaipur, India.
the business voice of advanced energy ILLINOIS' ELECTRIC POWER SYSTEM AND THE CLEAN POWER PLAN The U.S. Environmental Protection Agency (EPA) will soon release the final rule for carbon emissions from existing power plants, called the Clean Power Plan (CPP). The rule represents the next step in the process of carbon regulation that began with the Supreme Court's determination in 2007 that carbon dioxide (CO )