Joutsenmerkki.fi
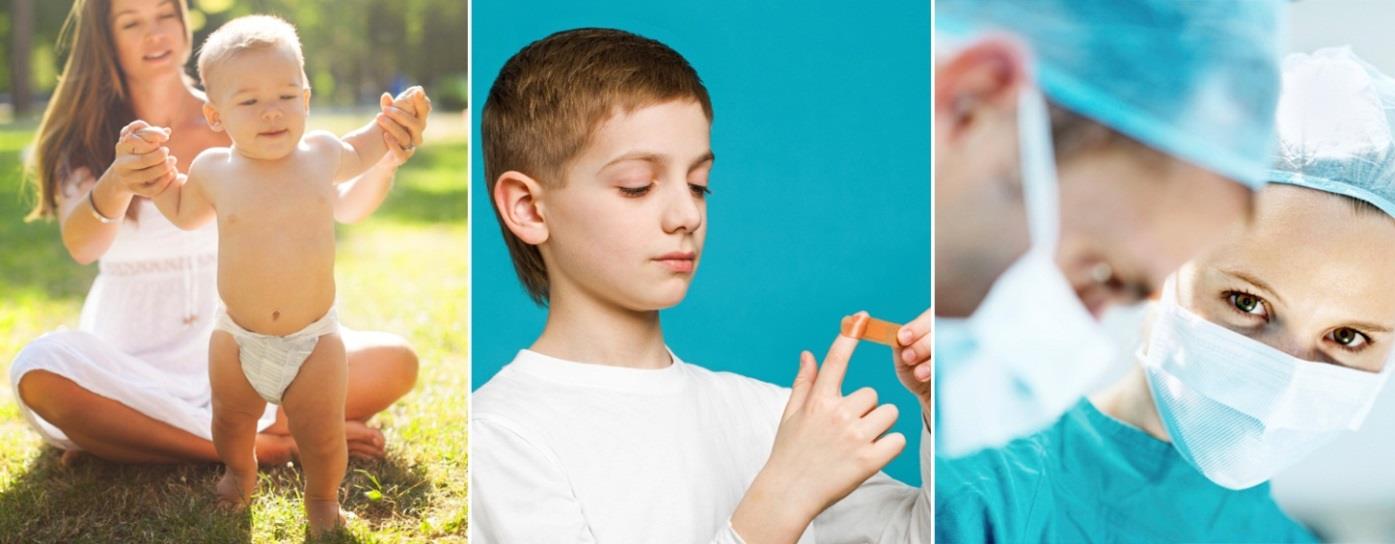
About Nordic Ecolabelled
Sanitary products
Version 6.0
Background to ecolabelling
27 November 2015
Draft for consultation
Nordic Ecolabelling
023 version 27 November 2015 This document is a translation of an original in Norwegian. In case of dispute, the original document should be taken as authoritative.
Addresses
In 1989, the Nordic Council of Ministers decided to introduce a voluntary official ecolabel, the Nordic
Ecolabel. These organisations/companies operate the Nordic ecolabelling system on behalf of their own
country's government. For more information, see the websites:
Ecolabelling Denmark
Ecolabelling Iceland
Danish Standards Foundation
Henrik Ibsens gate 20
Umhverfisstofnun
Suðurlandsbraut 24
Göteborg Plads 1
Tel: +47 24 14 46 00
IS-108 REYKJAVIK
DK-2150 NORDHAVN
Fax: +47 24 14 46 01
Tel: +354 591 20 00
Tel: +45 72 300 450
[email protected]
Fax: +354 591 20 20
Fax: +45 72 300 451
www.svanemerket.no
[email protected]
[email protected]
www.svanurinn.is
Ecolabelling Sweden
Ecolabelling Finland
This document may only be copied in its
entirety and without any type of change.
SE-100 64 STOCKHOLM
FI-00101 HELSINKI
It may be quoted from provided that
Nordic Ecolabelling is stated as the
[email protected]
[email protected]
Nordic Ecolabelling
27 November 2015
Background document
Nordic Ecolabelling has had criteria for sanitary products for over 20 years, covering products such as diapers and sanitary towels. The criteria have now been revised, and the
new version 6 is out for consultation from 27 November to 10 February. In this revision, the product group has been expanded to include more products in the health sector. This
document describes the environmental impact in the life cycle of sanitary products and how Nordic Ecolabelling has selected the requirements that have to be fulfilled in order
for the products to qualify for the Nordic Ecolabel.
The products that may be Nordic Ecolabelled are breast pads, children's diapers, incon-
tinence care products, sanitary towels, tampons, cotton buds, cotton wadding, cotton pads, cotton wool, sauna underlays, bibs, plasters, compresses, mattress
covers/protectors, draw sheets, bed linen, wash cloths, surgical gowns, patient gowns/patient covers, surgical masks and caps. Products with added cosmetics,
medication/medicines, disinfecting substances and similar cannot be ecolabelled in this product group. It is possible to ecolabel similar products under other Nordic
Ecolabelling criteria documents, including reusable diapers under the criteria for textiles, serviettes and paper towels under the criteria for tissue paper and wet wipes under the
criteria for cosmetics.
It has been shown that the majority of the environmental impact from disposable
sanitary products comes from the production of the constituent materials. The primary materials used in sanitary products are cellulose pulp, superabsorbents, cotton, viscose
and various polymers. The environmental impact of the products can be reduced by setting strict requirements concerning the production of the materials used, by shifting to
less environmentally problematic materials or by reducing the quantity of materials used in the products. The latter area is difficult for Nordic Ecolabelling to influence, because
even small changes in the product composition can change the function or other properties of the products which consumers appreciate. The products that fall under the
umbrella of sanitary products have an absorbent, protective and/or removing function for body fluids or faecal matter. They vary greatly and can have extremely complex
material combinations. This makes it difficult to set general requirements concerning the composition of the products in order to reduce the use of the more environmentally
problematic materials. Part of the environmental impact comes from the handling of the products in the waste phase. However this is another area of low steerability, since it is
difficult for Nordic Ecolabelling to influence how consumers handle the products after use. Nordic Ecolabelling also has little influence over municipal waste management
In this revision, Nordic Ecolabelling has continued to set detailed requirements
concerning the constituent materials and chemicals used in the manufacture of sanitary products. Version 5 of the criteria set a requirement to ensure that the product has either
a high proportion of renewable materials, a certain proportion of biopolymers among the plastic materials or limited CO emissions calculated as GWP (Global Warming
Potential). The options in the requirement are changed so that there must be a certain percentage of renewable and/or recovered material in the product or packaging.
The burden of requirements for a specific material is set in relation to their weight percentage in the finished product. The higher percentage of a specific material, the more
requirements are set. In many cases the limits for the different requirements to occur, are
023e_6_0_hearing_Background.docx 3 (93)
Nordic Ecolabelling
27 November 2015
Background document
divided into several levels according to the material type, with limits of 1, 5, 10 and/or 20 %.by weight.
The requirements for fluff pulp and paper are updated in relation to updates in the Nordic Ecolabel's general requirements for these types of materials. The biggest
amendment is that there is now set an absolute demand for energy for production of polymers if the content of a certain polymer type is 5 % or more of the product's total
weight. In addition, there are requirements for the renewable raw materials used in polymers and superabsorbent polymers. The requirements for content of chemical
substances in the materials are also tightened.
Basic facts about the criteria
2.1 Sanitary products that may carry the Nordic
Ecolabel
Products that can be labelled
The criteria document carries the following description of which products can be Nordic
Ecolabelled:
The product group "Sanitary products" covers disposable products with an absorbent and/or protective/removing function for bodily fluids and faecal matter. The function of the products may furthermore be to facilitate bodily cleansing of such fluids or to facilitate the removal of products applied intentionally to the body, such as cosmetics.
Products included are: breast pads, children's diapers, incontinence care products, (panty-liners, formed diapers and diapers
with tape strips), sanitary towels (pads and panty-liners), tampons, cotton buds, cotton pads, cotton wool, sauna underlays, bibs, plasters, compresses, mattress covers/protectors, draw sheets, bed linen, wash cloths, surgical gowns, patient gowns/patient covers, surgical masks and caps.
Relevant disposable products in addition to those specified above may be included in the product group upon request if they are
viewed as sanitary products. This applies only to products made of materials for which requirements are imposed in the criteria. Nordic Ecolabelling will determine which new products may be included in the product group.
It is thus specified that only disposable products are covered by the product group, and
that only products made from materials for which requirements are imposed in this document may be included. Requirement O2, Percentage composition, states that at least
95% of the materials used must be materials subject to requirements in the criteria. This means other materials that appear in small quantities may be included without specific
requirements being met. Such other materials may be rubber (elastic), CaCO and wax to
prevent leakage via the seams.
Relevant products may, however, have been overlooked, which is why the definition allows for other disposable sanitary products to be included with the consent of Nordic
Ecolabelling. It is thus up to Nordic Ecolabelling to determine which products may be included. This is because it is important to assess whether there are other performance
and quality requirements that the new products should meet, or whether the product could already be Nordic Ecolabelled in accordance with other criteria documents. It is
important that the new products comprise materials for which requirements have been set in the criteria, so that the set of criteria does not become too extensive. Further
information is provided in section 7.1.
023e_6_0_hearing_Background.docx 4 (93)
Nordic Ecolabelling
27 November 2015
Background document
Sanitary products that cannot be ecolabelled
The following definition describes which types of product cannot be Nordic Ecolabelled
under this product group:
Serviettes, wet wipes, dry wipes, paper towels or wash cloths made of paper, multiple use wash cloths, mesh pants, disposable
gloves and toothpicks are not eligible for a Nordic Ecolabel under these criteria for sanitary products. Many of these products can, however, be labelled under other criteria for the Nordic Ecolabel or the EU Ecolabel. Products that can be ecolabelled according to the criteria for tissue paper or cosmetic products (i.e. products that comply with the product group definitions in these criteria documents) cannot be ecolabelled according to the criteria for sanitary products.
Other, similar, products that have a function other than absorbing and/or protecting against bodily fluids/faecal matter or cleansing of cosmetic products, for example, cannot be ecolabelled under the criteria for sanitary products. Please contact Nordic Ecolabelling for more information.
Products with added cosmetics, medication/medicines, disinfecting substances and similar cannot be ecolabelled in this product
The definition of what may not be included covers various potential products that, in some cases, could be granted a licence in accordance with other criteria documents.
Alternatively, the examples have a function that does not fully match the product group definition. More information and justification of why these products are not included can
be found in section 7.1.
2.2 Justification for Nordic Ecolabelling
It has been shown that much of the environmental impact from disposable sanitary
products comes from the production of the constituent materials. This applies in particular to those used as primary materials, but also materials that have a larger carbon
footprint per kilo, for example, than other materials since they are more energy-intensive to produce and/or come from fossil raw materials. The primary materials used in sanitary
products include cellulose pulp, superabsorbents, cotton, viscose and polymers. The environmental impact of the products can be reduced by setting strict requirements
concerning the production of the materials used, or by shifting to renewable materials, as long as they do not have other undesirable effects. It is thus important to set require-
ments concerning the chemicals that are found in the product.
The environmental impact of sanitary products can also be reduced through the manu-
facturers focusing on a reduction in the weight of the end product, and on optimising the material composition of the products. The latter area is, however, difficult for Nordic
Ecolabelling to influence, because even small changes in the product composition can change the function or other properties of the products which consumers appreciate.
The products that fall under the umbrella of absorbent, protective and removing sanitary products vary greatly and can have extremely complex material combinations, something
which also makes it difficult to set general requirements concerning the composition of the products in order to reduce the use of the more environmentally problematic
Part of the environmental impact comes from the handling of the products in the waste
phase, but this is another area of low steerability, since it is difficult for Nordic Ecolabelling to influence how consumers handle the products after use. Nordic
Ecolabelling also has little influence over municipal waste management systems.
Section 6 provides a more in-depth assessment of the environmental conditions
surrounding disposable sanitary products. In addition, many of the materials used are
023e_6_0_hearing_Background.docx 5 (93)
Nordic Ecolabelling
27 November 2015
Background document
described in more detail in section 7, which also explains the requirements that have been set.
Nordic Ecolabelled sanitary products with an absorbent, protective and removing function:
Meet strict environmental requirements concerning the materials in the product Promote good health through tough chemical requirements Promote materials from renewable sources in the product and its packaging.
About the criteria revision
Purpose of the criteria revision
Before this revision began, an evaluation of the criteria for the Nordic Ecolabelling of
sanitary products was conducted in order to check whether the requirements have an
environmental benefit, have the correct limit values/levels, are not too complex and restrictive for the development of the product types, and so on. The conclusion of the
evaluation was that the criteria should be revised, with the aim of version 6 of the criteria being:
to tighten the requirements concerning various polymers, including bio-based
superabsorbent polymers (SAP)
to assess and improve the requirements concerning energy and climate,
particularly for renewable raw materials
to update requirements concerning paper and pulp in order to harmonise them
with corresponding requirements for the Nordic Ecolabelling of paper products
to review all the requirements in terms of requirement levels, nominal limits and
scope for simplifying the requirements.
About this criteria revision
The work was conducted as an internal review by the Nordic secretariats of Nordic
Ecolabelling in 2014 and 2015. The working group maintained ongoing contact with the
industry through licensees and other industry players, including material manufacturers and industry organisations.
Rebecca Uggla of Ecolabelling Sweden was project manager, while Ingvild Kvien and Elisabeth Magnus of Ecolabelling Norway also participated in the project.
3.1 Earlier versions of the criteria
This is the background document to the proposed version 6 of the criteria, which is now
subject to consultation in the period 27 November 2015 until 10 February 2016. Nordic
Ecolabelling looks forward to comments on the document.
Sanitary products are one of the older product groups within Nordic Ecolabelling.
Originally, there were separate criteria for diapers and feminine hygiene products. The criteria for diapers were first adopted in June 1994 and the criteria for feminine hygiene
products were adopted in December 1996. These two sets of criteria were merged to
023e_6_0_hearing_Background.docx 6 (93)
Nordic Ecolabelling
27 November 2015
Background document
create the criteria for sanitary products, version 4, which was approved on 27 August 2001.
New types of sanitary product have continuously been included in the product group, with version 5 of the criteria, for example, adding the following products: cotton buds,
cotton wadding, toothpicks, mattress covers, draw sheets, bed linen, wash cloths, surgical gowns and massage table paper roll. Version 5 was approved in March 2008 and will
remain valid until 31 March 2017.
Through all the revisions, new requirements have gradually been introduced with regard
to manufacture, emissions, chemical substances, waste management and waste quantities, plus packaging and product information. Version 5 gained a specific focus on climate
impact when we introduced requirements concerning Global Warming Potential (GWP) or alternative requirements on the proportion of renewable raw materials.
As part of the revision work for the sixth generation of the criteria, plasters and other products for healthcare have been included, as well as disposable materials used by
dentists and products that may be used in operations (patient gowns, exam table paper, surgical masks and caps), plus products used primarily within the care sector.
3.2 Nordic Ecolabel licences in the Nordic Market
The number of licences has generally risen over the years. There are a total of 30 Nordic
Ecolabel licences for sanitary products in the Nordic region as of mid-January 2015
based on version 5 of the criteria. Each licence may include several products, so it is estimated that a total of 383 products were covered in January 2015.
Figure 1 below shows how the 30 Nordic licences are distributed across the different product categories. Many of the licensees include more than one type of product under
their licence, which is why for example sanitary towels/panty-liners/tampons have been put together as one product category. It is clear that the three groups, sanitary
towels/panty-liners/tampons, diapers and incontinence care products; make up the greatest proportion of Nordic Ecolabelled sanitary products in the Nordic market. The
category "other" is a catch-all category for remaining product types.
023e_6_0_hearing_Background.docx 7 (93)
Nordic Ecolabelling
27 November 2015
Background document
Percentage distribution of trade names for
licensed sanitary products 2015
Incontinence care
Bed linen, mattress
Sängkläder, skyddslakan och
protectors, draw sheets
Figure 1 Distribution of licensed sanitary products in the Nordics as of January
2015. The products, which are covered by 30 different licences, have been
divided into seven categories. The percentage distribution relates to the total
number of licences, and has no relevance to share of market or sales.
The trade names stated in the licences are thus largely associated with children's diapers,
with these accounting for almost half of the total trade names. Sanitary towels and panty-liners are the second largest group, followed by incontinence care products. Altogether,
these account for over 80% of the trade names
The Nordic market
An assessment of Nordic Ecolabelled sanitary products in 20111 indicated that they have considerable penetration in the Nordic market. Exact figures are unavailable, but an
estimate shows that in 2015 ecolabelled products account for around 30% of the children's diaper market in Finland, with figures of 65% in Sweden and 60% in Norway.
The assessment also concluded that the market share for sanitary towels and panty-liners was around 25% in Finland and 2% in Denmark. Nordic Ecolabelled products have a
negligible share of the incontinence care product market, except in Denmark, where market share is around 50% in public procurement. Most of the information below on
the market has also been taken from the 2011 assessment.
Manufacturers of sanitary towels and panty-liners sold on the Nordic market include
SCA Hygiene Products, Procter & Gamble, Johnson & Johnson, Delipap, Ontex and Bodywise, with SCA and Procter & Gamble as the market leaders. According to a study
1 Utvärdering av Svanenmärkta Hygienprodukter Version 5. Rapport till Nordisk Miljömärkningsnemd. 21 november
2011. Kan fås ved å kontakte Nordisk Miljømerking.
023e_6_0_hearing_Background.docx 8 (93)
Nordic Ecolabelling
27 November 2015
Background document
by SCA2 , women in Western Europe aged 15-49 use around 350 sanitary towels per year. Market share for branded sanitary towels and tampons is dominated in the Nordic region
and the rest of Europe by just a few major manufacturers and their brands. In addition to these brands, there are several supermarket chains and pharmacies that have private label
products. Supermarkets and pharmacies are the leading sales channels for this type of product. They are, however, also sold in health food stores and online.
During the evaluation of the criteria for the Nordic Ecolabelling of sanitary products, the manufacturers noted the following developments:
Sanitary towels and diapers are becoming thinner, softer and at the same time
more effective. More SAP and less fluff.
Dyes and print are being used more. Biomaterials are likely to play a greater role in future product developed.
Biomaterials used today include compostable polymers such as PLA.
The two major players in incontinence care products in the Nordic region are: SCA
Hygiene Products AB (the "Tena" range) and Abena A/S (the "Abri" range). Other market share is accounted for by private label products such as Matas in Denmark and
Attends and Hartmann in Norway. Both Abena and SCA state that the market is largest in the professional segment (institutions, hospitals, care homes). Incontinence care
products are purchased primarily via public procurement. The products are used by hospitals and institutions, or they are provided to citizens in private homes. However,
incontinence care products can also be found in supermarkets such as Matas and in pharmacies, and they can be purchased online. Sales of incontinence care products are
rising, as the population ages and more people suffer from incontinence. The condition is considered a widespread disease, with one in ten Danes over the age of 67 suffering
incontinence, for example3. The predicted trend is for the products to be increasingly available in supermarkets.
There appears to be an increased interest in other types of sanitary products which are primarily used in the care sector. Players in the current market include Cellkomb, which
manufactures a number of disposable products for the health service4. Other industry players are 3M (Nexcare), Beiersdorf (Hansaplast), Cederroth (Salvequick), Johnson &
Johnson (Compeed), Mölnlycke Health Care and Norgesplaster. ASAP Norway AS is a small company, which has developed an absorbent disposable sheet for birthing beds5.
Other labels
There are very few other labelling systems for sanitary products in the Nordic market.
The most common label on diapers is the Asthma and Allergy label. There are also organic labels for products such as cotton wool, cotton buds and breast pads. Such
schemes apply to the cotton in the products, which may also carry the Fairtrade label.
2 SCA. Marknad - Mensskydd. 2015-03-24. http://www.sca.com/sv/Om_SCA/Var_verksamhet/Personliga_hygienprodukter/Marknad-menstruationsskydd-
SCA/ (hentet 13. april 2015) 3 Retsinformasjon Danmark. Forslag til folketingsbeslutning om styrkelse af inkontinensindsatsen. Fremsat den 12. april 2011 https://www.retsinformation.dk/Forms/R0710.aspx?id=136752 (hentet 13. april 2015) (hämtat 22 april 2015) mtat 22 april 2015)
023e_6_0_hearing_Background.docx 9 (93)
Nordic Ecolabelling
27 November 2015
Background document
Type 1 ecolabels
Type 1 ecolabels are the labels that make it easiest for consumers to choose. Products are
approved according to set environmental requirements, and an independent third party checks that the products meet these requirements. Ecolabelling sets fixed requirements
(limit values) for products. These requirements are based on a cradle-to-grave assess-ment, and are developed according to standard ISO 14 024. The system excludes
products that do not meet the requirements. The criteria for the Nordic Ecolabel are updated in an open process involving the participation of public agencies, consumers,
industry, researchers, environmental movements and retailers, for example, and the requirements are formulated to promote the best products. The official ecolabels that are
members of the Global Ecolabelling Network (GEN) and have requirements for sanitary products include the EU Ecolabel, which has criteria for "absorbent hygiene products"6.
These were adopted in October 2014. Another ecolabel that is a member of GEN is Green Seal in the USA, which has criteria for paper products, amongst them paper
diapers. One of their requirements is that 50% of the materials must be "post-consumer material"7.
Environmental product declarations (type 3 ecolabels)
Environmental product declarations (EPDs) do not set requirements for the products,
but provide documentation of the product's environmental impact associated with production, use and disposal, based on a life cycle analysis of the product. In order to
produce an EPD, Product Category Rules (PCR) must be in place for the product category. For sanitary products, there is version 2 of a PCR from EPD International
called "Absorbent hygiene products"8. As mentioned, there are no requirement levels in the EPDs, and it is difficult to compare different EPDs, since there are no standardised
methods for calculating the environmental impact of factors such as energy consumption.
Private labelling schemes
The Nordic Asthma and Allergy Associations have different criteria for labelling their
products, and only some of those criteria are public. In Norway, the products are assessed by an independent expert panel comprising two doctors and one researcher9. In
Denmark, the web page for diaper manufacturers states that declared products must contain no fragrance, dyes, formaldehyde or formaldehyde donors10.
Purchasing rules
Both the EU and several individual countries have their own purchasing rules and Green
Public Procurement (GPP) scheme. The EU has so far not developed anything for sanitary products, but Sweden has, and the industry organisation for non-wovens
(EDANA) has drawn up a number of requirements. The requirements set under these
6 EU Ecolabel. Product Groups and Criteria. Absorbent Hygiene Products. Commission Decision of 24 October 2014. http://ec.europa.eu/environment/ecolabel/products-groups-and-criteria.html (hentet 15. april 2015) 7 Green Seal Standard for Sanitary Paper Products, 3rd Edition. Hentet fra:
(21. Januar 2015) 8 EPD International AB, Sweden, PCR Absorbent hygiene products. 2015. Hentet fra: (hentet 13. april
2015) 9NAAF. Norge Astma og Allergi Forbund i Norge. Produktvurderingsutvalg. 08.09.2014. http://www.naaf.no/no/om_naaf/Egne-rad-og-utvalg/Produktutvalget/ (hentet 13. april 2015) 10 Astma-Allergi Danmark. Bleer og dyner. http://www.astma-allergi.dk/den-bla-krans/bleer-og-dyner (hentet 13.
023e_6_0_hearing_Background.docx 10 (93)
Nordic Ecolabelling
27 November 2015
Background document
schemes are summarised in a written report for the development of the EU Ecolabel's criteria for absorbent hygiene products11.
Current EU regulations allow considerable scope to use the requirements on which ecolabelling and environmental certification are based in public procurement. Article 23,
paragraph 6 of Directive 2004/18/EC of the European Parliament and of the Council states which criteria apply in order for ecolabels to be used. These are criteria that the
Nordic Ecolabel fulfils. In addition, there is now a new EU Directive on public procurement, 2014/24/EU, which opens the way for even more aggressive use of
ecolabelling and environmental certification in public procurement. This directive is in the process of being transposed into law in the Nordic region, but the final text for each
country has not yet been agreed. The Norwegian draft for consultation states that clients may require a particular labelling scheme as documentation that the goods, services or
building and construction work has environmental, social or other properties as stated in the specification of requirements,, tendering criteria or contractual terms12. The Nordic
Ecolabel and the EU Ecolabel are both labelling schemes that constitute sufficient documentation as regards this consultation draft for Norwegian public procurement.
Environmental assessment of sanitary
products
6.1 Disposable products
There has been a long-standing debate about disposable products versus reusable
products and which are best from an environmental perspective. It is a simple fact that disposable diapers and sanitary products are widely used, both by consumers and the
health service. In the years since the first disposable diapers came onto the market just before the Second World War, the products have undergone constant development in
terms of form, function and material composition.
There have been many studies and life cycle analyses aimed at determining whether
textile or disposable diapers are best. A British LCA study of diapers for the Environment Agency "Life Cycle Assessment of Disposable and Reusable Nappies in
the UK"13 from 2005 was updated in 2008 and concluded that there is no significant difference in environmental impact between the three diaper systems studied: disposable
diapers, textile diapers laundered at home and textile diapers with a collection system for laundering. The report gives recommendations on reducing the environmental impact of
all three systems. For disposable diapers, the key point is to reduce the environmental impact of the materials used in the product by reducing the weight and/or improving the
manufacture of the materials. A similar study "Life Cycle Assessment: Reuse and disposable nappies in Australia"14 from 2009 shows similar results. This study assessed
11EU Ecolabel for Sanitary Products. Preliminary report_5th draft. March 2013. Page 44 - 48.
http://susproc.jrc.ec.europa.eu/sanitaryproducts/whatsnew.html (hentet 14. april 2015) 12 Den norske regjeringen. Ny forskrift om offentlige anskaffelser. Høringsnotat 2. https://www.regjeringen.no/contentassets/a20179ad1beb4de9b4d7f5ccec80c094/horingsnotat-2-forskrift-offentlige-
anskaffelser.pdf (hentet 16. mai 2015) 13 Defra (the British Environment Agency). Life Cycle Assessment of Disposable and Reusable Nappies in the UK,
2005 with update in 2008. ISBN: 1-84-432427-3. https://www.gov.uk/government/publications/an-updated-lifecycle-
assessment-for-disposable-and-reusable-nappies (hentet 13. april 2015) 14 OBrien, K. R., Olive, R., Hus, Y.C., Bell, R., Morris, L. and Kendall, N. (2009). Life Cycle Assessment: Reusable and
disposable nappies in Australia. In: Australian Life Cycle Assessment Society Conference 2009. 6th Australian
Conference on Life Cycle Assessment, Melbourne, (1-14). 17-19 February. Life Cycle assessment: Reuse and
023e_6_0_hearing_Background.docx 11 (93)
Nordic Ecolabelling
27 November 2015
Background document
water consumption, non-renewable energy, waste and use of productive land for disposable and reusable diaper systems. The greatest difference between the systems was
that the consumer has greater control over the environmental impact when using reusable diapers. Unsurprisingly, diapers laundered in cold water and air dried had the
lowest environmental impact.
A life cycle analysis of surgical gowns for wet operations (specialist gowns) "Lifecycle
analysis of surgical gowns"15 from 2003 concludes that reusable gowns have less of an environmental impact than equivalent disposable products. Both the products contain
similar amounts of polyester, but that is where the similarities end. None of the gowns contain biopolymers. The disposable gowns also contain viscose, cellulose, PE and 1%
other plastics. The primary material in the reusable gowns is "Gore Surgical Barrier", which is a membrane based on polytetrafluorethylene (PTFE) from DuPont (Teflon).
This material also contributes to the reusable gowns' impact on ozone depletion. The LCA study of surgical gowns assessed fewer environmental factors than the British LCA
study of diapers, focusing on the factors: effect on the climate, depletion of stratospheric ozone, acidification, eutrophication and photochemical ozone formation. The study does
not seek to examine factors such as chemicals and biodiversity. In the years since 2003, there has been a growing concern about hormone-disruptive effects from the use of
fluorinated substances, which could mean that surgical gowns with a fluorinated coating would receive a different assessment today. Today's health sector uses large amounts of
disposable gowns and other protection, and Nordic Ecolabelling therefore believes it is important to set sound requirements concerning the manufacture of this type of
disposable product. Other, more recent life cycle analyses show that reusable products have a lower environmental impact than disposable products. One of these is the US
study "Life Cycle Assessments Of Single Versus Multiple Use Surgical Gowns"16, in which reusable polyester (PET) surgical gowns washed 50 times were compared with
equivalent disposable polypropylene (PP) products. The article shows that the disposable products were widely introduced due to concerns regarding blood-borne diseases such as
Hepatitis and HIV/AIDS. A degree thesis17 from Karlstad University in Sweden shows that the energy consumption for washable cotton/polyester bed linen is lower than for
disposable viscose products (Tencel) and negligibly less than for disposable polypro-pylene products. Both disposable products were laminated with a thin biofilm.
The US website "Sustainability Roadmap for Hospitals"18, run by the American Hospital Association, recommends using reusable medical textiles because they provide less waste,
lower costs and better patient comfort, and they are generally a better environmental option than disposable products in the health service. Nordic Ecolabelling is nevertheless
open to labelling disposable products in the hygiene sector, in order to promote the best disposable products where these are the preferred choice. Reusable textile products can
disposable nappies in Australia. 2009.
http://s3.amazonaws.com/zanran_storage/www.crdc.com.au/ContentPages/44777470.pdf (20. juli 2015) 15 Eriksson, E og Berg, H: " Livscykelanalys av operationsrockar", CIT Ekologik Ab
Chalmers Industriteknik, En rapport på uppdrag av Westma, Göteborg 2003. 16 Van den Berghe, AJ and Zimmer, C. Life Cycle Assessments Of Single - Versus Multiple- Use surgical Gowns. Finnes på nbettsiden til Sustainability Roadmap for Hospitals
.http://www.sustainabilityroadmap.org/pims/pdfs/pim247_lifecycle_assessment_disposable_versus_reusable.pdf (hentet 22. juli 2015) 17 Strömner, F. Jämförande LCA av engångssängkläder och tvättbara sängkläder i sjukvården. Examensarbete ved
Karlstad Universistet, Fakulteten för hälsa, natur- och teknikvetenskap. 2014. http://kau.diva-portal.org/smash/record.jsf?pid=diva2%3A731948&dswid=-6427 (hentet 22. juli 2015) 18 Sustainability Roadmap for Hospitals. Choose reusable textiles.
http://www.sustainabilityroadmap.org/pims/247#.Va9X6LA4Gul (hentet 22. juli 2015)
023e_6_0_hearing_Background.docx 12 (93)
Nordic Ecolabelling
27 November 2015
Background document
already be Nordic Ecolabelled under the criteria for Nordic Ecolabelling of textiles, hides/skins and leather.
The large amount of waste associated with disposable products is also a major environ-mental problem. This is particularly the case if the products end up in the ocean. It is
estimated that regular diapers that end up in the ocean will take 450 years to break down, according to the website Miljøstatus (Environmental status), run by the Norwegian
authorities, which refers to the National Oceanic and Atmospheric Administration (NOAA)19.
Various compostable diaper products have been launched, but they have not achieved any great commercial success. Manufacturers currently have no steerability when it
comes to the waste management of their products, and most of the composting facilities in the Nordic region would rather not compost diapers for hygiene reasons. Diapers are
therefore sorted out by composting facilities and sent for incineration, even if they are made from compostable materials. There are also no recycling facilities for sanitary
products in the Nordic region. The alternative is thus incineration, with or without energy recovery, or landfill. In the Nordic countries, a high proportion of household
waste is incinerated. Of the two alternatives incineration and landfill, incineration accounted for 97% in Sweden, Denmark and Norway, while the figure was 63% in
Finland and 11% in Iceland in 2013, according to the statistical office of the European Union, Eurostat20.
A company called Knowaste21 in the UK has launched a technology for separating incontinence care products and diapers, and recycling both the paper and the plastic
materials. They sterilise the waste and remove all moisture before sorting. The plastic is pelleted and used in various products, while the fibre is washed, dried and processed
before being used as an additive in concrete, asphalt, building blocks and installation materials.
Although it is the waste management systems in each country that determine whether a compostable material real y can become composted, some manufacturers have
nevertheless expressed a desire to use compostable materials. One example of such a bioplastic is the polymer polylactide (Polylactic Acid, PLA), which is produced from
starch deriving from plants such as maize.
Biodegradability and compostability are among the most commonly named sales
parameters for bioplastics, and the degradation time for different types of bioplastic is reported at between 90 and 180 days, depending on thickness and quality22. According to
standard EN 13432, 90% of the material must break down within 180 days. However, not all types of bioplastic meet the requirements in the international standards for
biodegradability and compostability, EN13432 and ASTM D6400, while there are conventional plastics that in some cases are able to meet these standards23. Biogas plants
19 Miljødirektoratet. Forsøpling av havet. Miljøstaus. Publisert 21.01.2015. http://www.miljostatus.no/Tema/Hav-og-
kyst/Forsopling-av-havet/ (hentet 4. februar 2015) 20 Eurostat. Waste generated by households by year and waste category.
http://appsso.eurostat.ec.europa.eu/nui/submitViewTableAction.do (hentet 22. juli 2015) 21 Knowaste. Recycling Process. http://www.knowaste.com/ (13. april 2015) ämtat 22. April 2015) 23 FORCE Technology (som en del af innovationsnetværket PlastNet). Engangsartikler i bioplast i Danmark. Marked, egenskaber og miljø. December 2010.
023e_6_0_hearing_Background.docx 13 (93)
Nordic Ecolabelling
27 November 2015
Background document
can also have a problem with bio-based plastics. The poor degradation is due to the lack of oxygen in the digestion chamber, which means that the degradation does not function
in the way that the manufacturers of the material intended24. Due the conditions described above and the fact that most diapers in the Nordic region are sent for
incineration after use, no requirements have been set concerning compostability for Nordic Ecolabelled sanitary products. In addition, it is assumed that most other sanitary
products included in the product group share the same fate as diapers after use.
6.2 Material composition
Sanitary products are often complex and composed of many different materials. This
translates into a complex environmental impact. The greatest differences on the environmental front between the different manufacturers are due to the product's
composition and the manufacturer's choice of raw materials, such as fluff (cellulose pulp), tissue paper, polymers, cotton and SAP. According to the article "Evolution of
disposable baby diapers in Europe"25 from 2015, the average European diaper is based on four primary components. The top layer that is in direct contact with the body is
made from a permeable non-woven PP fabric. The next component is a layer that temporarily stores the urine and distributes it onwards to the absorbent layer. These
components are both made from fluff pulp and SAP. The outer layer has to hold the diaper together and prevent leakage. It may contain small micro-holes to allow air to pass
through. This layer is made from PE. In addition, a diaper contains a fastening system such as tape, plus elastic and dyes and print. The results of the study show a clear link
between the environmental impact of disposable diapers and the quantity of materials in the product. They also show that the weight reductions of recent years are probably due
to the improved performance of the materials, components and product layout. The clear link between the quantity of the various materials and the product's environmental
impact is also confirmed by other studies of sanitary products. Table 2 shows the material composition of average European diapers from the EU Ecolabel's study during
its development of criteria for absorbent hygiene products. The diapers have 37% fluff pulp, 31% SAP and 16% non-woven PP.
Few independent LCA studies of sanitary products have been published. The best known is the British study, mentioned above, which compared disposable diapers with reusable
diapers. It outlines the contribution of the different materials to the overall environ-mental impact of the diapers, and gives the following advice: "disposable nappy
manufacturers should focus on weight reduction and improvements in materials manufacturing; and reusable users should focus on reducing energy consumed in washing
and drying." 2012 saw the publication of a comparative study of Pampers diapers26. Two of Pampers' 2007 diaper models were compared with their newly developed 2010
versions. The study gives the same recommendation as the British diaper study: "designing more effective products and influencing behaviours in the supply chain are
the most impactful things that a corporation can do to achieve sustainable product development and enable more sustainable living." The study showed that the newly
developed versions of the diapers, which were lighter and also had different material
24 Mailkorrespondens med Carline Steinwig, Avfall Sverige (13 maj 2015). 25 Mauro Cordellaa et al. Evolution of disposable baby diapers in Europe: life cycle assessment of environmental
impacts and identification of key areas of improvement. Journal of Cleaner Production, Volume 95, 15 May 2015,
Pages 322–331. http://www.sciencedirect.com/science/article/pii/S0959652615001535 (20. juli 2015) 26 Weisbrod, Anne V. and Hoff, Gert Van. LCA-measured environmental improvements in Pampers® diapers. Int J
Life Cycle Assess (2012) 17:145–153. Published online with open access at Springerlink.com. 10 November 2011.
http://link.springer.com/article/10.1007%2Fs11367-011-0343-1#page-1 (hentet 14. April 2015)
023e_6_0_hearing_Background.docx 14 (93)
Nordic Ecolabelling
27 November 2015
Background document
composition, had a lower environmental impact from the use of non-renewable energy and emissions of greenhouse gases, as well as a few other indicators. The results suggest
that the reduction is associated with lower energy use due to lower material consumption, and is not directly related to the production process or the use of the products. The
lower environmental impact was also attributed to the reduced amount of waste. The more recent study "Evolution of disposable baby diapers in Europe"27 shows that
disposable diapers have achieved significant environmental improvements over the past few years by designing lighter products and introducing superabsorbents. The study also
indicates that these improvements could continue through careful selection of materials in the design phase, checks on health and environment risks and ensuring functionality
and performance requirements are met. More efficient use of resources is also important during manufacture, and there is a need for structural changes to waste systems if the
products are going to require special waste management. The article suggests that the results of the study could be used to support design work and ecolabelling of disposable
children's diapers in order to promote the production and use of products with a lower environmental impact. The study has also revealed a distinct lack of statistically
representative data for products on the market, something that is fundamental for eco-based benchmarking of the products. But as the report points out, it is important to take
a precautionary approach and not to make broad generalisations based on the results of individual studies.
In its preliminary report28 for the development of criteria for absorbent hygiene products, the EU Ecolabel describes various LCAs for several of the products defined as sanitary
products (children's diapers, sanitary towels, breast pads and tampons). The purpose was to identify the critical environmental impacts associated with these products. The EU
Ecolabel has conducted its own cradle-to-grave LCA focused on diapers, sanitary towels, tampons and breast pads. They sourced information on the composition of the products
from the available literature, while environmental data was taken from the LCA database GaBi. Once again, the conclusion is that the constituent materials in a children's diaper,
for example, account for the highest proportion of the environmental impact (see Table 1). The table shows the extent to which the materials are responsible for the environ-
mental impact of the various parameters in relation to the rest of the disposable diaper's life cycle. The other phases, such as transport, manufacture of the diaper, packaging and
the use phase, have less of an impact on the results in the life cycle analysis. The relative effects of the materials are similar for the other products that were assessed (sanitary
towels, tampons and breast pads). A study by Mauro Cordella et al from 2015 (Evolution of disposable baby diapers in Europe) gives similar results and also used GaBi (version
5). The authors of this study are from the same institutions as those that drew up the EU Ecolabel preliminary report and the study is thus probably an updated LCA based on the
same information, but focusing solely on children's diapers. The material composition is the same in both studies.
27 Mauro Cordella et al. Evolution of disposable baby diapers in Europe: life cycle assessment of environmental
impacts and identification of key areas of improvement. Journal of Cleaner Production, Volume 95, 15 May 2015, Pages 322–331. http://www.sciencedirect.com/science/article/pii/S0959652615001535 (20. juli 2015) 28 EU Ecolabel for Sanitary Products. Preliminary report_5th draft. March 2013.
http://susproc.jrc.ec.europa.eu/sanitaryproducts/whatsnew.html (hentet 15. april 2015)
023e_6_0_hearing_Background.docx 15 (93)
Nordic Ecolabelling
27 November 2015
Background document
Table 1. The table illustrates in percent that the overwhelming majority of the
environmental impact from children's diapers derives from the constituent
materials. The table is taken from the EU Ecolabel for Sanitary Products,
Preliminary report29 and Mauro Cordella et al (Evolution of disposable baby
diapers in Europ
Impact category
Environmental impact of constituent materials in
relation to product's whole life cycle in %
Data from EU Ecolabel
Data from Mauro Cordella
Abiotic Depletion Potential (ADP) (kg
Sb-Eq) Acidification Potential (AP) (kg SO2-Eq) 85
Eutrophication Potential (EP) (kg
PO43-Eq) Global Warming Potential (GWP) (kg
CO2-Eq) Photochemical Ozone Creation
Potential (POCP) (kg Ethene-Eq) Primary Energy Demand (renewable
and non-renewable) (MJ) Primary Energy Demand (renewables)
(MJ) Primary energy Demand (non-
Table 1 shows that the environmental impact of the materials is most significant in the
life cycle of sanitary products. Table 2 sets up a comparison of how the different materials contribute to this environmental impact. The table is taken from the same
report that came out of the criteria development for the EU Ecolabel. The contribution from the individual materials depends on the quantity used, so the weight of the different
materials is included in a separate column. The table illustrates how (split into different environmental parameters) and to what extent the individual materials have an environ-
The constituent materials that generate the greatest environmental impact are: fluff, SAP
and non-wovens. Elastics account for a substantial part of ADP and affect POCP. The main effect of LDPE (low density polyethylene) is on POCP.
Looking at the environmental parameter GWP, the table shows that fluff, SAP and non-wovens are the greatest contributors in this area. In terms of weight, non-wovens
account for less than half of the fluff weight. The correlation between weight of constituent material and contribution to GWP appears to vary for the different materials,
with PP having a higher GWP value per kilo of material. Comparing non-wovens with fluff, the table shows that although non-wovens amount to less than half the weight of
the fluff, non-wovens' contribution to the GWP value is not half the size. The study does not include indicators that assess health factors, for example from the chemicals used.
This is generally a weakness of life cycle analyses and work is underway to make improvements. This EU study and the British LCA study also do not appear to have
environmental indicators such as biodiversity and land sequestration.
29 EU Ecolabel for Sanitary Products. Preliminary report_5th draft. March 2013. Table 21, page 113.
http://susproc.jrc.ec.europa.eu/sanitaryproducts/whatsnew.html (hentet 15. april 2015)
023e_6_0_hearing_Background.docx 16 (93)
Nordic Ecolabelling
27 November 2015
Background document
Table 2. Relative contributions of single materials to the overall impacts due to
materials for a children's diaper. The table is taken from EU Ecolabel for Sanitary
Products, Preliminary report, tables 18 and 2330.
Material
Relative contributions of single materials to the overall impacts
due to materials for a children's diaper. For abbreviations, see
Total energy 56%
non-renewable 31%
Total energy 14%
non-renewable 23%
non-renewable 8%
PP non-woven
Total energy 16%
non-renewable 26%
Adhesives
non-renewable 5%
Elastics
non-renewable 8%
Other materials
(PP non-wovens)
non-renewable 2%
-Elastic back ear
-Frontal tape
-Various synthetic
polymers
Total
ADP 7.0E-08 kg Sb-eq
Total energy 4.3E+00
renewable 1.5E+00
non-renewable 2.8E+00
For sanitary towels, the EU Ecolabel has shown that fluff generally accounts for the
greatest environmental impact. In terms of weight, the fluff also makes up the largest proportion of a sanitary towel (approx. 66% of the total weight). It is also worth
mentioning that release paper has a significant impact on ADP (due to the silicone) and that non-wovens, PET, LDPE and adhesive affect GWP.
When it comes to tampons, cotton accounts for the largest environmental impact associated with the product, and the accompanying polypropylene applicator also has an
impact on several environmental parameters (ADP, AP, GWP, POCO, Primary Energy Demand non-renewable). Once again, cotton is the largest constituent material by weight
in the product (approx. 90% if the applicator is excluded). Cotton buds and cotton wadding are products that employ the same materials as tampons. Cotton buds may have
a shaft of wood, plastic or cardboard. Individual measurements of purchased products have shown that the weight of the shaft can be up to 2 or 3 times the weight of the
cotton in the products.
30 EU Ecolabel for Sanitary Products. Preliminary report_5th draft. March 2013. Table 18 and 23, page 111 and 115.
http://susproc.jrc.ec.europa.eu/sanitaryproducts/whatsnew.html (hentet 15. april 2015)
023e_6_0_hearing_Background.docx 17 (93)
Nordic Ecolabelling
27 November 2015
Background document
In breast pads, which are mostly fluff (approx. 78%) and SAP (approx. 19%), the greatest environmental impact at material level unsurprisingly comes from fluff (all environmental
parameters) and SAP (GWP and primary energy demand). The release paper, which is a very small part of the product (approx. 2 %) does, however, affect ADP31.
Disposable wash cloths may be made of various materials, such as viscose, non-woven fabric or polyether/polyurethane, which are included in this version. As such, wash
cloths made of viscose, polymer or combinations of materials, for example in non-woven products, may be Nordic Ecolabelled.
Other disposable products, such as disposable bed linen, mattress covers and draw sheets, surgical gowns and diaper liners, contain many of the same materials as diapers,
incontinence care products and sanitary towels. Mattress covers, for example, may be made from several layers of cellulose, non-woven fabric and a plastic coating. They may
also contain fluff pulp to increase absorption. Some products state that they have seams which are strong enough that the patients can be lifted and that they have edges treated
with paraffin to ensure against leakage. The plastic film, which stops moisture from permeating through the products, may be polyethylene (PE), for example, or a bio-based
plastic film. The products may be laminated with plastic glued in place (water-based dispersion adhesive or hotmelt adhesive), or the plastic film may be directly extruded
onto the product. Use of non-woven products has risen in recent years, particularly in the health sector, in place of cotton/polyester products. There are various ranges of
disposable bed linen on the market that are made from non-woven fabric with PP fibres, for example.
The British LCA study shows that one of the main causes of environmental impact in the manufacture of diapers, i.e. combining the materials to form the product, is the
generation of electricity. Today's production is a fully automated process, where the diapers are packed at the end of the conveyor belt. The fluff pulp used often undergoes
mechanical fluffing in the factory. It is assumed that the manufacturing process is similar for other sanitary products.
While the majority of sanitary products such as diapers, sanitary towels and incontinence care products are becoming thinner and lighter, there may be practical obstacles to
further weight reduction. One example is tampons, with a number of customers preferring an applicator tube, and it appears that use of this varies from country to
country. Tampax makes products with cardboard and plastic applicators32. Another factor for sanitary products is that products may need individual packaging so that
customers can carry one in their handbag, for example. Products are therefore sold with and without packaging around each individual item.
This revision for sanitary products has expanded the product group to also include plasters and other equipment used in the health sector. Generally, a plaster is made up of
an absorbment pad (wound pad/gauze) which is attached to a strip of tightly woven fabric, plastic or latex rubber, covered by an adhesive and plastic strip or silicone treated
paper ("liner"). Manufacturers of plasters must comply with the EU Medical Device Directive (93/42/EEC). An examination of the materials in plasters has shown that they
mainly comprise of: cotton, paper, viscose, polyamide, polypropylene, polyester and 31 EU Ecolabel for Sanitary Products. Preliminary report_5th draft. March 2013. Tabell 18, 23, 24, 25 och 26 samt text på sidan 107. http://susproc.jrc.ec.europa.eu/sanitaryproducts/whatsnew.html (hentet 15. april 2015) 32 Procter & Gamble. Tampax. How to insert a tampon. http://www.tampax.co.uk/en-gb/firsttampon/how-to-insert-
a-tampon (hentet 13. april 2015)
023e_6_0_hearing_Background.docx 18 (93)
Nordic Ecolabelling
27 November 2015
Background document
polyurethane. Plasters can also contain nano-silver and other antibacterial agents, or fluoride-based materials like Gore-tex. Nordic Ecolabelling believes it is unnecessary to
use both antibacterial agents and flouride-based materials and chemicals in "normal" sanitary products due to their damaging impacts on health and environment. A newer
type of material found in plasters is hydrocolloids, providing a gelled material which may be based on carboxymethylcellulose mixed with gelatin. The plaster then has a top layer
based on rubber and an adhesive layer beneath which attaches it to the body.
6.3 Environmental conditions for the individual
materials
The manufacturers of diapers, sanitary towels and panty-liners rarely produce the various material components in the products themselves. They buy in cellulose pulp, tissue
paper, cotton, non-woven, SAP, plastic film and so on from suppliers. Larger manufac-turers have good scope to set requirements for their suppliers, but this is more difficult
for smaller manufacturers. It is easier the more eco-aware players there are in the market. Many of the component/raw material producers are major global players. Below are brief
descriptions of the environmental impact from the individual materials. Some of these themes are described in more detail in section 7, where the background to the require-
ments set for the materials is outlined.
Cellulose pulp and paper
Sanitary products may include cellulose pulp (fluff pulp), paper (for example silicone
paper), and tissue paper (e.g. airlaid). From a life cycle perspective, energy consumption, chemical use, emissions to water and air, and forestry are the key areas of environmental
impact within paper manufacture. According to the aforementioned article by Cordella et al., 90% of fluff pulp is produced in the USA. According to the criteria for the Nordic
Ecolabelling of tissue paper (version 5.0), tissue paper for sanitary products can currently be manufactured using the conventional and airlaid technique. There is high potential for
environmental improvements in the production of cellulose pulp, since there are considerable opportunities to set requirements concerning the factory's emissions to air
and water, energy consumption and energy efficiency, chemical requirements and requirements concerning management of the forests from which the wood is sourced.
Nordic Ecolabelling has had criteria for paper since 1991, and the environmental impact from the production of cellulose pulp and paper is described in more detail in the
background document for the Nordic Ecolabelling of paper products33.
Airlaid is a technique where the paper is manufactured using air instead of water. Airlaid
typically comprises cellulose pulp and possibly a binder. Airlaid may also contain other materials, such as superabsorbents, in addition to the cellulose pulp and binder. It is
assumed that the greatest potential for environmental improvements lies more with the constituent materials used and less with the process of making the actual airlaid material,
although defibering of the pulp also requires energy.
Cotton
The cultivation and harvesting of cotton is associated with serious environmental and
health problems. This is largely due to the use of pesticides and other chemicals in
production, but other factors, such as water consumption, can also have a major impact
33 Nordisk Miljømerking. Bakgrund till Svanenmärkning av pappersprodukter – basmodul och kemikaliemodul version
2. 2011. http://www.svanen.se/Foretag/Kriterier/kriterie/Pappersmoduler/ (hentet 16. april 2015)
023e_6_0_hearing_Background.docx 19 (93)
Nordic Ecolabelling
27 November 2015
Background document
on the environment. The environmental and social consequences of using genetically modified cotton plants in conventional cultivation are also a much debated subject. The
environmental impact of cotton cultivation and processing, and the availability of organic cotton, is described in more detail in the background document for the Nordic
Ecolabelling of textiles, hides/skins and leather34, which dates from 2012.
Polymer materials and non-wovens
The environmental impact from the manufacture of superabsorbents and other polymer
materials, and the potential for improvement, is difficult to estimate, since there is only
very limited factory-specific data available. The EU Ecolabel's work on developing criteria for absorbent hygiene products revealed that SAP and polypropylene non-
wovens in disposable diapers have a significant impact on GWP. In other words, there is considerable relevance in setting requirements concerning these constituent materials.
According to EDANA, however, the majority of the contribution to GWP for non-wovens comes upstream from the actual material production35. This could mean that the
production of the polypropylene is largely responsible for the GWP impact in relation to the non-wovens in sanitary products.
Even if the majority of the environmental impact in the constituent materials lies upstream of production, there may be great potential for improvement in the
manufacturing process for non-wovens. Non-wovens are made from short fibres that form a "sheet" that is bound together mechanically (e.g. with needles or water jets), with
the help of adhesive or thermally after the addition of a binder that melts at high temperatures. The majority of the non-wovens used in sanitary products are made using
a technique called spunbond. Sometimes a method for binding together the fibres called point-bond hot calendering is also used. This is associated with high energy consumption
and high heat generation. "Spin finish" is added to the non-wovens during production. This is an organic chemical that prevents the build-up of static electricity, amongst other
things. As mentioned before, airlaid is a type of non-woven based on cellulose pulp.
Viscose used to be used much more widely in non-wovens. One reason why more PET
and PP is used today may be that modern production methods for non-wovens in PP and PET give the same cotton-like feel that the viscose products were known for, but
with material properties that provide greater development opportunities in terms of process technology. Neither the British LCA study nor the report from the EU Ecolabel
used environmental data from viscose production, but viscose may occur in tampons and other types of sanitary product. Nordic Ecolabelling has previously described the
environmental impact of viscose in the background document for the Nordic Ecolabelling of textiles36.
Polymers such as PET (polyethylene terephthalate) and the polyolefins PP (polypro-pylene) and PE (polyethylene), PUR (polyurethane) and polyether are currently made
primarily from fossil raw materials. Depending on the polymer type, there may be many stages in the production process that leads to the final monomer, and various additives
appear in the different polymers, depending on what the plastic is going to be used for. PlasticsEurope provides LCA information on the environmental impact from the
production of the various materials in Europe, but it only gives average figures for each 34 Nordisk miljømerking. Om Svanemerkete Tekstiler, skinn og lær. 2012. http://www.svanemerket.no/for-
bedrifter/sok-om-svanemerket/svanens-krav/tekstiler-skinn-og-lar/ (hentet 16. april 2015) 35 Mailkorrespondens med Pierre Conrath, EDANA, 2 juni 2015 36 Nordisk Miljømerking. Om Svanemerkete Tekstiler, skinn og lær. 2012. http://www.svanemerket.no/for-
bedrifter/sok-om-svanemerket/svanens-krav/tekstiler-skinn-og-lar/ (hentet 16. april 2015)
023e_6_0_hearing_Background.docx 20 (93)
Nordic Ecolabelling
27 November 2015
Background document
plastic type, with no factory-specific data. The EU also has a reference document showing the best available technology, but unfortunately the most recent document is
from 200737, and the data on which it is based is therefore older than the information from PlasticsEurope. It has been difficult for Nordic Ecolabelling to access factory-
specific data for the production of polymers, in contrast to the availability of information from the paper industry in the Nordic region, for example. Awareness of more eco-
friendly processes and raw materials has also gradually grown within the petrochemical industry, but due to a lack of available data, it remains difficult, from an environmental
perspective, to choose materials that come from the best production sites. The lack of data also makes it difficult to set good requirements concerning the production of
polymers for the various ecolabels. When developing its criteria in 2014, the EU Ecolabel attempted to set requirements concerning the production of polymers, but as it states in
the minutes from the last meeting "Moreover, it was highlighted that the possibilities to select more eco-friendly polymers and plastics are limited with the current set of
Viscose
Viscose is made from cellulose fibre of various kinds, mainly wood fibre, although
bamboo fibre has grown in popularity in recent years. The environmental impact comes
from the sourcing of the raw material (e.g. the management of the forests), the production of pure cellulose fibre and its subsequent processing into viscose fibre. The
materials are based on renewable raw materials, but various chemicals and energy are used during production, and there are emissions to both water and air. An LCA by
Utrecht University39 shows that the different viscose fibres produced by Lenzing (Viscose, Modal and Tencel) have a lower environmental impact – in terms of use of
non-renewable energy, greenhouse gas emissions, toxic impact, water consumption and land use – than other fibres made from cotton, PET and PP. The study also shows that
there are variations in the environmental parameters for the different viscose fibres. The study made use of factory-specific data for the viscose fibres, but data from available
literature was used for the other materials. Such comparisons say nothing about which parameters are easiest to influence, but Nordic Ecolabelling has long-standing experience
in setting requirements for viscose in its criteria for both textiles and sanitary products. The main focus of the requirements has been on the final part of the viscose fibre
production, and it is only in the most recent version of the textile criteria that requirements have been set all the way back to the management of the forests.
Biopolymers
There is considerable potential for environmental improvements if new techniques can
be found for producing biopolymers with equivalent properties to today's polymers of fossil origin. The problem, as it stands today, is that the biopolymers available on the
market may have worse properties than those of fossil origin, and many are first-generation biopolymers, leaving scope for major environmental improvements in the
production process.
37 EU Best Available Techniques Reference Document (BREFs). Reference Document on Best Available Techniques
in the Production of Polymers. August 2007. http://eippcb.jrc.ec.europa.eu/reference/ (hentet 1. juni 2015) 38 EU Ecolabel for Absorbent hygiene products. 2nd Ad-Hoc Working Group Meeting for the development of the EU
Ecolabel Criteria for absorbent hygiene products. Brussels, 24 April 2013. Minutes of the meeting.
http://susproc.jrc.ec.europa.eu/Absorbenthygieneproducts/whatsnew.html (hentet 23. juli 2015) 39 LIFE CYCLE ASSESSMENT OF MAN-MADE CELLULOSE FIBRES
Li Shen and Martin K. Patel: Life cycle assessment of man-made cellulose fibres. 2010.
http://dspace.library.uu.nl/handle/1874/203542 (hentet 1. juni 2015)
023e_6_0_hearing_Background.docx 21 (93)
Nordic Ecolabelling
27 November 2015
Background document
Biopolymers may be produced using biological systems, for example fermentation with microorganisms, or they may be chemically modified from biological source material.
One example is PLA (polylactate), which is polymerised from lactic acid monomers produced by fermenting carbohydrates from maize or wheat. Green PE is made from
ethylene produced from biological materials such as sugar cane, and is known as a "drop-in" biopolymer, with similar material properties to fossil PE.
One of the best-known bio-based plastic films is Mater-Bi from Novamont in Italy. This is a biodegradable thermoplastic made from natural components (such as maize starch
and vegetable oil derivatives) and from biodegradable synthetic polyester. The material is thus certified as biodegradable and compostable, but it is not 100% from renewable
A third alternative is the production of biopolymers from bio-naphtha instead of the
ordinary fossil-based naphtha. This is currently done by applying the mass balance approach, where part of the naphtha is replaced with bio-naphtha and the renewable
proportion in the end product is calculated based on a "book and claim" system.
Section 7.2.8 provides an in-depth review of biopolymers and the environmental impact
from their production.
Superabsorbent polymers (SAP)
Superabsorbent materials are hydrophilic polymer networks that can quickly absorb
liquids to many times their own mass. They can also retain this liquid under a certain
pressure and are therefore suitable for use in sanitary products such as diapers and sanitary towels. Today superabsorbents usually means the sodium salt of polyacryclic
acid, which is a superabsorbent polymer. It is under development in a host of variants, e.g. through modification of the chain or the addition of different side groups to give
new properties. A variant introduced by BASF is SAP with a calculated renewable content based on the mass balance approach. A bio-based superabsorbent, often called
bioSAP, is also in production, and that is based on starch. According to previous information from manufacturers of sanitary products, bioSAP has a lower absorption
capacity than SAP of fossil origin40. There is a great deal of research and development work underway in this area, and this is expected to result in a wider range of commercial
products offering better quality and environmental performance in the near future. SAP and its biological variant are described in more detail in section 7.2.8.
Other materials
Diapers also contain composite materials such as tape and elastic materials to hold the
diaper in place. In addition to non-woven fabric and adhesive, these composite components may contain polymer types other than those named above, such as elastane,
polystyrene and styrene ethylene butadiene styrene (SEBS) copolymers. Overall, these polymers account for a low proportion of the product (diaper).
Constituent substances named in the British diaper study, over and above the primary materials previously mentioned, are adhesive, calcium carbonate, tape, elastic and lotion.
There are tampons that have added lactic acid bacteria and diapers that have tea leaves to counteract rashes. Incontinence care products in particular may contain odour control
40 Nordisk Miljømerking. Høringssammenstilling for Svanemerking av hygieneprodukterf for høringsutkastet til
versjon 5.0. Forslag til NMN 13. februar 2008.
http://www.ecolabel.dk/kriteriedokumenter/023_5_H%C3%B8ringssammenstilling.pdf (16. august 2015)
023e_6_0_hearing_Background.docx 22 (93)
Nordic Ecolabelling
27 November 2015
Background document
substances, such as active carbon, zeolites, cyclodextrin, etc. According to a patent on the Procter & Gamble website, cyclodextrin may be a suitable matrix for fragrance, and the
fragrance will only become active when the cyclodextrin becomes damp. Cyclodextrin is a cyclical oligosaccharide which can be produced from starch. What is used in practice is
often a commercial secret.
Plasters can comprise many different material types, including renewables and non-
renewables, such as cotton, paper, viscose, polyamide, polypropylene, polyester and polyurethane/polyether foams.
Packaging
Diapers tend to come in primary packaging containing several products, with examples
of packaging material including PE and paperboard/cardboard. With other sanitary products such as tampons and sanitary towels, the products may also be individually
packaged before being contained in a single pack. Stretch wrap, wood and wire mesh are often used in the transport packaging.
The British LCA study states that diaper consumption over the 2.5 years that a baby may be in diapers adds up to 170 kg. A total of 230 kg materials are used to make the diapers,
while the primary packaging uses 7.43 kg PE and 5.8 kg paperboard. According to the article by Cordella et al. (Evolution of disposable baby diapers in Europe), packaging
makes a marginal contribution to the environmental impact in relation to its weight
6.4 Renewable versus fossil-based materials
Renewable materials contribute to sustainable development through reduced CO 2
emissions and reduced use of materials from fossil sources. However materials based on renewable raw materials are not automatically sustainable. There are several key problems
concerning the cultivation and production of the renewable materials, such as land use in competition with food production, use of genetically modified organisms and energy and
chemical use in the production processes. Although there is a general desire to switch from fossil raw materials to increased use of biomass, there is a debate in many quarters
about how quickly this transition can take place and which areas should be prioritised. In a number of areas, people have embraced many of the good properties of synthetic
materials, and for bio-based materials to compete, their properties have to match those of the synthetic materials.
Nordic Ecolabelling has long-standing experience in setting requirements concerning cultivation, forest management and the production of traditional renewable materials for
sanitary products such as fluff pulp, paper and cotton, and these requirements are aimed at limiting many of the negative environmental consequences of such products.
The production of bio-based plastic materials is, however, a recent development that is showing two main trends. One is the appearance of new types of plastic (such as PLA)
and the other is the use of renewable materials for the production of traditional plastic types such as polyethylene, known as drop-in bioplastics. In 2010, the dominant force
was first-generation renewable raw materials, which were raw materials produced on agricultural land, but raw materials are also under development based on forest raw
materials or waste products (such as bagasse from sugar production) and these are known as second-generation bio-based raw materials. In the development of the new
bio-based plastic types (such as PLA), a great deal of emphasis has been placed on
023e_6_0_hearing_Background.docx 23 (93)
Nordic Ecolabelling
27 November 2015
Background document
properties such as degradability. Bio-based polymers are described in more detail in section 7.5.6.
Nordic Ecolabelling wishes to contribute to the "green shift" through increased use of bio-based materials, but at the same time wishes to see sanitary products that offer
sufficient quality and performance in their areas of use. It therefore remains relevant to require only renewable materials in Nordic Ecolabelling sanitary products. Whatever the
origin of the raw materials, requirements need to be set for the production of the materials. When it comes to procuring the raw materials, it is paradoxical that it is easier
to set strict requirements for cultivation and forest management with regard to renewable raw materials than it is to set requirements for the extraction of fossil raw materials. One
of the reasons why it is so difficult to set requirements for the extraction of the fossil raw materials is the lack of traceability systems.
Nordic Ecolabelling also wishes to promote the use of recycled materials. For the majority of the materials, material recovery would require fewer resources than
extraction/cultivation and production of new materials. It would also lead to the processing of used materials, so that they do not end up as waste. However, the use of
recycled material may also carry risks such as the spread of substances harmful to health and the environment, which may have been used in the original manufacturing process.
It is therefore important that this risk is assessed and that requirements are drawn up with regard to recycled materials.
6.5 Relevance, Potential and Steerability
Nordic Ecolabelling uses an analysis tool called the RPS model, where RPS stands for
Relevance, Potential and Steerability. The purpose of this model is to identify which
environmental problems are most relevant in the life cycle of the products and to assess the potential for reducing negative environmental impacts within these specific areas. In
addition, it is important to consider how the manufacturers in particular can influence the products in order to release this potential for environmental improvement. This is set out
in the ISO standard that the Nordic Ecolabel, as a type 1 ecolabel, follows (ISO 14 024). The standard states that the requirements must be product-specific and that they must
enable the best environmental products in the area to be ecolabelled. The Nordic Ecolabel is also a multi criteria-based labelling scheme, which means that it sets
requirements within several environmental parameters, in contrast to a label such as the Carbon Footprint, which focuses exclusively on one parameter. Another area that needs
to be assessed is how the requirements should be documented. The ecolabel should set requirements that can be documented and the main requirements can thus not be
environmental management requirements. Finally, the burden of documentation must also be assessed in relation to the environmental effect of the requirements set.
The previous sections describe which raw materials commonly occur in sanitary products, and the fact that environmental problems are caused by both the manufacture
of the products and the large quantity of waste generated. While the ecolabel cannot control whether consumers and purchasers choose disposable products, or how the
products are processed as waste, there is considerable potential for improving the products by setting requirements for the production phase.
It has been shown that much of the environmental impact from disposable sanitary products comes from the production of the constituent materials. This applies in
particular to those used as primary materials, but also materials that have a larger carbon
023e_6_0_hearing_Background.docx 24 (93)
Nordic Ecolabelling
27 November 2015
Background document
footprint per kilo, for example, than other materials since they are more energy-intensive to produce. It is therefore relevant to set requirements concerning the substances used as
raw materials in the manufacture of sanitary products. The same is true for any chemical products that may be used.
Nordic Ecolabelling has long-standing experience in setting material requirements for sanitary products and in other criteria for Nordic Ecolabelled products, and knows that
there is potential for environmental improvement in this area. This applies for materials such as cellulose pulp, cotton, viscose and polymers. Nordic Ecolabelling also knows
from experience that manufacturers are able to impose requirements on their suppliers and choose the best materials within each material type, so that both the raw materials
and the production conditions are among the best they can be. One way of reducing the impact on the climate is to use materials from renewable sources, assuming that the
production of such materials does not generate greater greenhouse gas emissions than for materials from non-renewable sources.
Another method of reducing the environmental impact of the materials in the product may be to use recycled materials. One of the problems with this is the risk of environ-
mental toxin migration, which can occur in recycled materials. Good enough systems are not yet in place to ensure that recycled materials do not contain chemicals that are
harmful to health and the environment. Nordic Ecolabelling is not aware of any recycled cellulose pulp being used in sanitary products. The most relevant recycled materials
would be paper and paperboard, but there is currently a shortage of recycled paper in the Nordic region. Since sanitary products come into close contact with the body and many
of the products are intended for young children, the use of recycled materials in the Nordic Ecolabelled products is prohibited. However, Nordic Ecolabelling wishes to
promote the use of recycled materials in the packaging and in the release paper that is removed from the products before use, and thus does not come into contact with the
The environmental impact of sanitary products can also be reduced through the
manufacturers focusing on a reduction in the weight of the end product, and on optimising the material composition of the products. The latter area is, however, difficult
for Nordic Ecolabelling to influence, because even small changes in the product composition can change the function or other properties of the products which
consumers appreciate. The products that fall under the umbrella of absorbent, protective and removing sanitary products vary greatly and can have extremely complex material
combinations, something which also makes it difficult to set general requirements concerning the composition of the products in order to reduce the use of the more
environmentally problematic materials. In RPS terms, there is low steerability in this area, despite there being relevant environmental problems and potential for environmental
Part of the environmental impact comes from the handling of the products in the waste
phase, but this is another area of low steerability, since it is difficult for Nordic Ecolabelling to influence how consumers handle the products after use. Nordic
Ecolabelling also has little influence over municipal waste management systems.
In this revision, Nordic Ecolabelling has continued to set detailed requirements
concerning the constituent materials and chemicals used in the manufacture of sanitary products. Version 5 of the criteria set a requirement to ensure that the product has either
a high proportion of renewable materials, a certain proportion of biopolymers among the
023e_6_0_hearing_Background.docx 25 (93)
Nordic Ecolabelling
27 November 2015
Background document
plastic materials or limited CO emissions calculated as GWP (Global Warming
Potential). The options in the requirement have been removed, and the requirement is
now that there must be a proportion of renewable and/or recycled material in the product or the packaging. The EU Ecolabel also came to the conclusion, in developing
its criteria for absorbent hygiene products in 2014, that it is not possible to set requirements concerning the product's total GWP, due to a lack of both the data and the
methodology for this41.
Justification of the requirements
This section describes in more detail the individual requirements and the background to
these. Detailed requirements have been set concerning the production of the constituent materials in the product and the chemical substances added during the manufacture of
the sanitary products, from both a health and an environmental perspective. It is also made clear whether the requirements have been changed since the previous revision. In
the text, the new requirements are shown before the background text explaining them.
7.1 Product group definition
The purpose of the product group definition (see section 2.1) is to focus on the types of
disposable products that can be found either in private bathrooms or in a more public environment such as a care institution. In other words, it excludes tablecloths, for
example, which are more likely to be found in other places. To clarify which disposable products are included within the definition, it focuses on the type of function that the
product has (absorbent, protective and removing). The definition also makes it clear what is being absorbed, protected or removed (bodily fluids and faecal matter, or cosmetics).
Products that have a similar function but a different purpose are excluded. An example of this can be found in the distinction between wash cloths and dry wipes. The products
can be assumed to have the same size and material composition. However, it can be reasonably assumed that wipes are intended for cleansing of both bodily fluids and faecal
matter, and cosmetics. Dry wipes, which could be used to wipe away the same matter, could also be used to clean a counter. In theory, they could also be cut into larger sizes to
serve as a paper towel. The function of the towel is certainly to absorb, but it is most likely to be water that is absorbed. The line between what should and should not be
included is clearly a fine one, but it has to be drawn somewhere. Therefore wash cloths (not those made only of paper) are included in the product group definition, but not dry
wipes. The reason that serviettes are not included in the product group definition is that they are mainly intended to wipe away something else (food). The same is true of bibs,
since they are meant to protect against something other than the matter referred to in the definition.
7.1.1 Sanitary products included in the definition
A number of products have been added to the sixth generation of the criteria – plasters,
compresses, cotton wool, surgical wear (clothing/gowns, surgical masks and caps) and
exam table paper. This means that disposable materials used in dental practices (for example the protective sheet placed on the chest during examinations and the cotton
wool that looks like a tampon) can also be Nordic Ecolabelled. In 2014 viscose massage
41 EU Ecolabel for absorbent hygiene products. 2nd Ad-Hoc Working Group Meeting for the development of the EU
Ecolabel Criteria for absorbent hygiene products. Brussels, 24 April 2013. Minutes of the meeting.
http://susproc.jrc.ec.europa.eu/Absorbenthygieneproducts/whatsnew.html (hentet 23. juli 2015)
023e_6_0_hearing_Background.docx 26 (93)
Nordic Ecolabelling
27 November 2015
Background document
table paper was included following an interpretation review by the licensing managers at Nordic Ecolabelling. In the new product group definition, it is proposed that massage
table paper (which is readily associated with a spa) is replaced with exam table paper (which belongs more in a healthcare context) and that this underlay may be made from
any of the materials addressed in the criteria document.
Disposable wash cloths that are not made of paper were included in version 5 of the
criteria. That version did not set any requirements concerning polyurethane/polyester, but the new version does. As such, wash cloths made of viscose, various polymers (e.g.
PET, PP, PET and PUR) or combinations of materials, for example in non-woven products, may be Nordic Ecolabelled.
7.1.2 Products not included in the definition
The judgment of whether a new product should or should not be included in the criteria
for sanitary products is not based exclusively on the product group definition. Nordic Ecolabelling looks at products from a life cycle perspective and in making its judgment,
must also consider the status of what could be called the product type. In this context, product type is a broader definition than the design and material composition of the
disposable product. There may be different variants of the product within a particular product type. Such variants may be disposable/reusable, being made of entirely different
materials (perhaps cotton or paper) or availability in different sizes. The argument that a particular product has the same material composition as other products that are already
included is not sufficient for the inclusion of the product in question. The reason why product type is prioritised over product is that it should be environmentally better to
manufacture the individual product with an entirely different material composition than the intended product has (compare the material composition of a reusable towel with an
equivalent disposable product of another material). It is also important to assess whether there are other performance and quality requirements that the new products should meet,
or whether the product could already be Nordic Ecolabelled in accordance with other criteria documents.
Disposable paper towels made from cellulose fibre combined with other material types (plastic, airlaid, etc), which can thus be ecolabelled under the criteria for tissue paper,
cannot be ecolabelled under the criteria for sanitary products. This also applies to products such as serviettes, tablecloths and so on which comprise combined materials.
Products with added cosmetics, medication/medicines, disinfecting substances and similar cannot be ecolabelled in this product group, since no requirements have been set
or environmental assessments conducted for cosmetics or medical additives for this product group. Packaging also cannot be ecolabelled as an independent product.
Nordic Ecolabelling has developed ecolabelling criteria for over 60 different products and services, and while it may appear that a product could be ecolabelled under several
criteria, it is Nordic Ecolabelling that determines which criteria document the product is covered by. Examples of products that may not be Nordic Ecolabelled under the sanitary
products criteria, but may be under other criteria:
Wet wipes can be ecolabelled under the criteria for the Nordic Ecolabelling of
cosmetic products.
023e_6_0_hearing_Background.docx 27 (93)
Nordic Ecolabelling
27 November 2015
Background document
Dry wipes, serviettes and paper wash cloths can be ecolabelled under the criteria
for the Nordic Ecolabelling of tissue paper.
Reusable wash cloths, textile diapers and mesh pants can be ecolabelled under the
criteria for the Nordic Ecolabelling of textiles, hide/skins and leather, or the EU Ecolabel criteria for textile products.
Microfibre cloths can be ecolabelled under the criteria for the Nordic
Ecolabelling of supplies for microfibre based cleaning.
Disposable gloves and toothpicks cannot be ecolabelled under the criteria for
sanitary products. Disposable gloves were assessed previously, but because they can be made from many different materials for which there are no requirements in the criteria, and because many people can be allergic to substances such as latex (usually due to a protein in latex), disposable gloves are not included in the product group. Disposable gloves are also not usually absorbent products, although they can protect against bodily fluids. Other materials used in disposable gloves are vinyl and nitrile rubber. The reason that toothpicks are not included is that their function does not match the product group definition. Toothpicks were included in version 5 of the criteria, but no licence has been issued for this type of product. Nordic Ecolabelling will consider whether toothpicks may be granted a licence under the criteria for disposables for food.
7.2 Environmental requirements in general
There are detailed requirements for the production of the constituent materials and the
chemical substances used within the sanitary products as well as for any additional components and the primary packaging. The requirements are based upon both health
and environmental perspectives. Generally speaking, most of the materials are subject to some obligatory requirement, and the levels in the requirements change in relation to the
weight percentage of the material used in the final product. The weight % of a specific material is related to the total weight of the materials in the sanitary products and in the
additional components in a pack. To make it clear the definitions below are used. Chapter 9 "Definitions and Abbreviations" contains an extended list of terms, definitions
and abbreviations.
Definitions
Sanitary products: refers to the product used, i.e. excluding additional
components, information sheets and primary packaging. S = the weight of the materials in the sanitary product.
Additional component: Components belonging to the hygiene product that are
removed before use of the product. Examples include release paper, a plastic film around a tampon, a sanitary towel or an applicator for tampons. A = the weight of the materials in the additional components.
Primary packaging: The packaging around the sanitary products and additional
components as sold in retail outlets or directly to the customer. Primary packaging does not include transport packaging. P = the weight of the materials in the primary packaging.
023e_6_0_hearing_Background.docx 28 (93)
Nordic Ecolabelling
27 November 2015
Background document
Material: For example material types like: fluff pulp, PP, PE, PET, SAP, paper,
viscose and cotton. A material type can be used in more than one component.
Component: Part made out of one or several materials and chemical products
that together fulfil a desirable function. For example: a layer of non-woven, an outer barrier film or an absorbent core of fluff pulp and super absorbents.
The weight of the individual material in the sanitary products and in the additional
components is further in the document referred to as (S+A). The weight % of a specific material can thus refer to this amount as:
The weight % of a specific material = (m + m )/(S+A)
m = the weight of the specific material in the sanitary product
m = the weight of the specific material in the additional component
S = the weight of the materials in the sanitary product
A = the weight of the materials in the additional components.
In addition to the different requirements for the materials used, Nordic Ecolabelling
wishes to promote the use of materials based on renewable and recovered sources, see requirement O36.
If there are several inputs which contain the same type of material, these must be added together. E.g. cellulose pulp or polyethylene (PE) from multiple suppliers must be
summarised. An exception to this is if the material type is already found in parts that require different production processes like fibre, film or foam. Examples of this can be
polypropylen (PP) or polyethylene terephthalate (PET). However, if the PP fibres use different non-woven materials, then the amount of PP fibres must be added together and
all the PP fibres need to fulfil the requirement. PUR foams and thermoplastic polyurethane are regarded as different types of materials. If a polymer/plastic contained
in four or more components reaches the weight limits, the requirement only needs to be met by a minimum of 50.0 % of weight of the material. This is an easing of demands to
reduce amount of documentation and difficulty in gathering information from many subcontractors.
Constituent materials that are already Nordic Ecolabelled, such as various textile fibres or paper, do not require any additional documentation. As described in O2, sanitary
products may contain a maximum of 5.0 % by weight of materials and additives for which no requirements have been set, but only 2.0 % of each material type.
As shown in table 3, the material requirements are divided into different levels of stringency, depending on how much of the individual materials are included. Generally
speaking, most of the materials are subject to some obligatory requirement, and the levels in the requirements change if the materials account for more than 5.0, 10.0 or 20.0 % per
weight. The background to this is that different hygiene products have very different compositions, and may comprise a single material, as with wash cloths, or many different
materials, as with diapers. It was decided to introduce these levels, to reduce the burden of documentation when the sanitary product is composed of many different materials.
Table 4 below provides a guiding overview of which requirements the different material types have to fulfil. The list is a guide and if there is any discrepancy with the texts in the
requirements, it is the O-requirements that apply. The environmental requirements are
023e_6_0_hearing_Background.docx 29 (93)
Nordic Ecolabelling
27 November 2015
Background document
described in more detail in the sections on chemical requirements, material requirements and performance requirements for the products (sections 7.4, 7.5 and 7.6). The table also
describes what requirement applies and who will document the requirement.
Table 3. Overview of the limits for the different level of requirements, depending
on the percentace of the specific materials included. The weight % for specific
materials is related to the total weight of the materials in the sanitary products
and in the additional components in a pack (S+A).
Material
> 1.0 weight % > 5.0 weight % > 10.0 weight
> 20 weight %
pulp/air-laid
Paper/paperboard/
cardboard
Wood materials
Table 4: Guiding overview of the requirements.
Requirement Material
Comments
document?
The manufacturer of
the sanitary product
The manufacturer of
the sanitary product
Requirements to classified
The producer of the
chemical products, CMR-
chemical product
substances and other
excludes substances
Applies to silicone added to
The producer of the
other materials or silicone for
product for silicone
The producer of the
The manufacturer of
the sanitary product
Odour control substances are
The manufacturer of
permitted only in incontinence the sanitary product
care products, and must fulfil
and the chemical
Prohibited with exemption of
The manufacturer of
lactic acid bacteria
the sanitary product
Applies to dying and printing
Manufacturer/Supplier
on the sanitary product
of the dyes and inks
Mandatory requirement
The pulp/airlaid
Additional requirement when
The pulp/air-laid
10.0 % by weight or more
Applies for tissue, printing and The paper
023e_6_0_hearing_Background.docx 30 (93)
Nordic Ecolabelling
27 November 2015
Background document
Requirement Material
Comments
document?
silicone paper, carton,
cardboard and other paper.
Additional requirement when
10.0 % by weight or more
Wood material Mandatory
The supplier of the
Mandatory, bleaching with Cl2
The supplier of the
Additional requirement when
The supplier of the
10.0 % by weight or more
Mandatory, bleaching with Cl2
The manufacturer of
prohibited and AOX limitation
Additional requirement when
5.0 % by weight or more
requirement when 10
% by weight or more
PVC (halogenated polymers)
The manufacturer of
prohibited in product and
the sanitary/plastic
Part A: Requirements to
The manufacturer of
chemical substances in PE,
the plastic product or
PP, PS, PET, PA, PUR
test by the producer
(included elastan)
of the component
Part B: when 20.0 % by
weight or more requirements
for added chemicals
When 5.0 % by weight or
The manufacturer of
more elastan/PUR: Production
the plastic/polymer
When 5.0 % by weight or
The manufacturer of
more PA: Production
the plastic/polymer
When 5.0 % by weight or
The polymer producer
more for fossil based
polymers: Energy
requirements for
polymerisation of PE, PP, PS,
When 5.0 % by weight or
The polymer producer
more for bio-based polymers:
Energy requirements for
When 20.0 % by weight or
The polymer producer
more for renewable raw
materials polymers:
Requirements to origin and
Mandatory requirement for
The producer of the
recycled plastic
recycled plastic
Mandatory requirement
The producer of the
Additional requirement when
The producer of the
5.0 % by weight or more
Additional requirement when
The producer of the
20.0 % by weight or more:
Requirements to origin and
Refers to the relevant material See relevant
023e_6_0_hearing_Background.docx 31 (93)
Nordic Ecolabelling
27 November 2015
Background document
Requirement Material
Comments
document?
and chemical requirements
Applies to product and
The manufacturer of
the sanitary product
Like cotton shafts material,
tape, elastic/rubber band etc.
Refers to relevant
Refers to relevant
The manufacturer of
the sanitary product,
see also relevant
May each make up a
maximum of 2.0 % by weight
of but not exceed 5.0 % by
weight. For example latex,
rubber, silicone and silk
The manufacturer of
the sanitary product
The manufacturer of
the sanitary product
Information on Applies to size designations
The manufacturer of
and that relevant products
the sanitary product
must not be discarded in the
The manufacturer of
the sanitary product
7.3 Description of the product (O1-O2)
Requirements O1 and O2 are intended to provide a description of the product and the
packaging, plus a statement of the percentage composition.
Description of the product
The applicant must provide a description of the product with a technical description of
the manufacture as well as information about packet sizes. The following information
on all components of the sanitary product, any additional components, product
information sheets and primary packaging must be provided: Function (as outer foil around each product, information sheet, primary packaging
Weight Constituent materials Chemical products that are added the sanitary product (with safety data sheets or
Supplier/producer (with the components or the production processes they perform,
business name, country of production and contact person)
The production chain with suppliers back to the material manufacturers (to the stage
where there requirements are) for the sanitary product and additional components
must be illustrated by i.e a flowchart.
023e_6_0_hearing_Background.docx 32 (93)
Nordic Ecolabelling
27 November 2015
Background document
Description in accordance with the requirement.
Material composition
Composition
The specific material types in the sanitary product and additional components must be
stated in terms of percentage by weight of (S+A). Also the specific material types in the primary packaging must be stated in terms of percentage by weight of (S+A). The same material type included in more than one component shall be summed up.
Nominal limit
Specific material types present in quantities of maximum 1.0 % by weight of (S+A) is
exempted from the material requirements, even if there is a requirement for the
particular material type in the document. Materials for which no requirements are imposed in the document, and which are not
explicitly prohibited, may each make up a maximum of 2.0 % by weight of (S+A), but
not exceed 5,0 % by weight totally. All chemicals added during the manufacturing of sanitary product must meet the
chemical requirements in Chapter 2.1.
Ecolabelled materials
Constituent materials/components with Nordic Ecolabel or EU Ecolabel added in the
sanitary product and additional components are exempted from further material
requirements.
Recycled materials
Recycled materials may not be used in the sanitary product, with exception of plastic
materials recycled in a closed loop system and meeting requirements for recycled
plastics materials and articles intended to come into contact with foods. For more
information, see requirement O30. Recycled materials can be used in additional
components, information sheets and primary packaging.
Description in accordance with the requirement. See Appendix 1 for template. Form 15
for non-woven materials may also be used. For materials/components marked with
Nordic Ecolabel or EU Ecolabel are includes shall licence number/standard contract number be included.
Background to the requirements O1-O2
The requirements O1 and O2 have been set to provide an overview of the product and the packaging for which a licence is being sought. This will make it easier to determine
which requirements have to be fulfilled for the raw materials.
Recycled materials must not be used in the sanitary products themselves, since these
products come into close contact with the body and many of the products are intended for young children. An exception is plastic materials recycled in a closed loop system and
meeting requirements for recycled plastics materials and articles intended to come into contact with foods. Recycled material can contain impurities that are undesirable in
sanitary products. Recycled materials are permitted in the packaging and in components that are removed from the products before use and thus do not come into contact with
the user, for example release paper, but with restrictions regarding chemical substances in for example recycled plastic.
For a Nordic Ecolabelled sanitary product, 100 % of the contents must be stated, and 95 % by weight of the materials, components and constituent substances in the sanitary
product and the additional components must meet the requirements set in the criteria document. This means that 5.0 % may consist of materials with no requirements, with a
023e_6_0_hearing_Background.docx 33 (93)
Nordic Ecolabelling
27 November 2015
Background document
maximum of 2.0 % by weight of each material type. This may be materials such as silk, rubber, latex, silicone and so on. Similarly, the composition of primary packaging must
be specified so it later in the document becomes clear which requirements apply for the various materials. As a basis for calculating the weight %, is chosen the sum of the
materials in the sanitary product and additional components belonging to each product. That is, what it takes for the product to be used. This sum is termed (H + T). It is
equivalent if it is calculated for all the products in the package or calculated per unit in the package.
Small parts of the sanitary product or additional components can be made of material types which requirements are imposed on in the document. One example is sewing
thread that may be made from cotton or polyester, where there may be several stages back in manufacturing chain, making it difficult to find sufficient documentation for such
a small component. Therefore, a nominal limit is introduced for every material of 1.0 % by weight. Chemical products used in the manufacture of sanitary products must always
meet the chemical requirements.
It's said in O2 that products with the Nordic Swan or EU Ecolabel included in the
sanitary product or additional components need not meet further material requirements. This may apply, for example, to viscose and other textile fibres, various kinds of paper
In contrast to previous versions of the criteria, the weight of the product and the
packaging must now also be stated.
7.4 Requirements for chemical products and
chemical substances
The chemical requirements are split into three sections: general chemical requirements, other chemical requirements and requirements regarding dyes and printing inks.
The general chemical requirements O3, O4 and O5 apply for all chemical products added during the manufacture/composition of the sanitary products and additional
components. The requirements apply to adhesives, odour control substances (only for incontinence care products), dyes and so on. These requirements are also to be consulted
for chemical products and additives used in materials/fibre used in the sanitary products. The reference to these requirements for such products appears in the material
requirements later in the document.
The section on other chemicals (O6 to 010) sets requirements concerning silicone
treatment and adhesives, prohibits the addition of fragrances, skincare substances and medication, and limits the use of odour control substances. The third section deals with
chemicals for printing and dyeing (O11 and O12).
What counts as a constituent substance?
Requirements O4 and O5 use the term "constituent substances". The following
definitions are given:
1. For chemical substances, unless otherwise stated, the constituent substances are
all substances in the product, including additives (i.e. preservatives or stabilisers) in the raw materials, but not impurities from the raw material production.
023e_6_0_hearing_Background.docx 34 (93)
Nordic Ecolabelling
27 November 2015
Background document
2. For chemical substances in materials, requirements are set for constituent
substances where these are added by the material/fibre producer or their supplier
(actively added), but not impurities from the production of the additive or its raw material production. The requirements for each material set out whether there are
requirements concerning chemical substances in the materials and state when to refer back to requirements O4 and O5.
Impurities are defined as residual products from the ingredient production that can be found in the final chemical product in concentrations below 100 ppm (0.01% by weight,
100 mg/kg), but not substances added to an ingredient or product deliberately and with a purpose, regardless of amount. However, impurities at the raw material level at concen-
trations of over 1.0% of the raw material will be regarded as a constituent substance. Substances known to be degradation products of the constituent substances are also
themselves considered to be constituent substances. The declaration concerning constituent substances is made by the chemical producer using the knowledge it
possesses at the time in question, based on information from the raw material producer/supplier, the formulation and available knowledge of the chemical product.
Reservations are made for developments and new knowledge. Should such new knowledge arise, the undersigned is obliged to submit an updated declaration to Nordic
Some materials are subject to requirements concerning residues that have not been
actively added. These may, for example, be residues of monomers or catalysts in polymerisation such as D4 and D5 in silicone, antimony in polyester or residues of
crosslinkers or monomers in SAP. The limitations on these substances are explained in the requirements for the relevant materials.
7.4.1 General chemical requirements
Chemical products, classification
Chemical products used in the production/composition of sanitary products and
additional components or added materials where it later in the document is referred to
this requirement, must not be subject to a classification requirement specified in Table
2
Table 2: Classification of chemical products
Classification under CLP Regulation (EC) No 1272/2008
Toxic to aquatic organisms
Aquatic chronic 1-4
H410, H411, H412, H413
H330, H310, H300
H331, H301, H311
H332, H312, H302
Specific target organ toxicity
Aspiration hazard
Causes serious eye damage or eye
023e_6_0_hearing_Background.docx 35 (93)
Nordic Ecolabelling
27 November 2015
Background document
Eye Dam. 1 Allergenic
Toxic for reproduction
*Classification in line with the Regulation on classification, labelling and packaging of substances and mixtures
(Regulation (EC) no 1272/2008). The producers of the chemical products are responsible for the classification.
Product data sheets for all chemical products in accordance with current European
legislation. Duly completed and signed Appendix 1, form 2, Declaration of chemical products, in
the criteria document. To be completed by the producer of the chemical product.
Chemical substances, CMR
The chemical products must not contain substances that are or may degrade into
substances that are classified as carcinogenic (Carc), mutagenic (Mut) and/or toxic for
reproduction (Rep) according to CLP Regulation (EC) No 1272/2008 (see Table 3). This requirement applies to chemical products used in production/composition of
sanitary products and additional components, or added to material, where reference is
made to this requirement (O4) later in the document.
Table 3: Classification of CMR substances
Classification in line with CLP Regulation (EC) No
1272/2008
Hazard class and category
H phrases (Code)
Toxic for reproduction
Duly completed and signed Appendix 1, form 2, Declaration of chemical products, in the criteria document. To be completed by the producer of the chemical product.
Other excluded substances
Chemical products used in the production/composition of sanitary products and
additional components or added to material, where reference is made to this
requirement later in the document, must not contain substances from the list below. Substances on the Candidate List*
023e_6_0_hearing_Background.docx 36 (93)
Nordic Ecolabelling
27 November 2015
Background document
Substances that have been judged in the EU to be PBT (Persistent, Bioaccumulative
and Toxic) or vPvB (very Persistent and very Bioaccumulative)**
Substances considered to be potential endocrine disruptors in category 1 or 2 on the
EU's priority list of substances that are to be investigated further for endocrine
disruptive effects***
In addition, the following individual substances and substance groups are prohibited or
restricted. There may be overlap between the substances listed below and substances
categorized over. Organotin compounds Phthalates APEO – alkylphenol ethoxylates and alkylphenol derivatives (substances that
release alkylphenols on degradation)
Halogenated organic compounds. Preservatives are exempt, and so are colourants
that meet the EU's requirements concerning colourants in food packaging under
point 2.5 of Resolution AP (89)
Preservatives that are not bioaccumulative in accordance with Appendix 2 (BCF <
500 / logKow < 4). The mixture CMIT + MIT (3: 1) may be present in quantities no more than 15 ppm. CMIT is 5-chloro-2-methyl-2H-isothiazol-3-one (CAS no.
26172-55-4) and MIT is 2-methyl-2H-isothiazol-3-one (CAS no. 2682-20 -4)
Antibacterial agents (e.g. nanosilver and triclosan)**** Flame retardants Additives based on lead, cadmium, chromium VI and mercury, or their compounds *The Candidate List can be found on the ECHA website: http://echa.europa.eu/candidate-list-table * PBT and vPvB in accordance with the criteria in Annex XIII of REACH ** Substances considered to be potential endocrine disruptors in category 1 or 2, see following link:
http://ec.europa.eu/environment/chemicals/endocrine/strategy/being_en.htm ****An antibacterial agent is a chemical that inhibits or stops growth of microorganisms such as bacteria, fungi or protozoa (single-celled organisms)
Duly completed and signed Appendix 1, form 2, Declaration of chemical products, in
the criteria document. To be completed by the producer of the chemical product.
Background to the requirements O3-O5
The general chemical requirements are divided into three specific requirements. The first
concerns classification of the chemical products used, while the next two apply to chemical substances that must not be included in these chemical products. The latter two
requirements place special emphasis on substances that are considered to be SVHC (Substances of Very High Concern). Certain specific chemical groups such as phthalates,
organotin compounds and flame retardants are also covered. In this revision, the requirement has been expanded from only having a classification requirement for
chemical products, to also having two requirements concerning constituent substances in the chemical products used in the manufacture of the sanitary products.
The requirements apply to chemical products and chemical substances used in production/composition of hygiene products and their additional components or are
added in materials where later in the document is referred to these requirements. That includes requirements for materials such as non-woven, fluff/pulp, regenerated cellulose
(viscose), cotton, superabsorbent polymers and plastics/polymers.
023e_6_0_hearing_Background.docx 37 (93)
Nordic Ecolabelling
27 November 2015
Background document
Substances of Very High Concern and the Candidate List
Substances of Very High Concern (SVHC): As the name suggests, SVHC covers
substances that give grounds for caution due to their inherent properties.
They meet the criteria in article 57 of the REACH Regulation, which defines SVHC as:
substances that are CMR (category 1 and 2 under the Dangerous Substances Directive 67/548/EEC or category 1A and 1B under the CLP Regulation), PBT substances, vPvB
substances (see section below) and substances that have endocrine disruptive properties or are environmentally harmful without meeting the criteria for PBT or vPvB. SVHCs
may be included on the Candidate List with a view to them being inscribed on the Authorisation List, which means that the substance becomes regulated (ban, phasing out
or other form of restriction). Since these substances face being phased out or banned, it is only logical for Nordic Ecolabelling not to permit this type of substance in ecolabelled
A substance may meet the criteria for SVHC without being included on the Candidate
List, so there is no direct equivalence between SVHC and the Candidate List.
To avoid cross-references between PBT, vPvB, CMR and endocrine disruptors, instead
of excluding SVHC (which does cover some CMR, PBT, vPvB, etc.) Nordic Ecolabelling chooses to exclude from use the substances on the Candidate List and to separately
exclude PBT, vPvB and endocrine disruptors. This should still cover all SVHC substances.
"Persistent, bioaccumulative and toxic (PBT) organic substances" and "very persistent and very bioaccumulative (vPvB) organic substances" are substances whose inherent
properties are not desirable in Nordic Ecolabelled products. PBT and vPvB substances are defined in Annex XIII of REACH (Regulation (EC) No 1907/2006).
Potential endocrine disruptors are substances that may affect the hormone balance in
humans and animals. Hormones control a number of vital processes in the body and are
particularly important for development and growth in humans, animals and plants. Changes in the hormone balance can have unwanted effects and here there is an extra
focus on hormones that affect sexual development and reproduction. Several studies have shown effects on animals that have been traced to changes in hormone balance.
Emissions to the aquatic environment are one of the greatest sources for the spread of endocrine disruptors42. Nordic Ecolabelling bans the use of substances that are
considered to be potential endocrine disruptors, category 1 (there is evidence of a change in endocrine activity in at least one animal species) or category 2 (there is evidence of
biological activity related to changes in hormone balance), in line with the EU's original report on "Endocrine disruptors" or later studies43.
This entails a ban on substances such as bisphenol A, several phthalates and certain alkylphenols. Phthalates are included as a separate point on the exclusion list to make it
absolutely clear that no phthalates are permitted.
42 Miljøstatus i Norge, 2008
023e_6_0_hearing_Background.docx 38 (93)
Nordic Ecolabelling
27 November 2015
Background document
Organotin compounds
Organotin compounds are regulated in Annex XVII, point 20 of REACH. Subsection 6a
states that dioctyltin (DOT) must not appear at more than 0.1% by weight of tin in feminine hygiene products, for example. A report from 2005 written by Risk & Policy
Analysts Limited (RPA), on behalf of the European Commission,44 states that organotin compounds have been reported in products that include diapers and feminine hygiene
products. According to the report, organotin has historically been used as a catalyst in polymer production, as a stabiliser in polymers and as a biocide in various products.
For more in-depth information on organotin compounds, please see the background document on the Nordic Ecolabelling criteria for chemical building products45. The same
reference also contains concerns about many of the other substances on the exclusion
list: phthalates, APEO (alkylphenol ethoxylates and alkylphenol derivatives) and
halogenated organic compounds with the exception of preservatives and colourants
that meet EU requirements for colourants in food packaging under point 2.5 of
Resolution AP (89).
Antibacterial agents and flame retardants
The article "The Regulation of Nano-particles under the European Biocidal Products Directive: Challenges for Effective Civil Society Participation" from 201146 mentions
diapers as an example of a product that may contain silver nanoparticles. A search on products containing nanosilver generates several hits for both diapers and sanitary
towels47. A product search on diapers and triclosan does not receive as many hits, but several websites mention triclosan in diapers and in other sanitary products48.
Antibacterial substances are not desirable in ecolabelled products, and particularly not in products that come into direct contact with the body. There has been an increase in
products with added antibacterial agents. Nanosilver, for example, is found in everything from socks and toothbrushes to refrigerators. There is particular concern that extensive
and unnecessary use of nanosilver and other antibacterial agents may eliminate desirable bacteria and cause resistance in bacteria, such that in contexts where they are needed
such agents will no longer have the desired effect.
Nordic Ecolabelling is not aware of any use of flame retardants in sanitary products. It
has, however, been noted that products have added flame retardants where the products are flammable and they will be stored in a place where the consequences of a fire would
The requirement concerning additives based on lead, cadmium, chromium VI and
mercury, and their compounds, is of most relevance to additives in polymers, and is described in more detail in section 7.2.8 Polymers. 44 Risk assessment studies on targeted consumer applications of certain organotin compounds, Final Report -
September 2005 prepared for the European Commission by Risk & Policy Analysts Limited (RPA) 45 Nordisk Miljømerking. Bakgrund till miljömärkning av Kemiska byggprodukter. 19 mars 2014, side 36-40.
lim-fugemasse-sparkel/ (hentet 19. mai 2015) 46 Reinsborough, M. T., Sullivan, G., The Regulation of Nano-particles under the European Biocidal Products
Directive: Challenges for Effective Civil Society Participation, European Journal of Law and Technology, Vol. 2, No.3, 2011 47 Produktsøk på bind:/5-15), produktsøk på bleier:
(20/5-15) 48 Produktsøk på bleier og triklosan:/5-15)
023e_6_0_hearing_Background.docx 39 (93)
Nordic Ecolabelling
27 November 2015
Background document
A test from May 2015 conducted by the Danish Consumer Council found polycyclic aromatic hydrocarbons (PAH) in three out of nine diaper brands49. PAH is typically a
pollutant from exhausts, tyre dust and oil, and not something added to diapers. The PAH found in the diapers may originate from the production machinery, and not from the
actual manufacture of the product. It would therefore not be relevant to introduce a ban on PAH in diapers.
7.4.2 Other chemical requirements
This section contains specific requirements for chemical products and chemical
substances that may be used in the manufacture of sanitary products or added to the constituent materials. The definition of constituent substances and impurities is the same
as in the previous section. There is no longer a separate requirement for nanomaterials or flame retardants. The judgment has been made that a general ban on nanomaterials is too
strict and nanosilver has now been removed as a type of antibacterial additive in O10. Flame retardants have been introduced as a separate point in the exclusion list.
Silicone
Silicone is used primarily to achieve a grease- or water-repellent effect as a coating on
materials or as an additive in materials. The following requirement applies where silicone is used, for example on silicone coated paper.
Silicone
The following requirements must be fulfilled in the event of silicone treatment of the
whole or parts of the sanitary product: Solvent-based silicone coatings must not be used. Octamethyl-cyclotetrasiloxane, D4, (CAS 556-67-2) and decamethyl
cyclopentasiloxane, D5, (CAS 541-02-6) must not form part of the product. The
requirement does not apply to D4 and D5 contained as impurities*.
Organotin catalysts must not be used in the production of the silicone polymer. The silicone emulsion (emulsion's coating bath) must fulfil the chemical
requirements O3-O5.
*Impurities of D4 and D5are defined as residual products from the raw material production that can be found in the finished product in concentrations below 800 ppm (0.08% by weight, 800 mg/kg),
Substances added to a raw material or product deliberately and with a purpose, regardless of amount are not
considered impurities, irrespective of quantity. Finished product means the silicone emulsion's coating bath.
Nordic Ecolabelled grease-proof paper meets the requirement.
Duly completed and signed Appendix 1, form 3, Silicones for coating and form 2 in the
criteria document. To be completed by the producers of the silicone products. If the paper is Nordic Ecolabelled, the certification number must be submitted.
Background to the requirement O6
The requirement has been changed in that solvent-based coatings may not be used. This method is being phased out since the use of solvents is undesirable. The requirement
concerning D4 and D5 as impurities has been harmonised with the requirements in the criteria for grease-proof paper from 2014. This entails a change in the limit for impurities
from 100 to 800 ppm based on experience of what the industry is currently able to
49 Artikkel i Politiken, "Dyreste ble taber test: Hver tredje ble har spor af kræftfremkaldende stoffer", 5. Mai 2015
(besøkt 30/6-15)
023e_6_0_hearing_Background.docx 40 (93)
Nordic Ecolabelling
27 November 2015
Background document
achieve. The limit will be reassessed in the next revision. For more information on the requirement concerning silicone, see the background document about the criteria for
grease-proof paper50.
Sanitary products such as diapers very often have a silicone strip, usually of paper, but
not always. The strip either provides protection for Velcro or it protects a self-adhesive strip. In the first case, the silicone treated surface (paper) is constantly held in place in the
diaper. The diaper's silicone surface does not come into direct contact with the baby's skin. A typical pull-up diaper (for a two-year-old child) contains around 2 mg of silicone.
In the second case, the silicone barrier (usually paper) is fully removed from the sanitary towel or sanitary protection in order to reveal the self-adhesive surface. The typical
amount of silicone is 1 g/m2 of paper. There has been no investigation into the amount of silicone used in other sanitary products.
Adhesives and binders
Adhesives/Binders
Adhesives/binders must not have added phthalates or rosin.
Formaldehyde generated during the production process may amount to no more than
250 ppm (0.025 %) measured in newly produced polymer dispersion. The content of free formaldehyde in hardened adhesive must not exceed 10 ppm
(0.001 %). The adhesive/binder must fulfil the general chemical requirements O3-O5. Hotmelt adhesives are exempted from the requirement to document formaldehyde.
Information on sampling, methods of analysis and analysis laboratories is provided in Appendix 2.
Declaration from the adhesive supplier that the adhesive used does not contain phthalates or rosin. Results of analysis of the formaldehyde content of the adhesive.
Appendix 1, form 2 in the criteria document may be used
Background to the requirement O7
The requirement has not been changed in this version of the criteria. The background to the ban on phthalates is that many of these are classified as harmful to health and the
environment51. They are used mainly in PVC, but may also be used as an additive in other materials or chemical products. Rosin is prohibited because it can cause contact
allergies. Rosin is derived from the resin of pine trees. The mixture contains several allergens and can cause a rash after prolonged skin contact. According to the website of
Astma-Allergi Danmark52, it can be found in plasters, sanitary towels and diapers, tape and adhesive, and may also go by the following names: colophony, abietin, abietic acid,
methyl abietate or abiethyl alcohol.
The requirement that the content of formaldehyde must not exceed 250 ppm in newly
produced polymer dispersion and the restriction to 10 ppm in hardened adhesive have been set because formaldehyde is carcinogenic and may cause allergic reactions. This
requirement is identical with the formaldehyde requirement for the Nordic Ecolabelling
50 Nordisk Miljømerking. Om Svanenmärkta Fettäta papper, tilläggsmodul, version 4. 18 november 2014.
http://www.svanemerket.no/for-bedrifter/sok-om-svanemerket/svanens-krav/papirprodukter/mat-og-bakepapir/ (hentet 7. juni 2015) 51 Miljødirektoratet i Norge. Miljøstatus.no. Ftalater. Publisert 30.06.2014, 15:41.
http://www.miljostatus.no/Tema/Kjemikalier/Noen-farlige-kjemikalier/Ftalater/ (hentet 7. juni 2015) 52 Astma-Allergi Danmark. Kolofonium. http://eksem.astma-
023e_6_0_hearing_Background.docx 41 (93)
Nordic Ecolabelling
27 November 2015
Background document
of chemical building products. Hotmelts are, however, exempted from this requirement, since formaldehyde is not relevant for hotmelt adhesives.
Fragrance, lotion and other additives
Fragrances and skin care preparations
Fragrance or other scents (e.g. essential oils and plant extracts) and lotion, skin care
and/or moisturising preparations must not be added to the product or to the
constituent materials.
Duly completed and signed declaration from the manufacturer. Appendix 1, form 4 in the criteria document may be used.
Background to the requirement O8
The requirement concerning fragrance or other scents remains unchanged in this revision, but the ban on flavourings has been deleted since toothpicks are no longer
included in the product group. Fragrance and other scents in the form of essential oils, plant oils and plant extracts, for example, must not be included in sanitary products.
Fragrance, essential oils and plant oils and extracts often contain a number of allergens or carcinogens. To avoid unnecessary effects on health from these types of substances, the
use of fragrance and scents is entirely prohibited. Fragrance and scents also have no function in relation to sanitary products and are considered unnecessary.
The requirement concerning lotion and skin care preparations has not been changed in this version of the criteria. To achieve a moisturising effect on the surface of the sanitary
product, ready-mixed lotion is sometimes added to the sanitary product, or ingredients with moisturising and skin care effects might be added individually to the product.
Moisturising and skin care preparations might include aloe vera, chamomilla recutita, glyceryl stearate and protolatum (Vaseline). Allergens and carcinogens can occur in lotion
preparations. Since lotion and skin care or moisturising preparations are not necessary for the function of the sanitary products, this type of additive is excluded from use on
Odour control substances
Odour control substances
Fragrance or other scents (e.g. essential oils and plant extracts) and lotion, skin care
and/or moisturising preparations must not be added to the product or to the
constituent materials.
Duly completed and signed declaration from the manufacturer. Appendix 1, form 4 in the criteria document may be used.
Background to the requirement O9
As in the previous version, odour control substances are prohibited in sanitary products, with the exception of incontinence care products. The criteria specify that any odour
control substances must fulfil the general chemical requirements O3-O5.
Medicaments and antibacterial agents
Medicaments and antibacterial agents
Sanitary products containing chemical substances designed to prevent, alleviate or cure
illness, sickness symptoms, pain and bacterial growth or to alter bodily functions
cannot be ecolabelled. Lactic acid bacteria added to tampons are exempted from the requirement.
023e_6_0_hearing_Background.docx 42 (93)
Nordic Ecolabelling
27 November 2015
Background document
The manufacturer must declare that the requirement is fulfilled. Appendix 1, form 4 in the criteria document may be used.
Background to the requirement
To avoid any doubt about the extent to which a product with added medication or disinfecting substances is effective and meets the health requirements set for the product
in question, Nordic Ecolabelling has chosen to entirely prohibit medicaments in ecolabelled sanitary products. In this context, medicaments means chemical substances
designed to prevent, alleviate or cure illness, sickness symptoms, pain and bacterial growth or to alter bodily functions (cf. definition in Section 2 of the Cosmetics
Directive). This definition also extends to chemical substances such as silver compounds (healing) and triclosan (antibacterial and disinfecting). Antibacterial agents are now also
named in the title of the requirement, to make it absolutely clear that the addition of antibacterial agents to the products is not permitted. Antibacterial agents could also
reduce any composting of the products.
There is an exemption for lactic acid bacteria in tampons. These are currently added in
one type of tampon to maintain the pH balance in the vagina. Lactic acid bacteria occur naturally in the body and are therefore not considered a medicament.
7.4.3 Dyes and printing inks
The requirements concerning printing and dyeing apply for the product as a whole, the
individual materials and the packaging.
Dyeing
Sanitary products and additional components must not be dyed. This requirement also
applies to the individual components and materials, with the exception of tampon strings. Materials that are not directly in contact with the skin may, however, be dyed if
the dye has a special function. An example of a special function can be dyeing of breast
pads to reduce the visibility of the product through white or light coloured clothing. Titanium dioxide in polymers and viscose is exempted from this requirement. Exceptions may be granted in the case of certain specialist products for use in hospitals
and nursing homes, subject to agreement with Nordic Ecolabelling. If the products are
dyed, the dyes must fulfil requirements O3-O5 in this criteria document and R9-R12 in
the Chemical Module (Nordic Ecolabelling of Paper Products – Chemical Module,
Version 2 or later).
Declaration from the manufacturer of the sanitary product that neither the product nor
the raw materials have been dyed. Appendix 1, form 4 in the criteria document may be
used. In the case of exemptions for specialist products, the manufacturer/supplier of the dye must declare that the requirement is fulfilled by means of safety data sheets and duly
completed and signed Appendix 2, form 2 and 16 in the criteria document.
Printing inks
The inks for printing on the sanitary products or part of this must fulfil O3-O5 in this
criteria document and R9-R12 in the Chemical Module (Nordic Ecolabelling of Paper
Products – Chemical Module, Version 2 or later). The requirement does not apply to
printing on additional components, information sheets and primary packaging.
The manufacturer/supplier must declare that the requirement is fulfilled by means of
safety data sheets and appendix 1, form 2 and 16.
023e_6_0_hearing_Background.docx 43 (93)
Nordic Ecolabelling
27 November 2015
Background document
Background to the requirements O11 and O12
The ban on dyeing sanitary products has been set to minimise the content of harmful
dyes in products that are in close contact with the skin, and unnecessary dyeing of the products. Exceptions may, however, be made for specialist products for use in hospitals
and nursing homes, if there are particular reasons why the products must be dyed. It may be that staff need to see the difference between different sizes, for example.
Materials that are not directly in contact with the skin may be exempted from the requirement if the dye has a special function. This could include dyeing the outer side of
breast pads, so they are not visible through white clothing, for example. Tampon strings are exempted from the requirement, since dyeing the string has an important function,
namely that the user can separate the string from the tampon without damaging the product.
If the products or raw materials are dyed, the dyes must fulfil the requirements set out in O3-O5 and in R9-R12 in the Chemical Module (Nordic Ecolabelling of Paper Products –
Chemical Module, Version 2 or later).
Print is added to certain sanitary products, such as diapers, on the back of the release
paper under panty-liners and incontinence care products, and so on. Flexography is the main printing method used for this. Other techniques such as inkjet are also used for
printing on sanitary products or their packaging. For printing inks, see the requirements in the Chemical Module. A more detailed description of the background to the
requirements set in the Chemical Module can be found in the document: "Background memo. Modules for Nordic Ecolabelled paper products – The Module system –
Background for the Basic Module and the Chemical Module, February 2003".
Dyeing with TiO is commonly used in polymers and viscose to stop them looking grey.
TiO affords good coverage and is permitted in foodstuffs such as sweets, toothpaste,
biscuits, bakery goods, ice cream, tablets, cheese etc
7.5 Requirements concerning materials in the
product and packaging
7.5.1 Fluff/cellulose pulp/airlaid
The requirements concerning fluff/cellulose pulp are split into different levels,
depending on the quantity of cellulose pulp present.
All fluff/cellulose pulp/airlaid must fulfil requirement O13. If there 10.0 % by weight or more of fluff/cellulose pulp/airlaid in the sanitary
product and additional components in a primary package (S+A), requirement O14 must also be fulfilled.
Requirements concerning more than 10.0 % by weight of fluff/cellulose pulp have been
deleted from the criteria for the Nordic Ecolabelling of paper products. The calculations for fulfilling the requirements concerning pulp and paper manufacture are detailed in the
Basic Module, version 2 or later. The calculations are made according to the calculation structure in the Basic Module, which also defines the calculation parameters and
abbreviations. The points are worked out with the help of a technical description of the production processes, where energy consumption and emissions are related to reference
023e_6_0_hearing_Background.docx 44 (93)
Nordic Ecolabelling
27 November 2015
Background document
values for the production. The reference values for different pulps can be found in the Basic Module, version 2 or later. This document contains limit values for the total
electricity and fuel points, limit values for the emission requirements and a limit value for total CO2 emissions. A calculation form developed by Nordic Ecolabelling is to be used
for the calculation.
The requirements concerning fluff production are to be documented by the fluff
manufacturer. The fluffing of the pulp is often conducted at the pulp mill, but may also be conducted at an external production site. It is given its own reference values, relative
to the mechanical fluffing process. If chemicals are used after the production of the cellulose pulp, i.e. in connection with the production of the fluff pulp, these chemicals
must meet the general chemical requirements described in
Fluff/cellulose pulp, general requirements
State State the name and quality of the pulp/airlaid. The following requirements must
be met: The pulp must not be bleached with chlorine gas (Cl2) Optical brightener or fluorinated chemicals must not be added to the pulp. The pulp must not have a growth inhibiting effect on microorganisms, under test
Chemicals added to the pulp to provide specific properties must fulfil the chemical
requirements O3-O11*.
*Production chemicals used during the production of the cellulose pulp are not included in the requirement.
Duly completed and signed Appendix 1, form 5, Fluff/cellulose pulp, general
requirements in the criteria document. To be completed by the pulp manufacturer.
Documentation as specified in requirements O3-O11 if chemicals are used.
Fluff/cellulose pulp, production requirements
The fluff/cellulose pulp/airlaid must fulfil all the requirements in version 2 of the Basic
Module for paper products, and version 2 of the Chemical Module, or corresponding
requirements in later versions. For the requirements concerning energy consumption
and emissions, the following limits and reference values apply:
Energy;
Pelectricity(total) < 1.25
Pfuel(total) < 1.25
The reference values for cellulose pulp are found in the Basic Module.
The reference values for fluff pulp are Ereference = 900 kWh/ADT and Fuelreference =
Addition in reference values for airlaid process: Elreference = 1000 kWh/ADT and
Fuelreference = 1000 kWh/ADT.
Emissions:
Emissions of AOX from production of fluff/cellulose pulp and pulp for airlaid ≤ 0.15
kg/tonne for each pulp. Total emission points ≤ 4.0, and individual emission points ≤ 1.5. The reference values
in the Basic Module shall be used.
Pemissions(total) = PCOD +PP + PS + PNOx ≤ 4
CO2
023e_6_0_hearing_Background.docx 45 (93)
Nordic Ecolabelling
27 November 2015
Background document
For production of fluff/cellulose pulp andairlaid, the limit value for emissions of CO2
is 450 kg CO2/ADT The application tool My Swan Account may be used. Contact the ecolabelling organisation for a password.
Documentation from the manufacturer of the fluff/cellulose pulp/airlaid showing that the requirements are fulfilled. If the pulp has previously been approved by Nordic
Ecolabelling, state the name of the pulp and when it was approved.
Background to the requirements O13 and O14
The requirements that apply to all pulps, irrespective of the quantity, are associated with
the use of chemicals. The pulp must not be bleached with chlorine gas (Cl ) and optical
brightener or fluorinated chemicals must not be added to the pulp. Bleaching with
chlorine gas is no longer used in Europe, but the requirement remains in place to cover imported pulps. It is less common for fluorinated chemicals to be added to the pulp, as is
the case for disposable products such as paper plates. Nordic Ecolabelling is, however, particularly concerned about the unnecessary use of fluorinated chemicals. The pulp
must also not have a growth inhibiting effect on microorganisms, under test method EN 1104. The use of chemicals intended to have an antibacterial effect is unnecessary in
sanitary products, and residues of process chemicals are also undesirable. Chemicals added to the pulp to provide specific properties must fulfil the general chemical
requirements O3, O4 and O5. This requirement therefore only applies to chemicals added after normal production of the cellulose pulp (unless added to provide specific
properties associated with sanitary products), and during the fluffing of the pulp, or those added to the pulp during composition of the sanitary product. This may relate to
debonding agents and plasticisers.
The requirements concerning cellulose pulp have been tightened in this revision and
follow the new requirements in the Basic Module and the Chemical Module for Nordic Ecolabelling paper, as revised in 2011. There are requirements concerning the origin of
the fibre material under requirements for certified forestry; requirements concerning emissions to air and water in the production of the cellulose pulp; and requirements
concerning energy consumption and CO emissions from the production of the pulp. In
addition, the Chemical Module sets requirements for chemicals used in the production
process. The background to the changes in version 2 of the Basic Module and the Chemical Module is described in "Background memo. Modules for Nordic Ecolabelled
paper products"53. In connection with the revision of the paper requirements, Nordic Ecolabelling has developed an electronic application guide, My Swan Account, which
may be used for information about the cellulose pulp.
Pulps may have been checked previously by Nordic Ecolabelling via the My Swan
Account database. Checks of the cellulose pulp mean that Nordic Ecolabelling has examined the information about the pulp. Contact one of the secretariats if this is the
Manufacturing requirements for pulps and air-laid applies only when the materials
contained 10.0% by weight or more. This limit is set so the documentation burden will not be too great for products which includes many materials in smaller quantities.
Requirements concerning energy and CO emissions as related to fluff pulp include the
cellulose pulp used. Energy and emissions data from the production of the cellulose pulp
must be used in order to calculate the final values. Nordic Ecolabelling has drawn up a 53 Nordisk Miljømerking. Baggrundsnotat. Moduler for Svanemærkede papirprodukter. 22. juni 2015.
http://www.svanemerket.no/Documents/Kriterier%20mm/kopipapir_bkg.pdf (hentet 19. mai 2015)
023e_6_0_hearing_Background.docx 46 (93)
Nordic Ecolabelling
27 November 2015
Background document
new calculation form to facilitate the required calculations. The requirements concerning energy and CO emissions with regard to fluff pulp have undergone the following
changes in this revision:
New reference values have been drawn up for both electricity and fuel for fluff
pulp and airlaid.
The values for the electricity and fuel points have been amended. The electricity
points have been tightened.
New requirements for CO emissions from energy consumption are calculated
based on purchased electricity and fuel used for heating and electricity generation (pulp and fluff process).
The underlying data for calculating the energy points and guidance on how the calculations work can be found in the Basic Module, version 2 or later. Further
information is available in the aforementioned background document for the Basic Module.
The reference values and point values include both the manufacture of the pulp and the fluffing process. The new reference values are based on the licence data available to
Nordic Ecolabelling. The values have also been compared with the reference values proposed for the EU Ecolabel's criteria for absorbent hygiene products. Since the EU
Ecolabel chose to drop the energy requirement in its last revision of the criteria, Nordic Ecolabelling's requirements may be seen as comparatively stricter.
The reference values have been assessed and revised in relation to the actual processes involved in the production of fluff pulp. The vast majority of the licence data available to
Nordic Ecolabelling relates to fluff pulp made from ECF/TCF pulps, which have to be dried to 95% dry matter content. This process is more energy intensive and these
additional energy needs have been accounted for in drawing up the reference values for electricity and fuel. CTMP pulp has not been accounted for in the requirements.
Version 5 of the criteria for sanitary products contained energy points for electricity and for total energy consumption (electricity plus fuel), while the new criteria have separate
requirements for electricity and fuel. Analysed licence data indicates that the point score value for electricity can now be tightened. Airlaid has beens given its own reference
values. A machine manufacturer reports that an air-laid-process uses in average 1150 - 1230 kWh el/tonne product and 1000 - 1200 kWh gas/tonne product (included air
conditioning) 54. The reference values found in the Basic Module are not based on averages but on manufacturing processes of good performance. But since it is the first
time that Nordic Ecolabelling proposes an energy requirement in relation to this process, it is considered as a sufficiently stringent level. Nordic Ecolabelling has, however, hope
that the consultation should generate additional data. More information on airlaid is described in the chapter on non-woven, 7.5.8.
The requirement for CO emissions has been set at 450 kg/ADT. This value includes the
fluffing process, where the pulp is dried to a dry matter content of 95%. The drying
process requires more energy and thus causes higher CO emissions. This is the first time
that a value for CO emissions has been set for the production of the fluff pulp. A
requirement on CO is important, since it is an indirect measure of energy consumption
54 Samtal och mailkorrspondans med Ingo Mählmann på Oerlikon Neumag (3/7-15)
023e_6_0_hearing_Background.docx 47 (93)
Nordic Ecolabelling
27 November 2015
Background document
from electricity and fossil fuels. The EU Ecolabel has set up the same limit value (450 kg/ADT) in its criteria for absorbent hygiene products. In order to calculate the CO 2
emissions in relation to purchased electricity, Nordic Ecolabelling uses a factor of 385 g CO /kWh. Nordic Ecolabelling's requirements in this respect can thus also be
considered stricter than those of the EU Ecolabel.
The requirement concerning emissions from cellulose production has been harmonised
with version 2 of the Basic Module. The background to the emissions requirement and guidance on how the calculations of the emissions (from the cellulose pulp production)
work are set out in the Basic Module, version 2 or later. Further information is available in the background document for the Basic Module55. The Basic Module allows the use of
a mix of pulps, with the limit value for AOX for each individual pulp set at 0.25kg/tonne of pulp. The limit value for the mixed pulps is, however, set at 0.17 kg/tonne of fluff
pulp. It is not common to use more than one pulp in sanitary products. The requirement for AOX of 0.15 kg/tonne of pulp has thus been retained from version 5 of the criteria.
The wording has, however, been amended to make it clear that the limit values apply per individual pulp, so there can be no misunderstanding or interpretation that the
requirement has been set for a mix of pulps.
The fluffing process entails no significant emissions to water. The reason for this is that
steam is formed as part of the drying process. No limit value has thus been set with regard to emissions to water from the fluff production. Overall, this requirement on
emissions to air and water can be considered to be harmonised with the Basic Module, with the difference that the Basic Module includes emissions for both pulp and paper
Fluff or other cellulose pulp based on recycled fiber is not allowed because of the risk of
spreading unwanted chemicals as pollutants.
7.5.2 Paper (tissue paper, release paper, paperboard and
other paper)
The paper requirements apply for different types of tissue paper, paper in tape or release
paper (silicone paper), other paper, carton and paperboard. The requirements for paper are separated into different levels, depending on the quantity of paper involved. The use
of recycled paper is not permitted in the products, unless the components are removed from the product before use, as with some types of tape and release paper. Recycled
paper is permitted in the packaging and in any accompanying information. Whatever the type of paper or paperboard, it is not permitted to coat the paper or paper pulp with or
add fluorinated compounds.
All paper/carton/cardboard/used in sanitary products must fulfil O15. In addition
paper/carton types that account for 10.0 % by weight or more of (S+A) must fulfil requirement O16. Each papertype shall be summarized separately.
All primary packaging of paper or cardboard must fulfill requirements O15, paragraphs a) and b).
The requirements refer to the criteria for the Nordic Ecolabelling of paper:
55 Nordisk Miljømerking. Baggrundsnotat. Moduler for Svanemærkede papirprodukter. 22. juni 2015.
http://www.svanemerket.no/Documents/Kriterier%20mm/kopipapir_bkg.pdf (hentet 19. mai 2015)
023e_6_0_hearing_Background.docx 48 (93)
Nordic Ecolabelling
27 November 2015
Background document
Nordic Ecolabelling of copy and printing paper, version 4. These include
requirements concerning wood-containing and wood-free non-converted printing paper made from chemical and/or mechanical pulp and/or recycled fibre, and the following paperboard types: Solid Bleached Board (SBB), Solid Bleached Sulphate (SBS), Solid Unbleached Board (SUB), Folding Boxboard (FBB) and recycled fibre-based White Lined Chipboard (WLC).
Nordic Ecolabelling of tissue paper, version 5. Cellulose-based tissue paper made
from virgin and/or recycled fibre.
Nordic Ecolabelling of grease-proof paper, version 4. This includes cellulose-
based paper, which may be coated in different ways as parchment paper/grease-proof paper and various types of release paper.
Paper/paperboard, general requirements
State the name, grade, grammage and manufacturer of the paper. The following
requirements must be met:
The paper/carton/cardboard must not be bleached with chlorine gas (Cl2).
The paper/carton/cardboard must also not be coated or treated with fluorinated
chemicals. Requirement also applies to fluorinated additives in the paper pulp. The pulp must not have a growth inhibiting effect on microorganisms, under test
method EN 1104. If the paper is coated with silicone, requirement O6 must be fulfilled*. *Nordic Ecolabelled grease-proof paper fulfils the requirement. Information on analysis laboratories is given in Appendix 2.
Documentation showing that the requirements are fulfilled. Appendix 1, form 6 in the criteria document may be used for the declaration.
Paper/paperboard, production requirements
The Paper/paperboard must be:
Nordic Ecolabelled according to the criteria for Nordic Ecolabelling of copy and
printing paper (version 4 or later) or complies with the Nordic Ecolabelling
requirements for inspected paper. The requirements for inspected paper are given in
or Nordic Ecolabelled according to the criteria for Nordic Ecolabelling of tissue paper
(version 5 or later)
or Nordic Ecolabelled according to the criteria for Nordic Ecolabelling of grease-
proof paper (version 4 or later).
If the paper/carton is treated with silicone, O6 silicone must be fulfilled if unless the paper is Nordic Ecolabelled according to Nordic Ecolabelling of grease-proof paper.
Documentation from the manufacturer showing that the requirements are fulfilled. If the paper material is already Nordic Ecolabelled, the certification number must be
submitted in addition.
023e_6_0_hearing_Background.docx 49 (93)
Nordic Ecolabelling
27 November 2015
Background document
Background to the requirements for paper O15 and O16
The requirements for paper are separated into different levels, depending on the quantity
of paper involved. This is done so the burden of documentation should not be too big for products that contain small amounts of many materials. This would hinder
manufacturers from Nordic Ecolabelling their products and so fewer environmental requirements would be fulfilled overall.
The requirement which all types of paper must fulfil is that they are not coated with fluorine or have fluorine added to the cellulose pulp. The use of fluorine additives
appears to have increased and these are problematic from both a health and an environmental perspective. More information on the background to this requirement can
be found in the background to the criteria for the Nordic Ecolabelling of grease-proof paper56.
The requirements concerning microbial activity and wet strength remain unchanged in this revision, and are the same as those set in the criteria for tissue paper. The paper's
microbial activity gives an indication of whether the paper contains antimicrobial agents. The ban on high wet strength has been removed. But there is a requirement for
information on the product that relevant products shall not be discarded in the toilet, see O41. Although wet strength agents may contain chlorinated organic compounds that are
not beneficial to the environment, it is believed that these will not be added unnecessarily.
If the product contains 10.0 % by weight of paper or more, the requirements for the Nordic Ecolabelling of paper must be fulfilled. This means that requirements are set for
the fiber raw material (that it comes from sustainably managed forests), for chemicals used in the production, for energy consumption and for emissions of AOX, CO (which
are also restricted by the energy requirement) and other emissions such as oxygen-demanding organic compounds (COD), sulphur, nitrogen oxides (NOx) and
phosphorus. More information on the requirements for the Nordic Ecolabelling of paper products can be found in the "Background document for the Basic and Chemical
Modules, version 2"57.
7.5.3 Wood materials
The requirements apply to components made from solid wood, such as the shaft of a
cotton bud.
Origin, legality and traceability
The applicant must state the name of the tree species (species name). Listed wood
species* must not be used.
The supplier of the wood material to the sanitary manufacturer must be Chain of
Custody (CoC) according to FSC or PEF certification schemes.
A minimum of 70 % by weight of all wood raw materials must come from certified
forestry according to FSC or PEF certification schemes. The remainder of the wood raw material must come from controlled sources, i.e. those covered by the
certification schemes FSC or PEFC (Controlled Wood).
56 Nordisk Miljömärkning. Om Svanenmärkta Fettäta papper, tilläggsmodul Version 4.0.18 november 2014. http://www.svanemerket.no/for-bedrifter/sok-om-svanemerket/svanens-krav/papirprodukter/mat-og-bakepapir/ 57Nordisk Miljömärkning. Bakgrundsdokument för bas- och kemikaliemodulerna, version 2. 22 juni 2011.
023e_6_0_hearing_Background.docx 50 (93)
Nordic Ecolabelling
27 November 2015
Background document
The requirement may be documented as volume of wood purchased on an annual
basis. *There will be prepared a list of excluded wood species.
Name (tree species) for the wood raw material used. Appendix 1, form 7 can be used. The applicant must document that at least 70 % of all the wood raw material used in
the Nordic Ecolabelled product on an annual basis comes from certified forestry, and
the remainder is Controlled Wood. Valid CoC form the supplier of wood. Nordic
Ecolabelling may request further documentation if there is lack of clarity surrounding
wood raw material.
Background to the requirement O17
Nordic Ecolabelling sets requirements concerning wood raw material in the relevant
criteria, in order to contribute to forestry that is sustainable in ecological, economic and social terms. From a life cycle perspective, forestry is an important part of the wood
product's environmental impact, and it is important that the renewable raw material is grown/used in a sustainable way. Nordic Ecolabelling's forestry requirements focus on
sustainable forestry and the traceability of the wood raw material. By setting a requirement that the wood raw material must come from certified forestry, Nordic
Ecolabelling is supporting a trend towards more sustainable forestry. The requirements for solid wood below are based on "new" forestry requirements, which were put out for
public consultation in spring 2015 and adopted by the Nordic Ecolabelling Board on 5th November 2015. Contributions to this consultation may therefore also lead to the wood
requirements being changed after the consultation on sanitary products.
Few parts of absorbent sanitary products are made from solid wood, but it may be used
in cotton buds and similar products. This is the main reason why the product group has requirements concerning wood materials. Since the requirements are now based on
Nordic Ecolabelling's new forestry requirements, the requirement has changed somewhat, although the proportion of certified wood is the same as before, at 70%. The
consultation document for the new forestry requirements describes why Nordic Ecolabelling wants to impose strict forest requirements, even though the actual wording
of the requirement was changed after the consultation58.
7.5.4 Cotton
The requirements for cotton depend on the quantities involved. All cotton must fulfil
O18. If cotton makes up 5.0 % percent or more by weight of (S+A), the requirements O19 and O20 must also be fulfilled.
Cotton, bleaching with chlorine gas
The cotton must not be bleached with the aid of chlorine gas (Cl2).
Declaration from the cotton manufacturer/supplier showing that the requirements are fulfilled. Appendix 1, form 8 in the criteria document may be used for the declaration.
Cotton, raw fibre
The cotton must be organically cultivated or cultivated in the transitionary phase to
organic production. The string on tampons is exempted from the requirement.
58 Nordisk Miljømerking. Skovkrav i Svanens kriterier. Høring: 9 marts 2015 - 5 juni 2015.
023e_6_0_hearing_Background.docx 51 (93)
Nordic Ecolabelling
27 November 2015
Background document
Organic means cotton grown in line with Council Regulation (EC) No 834/2007 of 28 June 2007 on organic production and labelling of organic products, or products produced in the same way and under similar control schemes. Examples include: KRAV, IFOAM, KBA, OCIA, TDA, DEMETER.
Duly completed and signed Appendix 1, form 8 in the criteria document and attached certificate or transition certificate from a competent body for the certification of
organic cultivation. If in the case of cultivation in a transitionary process no certificate
is available, the ecolabelling organisation must be supplied with information on the
supplier and method of cultivation and sufficient documentation showing that the
cultivation is in the process of transition to organic production. The cotton plantation
may be inspected by the ecolabelling organisation.
Cotton, additives
Substances added to cotton must fulfil the chemical requirements
Duly completed and signed Appendix 1, form 8 and in addition form 2, 3 and 4 and safety data sheets for any chemical additives.
Background to the requirements for cotton O18, O19 and O20
Our cotton requirement is strict but steerable for the manufacturer. We require all cotton used in 5.0 % by weight sanitary products and in the additional components to be
organically cultivated. This brings major environmental gains compared with conventionally grown cotton, since chemical pesticides, defoliants and artificial fertilisers
are not used. Cotton cultivation sometimes requires irrigation of large areas, which has an impact on the hydrology of the surrounding water resources and on biodiversity. It has
been estimated that cotton cultivation accounts for 1-6% of the decline in global freshwater resources. It should, however, be stressed that irrigation and excessive use of
water are not associated exclusively with cotton production. Water shortages are a general problem in agricultural areas. Cotton is grown in areas that use irrigation and in
areas that only make use of rainwater. The amount of water used in production depends on the country/area and the irrigation method. It is thus not an environmental problem
that can be resolved simply by means of organic production. The cotton requirement has not been changed in this version.
7.5.5 Viscose
The requirements for viscose depend on the quantities involved. All viscose must fulfil
O21. If viscose makes up 10.0 % by weight or more of (S+A), requirement O22 must be
Viscose, bleaching
Chlorine gas (Cl2) must not be used to bleach cellulose pulp or cellulose fibre.
The resulting total amount of adsorbable organic halogens (AOX) and organically
bound chlorine (OCl) must not exceed: 0.15 kg per tonne of fibre pulp in wastewater from the fibre pulp production
and 150 ppm in the finished fibre (OCl) Information on sampling, methods of analyses and analysis laboratories is provided in Appendix 2 in the criteria document.
Declaration from the manufacturers of the cellulose pulp and regenerated cellulose that the requirement is fulfilled including a test report. Appendix 1, form 9 in the cirteria
document can be used.
023e_6_0_hearing_Background.docx 52 (93)
Nordic Ecolabelling
27 November 2015
Background document
Viscose, production requirements
COD emissions from viscose production (the production of cellulose pulp and
regenerated cellulose) must not exceed a combined total of 35 kg per tonne of regenerated cellulose. Sulphur emissions to air must not exceed more than 20 g/kg of staple fibre expressed
as an annual average. Zinc emissions must not exceed 0.2 kg Zn/kg of regenerated cellulose, expressed as an
annual average. The cellulose pulp must fulfill the energy requirement 014. The quantity of oxygen depleting substances may also be stated as the equivalent quantity of TOC.
Information on sampling, methods of analysis and analysis laboratories is provided in Appendix 2 in the criteria document.
Duly completed and signed Appendix 1, form 9 and test report from the production of
regenerated cellulose showing that the requirement is fulfilled. The methods of analysis must be described and the laboratories responsible must be stated. The sanitary
manufacturer must inform the viscose producer on which paragraphs to fill in.
Background to the requirements O21 and O22
Viscose fibre is a type of regenerated cellulose fibre made from raw materials such as wood, bamboo and cotton (cotton linters). Viscose may comprise filament fibre or staple
fibre. Filament fibre is long, continuous fibre and is used in products as a replacement for silk. For staple fibre, the fibre is cut up before being spun. The product is then more
like natural fibre, which is mainly staple fibre, e.g. wool and cotton. According to the Global and China Viscose Fiber Industry Report from 201359, viscose staple fibre
production accounts for around 90% of total produced viscose. Rayon is a general term for regenerated cellulose fibre60, but in everyday speech rayon and viscose are often
interchangeable. Modal and lyocell are other regenerated cellulose fibre. Modal fibre is a second-generation viscose fibre developed by Lenzing. Modal is manufactured using a
modified viscose process that gives fibre with higher dry and wet strength, improved dimensional stability, and greater durability61. Lyocell is a relatively new cellulose fibre
that is similar to viscose, but more durable. Lyocell is also known by the trade name Tencel, which Lenzing has patented.
The following market data is taken from the Global and China Viscose Fiber Industry Report from 2013, as referred to above. The majority of viscose production is based in
Asia (approx. 80%) with China as the dominant country (approx. 62%). China largely produces first-generation viscose. In 2012, the Aditya Birla Group was the world's largest
manufacturer of viscose, with a capacity of around 800,000 tonnes, with factories in countries such as India, Thailand, Indonesia and China. Austria's Lenzing was ranked
second with a viscose capacity of 770,000 tonnes (2011) and factories in Austria, Indonesia, China, the UK and the USA, and it also has a monopolistic position in lyocell
fibre and modal fibre production. Other major viscose fibre manufacturers are located mainly in China.
59 Research in China; Global and China Viscose Fiber Industry Report, 2012-2015, 2013. Sammedrag og presentasjon
av rapporten finnes på Research in China sine hjemmesider:
http://www.researchinchina.com/htmls/report/2013/6635.html (10/10-14) 60 Wikipedia.com «Rayon»: http://en.wikipedia.org/wiki/Rayon 61 Om Modal på hjemmesiden til European Man-made Fibres Association:
023e_6_0_hearing_Background.docx 53 (93)
Nordic Ecolabelling
27 November 2015
Background document
Production process
For a detailed description of the viscose and lyocell process, see the report Reference
Document on Best Available Techniques (BREF) in the Production of Polymers, August 200762. A brief summary appears below.
Viscose fibre is based on cellulose fibre. Cellulose pulp is used and it is desirable to have more than 89% pure alpha-cellulose, i.e. most of the lignin and hemicellulose is removed
from the wood fibre. After refining and bleaching with NaOH (alkalisation), the pulp swells and is further treated with CS to form cellulose xanthogenate. (The suspension
has high viscosity, hence the name viscose). This coagulates in an acid bath containing H SO , NaSO and ZnSO . After further ripening, filtering and degassing, the viscose is
spun. Since viscose is normally based on chemical pulp, there may be major emissions of COD from the production. The manufacture of viscose also generates emissions of
sulphur and zinc. Lyocell fibre has been manufactured since 1998, in a slightly different process where the pulp is dissolved in an organic solvent (NMMO = N-
methylmorpholine-N-oxide) instead of CS /NaOH. The solvent is fully biodegradable
and can dissolve the cellulose without chemical processing.
For more information on the environmental problems associated with the production of cellulose pulp, see also Nordic Ecolabelling's background document for the Basic
Module for cellulose pulp production.
Background to the requirements
The production of viscose is covered by the EU's Reference Document on Best Available Techniques (BREF) for polymers and for pulp, paper and board. All the EU
BREF documents are available on the European Commission's Joint Research Centre website63. Table B1 in Appendix 1 gives an overview of BAT values from the two BREF
reports. Also included are the requirements set for viscose in the EU Ecolabel's criteria for textiles from 2014 and AHP (absorbent hygiene products). The table additionally
features Nordic Ecolabelling's requirements for viscose in version 5 of the sanitary product criteria and in version 4 of the textile criteria.
Raw material extraction: The raw material for regenerated cellulose fibre, e.g. viscose, is primarily wood pulp and
cotton (cotton linters), but it may also be bamboo. A requirement was recently added to the criteria for textiles (version 4) stating that the raw materials must come from
sustainable and legal sources. There is currently little experience of these requirements, and requirements have therefore not been introduced so far back in the chain in this
revision of the criteria for sanitary products.
Chlorine gas and AOX:
The requirement states that the cellulose pulp must not be bleached with chlorine gas. Chlorine gas is no longer used in Europe, but its use has not ended everywhere in the
world. Chlorine gas is an effective bleaching agent, but it causes considerable emissions of organochlorine substances. There are now good alternative bleaching methods for
cellulose pulp. According to Lenzing64 bleaching with ClO is the industry standard for
dissolving pulp. The industry standard for viscose and lyocell fibre is NaClO bleaching.
This is referred to as ECF (elemental chlorine free) bleaching. Some manufacturers also
62 Reference Document on Best Available Techniques in the Production of Polymers, August 2007 63 EU Kommisjonens BREF-dokumenter er tilgjengelige på siden: http://eippcb.jrc.ec.europa.eu/reference/ 64 Høringssvar fra Lenzing til versjon 5 av kriteriene (2007)
023e_6_0_hearing_Background.docx 54 (93)
Nordic Ecolabelling
27 November 2015
Background document
use the TCF (total chlorine free) bleaching method. Version 6 of the criteria introduces a limit value for emissions of AOX in cellulose pulp production, which corresponds with
the requirement for the production of fluff/cellulose pulp. In addition, there is now a limit value for organically bound chlorine in the actual fibre, in line with the EU
Ecolabel's requirements for absorbent hygiene products.
The requirement set for COD emissions applies to both the manufacture of the pulp and the further production of the viscose. Instead of measuring COD, TOC may be
measured, if there is a correlation between the two values for the production process. Routine analysis of COD applying the ampoule method makes use of environmentally
harmful mercury (Hg), and so several companies now use TOC as the parameter. The set value is based on the EU's BATC report for Pulp (3-5 kg/tonne), Paper and Board and
BREF Polymer (10-30 kg/tonne) (both referred to in the table) and has been tightened to 35 kg/tonne of regenerated cellulose.
Sulphur, Zinc and Copper: The requirement concerning emissions of sulphur to air has been kept at the same level
as before, and has proven to be achievable for licensees. During the revision of the EU Ecolabel's criteria for textiles, it was suggested that the sulphur emission requirement
should be tightened to 12.5 g S/kg for staple fibre. Stakeholders65 commented that this is not achievable and that the limit of 30 g S/kg already requires a combination of different
recycling technologies. There is no differentiation between staple and filament fibre in the requirement, since staple fibre is the relevant fibre for the product group. The level of
20 g S/kg in version 5 of the criteria has proven achievable for licensees and the requirement level has therefore been kept as it is.
A requirement was proposed for emissions of zinc and copper in the EU Ecolabel's criteria for textiles and absorbent hygiene products, but these requirements were deleted
from the final criteria. A copper requirement is relevant for cupro fibre, which is made from the hairs on a cotton plant (cotton linters) with a blend of copper and ammonia as
a solvent (Cu(NH ) (OH) ). This may still be produced outside the EU66. The fibre is
produced as filament fibre, and is therefore mainly of interest as a replacement for silk,
for example as liner in suits. Cupro fibre is not considered relevant for the product group sanitary products, and the requirement concerning cupro fibre has therefore been
removed from this version of the criteria. The limit value for emissions of zinc in version 5 of the criteria has been retained in version 6, since the value has proven to be at a
The viscose requirements in version 6 of the criteria for sanitary products do not entirely
match the Nordic Ecolabelling and EU Ecolabel requirements for textiles. Viscose that is labelled with either the Nordic Ecolabel or the EU Ecolabel does, however, automatically
meet the viscose requirements in version 6 of the criteria for sanitary products.
As for pulp and paper, the requirements are set only when the materials are included with
10.0 % by weight or more.
65 Rapporten «Stakeholder table of comments/responses», oktober 2013 på EU Ecolabels kriterieutviklingsnettside for tekstiler:5/10-14) 66 Rapporten «Technical background report», oktober 2013 på EU Ecolabels kriterieutviklingsnettside for tekstiler:
023e_6_0_hearing_Background.docx 55 (93)
Nordic Ecolabelling
27 November 2015
Background document
7.5.6 Polymers (materials/films and fibre)
Polymers/plastic materials that are subject to requirements when used in sanitary
products, additional components and primary packaging are: polyethylene (PE), polypropylene (PP), polyester (PET), polystyrene (PS), polyamide (PA), ethylene vinyl
acetate (EVA) and polyether/polyurethane (e.g. elastane, lycra, spandex, foam) and polymers based on renewable raw materials. Superabsorbents (e.g. SAP and bioSAP),
viscose and cotton are covered in this section. Other polymers may be included together with other materials for which no requirements have been set, up to a maximum of 5.0
% by weight, with maximum 2.0 % by weight for each material type, see O2. This means, for example, that silicone materials may be used in small quantities, even though no
silicone polymer requirement has been set. However, if silicone is used as an additive in other materials or as a coating, requiremust be fulfilled.
For polymers/plastic materials (such as foil, fibre or other components), there are general requirements concerning additives to or constituent substances of the polymer and
concerning energy consumption in polymerisation. The energy requirements differ for each polymer type and apply if a polymer type is included with 5.0 % by weight or more.
Where a plastic material is used that comprises two or more polymer types (e.g. in co-spun fibre), the energy requirement must be fulfilled for the polymer with the highest
proportion by weight. For polymers made from renewable materials, there is an additional requirement concerning the renewable raw material.
If a sanitary product with additional components comprises both a polymer film and a polymer fibre of the same polymer type (e.g. PP), these are counted individually when
calculating the percentage by weight to see which requirement applies. Polymer fibre of the same type from multiple suppliers should be combined to see whether the weight
limit is achieved. PP fiber and PP tape will be different polymer components. The weight of PP fiber from different suppliers must be summarised to see whether the requirement
shall be met for the material. PUR foam and thermoplastic polyurethane will be various polymer components. If the polymer/plastic type is contained in 4 or more components
to come up in the current weight limit, the requirement has to be fulfilled for at least 50.0 % by weight of the material.
The polymer requirements are divided into two different levels, depending on the quantities involved in relation to (S+A):
All polymers/plastic materials must meet requirement O23 and O24, part A. If elastane/polyurethane accounts for 5.0 % by weight or more, requirement O25
must also be fulfilled.
If polyamide accounts for 5.0 % by weight or more requirement O26 must be
If a polymer type accounts for 5.0 % by weight or more, one of the requirements
O27 and O28 must also be fulfilled.
If a polymer type accounts for 20.0 % by weight or more requirement O24, part B
must also be fulfilled.
023e_6_0_hearing_Background.docx 56 (93)
Nordic Ecolabelling
27 November 2015
Background document
Requirements regarding raw materials (O29) applies if:
o polymers which are based on one commodity type accounts 20.0 % by
o if a single commodity type (in polymers made of several commodity
types) accounts for 20.0 % by weight or more)
Recycled plastic must fulfil O30
The following requirements are set for polymers:
Polymers, halogen-based
Sanitary products, additional components and their packaging must not contain
halogen-based polymers, e.g. PVC.
Declaration from the polymer manufacturer or documentation from the manufacturer of the sanitary products showing that the requirement is fulfilled. Appendix 1, form 10
in the criteria document may be used.
Polymers, constituent substances
Part A:
The following substances must not be present in the polymer apart from impurities*:
a) halogenated organic compounds b) phthalates c) organotin compounds d) compounds based on lead, cadmium, chromiumVI and mercury
The amount of antimony in polyester, measured as an average value on an annual basis,
must not exceed 260 ppm (the requirement does not, however, apply to recycled
polyester**).
Part B:
Additives and chemical substances in polymers/plastics must fulfil the chemical
requirements O3-O11. *Impurities are traces from polymer production (including residual catalysts), which is contained in concentrations below 100 ppm (0.01 weight %, 100 mg/kg), but not substances that have been added to the raw material or
product actively and for a particular purpose irrespective of quantity. **For recycled polyester see 030.
Information about test methods and analysis laboratories is provided in Annex 2.
Declaration from the polymer producer that the requirement is fulfilled. Alternatively, a
test may be used as documentation for the requirement in part A. The test can be
requested by for example the non-woven supplier that is using the polymer/plastic
material. Annex 1, Form 10/11 in the criteria document may be used. The sanitary
manufacturer must inform the viscose producer on which paragraphs to fill used.
a) A closed process must be used when producing elastane/polyurethane. b) Organotin compounds shall not be used. c) Fibre (as elastan, spandex and lycra) d) Emissions to air of aromatic diisocyanates during polymerisation and, if
applicable, spinning must be less than 5 mg/kg of produced fibre, expressed as
an annual average.
023e_6_0_hearing_Background.docx 57 (93)
Nordic Ecolabelling
27 November 2015
Background document
N,N-Dimethylacetamide (DMAc, CAS no. 127-19-5) must not be used in the
production of elastane.
e) PUR foam and thermoplastic PUR must fulfil criterion 2 i EU Ecoabels
criteria for Bed mattresses.
Declaration from the polymer producer that the requirement is fulfilled. Annex 1, Form 10 in the criteria document may be used in addition to test reports from the
polymer producer. The sanitary manufacturer must inform the polymer/plastic material
producer on which paragraphs to fill in.
Polyamide
Emissions of nitrogen dioxide (N2O) to the air from the production of monomers
must not exceed 9 g/kg caprolactam (for PA 6) or adipinsyre (for PA 6.6), expressed as an annual average.
Detailed information and/or a test report from the polyamide manufacturer showing that the requirement is fulfilled or a valid EU Ecolabel licence in accordance with the
Commission's decision from July 2009. Annex 1, Form 10 in the criteria document may
Energy consumption in polymer production for fossil-based
polymers
The total energy consumption for polymerisation must not exceed:
2.1 MJ/kg for PP, HDPE and LLDPE
2.6 MJ/kg for LDPE and EVA
1.1 MJ/kg for PS
8 MJ/kg for PA 6.6
10 MJ/kg for PA 6
6.0 MJ/kg for PET
15 MJ/kg for elastane/PUR
The calculation must show the factory-specific energy for the polymerisation of the
Annex 1, Form 10 in the criteria document may be used in addition to a calculation of
the energy consumption in MJ/kg of polymer. A description must also be provided of how the energy consumption from different subprocesses has been included in the
calculation, divided according to the different energy types involved (electricity, fossil
energy sources, steam and so on). The energy consumption must be declared by the
polymer producer. The sanitary manufacturer must inform the polymer/plastic material
producer on which paragraphs to fill in.
Energy consumption for production of polymers from renewable
raw materials
The energy consumption from fossil fuels in the production of renewable polymers
must not exceed: 37 MJ/kg of polymer based on renewable raw materials The calculation of energy consumption for renewable polymers must include the
processes from the monomer production to the finished polymer. Energy from raw
material cultivation from extraction of the raw material, transport of the raw material to
the production site or the energy content of the actual raw material should not be
included in the calculation.
023e_6_0_hearing_Background.docx 58 (93)
Nordic Ecolabelling
27 November 2015
Background document
Annex 1, Form 11 in the criteria document may be used in addition to a calculation of the energy consumption of accordance with the certification scheme fossil fuels in
MJ/kg of polymer. A description must also be provided of how the energy
consumption from the different sub processes is included in the calculation. The
sanitary manufacturer must inform the polymer/plastic material producer on which
paragraphs to fill.
Palm oil, soybean oil and sugar beet as feedstock for the
renewable polymer
The following requirements are set for certification of the raw materials:
Palm oil must be RSPO certified after version P&C 2013 with physical segregation
at all process steps (Track and Trace).
Soya oil must be RTRS certified after version 2/2013 with physical segregation in all
process steps (Fully Segregated type).
Sugar beet must be Bonsucro* ccertified with physical separation at all stages
(Physical shipment).
The polymer producer, buying in the renewable feedstock, must be chain of custody
certified (CoC) accordance with the certification scheme.
*Nordic Ecolabelling will assess whether the standard meets the Swans requirements set for standard, certification scheme and certification bodies given in Appendix 4.
Annex 1, Form 12 in the criteria document, copy of relevant certificates or other
documentation. Nordic Ecolabelling may require further documentation if there is any
uncertainty about the origin of the raw material.
Recycled plastic
a) Recycled plastic must comprise pre- and/or post-consumer* recycled material
and/or industrial scrap.
b) Recycled plastic must not contain polybrominated biphenyls or diphenyl
ethers, phtalates, organotin compounds, lead, cadmium, mercury or chromiumVI. Impurities up to 100 ppm are, however, permitted. A test of the
recycled plastics is required or documentation that the material comes from
known sources where it has been established that this type of content is
unlikely to occur.
c) Recycled plastic materials used in the sanitary product must be recycled in a
closed loop system** and meet requirements for recycled plastics materials and articles intended to come into contact with foods***.
d) The requirement does not apply to recycled plastic in additional components,
information sheets and primary packaging.
e) If the polymer type makes up 20 % or more by weight of the sanitary product
and the additional components (S+A) substances added to the recycled plastic
material must meet the requirements O3, O4, O5 and O11.
*Pre- and/or post-consumer recycled material is defined in the standard ISO 14 021. **Closed loop systems mean controlled systems where the materials are traceable from source through to the finished recycled material. ***EU commission regulation (EC) No 282/2008 on recycled plastic materials and articles intended to come
into contact with foods and amending Regulation (EC) No 2023/2006.
Documentation from the plastics supplier showing that the requirements have been fulfilled. Appendix 1, form 13 in the criteria document may be used for a) and b). If the
material is not tested, documentation regarding sources and a description of why a test
is not required must be provided
023e_6_0_hearing_Background.docx 59 (93)
Nordic Ecolabelling
27 November 2015
Background document
Background to the requirements
PVC
The requirement prohibiting halogenated polymers remains unchanged from the previous version of the criteria. It is a requirement that Nordic Ecolabelling includes in
many criteria where the plastic materials have a short lifetime, and is primarily a requirement that excludes the use of PVC. PVC is probably not relevant in the actual
sanitary products. The requirement ensures that PVC is also not used in the packaging. The key problem areas for PVC are described in Nordic Ecolabelling's background
report on floor coverings67. Below is a brief summary of the environmental challenges associated with the use of PVC.
The environmental impact of PVC is associated primarily with waste management, the
use of additives and dioxin emissions, for example in the production of PVC, plus the use of mercury in the production of the chlorine. According to the report "Hazardous
substances in plastic materials"68 published by the Norwegian Environment Agency in 2013, PVC may have over 50% plasticiser added, of which phthalates remain the most
popular since they are cheap and have solubility parameters that are very similar to the PVC polymer. PVC requires stabilisers to tolerate the temperatures needed to manu-
facture a PVC product (extrusion, injection moulding, etc). These stabilisers may be based on lead, metal mixtures (such as barium-zinc and calcium-zinc), tin or cadmium.
Overall, the environmental impact associated with the production, use and disposal of PVC is steadily reducing, in part due to new knowledge and technical advances.
However, there is every suggestion that problems associated with PVC remain. There are also not good enough controls over PVC imported into the EU and the Nordic region
from other parts of the world, which is not subject to the same European restrictions. For Nordic Ecolabelled sanitary products, which are disposable, there is therefore a ban
on the use of PVC in the products and their packaging.
Additives to plastics and polymers
The report "Hazardous substances in plastic materials"69 was published by the Norwegian Environment Agency in 2013. It was prepared by COWI in cooperation with
the Danish Technological Institute. According to the report, the following "hazardous substances" are relevant for different types of polymer (PVC is not included because
PVC is excluded from use in sanitary products):
LDPE and HDPE: colourants/pigments, flame retardants (cables, electronics).
Chromium oxide might be used as a catalyst (the Phillips method).
PP: antioxidants, colourants/pigments, flame retardants (cables, electronics).
PET: colourants/pigments. Antimony is not mentioned.
PU: flame retardants (relevant in UK) and biocides (methyl fumarate is named as an
example). Mercury may occur as an impurity, as it is used as a catalyst in the production of PU polymers.
67Nordisk Miljömärkning. Om Svanenmärkta Golv, Version 6.0. Bakgrund för miljömärkning 18. November 2014.
http://www.svanemerket.no/for-bedrifter/sok-om-svanemerket/svanens-krav/byggevarer-og-hus/gulv/ (hentet 8. juni 2015) 68 Klima- og forurensningsdirektoratet, Hazardous substances in plastic materials, Cowi, januar 2013. 69 Klima- og forurensningsdirektoratet, Hazardous substances in plastic materials, Cowi, januar 2013.
023e_6_0_hearing_Background.docx 60 (93)
Nordic Ecolabelling
27 November 2015
Background document
The report also goes through specific prioritised substances in plastics. The following additives may be relevant for the plastic types used in sanitary products:
Arsenic and its compounds: used in antimicrobial additives such as 10,10'-
oxybisphenoxarsine (OBPA). OBPA accounts for 70% of the demand for antimicrobials in plastics. Relevant for soft PVC, PUR, LDPE and polyester.
Triclosan (CAS no 3380-34-5): PE, PP, PET, PA, PVC Organotin compounds: here only polyurethane foam and PVC are named as
relevant, as a catalyst and a stabiliser respectively. For dibutyltin used as a catalyst, the normal residue concentration in polyurethanes is 0.05-0.3% (i.e. from 500 ppm).
2,2'-dichloro-4,4'-methylenedianiline (MOCA): most relevant for PU
(crosslinker), but also polystyrene (curing agent)
Diisobutyl phthalate (DIBP): polystyrene Pigments based on lead, chromium, cobalt: relevant for dyed polymers.
The requirements set for additives in polymers prohibit the use of antibacterial additives.
It is therefore not possible to use triclosan or other antibacterial additives. Flame retardants, organotin compounds, phthalates and additives based on lead, chromium and
cadmium that are listed as hazardous are also prohibited in chemical requiremeThe report from COWI also mentions pigments based on cobalt, but these are not
prohibited in this version of the criteria. The crosslinker 2,2'-dichloro-4,4'-methylenedianiline (MOCA) is on the ECHA's Candidate List and thus cannot be used
for that reason. The ban on organotin compounds may make it difficult to find polyurethane foam that meets the requirements, since it is common to use organotin
compounds as a catalyst in production. Requirement O5 sets a limit of 100 ppm for impurities from the raw material production.
Halogenated organic pigments are also prohibited via the requirement concerning "Other excluded substanc there is an exception if the pigments comply with
European Council resolution AP (89) 1 on the use of colourants in plastic materials coming into contact with food.
Antimony/Polyester Antimony trioxide (CAS no 1309-64-4) is not named in the report from the Norwegian
Environment Agency, but it is mentioned in the 2014 report "Everything you (don't) want to know about plastic" by the Swedish Society for Nature Conservation70 as
carcinogenic and as the key catalyst in PET production. EU Regulation No. 10/2011 "Plastic materials and articles intended to come into contact with food" sets a limit for
antimony of 0.04 mg antimony per kg of food, expressed as migrated antimony. This limit value says nothing about the content of antimony in the actual polyester material.
Of the world's PET production of around 60 million tonnes per year, approximately 65% is used for textile fibre and about 30% for packaging/bottles71. The production
process for PET fibre often uses the catalyst diantimony trioxide (Sb O ). This substance
is used primarily as a flame retardant in plastic materials and textiles, and as a catalyst in 70 Klar, M., Gunnarsson, D., Prevodnik, A., Hedfors, C. og Dahl, U., Allt du (inte) vill veta om plast,
Naturskyddsföreningen, 2014 71 Om PET på Wikipeida.com (august 2012)
023e_6_0_hearing_Background.docx 61 (93)
Nordic Ecolabelling
27 November 2015
Background document
PET production and in pigment. Version 5 of the criteria has a requirement concerning residues of the antimony catalyst in polyester, since antimony is harmful to health, with
the classification Carc 2 (formerly cat 3) and has been risk-assessed as an existing substance in EU 2008 (SE)72. The risk assessment concluded that the classification of the
substance should remain (without environmental hazard classification). The report states that the risk areas that should be further investigated were human and environmental
exposure to pure diantimony trioxide, including in the PET industry. Polyester usually contains antimony in concentrations of 150-350 ppm (mg/kg)73. As part of the EU
Ecolabel's work on criteria for textiles in 2001-2002, information on "best available technology" (BAT) and submissions from the PET fibre industry led to a decision that
260 ppm was a suitable base level for the EU Ecolabel, with a best level of "antimony free". In the EU Ecolabel's criteria for textiles from 2014, the level remains at 260 ppm.
The EU Ecolabel's criteria for absorbent hygiene products does not have a separate requirement for antimony, but antimony trioxide is limited to a maximum of 1000 ppm
through the requirement limiting classified compounds, as mentioned above.
Work on developing alternative catalysts is underway, but Nordic Ecolabelling has no
information on any major successes so far, and the situation will be monitored until the next revision. According to a player in the textile market, there is greater pressure to
phase out antimony in the production of PET bottles than there is on textiles, since PET bottles are used in the food industry. In order to minimise anthropogenic production and
accumulation of and exposure to harmful substances in the ecocycle, Nordic Ecolabelling should continue to set a limiting requirement concerning residues of such substances,
even if the requirement serves primarily as a signal to the industry to maintain a good technical level in the production of PET. Since the content of diantimony trioxide
(Sb O ) in finished PET fibre can vary somewhat, the limit value is set as an average over
a period of one year. In version 6 of the criteria, the limit value is set at 260 ppm, because
experience shows that it is a challenge to find polyester producers that come in below this value.
Polystyrene Polystyrene was introduced as one of the polymers which have specific requirements in
version 5.2 of the criteria. Polystyrene is a thermoplastic with uses that include food packaging74. Polystyrene is produced through the polymerisation of styrene. Styrene is
classified as harmful to health and as an irritant (Xn; R20, Xi; R36/38) and is furthermore placed on the Danish Working Environment Authority's list of carcinogenic substances,
with a limit of 25 ppm in the working environment. An EU Risk Assessment Report (EU RAR) was drawn up for styrene in 2008 and this report has subsequently been evaluated
by the Scientific Committee on Health and Environmental Risks (SCHER). SCHER disagrees with the conclusion in the EU RAR, which indicates that there is no need for
concern in relation to human carcinogenicity, but apart from that SCHER generally agrees with the exposure and effect assessments made. SCHER concludes that – apart
from specific exposure scenarios (boat building, working with styrene containing liquids or styrene based pastes) – there is no need for further information or risk reduction
measures beyond those already being applied for consumers75. The EU Directive relating to plastic materials and articles intended to come into contact with foodstuffs 72 European Union, Risk Assessment Report DIANTIMONY TRIOXIDE, Swedish Chemicals Inspectorate, DRAFT
2008 73 Miljøstyrelsen, Miljøprojekt nr. 892, 2004, Antimon - forbrug, spredning og risiko 74 Informasjon om polystyren på Wikipedia, http://en.wikipedia.org/wiki/Polystyrene 75 SCHER 2008: Risk Assessment Report on Styrene Human Health Part, May 2008.
023e_6_0_hearing_Background.docx 62 (93)
Nordic Ecolabelling
27 November 2015
Background document
(2002/72/EC) sets no limitations on the content of styrene monomers. Based on the above, it is thus not considered relevant to establish limit values for the content of
styrene in sanitary products in the criteria for the Nordic Ecolabelling of sanitary products.
In version 6 of the criteria document for sanitary products are introduced specific
requirements for the manufacture of polyamide (PA) and polyurethane (PUR). Both polyamide and polyurethane used partly as a carrier material in plaster76. Energy
Requirements for PA6 and PA6.6 are taken from Plastics Europe's Ecoprofiles77,78, see Table 4 for values. In these reports, overviews of the manufacturing processes for the
two polymers are given. For PA6 and PA6.6 there is in addition set a requirement regarding emission of nitrogen dioxide to the air from the preparation of the monomers
caprolactam (PA 6) and adipic acid (PA 6.6). This value is taken from the EU Ecolabel requirements for textiles from 201479.
Elastane/Polyurethane Elastane is a polyurethane elastomer. It is not used alone as a textile fibre, but is
incorporated into other materials to make them elastic. The catalyst in the polymerisation may be either special amines or organotin compounds80. Organotin compounds are
highly toxic to both people and animals81, and there is a requirement that polymers must not include organotin compounds.
Elastane can be produced in four different ways: through extrusion, reaction spinning, solution dry spinning or solution wet spinning82. Solution dry spinning is used to produce
94.5% of the world's elastane. This method uses dimethylacetamide (DMAc) as a solvent83. Many other solutions may also be used, including dimethylformamide (DMF)
and nitric acid (HNO3). DMAc was entered onto the Candidate List for REACH in 2012. According to BREF Polymer84, residues of DMAc may be found in the fibre
(< 1% of the fibres' weight) and also in the wastewater from pre-treatment. To ensure the plasticity of the fibre during processing, auxiliary chemicals are added to the fibre.
These auxiliary chemicals contain 95% silicone-based oils and 5% surfactants. High levels of silicone oil have an environmental impact during the pre-treatment of textiles, when
these chemicals are removed. Established manufacturers of elastane fibre are Invista, Hyosung, Asahi Kasei and RadiciSpandex85.
The report "Hazardous substances in plastic materials"86 points out that mercury may be used as a catalyst in the production of PU polymers, but it is unclear whether these
polymer types are relevant to sanitary products. The report states that mercury was 76 Epost korrespondanse med Beiersdorf 7/11-13 77,Eco-profiles and Environmental Product Declarations fo the European Plastics Manufacturers Polyamide 6.6
(PA6.6), Plastics Europe February 2014. 78 Eco-profiles and Environmental Product Declarations fo the European Plastics Manufacturers Polyamide 6 (PA6), Plastics Europe February 2014. 79 COMMISSION DECISION of 5 June 2014 establishing the ecological criteria for the award of the EU Ecolabel for
textile products (2014/350/EU) 80 EU Ecolabels bakgrunnsrapport;"Establishment of ecological criteria for textile products", final report April 1998 81 http://www.miljostatus.no/tema/Kjemikalier/Noen-farlige-kjemikalier/TBT/ (tilgjengelig 18.11.2011) 82 Wikipedia.com:ept 2012) ept 2012) 84 BREF-dokument for polymerer, 2007, er tilgjengelig på følgende nettsted: http://eippcb.jrc.ec.europa.eu/reference/BREF/pol_bref_0807.pdf 85 http://www.textilesintelligence.com/til/press.cfm?prid=440 86 Klima- og forurensningsdirektoratet, Hazardous substances in plastic materials, Cowi, januar 2013.
023e_6_0_hearing_Background.docx 63 (93)
Nordic Ecolabelling
27 November 2015
Background document
formerly used as an antibacterial agent in plastic, but it is not thought to be used any longer. It may, however, occur as a catalyst, and mercury is therefore prohibited in
polymers that form part of Nordic Ecolabelled sanitary products. The report states that new products will typically contain 0.1-0.3% mercury.
In version 6 criteria of the criteria for sanitary products, additional requirements for PUR foams and thermoplastic PUR are introduced in addition to the requirements to elastane.
PUR foam is used in wash cloths and thermoplastic polyurethane used in adhesive plaster. In these product types, a significant amount of PUR can be included. It's
introduced a requirement that the manufacture of PUR shall meet "criterion 2" in EU Ecoabels criteria for Bed mattresses87. This including requirements for biocides,
plasticisers, heavy metals, monomers, organotin compounds, VOC emissions, total chlorine content and blowing agents.
Background to the production energy requirement As mentioned under the RPS, the production of the constituent materials accounts for
the greatest environmental impact from a sanitary product. It is therefore desirable to promote the materials that require least energy to produce and have the lowest GWP
value over their lifetime, in addition to reducing use of environmentally problematic chemicals during production. It is, however, difficult to obtain factory-specific data, and
thus to gain an overview of the variation between manufacturers. The table in Appendix 2 gives information from PlasticsEurope's "Eco-profiles"88 together with GWP values
from version 5 of the criteria for sanitary products. It also includes values for PLA and PHA, which are taken in part from the criteria for the Nordic Ecolabelling of disposables
for food. The GWP figures from version 5 of the criteria are based on various LCA studies with an added uncertainty factor, so that they can be used as default values if it is
not possible to use factory-specific figures. In addition, there are GWP values for HDPE from sugar cane and for fossil HDPE, both produced by Braskem in Brazil. These
figures are taken from Braskem's report "Environmental assessment of Braskem's bio-based PE resin"89. The report states that the use of fossil energy in the production of bio-
based PE is around 18 MJ. Note that the report states that over 80% of the production energy is from renewable energy sources, which gives much higher energy consumption
than is the case with fossil energy. In comparison, a figure of approx. 85 MJ fossil energy is given for the production of fossil HDPE. This figure includes the inherent energy in
the fossil raw material that is used in the production of the actual HDPE polymer. Both types of HDPE share the same polymerisation process, such that the energy
consumption at this process stage is similar.
According to the report "Eco-profile and EPD of HDPE, LDPE and LLDPE"90 from
PlasticsEurope, there are 90 polythene factories in Europe, of which 64 are members of PlasticsEurope. Of these, 52 factories took part in the survey, which represents 74% of
the production capacity in Europe. According to the report, the production of monomers (and co-monomers) requires the most energy over the course of production.
For HDPE, LDPE and LLDPE, monomer production accounts for 91.3%, 88.3% and 87 COMMISSION DECISION of 23 June 2014 establishing the ecological criteria for the award of the EU Ecolabel for bed mattresses (notified under document C(2014) 4083) (2014/391/EU) 88 Plastics Europe har laget «Eco-profiles» for ulike materialer, finnes på siden: http://www.plasticseurope.org/plasticssustainability/eco-profiles.aspx 89 Environmental assessment of Braskem's biobased PE resin, November 2013, sammendrag av rapport laget av
E4tech og LCAworks. 90 Eco-profiles and Environmental Product Declarations of the European Plastics Manufacturers, High-density
Polyethylene (HDPE), Low-density Polyethylene (LDPE), Linear Low-density Polyethylene (LLDPE), Plastics Europe,
023e_6_0_hearing_Background.docx 64 (93)
Nordic Ecolabelling
27 November 2015
Background document
92.0% respectively of the total process energy. The corresponding values for GWP are 81.3%, 78.0% and 82.0% for monomer production. The report states that the polythene
factories tend to be located near the refineries that produce the monomers. In correspondence, PlasticsEurope91 states that some polymer producers produce their own
monomers, others sell the monomers and some buy in all or parts of their monomer need. The raw material that makes up the cracker (naphtha, propane, etc) also depends
on whether it is financially viable to sell any raw material produced in-house or rather to buy in the raw material for the cracker from external suppliers. Against this background,
there is little steerability for Nordic Ecolabelling to set requirements concerning energy consumption in monomer production, which is a substantial contributor to the overall
energy consumption for the polymer production. The EU's Joint Research Centre is currently drawing up a BAT report for Large Volume Organic Chemicals, which includes
cracking. There is a draft from 2014, and Nordic Ecolabelling will be monitoring this work.
Although the greatest energy consumption in the traditional fossil-based polymers comes in the production of the monomer, the choice has been made to set a requirement only
for the later polymerisation. The reason that the monomer production is excluded is the lack of steerability, as outlined above. As mentioned before, there is also a lack of data
for the production of polymers, but because there is greater steerability here, Nordic Ecolabelling would like to see the industry reporting factory-specific figures. The
proposed requirement level is based on data in the EU's BAT report on polymers from 200792, see Table 4. The figures in the BAT report are from 1999, and where data has
been reported for several parts of the industry, the best part has been chosen. The figure for polyolefins, for example, is an average from the best 50% of the factories.
The BAT report gives no exact value for PP, but compares it with the other polyolefins. Other averages for polymerisations are figures from the International Energy Agency
(IEA) in 200993 which show some higher values than in the BAT report, with 3.14 MJ/kg for HDPE, 5.96 MJ/kg for LDPE and 2.27 MJ/kg for PP as best practice in Europe.
The report states that, in considering the average figures for European production, there is energy efficiency potential of 30-40% for polyolefin production. Another source is a
PhD thesis94 from Utrecht University in the Netherlands, whose energy figures are based on studies from the mid-1990s. Here the total energy (electricity, steam and fuel) is 2.3-
3.9 MJ/kg for different polyolefins, 2.4 for PS and 19.9 for PUR. The variation for the polyolefins depends on whether the polymerisation takes place in a gas phase, slurry
phase or in a suspension. The industry body PlasticsEurope has drawn up Eco-profiles95 for the various polymers, based on data from its members. The figures are from 2005 up
to 2013 and are presented as an "Analysis by type of useful energy for polyolefin production process per 1 kg of product". Any energy production within the process,
such as the production of steam, is deducted. Values from the named sources are also included in the table, but it is the figures from the BAT report that have been used as the
basis for setting a requirement limit, where data is available. According to the BAT 91 Epostkorrespondanse med Plastics Europe 7/7-15 92 EU's Joint Research Centre. Reference Document on Best Available Techniques in the Production of Polymers, August 2007. http://eippcb.jrc.ec.europa.eu/reference/ (hentet 27. juli 2015) 93 IEA, International Energy Agency. Tracking Industrial Energy Efficiency and CO2 Emissions. 2007. https://www.iea.org/publications/freepublications/publication/tracking_emissions.pdf (hentet 27. juli 2015) 94 Jootsen, Lois. The Industrial Metabolism of Plastics - Analysis of Material Flows, Energy Consumption and CO2
Emissions in the Lifecycle of Plastics._Ph.D theses._2001._Universiteit Utrecht. http://dspace.library.uu.nl/bitstream/handle/1874/751/full.pdf (hentet 27. juli 2015)
profiles.aspx(hentet 27. juli 2015)
023e_6_0_hearing_Background.docx 65 (93)
Nordic Ecolabelling
27 November 2015
Background document
report, the polymerisation to EVA requires more energy compared to polymerisation to LDPE. However, due to lack of more information, the same energy limit is proposed for
EVA and LDPE to the hearing.
Table 4. Energy consumption from the polymerisation of different polymers,
taken from the EU's BAT report, a PhD study and PlasticsEurope's Eco-profiles,
plus the proposed requirement limit.
Energy consumption,
Proposed
BAT report
req. limit in
, PhD study,
profile, MJ/kg
720 kWh/t* (2.6 MJ/kg)
580 kWh/t* (2.1 MJ/kg)
570 kWh/t* (2.1 MJ/kg)
1.08 GJ/tonne** (1.1
0.9 (general purpose
1250 kWh/t*(4.5 MJ/kg)
4,400-8,600 MJ/kg**
7.6 (amorphous PET
polymerisation to
EU's BAT report by Joint Research Centre: Reference Document on Best Available Techniques in the Production of
Polymers, August 2007
* Average top 50%, EU's BAT report
** European average, EU's BAT report
*** Staple fibres, EU's BAT report
PhD study: Jootsen, Lois. The Industrial Metabolism of Plastics – Analysis of Material Flows, Energy Consumption and CO2 Emissions in the Lifecycle of Plastics.
Background to requirements
When calculating production energy, the focus is on the actual polymerisation. The
production of the monomer and further processing of the polymer are thus not included.
polymerisation of the various types of PE from ethylene polymerisation of PP from propylene polymerisation of PS from styrene polymerisation of PA 6.6 from adipic acid and HMDA (hexamethylenediamine) polymerisation of PA 6 from caprolactam. polymerisation of EVA from ethylene and vinylacetate. polymerisation of PET from terephthalic acid and ethylene glycol polymerisation of polyurethanes (polyether polyols and polyester polyols) from
isocyanates and polyols
023e_6_0_hearing_Background.docx 66 (93)
Nordic Ecolabelling
27 November 2015
Background document
Energy requirements, renewable polymers
For renewable polymers, such as PLA and sugar cane-based PE, the polymer producer is
also the producer of the monomer96, giving steerability over traceability as far as the process stage. A life cycle analysis of PLA from 201597 shows that the production of
lactic acid makes the greatest contribution (around 50%) to the use of fossil energy in the production of PLA. The LCA stresses that the production of PLA is still in its infancy
compared with traditional petroleum-based polymers. There is therefore significant potential for improvement of the process, something which applies generally for
biopolymers. To prevent the use of biopolymers with unreasonably high energy consumption, there is therefore a requirement that fossil production energy must not
exceed 50 MJ/kg.
Based on a search of the literature on renewable polymers, the criteria document for the
Nordic Ecolabelling of disposables for food98 sets a limit value of 50 MJ/kg of polymer. It should be mentioned that the literature search produced data almost exclusively for
fossil energy rather than renewable energy. Nordic Ecolabelling is concerned about total energy consumption, but chooses here to set a minimum requirement for energy
consumption in the production of biopolymers in order to gain knowledge about the production process, with a view to developing requirements for biopolymers in later
versions of the criteria.
The background document for the Nordic Ecolabelling of disposables for food99 refers
to several studies which conclude that renewable raw materials are beneficial compared with fossil raw materials in terms of energy consumption and the greenhouse effect. The
background document shows that renewable raw materials have two benefits over fossil raw materials. Energy content in the renewable raw material can be discounted from the
total energy balance sheet, since this energy is renewable. This also brings a benefit when calculating the impact on the climate of a material or product, since renewable raw
materials in themselves do not contribute to increased emissions of greenhouse gases. It is common with fossil raw materials to include the energy content in the raw material in
the energy balance sheet. In addition, the use of fossil raw materials contributes to greater emissions of greenhouse gases, since they are not part of the natural carbon
ecocycle. Note that the CO contribution from renewable materials is often deducted
from the GWP calculation in a cradle-to-gate analysis, since renewable materials are
considered to save the atmosphere from CO until the material is burned. This gives a
skewed picture of the CO balance sheet for disposable products, since these are only
used once before releasing CO back into the atmosphere.
About bioplastics/biopolymers
The bioplastics market has previously been dominated by plastic materials made for composting. In recent years, there has been a major increase in bioplastics which have
the same properties as fossil plastics, are not compostable, are included in recycling systems and are able to directly replace fossil plastics. See the overview of different
bioplastic types on the website of European Bioplastics100. There are around 115
96 Epostkorresponanse med Braskem 8/7-15. 97 Vink, E. And Davies, S., Life Cycle Inventory and Impact Assessment Data for 2014 Ingeo Polylactide Production,
Industrial Biotechnology, vol 11, no 3, June 2015 98 Nordisk Miljømerking, Om svanemerkede Engangsartikler til fødevarer, Baggrund for miljømærkning version 1, Version 1 21.mars 2012. 99 Ibid 100 European Bioplastics hjemmeside:(9/2-15)
023e_6_0_hearing_Background.docx 67 (93)
Nordic Ecolabelling
27 November 2015
Background document
producers in the market who play a significant role in bioplastic production capacity101. In 2013, Asia accounted for the most bioplastic production102. The same trend can be seen
in biopolymers generally; that there is a greater focus on producing "traditional" polymers, but replacing the fossil raw material with renewables. For some material types,
one way forward is to apply a mass balance approach.
The overall environmental gain from biopolymers will depend on the production method
and inputs (renewables or fossil in production), transport and the refining process. The figures will change with increased volumes of biopolymers and a greater environmental
focus in production. According to a 2014 report by the Norwegian environmental foundation ZERO on bioplastics103 various life cycle analyses (LCA) of emissions from
different bioplastic products have been conducted. ZERO states that it primarily found studies on the biodegradable bioplastic variants, and not the newer non-degradable
bioplastic variants such as bioPET. The report quotes PlasticsEurope in stating that sugar cane-based ethene has the greatest potential for the reduction of greenhouse gas
emissions. Globally, the largest volumes of bioethanol are currently produced from sugar cane in Brazil, and this can in turn be used as a raw material for products such as bioPE
and bioPET. In 2014, PE International launched a new LCA database for bioplastics104.
Use of bioplastics and biopolymers today:
The report "Market study on Bio-based Polymers in the World"105 estimates that the production capacity for bio-based polymers will rise from 3.5 million tonnes in 2011 to
12 million tonnes in 2020. It is bio-based PET, PE/PP polymers and the new polymers PLA and PHA that are showing the strongest market growth. The greatest investment is
expected in Asia and South America. The most dynamic development is expected in the area of "drop-in" polymers, which are chemically similar to their petrochemical
counterparts, such as PET, PE and PP.
Examples of the use of bioplastics and biopolymers today:
Ecover (British manufacturer of cleaning products) uses renewable PE combined
with recycled plastic in its packaging106.
Serla uses "Green PE" from Trioplast107 as packaging for most of its product
groups108. Trioplast purchases the plastic from Braskem, which produces Green PE from sugar cane.
Coca Cola Norway uses only PlantBottleTM bottles. PlantBottle is a mineral
water bottle made from PET plastic, with up to 22.5% of the material extracted from plants and up to 50% recycled plastic. The PET bottle is manufactured in a chemical reaction between oil-based terephthalic acid (70%) and plant-based
101 European Bioplastics hjemmeside, Liste over «bioplast bedrif
2-15) 102 European Bioplastics hjemmeside http://en.european-bioplastics.org/market/europebeyond/ 103 Stiftelsen Zero i Norge: Gjerset, M., Arnøy S., Hojem, J. F., Klimaløsning: Bioplast! –Status, barrierer og
virkemidler for fornybar plast, Zero, januar 2014 104 PE Internationals hjemmesider:
(10/4-15) 105 Market study on Bio-based Polymers in the World, Capacities, Production and Applications: Status Quo and Trends
towards 2020, Nova Institute, Version 2013-07. 106 Nettsiden til Ecover: http://www.the-splash.co.uk/articles/plant-plastic 107 http://www.triogreen.se/ 108 Eksempler på produkter på Serlas hjemmesider: http://www.serla.no/products?product_category=All
023e_6_0_hearing_Background.docx 68 (93)
Nordic Ecolabelling
27 November 2015
Background document
ethylene glycol (30%), which is currently produced from sugar cane and molasses109. Coca Cola is working with such companies as Procter & Gamble and Heinz to produce 100% plant-based PET bottles110,111.
PEF (ethylene glycol + furan dicarboxylic acid (FDCA)) may become the new
100% renewable alternative to PET (ethylene glycol + terephthalic acid (TPA))112. Avantium (Netherlands), in partnership with a consortium comprising Swire Pacific, The Coca-Cola Company, DANONE and ALPLA, has entered into an agreement worth USD 50 million to conduct an industrial validation of PEF and finalise the planning and design of the first commercial scale plant. They will also be looking to validate the use of second-generation raw materials in the production process.
Elopak has launched new cartons using bioPE113. Tetrapak has launched 100% renewable packaging with LDPE in the barrier and
HDPE in the cap114.
SABIC (a petrochemicals company) recently announced that it is beginning
production of renewable PE and PP at its factory in the Netherlands115,116. The company will use the mass balance system to include various types of bio-raw material in their existing fossil production chain in the naphtha cracker plant. According to contact with SABIC117 the bio-raw material is waste fats and oils. SABIC uses ISCC Plus certification.
Braskem118 lists the following packaging producers as users of Green PE:
Trioplast, Amcor Flexibles, Coveris, Barbier and RKW. According to Braskem, no production adaptations are needed in order to convert with Green PE. In some cases, the producer will add special grade material in order to achieve better properties, while at the same time achieving more than 50 percent renewable materials. On request, the ethanol can be Bonsucro certified and the polymer can have ISCC+ certification. See more details about the certification schemes below.
Cargill produces bio-based polyols (BiOH®)119 that can be used to produce
polyurethane, for example as a foam.
There are many projects focusing on increased use of renewable raw materials in
manufacturing (both first and second-generation raw materials). Here are some examples:
109 Nettsiden til Coca Cola Norge: http://www.coca-cola.no/nordic-corp/cc/no_NO/pages/sustainability/om_plantbottle.html 110 Procter & Gamble Sustainability report, 2012: http://www.pg.com/en_US/downloads/sustainability/reports/PG_2012_Sustainability_Report.pdf 111Nyheter fra nettsiden Packnews:
packaging-materials 115 Nettsidene til SABIC: http://www.sabic.com/europe/en/news-and-media/news/2014/20140423--SABIC-
launches-new-renewable-polyolefins-portfolio 116 http://www.bioplasticsmagazine.com/en/news/meldungen/Sabic-launches-renewable-polyolefins.php 117 Epostkorrespondanse med Sabic 10/2-15. 118 Epostkorrespondanse med Martin Clemensha, Braskem 119 http://www.cargill.com/products/industrial/foam/
023e_6_0_hearing_Background.docx 69 (93)
Nordic Ecolabelling
27 November 2015
Background document
Närodlat plast120 (2014-): A joint venture in Sweden looking at the potential for
bioplastics from the forest. Borealis, Trioplast and Tetra Pak are involved.
Skog22121 (2015-): Norwegian strategy process to increase research, development,
innovation and knowledge dissemination within the forest-based value chains. Launched in 2015.
Hållbar Kemi 2030122: The vision is to encourage manufacturers in Stenungsund
to switch to the use of renewable raw materials and increase recycling.
The Bioplastic Feedstock Alliance (BFA)123: Formed in November 2013 to
increase awareness of the environmental and social benefits of potential raw materials for bioplastics. Members include Coca Cola, Heinz, Nestle, Nike, P&G, Unilever and WWF. Supports the sustainable use of raw materials.
Forum for renewable plastics initiated by the ZERO Foundation in Norway
(2014-)124: Development of skills and information, establishment of collaborations, development projects.
Biomass resources are limited and a switch from fossil raw materials to renewable raw materials based on biomass could have major negative consequences for the
environment, for example in the form of loss of biodiversity due to direct and/or indirect changes in land use. Greater demand for biomass could thus lead to
deforestation, which in turn contributes to global warming. This would most likely be associated with plantation production primarily in South America, Asia and Africa. There
is a strong focus on developing second-generation biopolymers, whose raw materials do not compete with food production, for example making use of waste products from
sugar production (bagasse) or using wood instead.
There are, however, also arguments in favour of first-generation bioplastics over second-
generation bioplastics. The industry organisation European Bioplastics points out that of the 13.4 billion hectares of land globally, 37% is used for agriculture125. Of this 70% is
pasture and 30% is arable land. This 30% arable land is used mainly for food and animal feed (27%) and for materials (2%, including bioplastics) and energy crops (1%). Only
0.006% of global agricultural land is used to grow raw materials for bioplastics, compared with the 98% that is used for food, feed and pasture. There is still plenty of farmland
available for production, even in the EU. If the whole world's plastic production were to be replaced with bioplastics, this would account for 7% of the world's agricultural land. It
is also thought-provoking that around a third of the food produced is lost or discarded. Independent third-party certification systems can ensure socially, environmentally and
economically sustainable production of bioplastics.
In an article in Bioplastics Magazine126 from 2011, the nova-Institute discusses the pros
and cons of using first and second-generation bioplastics. The main point is that the technical solutions for first-generation bioplastics are more developed. Within the EU
120 www.processum.se/sv/spprocessum/media/nyhetsarkivet/1213-naerodlad-plast-aer-det-moejligt /2-15) 122 http://www.kemiforetagenistenungsund.se/index.php 123 http://www.bioplasticfeedstockalliance.org/ 124 http://blogg.zero.no/2014/06/bli-med-i-forum-for-fornybar-bioplast/ 125 Hjemmesiden til European Bioplastics, FAQ Aug 2013: http://en.european-bioplastics.org/press/faq-bioplastics/#competition 126 Carus, M. and Raschka, A., Agricultural Resources for Bioplastics, Feedstock for bio-based plastics today and
tomorrow, 1st and 2nd generation crops: Pros and cons, bioplastics Magazine [06/11], vol 6
023e_6_0_hearing_Background.docx 70 (93)
Nordic Ecolabelling
27 November 2015
Background document
there is still vacant farmland and this is best used for crops that have been developed for maximum yield over many many years, plus the infrastructure is already in place. Crops
for industry can also serve as an emergency reserve for supply of food and feed. The article also points out that there is enormous potential to free up farmland through more
sustainable use of biomass, for example by reducing meat in the diet and cutting food waste.
Certification of sustainable use of renewable raw materials The European CEN Technical Committee CEN/TC 411127 is working on standards for
bio-based products. The following five working groups have been set up:
WG1: Terminology WG2: Bio-solvents WG3: Bio-based content WG4: Sustainability criteria, life cycle analysis and related issues WG5: Certification and declaration tools.
There are currently no published standards under WG4 and WG5. WG5 is developing standards for the sustainable use of renewable raw materials. There are, however, good,
established systems that could be used in this area, according to the nova-Institute. These include ISCC, RSB, RSPO, PEFC, FSC and Bonsucre, all of which are described in brief
Certification schemes for products:
ISCC ISCC stands for "International Sustainability & Carbon Certification System for Biomass
and Bioenergy". The standard was developed by private players with support from the authorities and is approved as the basis for fulfilling the sustainability criteria in the
Renewables Directive.
ISCC PLUS is a certification system for food and feed which also covers technical and
chemical applications, such as bioplastics, and was introduced in 2012128. ISCC Plus 202 deals with sustainable production areas, ISCC Plus 203 covers traceability and ISCC Plus
204-01 relates to mass balance.
RSB (Roundtable on Sustainable Biofuels)129 is a multi-stakeholder initiative set up by the
Ecole Polytechnique Federale de Lausanne (EPFL) in 2007 to develop standards for the sustainability of biofuels. The goal is to achieve global consensus on the principles and
criteria for sustainable production of biofuels. RSB aims to create a tool that consumers, political decision-makers, businesses, banks and other players can use to ensure that
biofuels live up to the promise of sustainability. The first version of the criteria was approved and published on 12 November 2009, and is based on 12 consolidated
principles for sustainable production.
127 Hjemmesidene til CEN:
E56EB230DDAA05D6F2CE70#1 128 ISCCs hjemmeside(10/4-15) 129 Round Table on Sustainable Biofuels, URL:
023e_6_0_hearing_Background.docx 71 (93)
Nordic Ecolabelling
27 November 2015
Background document
Certification schemes for renewable raw materials:
RSPO (Roundtable on Sustainable Palm Oil)130 was set up by organisations involved in
the whole supply chain for palm oil. The standard comprises eight principles and 39 criteria for sustainable palm oil production. The criteria cover social, economic,
ecological and general aspects. There is considerable interest in the scheme and several businesses have been granted certificates.
RTRS (Roundtable on Responsible Soy)131 is an initiative established by players from the whole production and distribution chain for soya oil. Consumer interests are also
represented. The aim of the standard that has been developed is to promote soya produced in an economically viable way, but also on a socially just and environmentally
sustainable basis. The first version of the criteria was approved and published on 10 June 2010. The criteria are based on five general requirements concerning the sustainable
production of soya. The majority of RTRS certified soya comes from Brazil (60% by weight of a total 1.3 million tonnes in 2014) and Argentina (32% by weight), according to
information on the organisation's website (as at 28 July 2015). Other producer countries are Canada, China, Paraguay and India. RTRS permits the use of genetically modified
Bonsucro132 (formerly the Better Sugar Cane Initiative, BSI) is a collaboration between a
number of stakeholders, including sugar cane producers, investors, dealers and NGOs. The aim is to develop international guidelines that define the sustainable production and
processing of sugar cane. The initiative includes principles and criteria on environmental, economic and social issues. The first version of the criteria was approved and published
on 27 June 2010. The criteria are based on five general principles for the sustainable production of sugar cane and products based on sugar cane. BSI has also developed a
Chain of Custody standard that is intended to ensure full traceability along the whole supply chain from raw material delivery to the mill onwards. According to the website,
around 4% of the world's sugar cane production is certified (information on website 28 July 2015). The website gives no information on whether genetically modified sugar cane
is approved for use.
FSC133 and PEFC134 are the two increasingly dominant certification schemes for
sustainable forestry. Although there are a number of differences between the schemes, both are considered by Nordic Ecolabelling to be at the forefront in setting standards
and steering towards more sustainable forestry. Neither of the schemes permit the use of genetically modified trees.
Background to the requirements for biopolymers
To ensure sustainable use of renewable polymers and to prevent a switch from fossil-
based polymers to renewable polymers causing greater or different environmental problems, requirements have been set for the sustainable production of the raw material
and for energy use in the production of the renewable polymer. The desire is that the cultivation of the raw material must be certified to the requirements Nordic Ecolabellings
sets of standards, certification systems and certification bodies, see Appendix 3. Nordic Ecolabelling's raw materials group has assessed the standards for RSOP and RTRS and
130 Roundtable on Sustainable Palm Oil, URL: http://www.rspo.org 131 Roundtable on Responsible Soy Association, UR131 Forest Stewardship Council, URL: 132 Bonsucro: URL: http://www.bonsucro.com/ 133 Forest Stewardship Council, URL: http://www.fsc.org 134 Programme for the Endorsement of Forest Certification, URL: http://www.pefc.org/
023e_6_0_hearing_Background.docx 72 (93)
Nordic Ecolabelling
27 November 2015
Background document
see that they in today's versions do not fully meet Nordic Ecolabelling's requirements concerning sustainability labels.
It is, among other things, unclear whether the standards go beyond legislation, particularly in relation to international conventions. Both schemes have absolute
requirement, but the possibility of exceptions to these are given. In addition, for RTRS it is not found claims that safeguard protected areas and RSOP allows the creation of
plantations on peatlands which are an important as carbon sink.
Since the production of these plant raw materials currently has major environmental
consequences, Nordic Ecolabelling takes a strict line when it comes to these two raw materials and wants to set requirements that are as stringent as possible within the
framework of the respective product groups. In the product groups where there are alternative raw materials and there is good steerability to exclude these without
experiencing any "Burden Shift" Nordic Ecolabelling wishes to exclude palm oil and soya oil from use in those products. This is reason why neither palm oil nor soya oil can
be used in Swanlebelled Candles. In product groups where there are no alternatives and/or no steerability to avoiding these raw materials, Nordic Ecolabelling wishes to set
requirements that are as stringent as possible. This is to ensure that the most eco-friendly alternative is used in Nordic Ecolabelled products. In this case, Nordic Ecolabelling
assess that RSPO and RTRS, plus their associated traceability systems, are the best tools available and will therefore be setting requirements that the raw materials are certified
after these schemes. The precondition is that there is full traceability with physical separation of the certified raw materials. The RSPO and RTRS schemes are both moving
in the right direction, and Nordic Ecolabelling will be monitoring their development, with a view to potentially approving and using them in all types of products at a later
The background to the setting of these requirements for renewable polymers is described
in more detail in the Nordic Ecolabelling criteria for disposables for food135. In the criteria for disposables for food, there is also a requirement that prohibit the use of
genetically modified organisms (GMO) in the cultivation of the raw materials. Nordic Ecolabelling is critical about the use of many types of GMO, including those that are
pesticide tolerant. A requirement to use non-GMO-based raw materials would, however, be too strict for the producers of the polymers. The availability of GMO raw materials
depends on which plant is being cultivated. Braskem reports that it does not use genetically modified sugar cane, since it is not available in Brazil, but most of the maize
produced in Canada for PLA is genetically modified. The judgment has so fare been made that in these criteria it is more important to promote the use of renewable raw
materials in sanitary products, and there is therefore no requirement concerning genetic modification. Nordic Ecolabelling would like feedback on whether these requirements
are too strict in this version of the criteria, and whether this inhibits the use of renewable polymers.
Recycled plastics
According to a Danish plastics recycling company136, their recycled plastic can be tested
in accordance with the RoHS Directive for cadmium, lead, mercury, chromium VI, polybrominated biphenyls and polybrominated diphenyl ethers. They can detect
135 Nordisk Miljømerking, Om svanemerkede Engangsartikler til fødevarer, Baggrund for miljømærkning version 1,
Version 1 21.mars 2012 136 Epostkorrespondanse med bedriften Aage Vestergaard Larsen A/S, Danmark, 25/4-14
023e_6_0_hearing_Background.docx 73 (93)
Nordic Ecolabelling
27 November 2015
Background document
quantities down to 100 ppm. The test is not conducted on a routine basis, but only in conjunction with specific deliveries. The company stresses that the equipment is
extremely expensive and they do not know of any other plastics recyclers that can test the material in this way. According to the company, it is possible to pack diapers, for
example, in recycled PE foil. It can be a challenge to procure enough PE of foil quality, if it needs to be a natural colour, which would be the case if the foil had to be printed on.
According to the producer, it is possible to use 100% recycled plastic for foil. The company uses only industrial waste (not post-consumer) and it rarely finds traces of the
impurities mentioned above. If anything does appear, it tends to be brominated flame retardants. Version 6 of the criteria nevertheless contain a requirement concerning
content of cadmium, lead, mercury and chromiumVI, phtalates, organotin compounds plus flame retardants, since these may occur in post-consumer plastics. The limit value
for several of the substances is 1,000 ppm in RoHs Directive (Restrictions of Hazardous Substances) which applies to electrical and electronic products, except for cadmium
where the limit is 100 ppm. If the recycled plastic material contain 1.0 % by weight or more related to the sum of the sanitary product and additional components also O24
Part A (Polymers/Plastics materials constituent substances) must be met.
7.5.7 Superabsorbent polymers
All superabsorbent polymers must meet O31. If superabsorbant polymers accounts for
5.0 % by weight or more of (S+A) requirement O32 must also be fulfilled. If renewable
feedstock for superabsorbent polymers makes up 20.0 % by weight or more of (S+A) the renewable raw materials must meet requirements O33.
Superabsorbent polymers (SAP), residual monomers and extracts
Acrylamide (CAS no. 79-06-1) must not be used as a monomer.
Superabsorbents polymers (SAP) may contain a maximum of 400 ppm residual
monomers (the total of unreacted acrylic acid and crosslinkers) that are subject to a
classification requirement and have been allotted the risk or hazard phrases specified in
requirement O3, Table 2. SAP may as a maximum contain 5.0 % by weight of water-soluble extracts. Water-soluble extracts in SAP: monomers and oligomers of acrylic acid with lower molecular weight than SAP, and salts.
Information on sampling, methods of analysis and analysis laboratories is provided in Appendix 2.
The manufacturer must document the composition of the superabsorbent polymer by
means of a product safety data sheet which specifies the full name and CAS number
and the residual monomers contained in the product classified in accordance with the
above requirement and the quantities thereof. The manufacturer must specify the quantity of water-soluble extracts in the superabsorbent. The methods of analysis must
be described and the laboratories responsible must be stated. Appendix 1, form 14 in
the criteria document may be applied. The sanitary manufacturer must inform the
producer of the superabsorbent on which paragraphs to fill in.
Superabsorbent polymers, additives
Additives in superabsorbent materials must fulfil requirements O3-O11.
Documentation as specified in the requirements listed above. Duly completed and
signed Appendix 1, form 2, 3 and 4 in the criteria document. The sanitary manufacturer
must inform the producer of the superabsorbent on which paragraphs to fill in.
023e_6_0_hearing_Background.docx 74 (93)
Nordic Ecolabelling
27 November 2015
Background document
Superabsorbent polymers based on renewable raw materials
Renewable feedstock must fulfil relevant requirements O29.
If a mass balance used as approach to calculate the proportion of renewable feedstock
in superabsorbent polymers the calculation must be certified by an independent third
party or standard that lives up to the guidelines for mass balance sheets given the
Renewables Directive (2009/28 / EC).
Documentation as specified in the requirements listed above. Certificate showing the
percentage of renewable raw material in the superabsorbent if it is less than 100 %.
Background to the requirements
A superabsorbent is a material that, according to EDANA's website,137 can absorb up to
300 times its own weight in water, and retain that liquid thereafter, making it ideal for use in absorbent sanitary products. The superabsorbents currently used in absorbent sanitary
products are mainly sodium polyacrylate, which is a superabsorbent polymer. This is under development in a host of variants, e.g. through modification of the chain or the
addition of different side groups to give new properties. Superabsorbents from renewable raw materials are mentioned later in this section. According to EDANA138,
superabsorbents based on substances including polyacrylamide copolymers, ethylene-maleic anhydride copolymers and polyvinyl alcohol copolymers139 are not used in sanitary
products. The use of acrylamide as a monomer has, however, been specifically prohibited in these criteria. The fact that it is not permitted as any other additive to superabsorbents
is covered in the additives requirement, with reference to the chemical requirements.
The world's largest manufacturers of SAP are Nippon Shokubai, BASF, Evonik,
Sumitomo Seika, San-Dia Polymers, LG Chemical and Taiwan Plastics140. Of these, BASF, Nippon Shokubai, Evonik Industries and Sumitomo Seika Europe are members
of EDANA's association for SAP manufacturers141. These all manufacture SAP in Europe for sanitary products.
Below is a description of the production process for sodium polyacrylate-based SAP.
Production of SAP
A general overview of how sodium polyacrylate is made can be found on EDANA's website (see reference above). The polymerisation includes the addition of a copolymer
which has more functional units than the acrylic acid, so that it can bond to more molecules and help to form a three-dimensional structure. The free-radical
polymerisation is exothermic.
According to information from BASF142, the polymer in the surface of the particles can
be further crosslinked to give the material specific absorption properties such as retention under higher pressure. (Tetraallylethoxy) ethane and 1,1,1-Trimethylolpropane-
137 Nettsidene til EDANA, beskrivelse av SAP-produksjon
(6/5 2015) 138 Epostkorrespondanse med Pierre Conrath 21/4-15 139 Nettsiden til Transparency Market research:
5-15) 140 NONWOVENS INDUSTRY monthly trade magazine: http://www.nonwovens-industry.com/issues/2013-11-
01/view_far-east-report/a-look-at-the-top-superabsorbent-polymer-makers-in-the-world/ 141 Fra EDANAs hjemmesider: «SAP Producers Committee, Info Sheet (March 2014)". Tilgjengelig på siden:
(23/3-15) 142 Foredraget "Superabsorbent Polymers" av Mark Elliott, Product Development Scientist for SAP, BASF
Aktiengesellschaft, tidligere publisert på nettsidene til BASF. Nå kan den blant annet finnes på denne nettsiden:
023e_6_0_hearing_Background.docx 75 (93)
Nordic Ecolabelling
27 November 2015
Background document
tricrylate (TMPTA) are customarily used for crosslinking. The background document to version 5 of the criteria also mentioned other examples of monomers that can contribute
to crosslinking: glycerol propoxy triacrylate, triallylamine, divinyl toluene, polyethylene glycol monoallyl ether, ethylene glycol, di- or polyglycidyl ether. The manufacturers
reveal very little about the crosslinkers they use and it seems that virtually anything that can react with carboxylic acid has been tried. Very small quantities are used and analysis
is therefore difficult according to Fredric L. Buchholz, former research leader at Dow Chemicals, writing in an article in Chemistry in spring 2005143.
According to information from BASF (see earlier reference) polymer additives include surfactants which help the gel to break down into smaller units. They may also increase
"wetting" of the surface in order to improve swelling speed. Antioxidants are added to retain the whiteness of the SAP and reduce aging. Thermal or redox initiators reduce
residual monomer levels, which is important in sanitary products that come into contact with skin. Fumed silica may be added as an anti-caking agent144.
Extractives from SAP are low-molecular compounds that can be extracted from the polymer in the event of a fluid surplus. Residual monomers from SAP are also measured
and these might for example be crosslinkers that were not taken up in the polymer network during polymerisation. The major manufacturers have no information on
residual monomer content or extractives on their websites. The requirements for these have been retained at the same level as before.
Risk assessment of acrylic acid residues EDANA's report "Risk assessment of acrylic acid in absorbent hygiene products" from
2008145 states that SAP contains a small amount of unreacted acrylic acid and its neutralised form sodium acrylate as residual monomers. The report shows that in a
typical diaper with a pH of 6.5, around 99% of the residual acrylic acid will be in the form of the salt sodium acrylate. The proportion of sodium acrylate rises from 84.6% to
99.8% from pH 5 to pH 7. The report gives examples of acrylic acid/sodium acrylate residues, with 730 ppm as the highest value.
Acrylic acid has the CAS no. 79-10-7 and has a harmonised classification in ECHA of: R10, Xn with R20/21/22, C: R35 and N with R50 (to date). Classification is not
necessary at concentrations of < 1%. EDANA's report (referenced above) refers to a 2002 risk assessment of SAP by the EU, which showed that long-term exposure to
acrylic acid at 1% (10,000 ppm) does not result in treatment-related signs of irritation. Acrylic acid is not considered to be sensitising.
Sodium acrylate has the CAS no. 7446-81-3 and does not have a harmonised classification in the ECHA database (to date). Over 400 registrants have registered
sodium acrylate as H400, 82 have registered no classification and a small number have classified it as H315 and H319 (causes skin and eye irritation).
EDANA's risk assessment is based on an unpublished study from 2006 by H. Schmidt (Evonik Stockhausen GmbH), which looks at skin exposure when using diapers. The
study shows low transference of acrylic acid from the SAP to the skin (0.25 to 2.5%). In the worst case scenario, no more than 1.1% of the total acrylic acid in the SAP is 143 artikkel i Chemistry, våren 2005, http://www.lysac.com/lysac/Chemistry_spring_2005.pdf, (01.01.2007) 144 Kontakt med EDANA, 2010. 145 Schmist, H., Diener, B., Mezaiti, H., Kosemund, K., Risk assessment of acrylic acid in absorbent hygiene products»,
023e_6_0_hearing_Background.docx 76 (93)
Nordic Ecolabelling
27 November 2015
Background document
released. This reinforces the view that very little may come into contact with the skin. EDANA's risk assessment assumed a residual monomer content of 1000 ppm in order
to harmonise with REACH. It was also assumed that these 1000 ppm were pure acrylic acid (and not sodium acrylate). The conclusion from EDANA's risk assessment is that
residual quantities of acrylic acid in SAP pose no risk to consumers, and that a residual monomer content of 1000 mg/kg in absorbent sanitary products is safe. Nevertheless,
Nordic Ecolabelling wishes to maintain the limit value of 400 ppm in order to minimise the content of classified compounds. The focus of EDANA's risk assessment report was
acrylic acid but, as mentioned above, other monomers (crosslinkers) may also be present.
EDANA has developed a number of tests for polyacrylate superabsorbents, which are
listed in the report "Harmonized test methods, Nonwoven and related industries"146. These include "pH of Polyacrylate (PA) Powders", "Residual monomers", "Particle size
distribution", "Free swell capacity in saline", "Fluid retention capacity in saline", "Absorption under pressure", "Flow-rate and density" and "Extractables".
Polyacrylic acid is currently fossil-based and not readily biodegradable. Below are examples of bio-based SAP, both biodegradable and non-biodegradable.
Bio-based superabsorbents ADM (formerly Lysorb®) manufactures BioSAP™147. It is made from renewable raw
materials, it is biodegradable and it is not considered allergenic. The manufacturer says that the product is "hypoallergenic", a term used for something that does not normally
cause allergic reactions, but this term is not medically defined. ADM makes the product from natural or modified starch from grain products such as maize and wheat, and also
from guar gum. The material biodegrades 91.8% in 28 days, and has no residual monomers, according to the website.
To date, bioSAP has had a larger particle size than SAP based on sodium polyacrylate, and has been used in mixes with the latter. Several manufacturers also mention that
bioSAP has a poorer absorption capacity than sodium polyacrylate-based bioSAP. It has not been possible to make contact with ADM to check on the development of their
bioSAP in the revision for version 6 of the criteria.
2014 saw BASF launch a bioSAP of sodium polyacrylate, HySorb B7015 MB, which
counts as renewable based on the mass balance system148. According to an article by BASF from January 2015 on the subject of mass balance149, the renewable raw material is
currently agricultural waste, food waste and certified bio-naphtha. Bio-naphtha comes from oils and organic waste. According to the article, in terms of certification systems,
bio-naphtha is approved under the Renewables Directive, and by the ISCC (see above), RSPO (Roundtable on sustainable palm oil) or equivalent. To verify the renewable
proportion of the actual product, a certification system was developed in partnership with TÜV SÜD. The certification includes all stages in the production of the product,
146 Harmonized test methods, Nonwoven and related industries, 2012: Finnes på EDANAs nettsider
5-15) 147 ADMs nettsider (produsent av biobaserte piopolymerer):
5-2015) 148 Artikkel i Allgemeiner Vliesstoff-Report Nonwovens & Technical Textiles 24. Juni 2014 "HySorb B7015MB –
superabsorbent polymer based on renewable feedstock" Finens på nettsiden
søkt 30/6-15) 149 Klein, D. And Frietsch, S., Identical Product Properties - Chemical Products Based on Renewable Resources
through Use of the Mass Balance Approach, European Polyurethane Journal, January 2015.
023e_6_0_hearing_Background.docx 77 (93)
Nordic Ecolabelling
27 November 2015
Background document
plus an examination of the amount of renewable raw material used on an annual basis. This means that all the constituent substances, including those not present in the end
product (e.g. solvents) are counted over the whole production period. According to contact with BASF150, they offer HySorb with a renewable proportion from 20% up to
100%, according to the customer's wishes. BASF reports that supply of renewable raw material currently exceeds demand.
Research is also underway into the production of sodium polyacrylate-based SAP from renewable acrylic acid151. SAP manufacturers Dow Chemical, BASF, OPX Biotechno-
logies, Myriant and Metabolix152 all have current projects with this focus. According to BASF153, commercialisation probably lies several years in the future, if success is achieved
The limits for the requirements
The limit value for the content of classified residual monomers has been kept at 400 ppm. Many different chemicals may be added in the production of SAP, and so there is
now a stipulation in the requirement that SAP must fulfil the requirement concerning prohibited substances. This is new for version 6 of the criteria.
At the EU Ecolabel's 2nd ad hoc working group meeting for the EU Ecolabel's AHP criteria, the industry commented that there may be traces of acrylamide in SAP.
Acrylamide (CAS no. 79-06-1) is classified as mutagenic and carcinogenic, amongst other things154. It was agreed that only intentionally added acrylamide should be prohibited, and
this was introduced into the criteria. Whether added intentionally or unintentionally, acrylamide is not desirable in SAP for Nordic Ecolabelled products. It is therefore in the
criteria for consultation proposed that acrylamide should be prohibited for used as monomer.
In this revision of the criteria requirements for additives in superabsorbent polymers and renewable raw materials or production of superabsorbent polymers are set if they
contribute to more than respectively 5.0 or 20.0 % by weight, related to the sum of sanitary product and additional components in a package.
7.5.8 Non-woven
Non-woven may be produced from a variety of materials. The requirements concerning
non-woven therefore regularly refer to other requirements in the document.
No specific nominal limit has been set for non-woven. The choice of applicable
requirement depends on how much of the different materials are contained in the sanitary product. The description of which requirements apply to the quantity of
materials can be found under the chapters for the different materials.
150 Epostkorrespondanse med BASF 30/6-15 151 Nettsiden til SpecialChem:(7/5-15) 152 Nettsiden til Chemical & Engineering news:
5-15) 153 Epostkorrespondanse med BASF 2014 154 ECHAs database: http://echa.europa.eu/information-on-chemicals/cl-inventory-database/-/cl-inventory/view-
023e_6_0_hearing_Background.docx 78 (93)
Nordic Ecolabelling
27 November 2015
Background document
Non-woven, general requirement
The manufacturer of the non-woven used must specify the materials (raw materials and
additives) used in the production and state the names of the raw material suppliers. The materials must fulfil the following requirements: Fluff/cellulose pulp must fulfil the requirements in chapter 2.2.1 in the criteria
Cotton must fulfil the requirements in chapter 2.2.4. Viscose must fulfil the requirements in chapter 2.2.5. Polymers as fibre or binder must fulfil the requirements in chapter 2.2.6. Superabsorbents must fulfil the requirements in chapter 2.2.7. If other materials are present and have requirements in these criteria, these must also
be fulfilled. If co-spun fibres are used, the polymer that accounts for the highest
proportion must fulfil the requirements.
The manufacturer of the non-woven used must specify the materials used in
production and state the names of the raw material suppliers. Documentation as in the referred requirements. Appendix 1, form 15 in the criteria document can be used.
Non-woven, chemicals
All additives/chemical products used in the production of the non-woven must fulfil
the chemical requirements O3-O11. A substance that is classified as sensitising with risk phrase H317 and/or H334 can
only be used in the process water if the residue in the non-woven is <0,10 ppm for
each sensitising substance. Other process- and auxiliary chemicals (e.g. spinning additives and machine oils) are
exempt from the requirement. The requirement applies, for example, to CaCO3.
Documentation in accordance with O3-O11. Appendix 1, form 2, 3 and 4 in the
criteria document may be used in addition to form 15.
Background to the requirements O34 and O35
Sanitary products often have one or more layers of non-woven fabric. This is most
commonly made from viscose, polythene (PE), polyester (PET), polypropylene (PP) or fluff/cellulose pulp. Non-woven is also a component of materials such as tape and elastic
side panels, for example in diapers. According to industry organisation EDANA155, the non-woven in absorbent sanitary products is almost exclusively PP spunbond, where 40
years ago it was only viscose that was used. According to non-woven producer Fitesa156, there is market interest in bio-based non-woven. Fitesa has launched co-spun fibre non-
woven with PLA (NatureWorks, Ingeo) as the core and renewable PE from Braskem around the outside. Fitesa sells this primarily in North and Central America, but also in
Europe and other territories. The material costs 50-150% more than today's 100% PP-based material. Fitesa also sells co-spun fibre non-woven with PLA as the core and PP
Non-woven is defined in the standards ISO 9092 and CEN EN 29092. According to the
international industry body for non-woven, EDANA, these two documents give the only internationally recognised definitions of non-woven157. They were published in 1988, and 155 Epostkorrespondanse med EDANA 22/1-15 156 Epostkorrespondanse med Fitesa 26/11-15 157 EDANA, the international association for the nonwovens. What are nonwovens? :
023e_6_0_hearing_Background.docx 79 (93)
Nordic Ecolabelling
27 November 2015
Background document
work is now underway to update the standards to account for developments in the field and better reflect what is meant by non-woven today.
Below is a brief overview of the various production processes for the manufacture of non-woven. The descriptions are taken from EDANA's website158.
General Non-woven manufacture starts with the arrangement of fibres in a sheet or web. The
fibres can be staple fibres packed in bales (wetlaid, airlaid, carding), or filaments extruded from molten polymer granules (spunmelt). Three basic methods are used to form a web,
and non-wovens are usually referred to by one of these methods.
Drylaid: There are two methods of drylaying: carding and airlaying. The fibres are first
"opened" from the bale and placed on a conveyor. Then the clumps of fibres are carded to separate out the individual fibres. In airlaying, the fibres are fed into an air stream after
carding to form a randomly oriented web. The fibre usually accounts for around 85% by weight of airlaid. The remaining 15% comprises various binders. Airlaid without binders
is also available. It may also contain other materials such as superabsorbents, in addition to fluff pulp and binder. Airlaid is used in various types of sanitary product, including
feminine hygiene products, sauna underlays, bibs, etc. Airlaid is a technique where the paper is manufactured using air instead of water. Airlaid typically comprises cellulose
pulp and possibly a binder. The grounds for the requirement of energy consumption in the production of air-laid is described in section 7.5.1.
Spunmelt (also called spunbond when spunmelt is bonded via calendering159): Spunmelt is a generic term describing the manufacturing of non-woven webs directly from
thermoplastic polymers. It encompasses two processes (spunmelt and meltblown) and the combination of both, with no use of binders.
Wetlaid: The principle of wetlaying is similar to paper manufacturing. The difference lies in the amount of synthetic fibres present in a wetlaid non-woven. A dilute slurry of water
and fibres is deposited on a moving wire screen and drained to form a web. The web is pressed between rollers and dried. Impregnation with binders is often included in a later
stage of the process. Binding may occur through binders or the fibres themselves providing chemical binding (with the addition of various polymers), thermal binding or
mechanical binding. Examples of disposable products using the wetlaid technique include paper handkerchiefs, serviettes, gowns, gloves, teabags and gauze.
Finishing: A variety of different chemical substances can be employed before or after binding.
There are also various mechanical processes that can be applied to the non-woven after binding.
Non-wovens can be made conductive, flame retardant, water repellent, porous, antistatic, breathable, absorbent and so on. They can also be coated, printed, flocked or dyed, and
can be combined with other materials to form complex laminates.
For absorbent sanitary products it is common to add surfactants to non-woven to make
it hydrophobic or hydrophilic, since it has to either drain or stop liquids. The require-158 EDANA, the international association for the nonwovens. Formation (om produksjonsprosessen til non-woven)
11-14) 159 Wikipedia.org, søkeord non woven:(6/11-14)
023e_6_0_hearing_Background.docx 80 (93)
Nordic Ecolabelling
27 November 2015
Background document
ments concerning non-woven refer to the material requirements for the constituent materials and to the chemical requirements if chemicals have been used during the
manufacture of the non-woven material. Although the processes associated with the manufacture of non-woven use energy and may generate emissions to water, no
requirements concerning this have been included in this version of the criteria. There are also no requirements concerning process chemicals such as spinning additives.
7.5.9 Material composition
Material composition, renewable and recycled materials
1. Share of renewable and recycled material
One of the following requirements (a, b, c or d) must be fulfilled:
a) The primary packaging and additional components in a pack must comprise
plastic/polymer from renewable feedstock or recycled* materials from
b) The weight of renewable raw materials (excluding fluff, airlaid and paper) in
the sanitary product in a pack must, as a minimum, be at a level equivalent to
the weight of the primary packaging and additional components.
c) The sanitary product in a pack must, as a minimum, comprise material from
recycled plastic at a level equivalent to twice the weight of the primary
packaging and additional components.
d) A combination of a, b and c.
The following condition must be met in order to comply with the requirement:
Y = The weight of primary packaging and additional components, expressed in
grams (g) X = Material from renewable raw materials (excluding fluff, airlaid and paper) in the
sanitary product, additional components and/or the primary packaging, expressed
in grams (g) Z = Recycled material expressed in grams (g) in the primary packaging and in additional components plus two times the amount in the sanitary product.
If the sanitary product is marketed in different pack, the calculation must be made for a
worst case scenario, which in many cases is the smallest pack size (i.e. the pack that
contains the lowest number of products). The material is considered fully renewable if at least 90 % of the raw materials originate from renewable sources.
If it is below 90 %, the actual share shall be accounted for in the calculation, se paragraph 2.
*Recycled material means post- and pre consumer recycled material as defined in the standard ISO 14021.
2. Calculation of the share of renewable raw material in the polymer
If the renewable raw material comprises less than 90 % by weight, the share can be
documented by mass balance. The calculation must be certified by an independent
third party in accordance with a standard that lives up to the guidelines for mass
balance sheets given the Renewables Directive (2009/28 / EC).
The manufacturer of the sanitary product must include a calculation showing fulfilment
of the requirement. Documentation of the actual content of renewable or recycled raw material in the materials on which the calculation is based must also be provided.
Examples of such documentation include information sheet/product data sheet.
023e_6_0_hearing_Background.docx 81 (93)
Nordic Ecolabelling
27 November 2015
Background document
Background to % provisions for renewable and recycled content
The criteria document for disposables for food (as referred to above) examined what
proportion of renewable material it is possible to require for a material to be considered 100 % renewable. For disposable items, a product is considered fully renewable if
renewable raw materials account for 90 % by weight of the product. Inorganic fillers are not included in the calculation, and may account for 20 %. The same approach has also
been applied in the assessment of renewable polymers in version 6 of the criteria for sanitary products.
As mentioned above, it is possible to use 100% recycled plastic in the packaging, but due to the limited availability and variable quality of recycled plastics, Nordic Ecolabelling
accepts that a material can be considered 100% recycled if it contains at least 75% recycled material.
If less than 75% recycled or 90% renewable material is included (excluding inorganic fillers), the actual percentage should be calculated and the requirement must then be
fulfilled as a combination of several materials.
Background to the material composition requirement
The scope to set a well balanced material requirement at product level is limited in the absence of a good functional unit and good information about reference values, with the
added complication of not wanting to affect the performance of the product, coupled with the ambition to formulate a clear and not too convoluted requirement. A require-
ment is now being set for the individual materials that make up the product, in order to ensure that the best in each category are chosen. Version 5 of the criteria also aimed to
promote the use of the best materials. That generation of the criteria contains a require-ment on the product's material composition which could be fulfilled via three alterna-
tives. One of these involved a calculation of the product's contribution to global warming (global warming potential, GWP), expressed in the unit CO eq/kg sanitary
product. To meet the requirement, the product's value had to fall below a certain limit value. The second alternative was that at least 50 % of the weight of the materials in the
sanitary product should come from renewable sources, and the third was that a minimum of 7 % of polymers should be based on renewable raw materials. Although the idea was
good, the calculation of two of the alternatives meant that products containing large quantities of fluff and paper found it easier to fulfil the requirement. This is incompatible
with one of the industry's ambitions, to create lighter products, and this option has therefore been removed in version 6 of the criteria.
The revision of the sanitary products criteria has included a great deal of work on finding a better alternative to the previous requirement. The product group's greatest challenge
in forming good requirements relates to the difficulty in finding a good functional unit. Since it can be difficult to find a good functional unit for just one product type, it is
naturally even more difficult to find a good unit for all the different product types. Nevertheless, Nordic Ecolabelling wishes to reduce the fossil carbon footprint, and to
stimulate increased demand and thus a greater range of materials made from renewable raw materials. Nordic Ecolabelling has therefore chosen to draw up a requirement on
materials from renewable raw materials, despite the arguments against it.
Section 6.2 explains that some materials make more of a contribution to the overall
environmental impact than others in the areas of energy and the climate. It would be desirable to steer manufacturers away from the more environmentally problematic
materials and towards material types that could be considered to have less of an
023e_6_0_hearing_Background.docx 82 (93)
Nordic Ecolabelling
27 November 2015
Background document
environmental impact. Nordic Ecolabelling realises, however, that implementing such a conscious drive is not practical. Version 6 of the criteria therefore adopts a broader
perspective and stimulates a higher proportion of materials from renewable raw materials generally – without abandoning attempts to highlight which material types could be
replaced with something else. In this way, the requirement does not affect the function or performance of the product. It is up to the manufacturer to freely choose which material
types may be considered desirable, as long as the raw material is partially derived from renewable sources. Another way of limiting the fossil carbon footprint is to focus on
recycled materials. However, in the case of sanitary products, which come into close contact with the body, there is concern that recycled materials could contain undesirable
chemical components. Recycled materials must therefore not be incorporated in the products, so that they are suitable for bodily contact. It is permitted for these materials to
occur in the packaging or in the release paper that is removed before the product is used. Nordic Ecolabelling thus wants manufacturers of sanitary products to continue being
able to fulfil the requirement without too great an impact on the function and quality of the product.
Justification of requirement
Why is the requirement based on packaging weight and not simply a clear percentage? If
Nordic Ecolabelling wishes to stimulate a greater proportion of material from renewable raw materials, it is important to:
Act on the basis of the types of material that are available Find out where in the product these renewable materials might be included Find out how much of the product could be made up of the renewable materials
Diapers primarily comprise fluff, polypropylene (PP) and superabsorbent polymers (SAP). The packaging material usually tends to be PE. Fluff is already subject to its own
requirement and by setting up a requirement that cannot be fulfilled by a high proportion of paper and fluff, thick products are not encouraged. Of the various materials involved,
it is most likely that the packaging could be made from renewable raw materials. Packaging could also be recycled.
Under a single brand, the various product sizes often appear to be packaged in the same type of packaging (size and material). The number of products in the pack is often larger
for smaller product sizes. Basing the requirement on the packaging instead of a percentage of the actual product makes it "easier" to fulfil the requirement. In order not
to restrict licence applicants to only being able to fulfil the requirement via the packaging material, it is suggested that it should also be possible to fulfil the requirement via other
materials in the product. In other words, the requirement can be fulfilled via the packaging, but also by one or more types of material in the product.
023e_6_0_hearing_Background.docx 83 (93)
Nordic Ecolabelling
27 November 2015
Background document
As part of the development of the criteria, the following SWOT analysis was drawn up for the material composition requirement:
Strengths:
Weaknesses:
The requirement does not affect the overall material
Bioplastics are not always better for the
composition. I.e. it does not lead to reduced use of
other renewable materials.
Does it actually entail a switch to better
It does not promote heavier products with high
amounts of fluff and paper.
Recycled release paper can only meet the
Gives choice of which material meets the
requirement if it is removed from the product
Does not affect performance.
Tampons always meet the requirement, since
The requirement shows a direction, can be tightened
they contain such large levels of cotton or
using higher levels later.
viscose. This can be adjusted by setting a
If the requirement is not fulfilled via the packaging
special requirement that the outer packaging
material alone, it means that the lighter the
must be renewable or recycled. It is, however,
packaging, the easier it is to meet the requirement
difficult to meet the requirement if we require
with other types of material.
that the packaging around each individual
tampon must be renewable/recycled.
Recycled release paper may be used to meet the requirement, since it is removed before use of the
product.
Opportunities:
Threats:
Drives towards more renewable plastics
Manufacturers might add unnecessary
Drives towards more recycled materials
quantities of material to meet the
requirement. Risk of tight plastic packaging being replaced
with looser paperboard (since it may be easier
to source recycled paperboard).
Materials in cotton buds
Cotton buds, shaft material
The shaft of cotton buds must be made from renewable raw materials, such as wood,
board or polymers from renewable raw materials. If the shaft is made of board, the material must not be bleached using chlorine gas. If the shaft is made of wood, requirements O17 must be fulfilled. If the shaft is made of polymers from renewable raw materials, requirements in
chapter 2.2.6 must be fulfilled.
Other material parts as tape, elastic etc. shall fulfil relevant material requirements if
comprises in percentage by weight that require this, see O2. A polymer is counted as 100 % renewable if it consists of more than 90 % renewable
Documentation showing that the requirement is fulfilled. For O17 Appendix 1, form 7
in the criteria document may be used.
Primary packaging, material requirements
The following material requirements must be met if the primary packaging makes up
more than 1.0 % of the weight of the sanitary products plus the additional components
in a pack. If the packaging is made of board, the material must meet the requirement part A
and part B in O15.
If the packaging is made of plastic, the requirement O23 and O24 part A must be
fulfilled. For recycled plastic, the requirement O31 shall be fulfilled in addition.
Documentation showing that the requirement is fulfilled.
023e_6_0_hearing_Background.docx 84 (93)
Nordic Ecolabelling
27 November 2015
Background document
Background to the requirements O37 and O38
The requirement concerning labelling of plastic packaging is taken away, and the ban on
PVC in packaging is in requirement O23. However, it is new to set material requirements for the primary packaging.
is the same as it was in the previous version of the criteria. The prohibition of PVC in the packaging remains (see requirement O34). Material requirements for the packaging
are, however, new. Today's sanitary products are often packaged in group packs, while individual product types such as incontinence care products, panty-liners and tampons
may also have packaging around each individual product, so that they are easy to carry in a handbag, for example. Some sanitary towels may be packaged in plastic packaging that
also functions as release paper. Because individual packaging may be important for reasons of hygiene, the material requirements concentrate on the primary packaging.
7.6 Product performance
Performance
The performance/quality of the product must be satisfactory and must match that of
equivalent products on the market.
In the case of products where an acknowledged test exists, this test must be used. The
test may be a laboratory test, the applicant's internal quality test, a consumer test or a
comparative test with an equivalent product. In the case of diapers, sanitary products (sanitary towels and panty-liners), incontinence
care products and breast pads, the performance test must as a minimum include
absorption capacity and rewet under pressure (dryness on the outside). In the case of tampons, the performance test must as a minimum encompass absorption capacity. If a consumer test is performed, a minimum of 80 % must be satisfied with the product
out of a minimum of 10 users, see the conditions in Appendix 2 in the criteria
Documentation (test report or user report) of the performance of the product
including, where applicable, tests of absorption capacity and wet back. The chosen test
must be described and data attached.
Background to the requirement
The requirement remains unchanged. It is in the interest of both licensees and Nordic
Ecolabelling that Nordic Ecolabelled sanitary products should have satisfactory performance characteristics. The function requirement states that: "The
performance/quality of the product must be satisfactory and must match that of equivalent products on the market. In the case of products where an acknowledged test
exists, this test must be used. The test may be a laboratory test, the manufacturer/applicant's internal quality test, a consumer test or a comparative test with
an equivalent product. In the case of diapers, sanitary products (sanitary towels and panty-liners), incontinence care products and breast pads, the performance test must as a
minimum include absorption capacity and dryness on the outside (or: "rewet under pressure" or "wetback"). In the case of tampons, the performance test must as a
minimum encompass absorption capacity. If a consumer test is performed, a minimum of 80% must be satisfied with the product out of a minimum of 10 users."
Standard performance tests do not exist for most types of sanitary products. One exception is incontinence care products, where a standard does exist. Manufacturers may
023e_6_0_hearing_Background.docx 85 (93)
Nordic Ecolabelling
27 November 2015
Background document
accordingly use their own modified tests for children's diapers, sanitary towels, breast pads and other sanitary products. In other words, there is a certain degree of freedom in
relation to documentation. Different tests may be used, provided that the test used provides answers to relevant parameters, and comparisons must be made with equivalent
products available on the market. The responsibility for finding equivalent products is left to the licence applicant, and considerable variations and degrees of detail exist for
sanitary products.
Many manufacturers of sanitary products and producers of the raw materials used in
sanitary products have expressed the wish that Nordic Ecolabelling should impose requirements as to the performance of specific tests and the measurement of various
parameters such as absorption ability under pressure, swelling capacity, etc. However, variations exist in the composition of the products and the way the products function for
the individual consumer. For example, some parents prefer a particular brand of diaper, while others are of the view that a different brand suits their child better. A range of tests
has been performed by various consumer organisations/consumer magazines, and as long as these tests show that the products function "well enough", Nordic Ecolabelling
does not wish to impose specific requirements in relation to the tests conducted. For example, some consumers may prefer the product to have a different fit, some prefer the
thinnest products, others in turn may prefer a slightly thicker product that allows more air to circulate and does not feel so enclosed.
In its criteria for absorbent hygiene products from 2014, the EU Ecolabel has similar requirements, but has specified which tests should be performed. These relate to
absorption ability and protection against leakage for diapers and tampons, plus a dry skin test using the TEWL method for children's diapers.
Tampons
Tampons may as a maximum contain 1,000 aerobic microorganisms per gram of
Description of the test for aerobic microorganisms and a statement on the test results
from the sanitary product manufacturer.
Background to the requirement
The requirement has not been changed in the revision and has a limitation in relation to the content of aerobic microorganisms per gram of product. This requirement is set by
hygienic considerations.
Information on the primary packaging
Copy of the information on the primary packaging (artwork) for all the relevant
languages must be submitted. The absorption ability must be specified on the packaging in the case of product types
where this is relevant. For diapers, sanitary products (sanitary towels and panty-liners), tampons and incontinence care products, for example, this information can be
provided by means of clear details of the size (e.g. the weight of the child in kilos or
pictograms/values indicating the absorption capacity of the product). In the case of relevant products, consumers must be urged not to discard them down
the toilet. This information can be stated using a pictogram. Relevant products include diapers, sanitary towels, panty-liners, tampons, cotton buds, etc.
Sample of the packaging information
023e_6_0_hearing_Background.docx 86 (93)
Nordic Ecolabelling
27 November 2015
Background document
Background to the requirement
The requirement concerning the information text on the products remains unchanged
from the previous version of the criteria.
The requirement concerning information that the products must not be discarded down
the toilet applies to products such as cotton buds, diapers, sanitary towels, panty-liners and tampons. Cotton buds get caught in the mechanical filters of wastewater treatment
plants, creating problems. Disposal of sanitary products down the toilet causes blockages and build-ups in sewage pipes in many municipalities which, in turn, can lead to
basement flooding and the discharge of pollutants into nature. Such information is not relevant to other, larger, products such as bed linen.
The other requirements applicable to the information text, such as the disclosure of information on the absorption of the relevant products and the specification of the size
of the product are unchanged. This information is important to consumers, because they want products that perform satisfactorily from first use. The parameters that are of
interest to consumers are the purpose of the product, if applicable the age or size of the consumer (this applies in particular to children's diapers) and the time at which the
product is to be used.
7.7 Quality and regulatory requirements
Requirements O42-O49 are standard requirements in criteria for Nordic Ecolabelled
products. The final sentence of requirement O49 states that the products must also meet relevant product-specific requirements imposed by the authorities.
Changes compared to previous version
In version 5 of the criteria for sanitary products, Nordic Ecolabelling did not set absolute requirements concerning energy use in the manufacture of all subcomponents/raw
materials. The aim of option b in requirement 26, concerning a calculation of Global Warming Potential (GWP)/kg product, was to indirectly steer towards more energy-
efficient processes for all constituent raw materials. According to the EU Ecolabel's (aforementioned) study, the process of putting together the end product is less significant
than the environmental impact of the individual subcomponents. The GWP calculation was also based on the individual materials, excluding the process that finally put together
the end product.
The previous requirement for waste is removed. It included a waste management plan
and there was a limitation in relation to material waste. This is an area where there have been more stringent requirements in for example Europe, although there are still many
countries where large amounts of waste going to landfill. Because it is in the manufacturer's interest to reduce the amount of in the factory, the requirement
regarding waste is removed.
The requirement for labeling of plastic packaging is also taken away.
023e_6_0_hearing_Background.docx 87 (93)
Nordic Ecolabelling
27 November 2015
Background document
Terms and definitions
Explanation or definition
Additional components
Additional components mean components belonging to the hygiene product that are removed before use of the product. Examples include
release paper, a plastic film around a tampon or a sanitary towel or an
applicator for tampons.
abiotic depletion potential (Materials and fossil fuels)
acidification potential
Term used for superabsorbent polymers made from renewable raw
Chemical product
A chemical product is made of one substance or a mixture of
substances. For chemical substances, unless otherwise stated, the constituent
substances are all substances in the product, including additives (i.e.
preservatives or stabilisers) in the raw materials, but not impurities
from the raw material production. For chemical substances in materials, requirements are set for
constituent substances where these are added by the material/fibre
producer or their supplier (actively added), but not impurities from the
production of the additive or its raw material production. The
requirements for each material set out whether there are
requirements concerning chemical substances in the materials and
state when to refer back to the relevant requirements. Impurities are defined as residual products from the ingredient
production that can be found in the final product in concentrations below 100 ppm (0.01% by weight, 100 mg/kg), but not substances
added to an ingredient or product deliberately and with a purpose,
regardless of amount. However, impurities at the raw material level at
concentrations of over 1.0 % of the raw material will be regarded as a
constituent substance. Substances known to be degradation products
of the constituent substances are also themselves considered to be
constituent substances. The declaration concerning constituent
substances is made by the chemical producer using the knowledge it
possesses at the time in question, based on information from the raw
material producer/supplier, the formulation and available knowledge
of the chemical product. Reservations are made for developments and
new knowledge. Should such new knowledge arise, the undersigned is
obliged to submit an updated declaration to Nordic Ecolabelling.
Components are formed out of one or several materials and chemical products that together fulfil a desirable function. For example: a layer
of non-woven, an outer barrier film or an absorbent core of fluff pulp
and super absorbents.
eutrophication potential
global warming potential
Information sheet
Printed information that is included in the primary package. They do
not have to meet any requirements.
life cycle assessment
For example: fluff pulp, PP, PE, PET, SAP, paper, viscose and cotton
Plastic materials are polymers that has been added chemical products like dyes, stabilisers or other additives. Plastic materials may in
addition be processed into foil, fiber or other components.
A polymer is a substance consisting of molecules with high molecular
mass with a repeating structural unit (monomers). In this document polymers includes various synthetic polymers such as polyethylene
(PE), polypropylene (PP), polyester (PET), polystyrene (PS), polyamide
(PA) and polyether/polyurethane (e.g. spandex, lycra, spandex,
thermoplastic polyurethane and polyurethane foam) and polymers
based on renewable raw materials like PLA and bio-based PE. The document differs between the polymers and other materials such
023e_6_0_hearing_Background.docx 88 (93)
Nordic Ecolabelling
27 November 2015
Background document
as pulp, superabsorbent polymers, viscose fibers and cotton that have
other requirements in this criteria document.
photochemical oxidation potential
photochemical ozone creation potential
Primary packaging
Primary packaging means the packaging around the sanitary products
and additional components as sold in retail outlets or directly to the
customer. Primary packaging does not include transport packaging.
Renewable raw material
Renewable resources are defined as raw materials taken from biological materials that are continuously regenerated within a short
space of years, such as corn and treas.
Recycled material
Recycled plastic can be used in sanitary products when derived from a
closed loops recycling system, which include tractability of the raw
material to the source of it. It must also fulfil the EU commision
directive (EF) nm. 282/2008. In additional components, information sheets and primary packaging
also other types of recycled material can be used. Like plastic
materials and cardboard that is not derived from closed loop system.
Sanitary product
Sanitary product refers to the product used, i.e. excluding additional
components, information sheets and primary packaging
superabsorbent polymer
styrene butadiene rubber
Transport packaging
Transport packaging contains and protects the packs of sanitary
products during transport to stores and consumers.
thermoplastic polyurethane
023e_6_0_hearing_Background.docx 89 (93)
Nordic Ecolabelling
27 November 2015
Background document
Appendix 1 Requirement for viscose
Table B1 Summary of BAT values and requirements for viscose
0.3 g/0.5-3 g Zn/tonne)
quirement also apply to viscose?
Ecolabelling sanitary, consultation prop. version 6
120 g S/kg Staple: 30 g S/kg
160 BREF-dokument for polymerer, 2007, er tilgjengelig på følgende nettsted: http://eippcb.jrc.ec.europa.eu/reference/BREF/pol_bref_0807.pdf 161 BREF-dokument for polymerer, 2013, er tilgjengelig på følgende nettsted:
Nordic Ecolabelling
27 November 2015
Background document
Appendix 2 Energy consumption Polymers
The table below is a summary of energy figures and GWP values for the production of
various polymer types. The background to the table is described in section 7.5.6.
Polymers (materials/films and fibre).
Table B2.1 Energy figures and GWP values
Process energy, [MJ]
content in
sanitary v 5
material,
PS (general purpose),
PlasticsEurope PU (only found for
foam) HDPE (sugar cane)
96 (primary energy demand)
33.6 (ethene HDPE) Of this, 18.3 is non-renewable
HDPE fossil Braskem
42 (PED) disposable
* Values from PlasticsEurope
** GWP values that may be used as default values in the absence of factory-specific figures. Global warming potential, GWP, applies a time horizon of 100 years and is expressed as kg CO2 equivalents per kg material from cradle to gate. The background to the values is described in the background document for version 5 of the criteria for the Nordic Ecolabelling of
sanitary products. The values have been calculated based on LCA studies, with an added uncertainty factor, since current databases are based on average values from the industry.
Nordic Ecolabelling
27 November 2015
Background document
Appendix 3 Guidelines for standard,
renewable comoditives
Nordic Ecolabelling sets requirements on the standards to which cultivated commoditives is certified. These requirements are described below. Each individual
national sustainability standard and each certification system is reviewed by Nordic Ecolabelling as to fulfilment of the requirements. When a standard is revised, it is re-
Requirements on standards
The standard must balance economic, ecological and social interests and comply
with the Rio Declaration's principles, Agenda 21 and the Forest Principles, and respect relevant international conventions and agreements.
The standard must contain absolute requirements and promote and contribute
towards sustainable cultivation. Nordic Ecolabelling places special emphasis on the standard including effective requirements and that the requirements protect the biodiversity.
The standard must be available to the general public. The standard must have
been developed in an open process in which stakeholders with ecological, economic and social interests have been invited to participate.
The requirements related to the sustainable standards are formulated as process requirements. The basis is that if stakeholders agree on the economic, social and
environmental aspects of the standard, this safeguards an acceptable requirement level.
If a sustainability standard is developed or approved by stakeholders with ecological,
economic and social interests, the standard may maintain an acceptable standard. Accordingly, Nordic Ecolabelling requires that the standard balances these three interests
and that representatives from all three areas are invited to participate in development of the sustainable standard.
The standard must set absolute requirements that must be fulfilled for the certification. This ensures that the agriculture management fulfils an acceptable level regards the
environment. When Nordic Ecolabelling requires that the standard shall "promote and contribute towards sustainable cultivation, the standard must be assessed and revised
regularly to initiate process improvement and successively reduce environmental impact.
Requirements on certification system
The certification system must be open, have significant national or international
credibility and be able to verify that the requirements in the sustainable standard are fulfilled.
Requirements on certification body
The certification body must be independent, credible and capable of verifying
that the requirements of the standard have been fulfilled. The certification body must also be able to communicate the results and to facilitate the effective implementation of the standard.
Nordic Ecolabelling
27 November 2015
Background document
The certification system must be designed to verify that the requirements of the standard are fulfilled. The method used for certification must be repeatable and applicable so the
requirements can be verified. Certification must be in respect to a specific sustainable standard. There must be inspection prior to certification.
Requirements on Chain of Custody (CoC) certification
Chain of Custody certification must be issued by an accredited, competent third
The system shall stipulate requirements regarding the chain of custody that assure
traceability, documentation and controls throughout the production chain.
Copy of cultivation standard, name, address and telephone number to the organisation who has worked out the standard and audit rapports.
References to persons who represents stakeholders with ecological, economic and social interests who have been invited to participate.
Nordic Ecolabelling may request further documents to examine whether the requirements of the standard and certification system in question can be approved.
Source: http://joutsenmerkki.fi/wp-content/uploads/2015/12/Sanitary-products_Background.pdf
Long-Term Experiences with an Iterative Design of a QR-Code-Based Payment System for Beverages Max-Emanuel Maurer, Alexander De Luca, Alina Hang, Doris Hausen, Fabian Hennecke, Sebastian Loehmann, Henri Palleis, Hendrik Richter, Simon Stusak, Aurélien Tabard, Sarah Tausch, Emanuel von Zezschwitz, Franziska Schwamb, Heinrich Hussmann, and Andreas Butz
Contents lists available at Journal of Chromatography A Recent developments in liquid chromatography–mass spectrometry and related Michal Holˇcapek , Robert Jirásko, Miroslav Lísa Department of Analytical Chemistry, Faculty of Chemical Technology, University of Pardubice, Studentská 573, 53210 Pardubice, Czech Republic This review summarizes the state-of-art in liquid chromatography–mass spectrometry (LC–MS) and